Устройство холодильной машины | Техническая библиотека ПромВентХолод
Охлаждение различных объектов – продуктов питания, воды, других жидкостей, воздуха, технических газов и др. до температур ниже температуры окружающей среды происходит с помощью холодильных машин различных типов. Холодильная машина по большому счету не производит холод, она является лишь своеобразным насосом, который переносит теплоту от менее нагретых тел к более нагретым. Основан же процесс охлаждения на постоянном повторении т.н. обратного термодинамического или другими словами холодильного цикла. В самом распространенном парокомпрессионном холодильном цикле перенос теплоты происходит при фазовых превращениях хладагента – его испарении (кипении) и конденсации за счет потребления подведенной извне энергии.
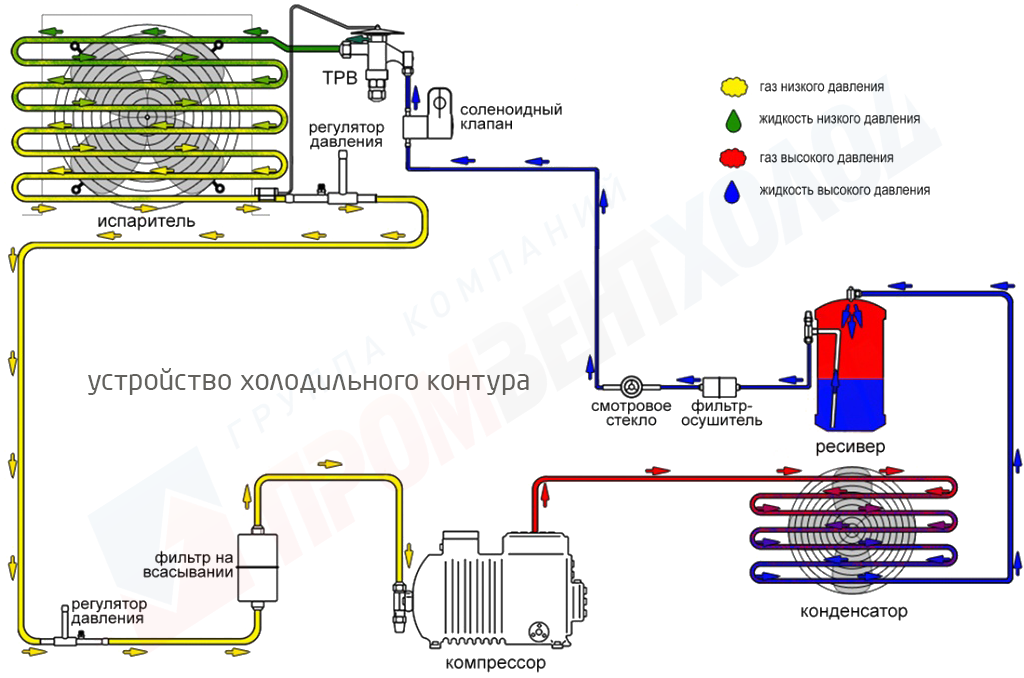
Основными элементами холодильной машины, с помощью которых реализуется ее рабочий цикл, являются:
- компрессор – элемент холодильного цикла, обеспечивающий повышение давления хладагента и его циркуляцию в контуре холодильной машины;
- дросселирующее устройство (капиллярная трубка, терморегулирующий вентиль) служит регулирования количества хладагента, попадающего в испаритель в зависимости от перегрева на испарителе.
- испаритель (охладитель) – теплообменник, в котором происходит кипение хладагента (с поглощением тепла) и непосредственно сам процесс охлаждения;
- конденсатор – теплообменник, в котором в результате фазового перехода хладагента из газообразного состояния в жидкое, отведенная теплота сбрасывается в окружающую среду.

При этом необходимо наличие в холодильной машине других вспомогательных элементов, – электромагнитные (соленоидные) вентили, контрольно-измерительные приборы, смотровые стекла, фильтры-осушители и т.д. Все элементы соединены между собой в герметичный внутренний контур с помощью трубопроводов с теплоизоляцией. Контур холодильной машины заполняется хладагентом в необходимом количестве. Основной энергетической характеристикой холодильной машины является холодильный коэффициент, который определяется отношением количества тепла, отведенного от охлаждаемого источника, к затраченной энергии.
Холодильные машины в зависимости от принципов работы и применяемого хладагента бывают нескольких типов. Наиболее распространенные парокомпрессионные, пароэжекторные, абсорбционные, воздушные и термоэлектрические.
Хладагент
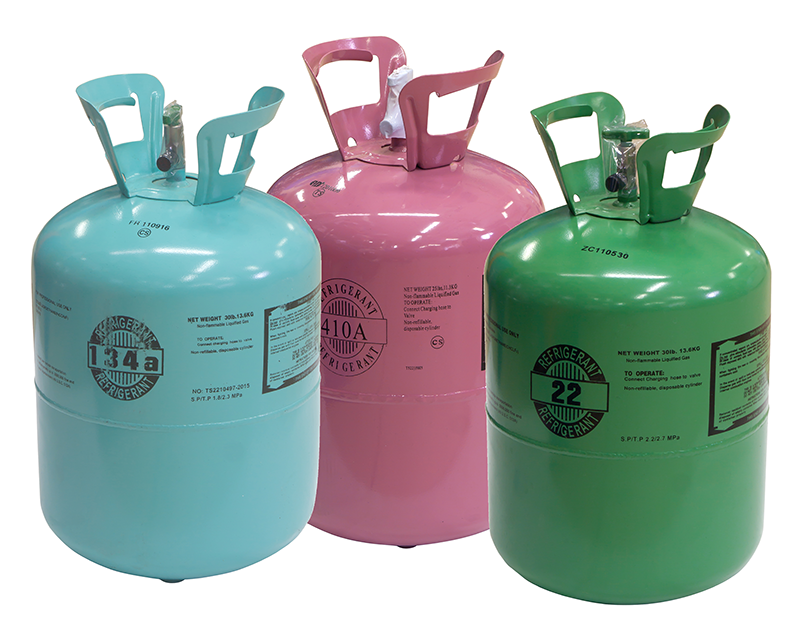
Хладагент – рабочее вещество холодильного цикла, основной характеристикой которого является низкая температура кипения. В качестве хладагентов чаще всего применяют различные углеводородные соединения, которые могут содержать атомы хлора, фтора или брома. Также хладагентом могут быть аммиак, углекислый газ, пропан и т.д. Реже в качестве хладагента применяют воздух. Всего известно около сотни типов хладагентов, но изготавливается промышленным способом и широко применяется в холодильной, криогенной технике, кондиционировании воздуха и других отраслях всего около 40. Это R12, R22, R134A, R407C, R404A, R410A, R717, R507 и другие. Основная область применения хладагентов – это холодильная и химическая промышленность. Кроме того, некоторые фреоны используют в качестве пропеллентов при производстве различной продукции в аэрозольной упаковке; вспенивателей при производстве полиуретановых и теплоизолирующих изделий; растворителей; а также в качестве веществ, тормозящих реакцию горения, для систем пожаротушения различных объектов повышенной опасности – тепловых и атомных электростанций, гражданских морских судов, боевых кораблей и подводных лодок.
Терморегулирующий вентиль (ТРВ)
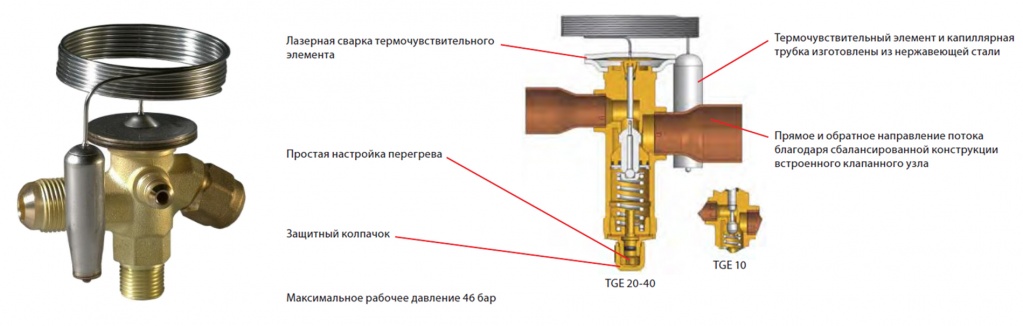
Терморегулирующий вентиль (ТРВ) – один из основных компонентов холодильных машин, известен как наиболее распространенный элемент для дросселирования и точного регулирования подачи хладагента в испаритель. ТРВ использует в качестве регулятора расхода хладагента клапан игольчатого типа, примыкающий к основанию тарельчатой формы. Количество и расход хладагента определяется проходным сечением ТРВ и зависит от температуры на выходе из испарителя. При изменении температуры хладагента на выходе из испарителя, давление внутри этой системы меняется. При изменении давления меняется проходное сечение ТРВ и, соответственно, меняется расход хладагента.
Термосистема заполнена на заводе-изготовителе точно определенным количеством того же хладагента, который является рабочим веществом данной холодильной машины. Задача ТРВ – дросселирование и регулирование расхода хладагента на входе в испаритель таким образом, чтобы в нем наиболее эффективно проходил процесс охлаждения. При этом хладагент должен полностью перейти в парообразное состояние. Это необходимо для надежной работы компрессора и исключения его работы т.н. «влажным» ходом (т.е. сжатие жидкости). Термобаллон крепится на трубопровод между испарителем и компрессором, причем в месте крепления необходимо обеспечить надежный термический контакт и теплоизоляцию от воздействия температуры окружающей среды. Последние 15-20 лет в холодильной технике стали получать широкое распространение электронные ТРВ. Они отличаются тем, что у них отсутствует выносная термосистема, а ее роль играет терморезистор, закрепленный на трубопроводе за испарителем, связанный кабелем с микропроцессорным контролером, который в свою очередь управляет электронным ТРВ и вообще всеми рабочими процессами холодильной машины.
Соленоидный вентиль
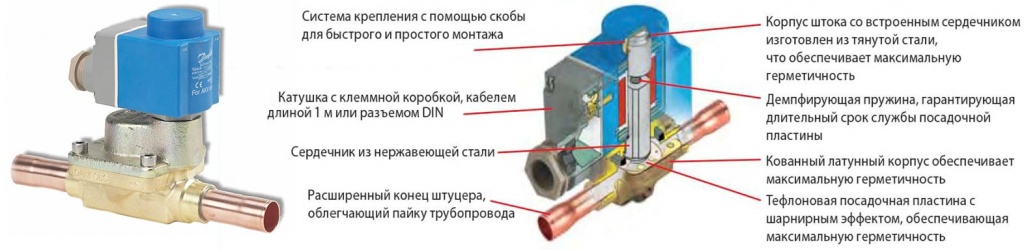
Соленоидный вентиль служит для двухпозиционного регулирования («открыто-закрыто») подачи хладагента в испаритель холодильной машины либо для открытия-закрытия от внешнего сигнала определенных участков трубопроводов. При отсутствии питания на катушке тарелка клапана под воздействием специальной пружины удерживает соленоидный вентиль закрытым. При подаче питания сердечник электромагнита, соединенный штоком с тарелкой, преодолевает усилие пружины, втягивается в катушку, тем самым приподнимая тарелку и открывая проходное сечение вентиля для подачи хладагента.
Смотровое стекло
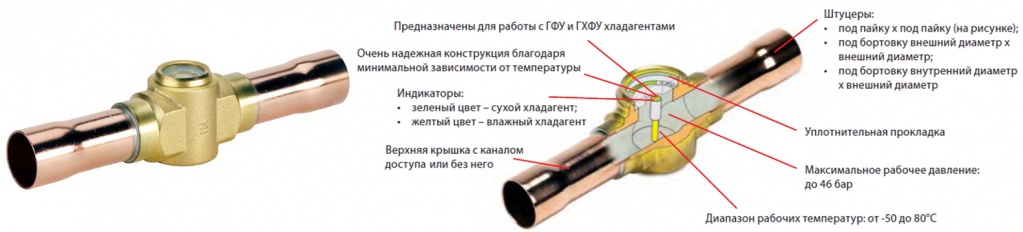
Смотровое стекло в холодильной машине предназначено для определения:
- состояния хладагента;
- наличие влаги в хладагенте, которое определяется цветом индикатора.

Смотровое стекло обычно монтируют в трубопроводе на выходе из накопительного ресивера. Конструктивно смотровое стекло представляет собой металлический герметичный корпус с окном из прозрачного стекла. Если при работе холодильной машины в окне наблюдается поток жидкости с отдельными пузырями парообразного хладагента, то это может свидетельствовать о недостаточной заправке или других неисправностях в ее функционировании. Может устанавливаться и второе смотровое стекло на другом конце указанного выше трубопровода, в непосредственной близости от регулятора расхода, которым может быть соленоидный вентиль, ТРВ или капиллярная трубка. Цвет индикатора показывает наличие или отсутствие влаги в холодильном контуре.
Фильтр-осушитель
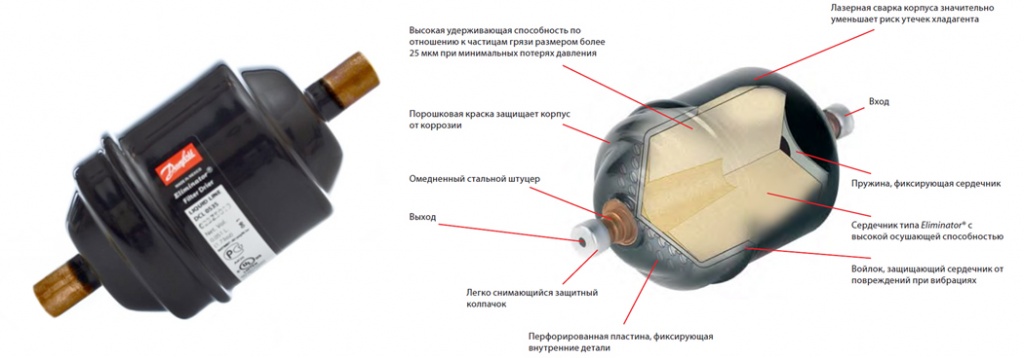
Фильтр-осушитель или цеолитовый патрон еще один важный элемент контура холодильных машин. Он необходим для удаления влаги и механических загрязнений из хладагента, тем самым защищая от засорения ТРВ. Обычно он монтируется с помощью паяных или штуцерных соединений непосредственно в трубопровод между конденсатором и ТРВ (соленоидным вентилем, капиллярной трубкой). Чаще всего конструктивно представляет собой отрезок медной трубы диаметром 16…30 и длиной 90…170 мм, закатанный с обеих сторон и с присоединительными патрубками. Внутри по краям установлены две металлические фильтрующие сетки, между которыми расположен гранулированный (1,5…3,0 мм) адсорбент, обычно это синтетический цеолит. Это т.н. разовый фильтр-осушитель, но существуют многоразовые конструкции фильтров с разборным корпусом и резьбовыми трубопроводными соединениями, требующими только время от времени замены внутреннего цеолитового картриджа. Замена разового фильтра- осушителя или картриджа необходима после каждого вскрытия внутреннего контура холодильной машины. Существуют одно-направленные фильтры, предназначенные для работы в системах «только холод» и дву-направленные, используемые в агрегатах «тепло-холод».
Ресивер
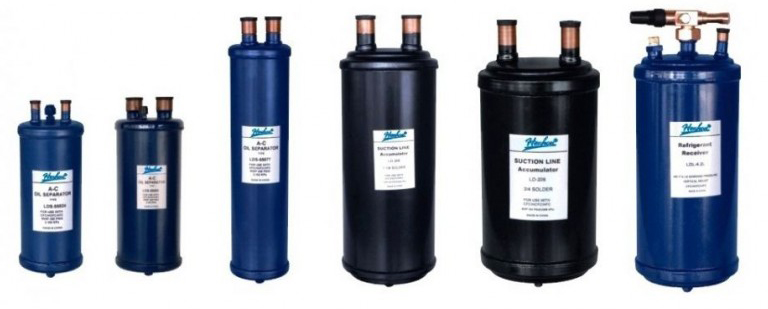
Ресивер – герметичный цилиндрический накопительный бак различной емкости, изготовленный из стального листа, и служащий для сбора жидкого хладагента и его равномерной подачи к регулятору расхода (ТРВ, капиллярная трубка) и в испаритель. Существуют ресиверы как вертикального, так и горизонтального типа. Различают линейные, дренажные, циркуляционные и защитные ресиверы. Линейный ресивер устанавливается с помощью паяных соединений в трубопровод между конденсатором и ТРВ и выполняет следующие функции:
- обеспечивает непрерывную и бесперебойную работу холодильной машины при различных тепловых нагрузках;
- является гидравлическим затвором, препятствующим попаданию пара хладагента в ТРВ;
- выполняет функцию масло- и воздухоотделителя;
- освобождает трубы конденсатора от жидкого хладагента.
Дренажные ресиверы служат для сбора и хранение всего количества заправленного хладагента на время ремонтных и сервисных работ, связанных с разгерметизацией внутреннего контура холодильной машины.
Циркуляционные ресиверы применяют в насосно-циркуляционных схемах подачи жидкого хладагента в испаритель для обеспечения непрерывной работы насоса и монтируют в трубопровод после испарителя в точку с самой низкой отметкой по высоте для свободного слива в него жидкости.
Защитные ресиверы предназначены для безнасосных схем подачи фреона в испаритель, их устанавливают совместно с отделителями жидкости во всасывающий трубопровод между испарителем и компрессором. Они служат для защиты компрессора от возможной работы «влажным» ходом.
Регулятор давления
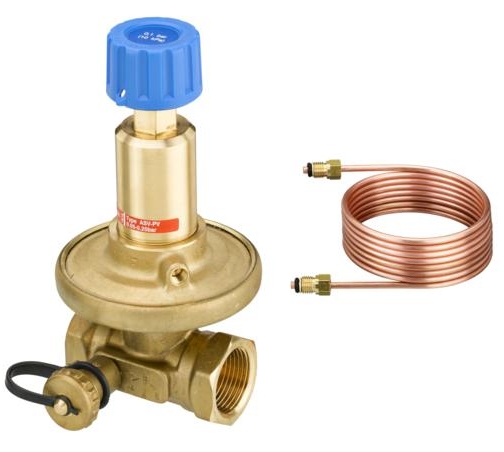
Регулятор давления – автоматически управляемый регулирующий клапан, применяемый для снижения либо поддержания давления хладагента путем изменения гидравлического сопротивления потоку проходящего через него жидкого хладагента. Конструктивно состоит из трех основных элементов: регулирующего клапана, его исполнительного механизма и измерительного элемента. Исполнительный механизм непосредственно воздействует на тарелку клапана, изменяя или закрывая проходное сечение. Измерительный элемент сравнивает текущее и заданное значение давления хладагента и формирует управляющий сигнал для исполнительного механизма регулирующего клапана. В холодильной технике существуют регуляторы низкого давления, чаще называемые прессостатами. Они управляют давлением кипения в испарителе, их устанавливают во всасывающий трубопровод за испарителем. Регуляторы высокого давления называют маноконтроллерами. Их чаще всего применяют в холодильных машинах с воздушным охлаждением конденсатора для поддержания минимально необходимого давления конденсации при понижении температуры наружного воздуха в переходный и холодный период года, обеспечивая тем самым т.н. зимнее регулирование. Маноконтроллер устанавливают в нагнетательный трубопровод между компрессором и конденсатором.

Специалисты рекомендуют
Вернуться
Схема холодильной установки — Наши статьи ПрофХолодСистемс
Понять, как работает холодильное оборудование разных моделей и типов, помогает схема установки. Она состоит не только из базового комплекта, но и вспомогательных устройств, обеспечивающих бесперебойную и эффективную работу.
Особенности схемы
План установки показывает количество, тип и расположение компрессоров, теплообменников и других компонентов. Все эти детали нужны для полноценного функционирования оборудования. Из-за конструкции и устройства установок, их сервисное обслуживание существенно усложняется.
Основные причины возникающих проблем:
Большое количество охлаждаемых объектов. Они часто расположены на большом расстоянии от диспетчерского пункта.
Разветвленная сеть трубопроводов.
Использование аммиака или других токсичных хладагентов.
Резкие перепады тепловых нагрузок.
Особенности разработки установки
Чтобы создать схему холодильной установки, учитываются определенные требования.
К ним относятся:
Соблюдение стабильного температурного режима с возможностью корректировки для проведения ремонта или изменения параметров работы.
Обеспечение безопасности для обслуживающего персонала и долгой службы оборудования.
Сделать схему наглядно простой и понятной, чтобы можно было быстро внести изменения, не совершая ошибок.
Обеспечение бесперебойного поступления хладагента и теплоотдачи.
Внедрение частичной или полной автоматизации.
Простой монтаж и эксплуатация.
Как автоматизировать холодильную установку?
Большая часть современного оборудования работает автономно. Но важно подготовить его к этому процессу. Точнее, убедиться, что эксплуатация оборудования безопасна для персонала. Для этого улучшают схемы. Они предотвратят возникновения опасных ситуаций из-за резкого изменения тепловых нагрузок. Если оборудование не будет автоматизировано, велика вероятность частичного отключения компрессоров.
Разработка правильной схемы поможет избежать этого.
Холодоснабжение бывает двух типов:
Централизованным. Главными его минусами являются разветвленная сеть и большая протяженность трубопроводов, большое количество хладагента и сложная автоматизация.
Децентрализованным, в котором каждый объект обслуживается отдельным агрегатом.
Создание компаундных схем внесло положительные изменения при обустройстве холодильных машин. Благодаря циркулярным ресиверам, выполняющим функцию промежуточных сосудов и работающих при повышенном давлении, количество компонентов снизилось, а обслуживание и эксплуатация оборудования стало проще.
Любая установка включает набор узлов со специфическими деталями. Их также следует учитывать при создании эффективной схемы.
Описание принципа работы холодильной установки
Обычному человеку, как правило, нет необходимости разбираться в принципе действия холодильной машины, для него важен результат. Результатом работы холодильной установки является: охлажденные продукты – от замороженных овощей, до мясо-молочной продукции или например охлажденный воздух, если речь идет о сплит-системах.
Другое же дело, когда холодильные машины выходит из строя и для проведения ремонта холодильных установок требуется вызов специалиста. В данном случае уже было бы не плохо разбираться в принципе работы таких агрегатов. Хотя бы для того, чтобы понимать необходимость замены или ремонта составляющей холодильной машины.
Основное назначение холодильной установки – это забор тепла от охлаждаемого тела и перенос этого тепла или энергии другому объекту или телу. Для понимания процесса требуется уяснить простую вещь – если мы нагреваем или сжимаем тело, то мы сообщаем этому телу энергию (или тепло), охлаждая и расширяя, мы отбираем энергию. Это основной принцип, на основе которого и построен перенос тепла.
В холодильной машине для переноса тепла применяются хладагенты – рабочие вещества холодильной машины, которые при кипении и в процессе изотермического расширения отнимают теплоту от охлаждаемого объекта и затем после сжатия передают её охлаждающей среде за счёт конденсации
Холодильный компрессор 1 отсасывает газообразный хладагент – фреон из испарителей 3, сжимает его и нагнетает в конденсатор 2. В конденсаторе 2 фреон конденсируется и переходит в жидкое состояние. Из конденсатора 2 жидкий хладагент попадает в ресивер 4, где происходит его накопление. Ресивер оснащен запорными вентилями 19 на входе и выходе. Из ресивера хладагент поступает в фильтр-осушитель 9, где происходит удаление остатков влаги, примесей и загрязнений, после этого проходит через смотровое стекло с индикатором влажности 12, соленоидный вентиль 7 и дросселируется терморегулирующим вентилем 17 в испаритель 3.
В испарителе хладагент кипит, забирая тепло от объекта охлаждения. Пары хладагента из испарителя через фильтр на всасывающей магистрали 11, где они отчищаются от загрязнений, и отделитель жидкости 5 поступают в компрессор 1. Затем цикл работы холодильной установки повторяется.
Отделитель жидкости 5 предотвращает попадание жидкого хладагента в компрессор. Для обеспечения гарантированного возврата масла в картер компрессора, на выходе из компрессора устанавливаться маслоотделитель 6. При этом масло через запорный вентиль 24, фильтр 10 и смотровое стекло 13 по линии возврата – поступает в компрессор.
Виброизоляторы 25, 26 на всасывающей и нагнетательной магистралях гасят вибрации при работе компрессора и препятствуют их распространению по холодильному контуру.
Компрессор оснащён картерным нагревателем 21 и двумя запорными вентилями 20. Картерный нагреватель 21 выпаривает хладагент из масла, предотвращая конденсацию хладагента в картере компрессора во время его стоянки и поддержания заданной температуры масла.
В холодильных машинах с полугерметичными поршневыми компрессорами, у которых в системе смазки установлен масляный насос, используется реле контроля давления масла 18. Задача этого реле – отключить компрессор в случае снижения давления масла в системе смазки.
В случае установки агрегата на улице он должен быть дополнительно укомплектован гидравлическим регулятором давления конденсации, для обеспечения стабильной работы в зимних условиях и поддержания необходимого давления конденсации в холодное время года.
Реле высокого давления 14 управляют включением/выключением вентиляторов конденсатора, для поддержания необходимого давления. Реле низкого давления 15 управляет включением/выключением компрессора.
Аварийное реле высокого и низкого давлений 16 предназначено для аварийного отключения компрессора в случае пониженного или повышенного давления.
Основные узлы холодильной системы | Промхолд
Холодильная система – это компоненты, собранные в единое целое, посредством трубопроводов.
Схема холодильной системы
Сердце холодильной системы – компрессор. Часто объединяют компрессор, нагнетательный трубопровод, конденсатор и ресивер в один компактный агрегат.
У компрессора имеются 2 патрубка: всасывающий и нагнетающий. На схеме показано движение хладагента (фреона) по системе. В разных местах холодильной системы хладагент будет находиться в разных фазовых состояниях, он будет либо в состоянии кипения, либо конденсации. Фазовые переходы нужны для создания нужного процесса: охлаждение или нагревание.
Сначала система заправляется газом фреона. Компрессор начинает качать и сжимать газ (может сжать примерно в 15 раз), повышает давление газа и он превращается в жидкость. Чем выше разница давлений между нагнетанием и всасыванием, тем выше температура нагнетаемых паров.
После компрессора газ перемещается в маслоотделитель. Маслогазовая смесь попадает в маслоотделитель и там масло отделяется от хладагента. Происходит это следующим образом: смесь завихряется и, по принципу турбулентности, масло отделяется (с помощью вращения цетробежной силой). Далее приподнимается игольчатый клапан и всё масло, которое скопилось на дне маслоотделителя, поступает в компрессор, благодаря разнице давлений. Пять процентов остаётся и идёт дальше с фреоном, но из-за наклона труб возвращается в компрессор.
Конденсатор — специальные теплообменник, необходимый для отвода отобранного у продукта тепла. Внутри них горячий газообразный фреон охлаждается за счет нагревания окружающего воздуха и конденсируется в жидкость. Пар проходит по системе трубок, охлаждается и превращается в жидкость. На входе в конденсатор температура хладагента может достигать 120 °С. Температура конденсации поддерживается на уровне 45 °С, но может быть и от 30 до 50 °С (в летнее время может возрасти, в зимнее уменьшиться). Газ полностью превращается в жидкость и дальше будет охлаждаться и на выходе будет не 45, а примерно 30 °С. Разница между температурой конденсации и температурой на выходе из конденсатора, называется переохлаждением.
Из конденсатора жидкий фреон попадает в ресивер – это вспомогательный узел. Он помогает стабилизировать работу холодильной установки. Ресивер – накопитель, сосуд, в который входит 2 трубки, одна из них доходит почти до дна. Жидкость попадает в ресивер через трубку, которая не достаёт дна. В ресивере давление такое же, как в компрессоре. По трубе, которая выходит из ресивера мы гарантированно получаем жидкость, до ресивера в трубах может пролетать газ (т.к. не весь сконденсировался), это бы могло вредить системе, если ресивер отсутствует. В испаритель должна попадать только жидкость. После ресивера в трубу можно впаивать спец. стекло, чтобы видеть: жидкость выходит или газ.
Диаметр соединительных труб, от конденсатора к ресиверу, от испарителя к конденсатору, подбирается специально, чтобы не было перепада давления на входе и выходе трубки.
Испаритель – основной элемент холодильной системы, в нём происходит кипение хладагента. Терморегулирующий вентиль (ТРВ) – автоматически регулирует подачу хладагента в испаритель и устанавливается непосредственно на входе в испаритель, имеет датчик – термобалон, который устанавливается на выходе испарителя, ТРВ и термобалон соединяются тонкой трубочкой. В зависимости от температуры трубы на выходе из испарителя будут разные давления в термобалоне, это давление воздействует на мембрану ТРВ, которая регулирует подачу хладагента.
В некоторых системах устанавливается отделитель жидкости, для того чтобы не выкипевший хладагент не попал в компрессор. Жидкость, пролетая в трубе, через входную трубку попадает в отделитель жидкости и под силой тяжести падает на его дно, газ проходит дальше через выходную трубку. Чистые пары попадают в компрессор и охлаждают статор.
Холодильная техника комплектуется надежной автоматикой (щитами управления), собранной на базе микропроцессоров.
5.1.4. Схемы двухступенчатых холодильных машин и их изображения в диаграмме i — lgP
Для получения низких температур в охлаждаемых объектах необходимы низкие температуры кипения t0, т. е. в испарителе приходится поддерживать и низкое давление P0. Это приводит к увеличению значения отношения давлений Рк / Р0 и к трем нежелательным явлениям: увеличению температуры нагнетания компрессора, возрастанию объемных потерь в компрессоре и увеличению дроссельных потерь в регулирующем вентиле, что вызывает уменьшение холодопроизводительности установки. Для современных быстроходных аммиачных поршневых компрессоров температура нагнетания хладагента не должна превышать 160 °С, так как дальнейшее ее повышение приводит к нарушению нормальной смазки, вызывает пригорание масла и его самовозгорание. Снижение производительности компрессора при больших значениях отношения давлений Рк / Р0 связано с уменьшением коэффициента подачи. На основании опытных данных установлено, что при Рк / Р0 > 8 целесообразно применять многоступенчатое сжатие хладагента в двух (и более) последовательно соединенных цилиндрах или компрессорах. Для ограничения роста температуры нагнетания в результате последовательных сжатий (после каждой ступени сжатия) пар хладагента охлаждается либо водой в промежуточном холодильнике, либо кипящим хладагентом в специальном теплообменном аппарате.
Наиболее распространенной двухступенчатой схемой является схема двухступенчатого сжатия со змеевиковым промежуточным сосудом и промежуточным охлаждением пара (рис. 59). Пар хладагента после сжатия в цилиндре низкого давления ЦНД до промежуточного давления РПР поступает в промежуточный сосуд ПС ниже уровня кипящего хладагента и охлаждается до состояния насыщения, барботируя через слой жидкости. Выходя из ПС, пар перегревается во всасывающем трубопроводе перед цилиндром высокого давления ЦВД и в перегретом состоянии поступает в него. Следует отметить, что даже в цикле с полным промежуточным охлаждением пар должен поступать в компрессор высокого давления (так же, как и в компрессор низкого давления) в перегретом состоянии, что является обязательным требованием техники безопасности. После сжатия в ЦВД до давления конденсации РK, пар конденсируется в конденсаторе КД, после чего жидкость высокого давления разделяется на два потока (точка 5′). Основной поток поступает в змеевик ПС, где переохлаждается, отдавая теплоту кипящей жидкости, и в состоянии глубокого переохлаждения поступает через регулирующий вентиль РВ2 в испаритель. Другой поток жидкости дросселируется в РВ1 от РK до промежуточного давления Рпр и поступает в промежуточный сосуд. Таким образом, в промежуточном сосуде происходит сбив перегрева пара между компрессорами низкого и высокого давления, а также переохлаждение жидкости перед РВ2 за счет кипения жидкого хладагента при РПР. Для анализа работы двухступенчатых схем и построения цикла в диаграмме необходимо определить промежуточное давление РПР. При минимальной работе компрессоров низкого и высокого давления определяют РПР из равенства отношений давлений в обеих ступенях сжатия по формуле
На диаграмме (рис. 59) проводят три изобары: Р0, РПР и РK , которым соответствуют три температуры насыщения: t0, tПР и tK . Задавшись значением перегрева пара на всасывании перед ЦНД, строят точку 1. Из этой точки по адиабате идет процесс сжатия до изобары РПР — (точка 2). В промежуточном сосуде пар охлаждается до состояния насыщения 3» , а затем перегревается во всасывающем трубопроводе (точка 3). Температуру перегрева пара перед ЦВД следует принимать в пределах 5…10°С, тогда t3 = tПР + (5…10 °С). Из точки 3 проводится адиабата до пересечения с изобарой РK (точка 4). Это конечная температура нагнетания пара двухступенчатого сжатия. Из диаграммы видно, что если бы было применено одноступенчатое сжатие 1 — 2′ , то конечная температура нагнетания была бы значительно выше (сравните точки 2′ и 4). Процесс 4 — 5′ происходит в конденсаторе при РK = const , и жидкость высокого давления в точке 5′ разделяется на два потока. Процесс дросселирования в РВ1 изображается вертикалью, опущенной из точки 5′ до пересечения с изобарой РПР . Парожидкостная смесь состояния точки 6 поступает в промежуточный сосуд, где кипит при промежуточных параметрах (процесс 6 — 3′′). Переохлаждение в змеевике ПС происходит при давлении конденсации, поэтому точка 7, определяющая состояние хладагента на выходе из змеевика, лежит в области переохлажденной жидкости на изобаре РK . Температура точки 7 определяется из выражения t7 = tПР + (2…3 °С) . Дросселирование в РВ2 изображается вертикалью, опущенной из точки 7 до пересечения с изобарой Р0 . Парожидкостная смесь состояния точки 8 поступает в испаритель, где кипит (процесс 8 — 1′′).
На диаграмме (рис. 59):
1′′ — 1 — перегрев пара на всасывании в ЦНД при Р0 = const ;
1 — 2 — адиабатическое сжатие в ЦНД от Р0 до РПР ;
2 — 3′′ — сбив перегрева пара в промежуточном сосуде при РПР = const ;
3′′ — 3 — перегрев пара на всасывании в ЦВД при РПР = const ;
3 — 4 — адиабатическое сжатие в ЦВД от РПР до РK ;
4 — 4′′ — сбив перегрева пара в конденсаторе при РK = const ;
4′′ — 5′ — конденсация в конденсаторе при РK = const , tK = const ;
5′ — 6 — дросселирование в РВ1 от РK до РПР при i = const ;
6 — 3′′ — кипение в ПС при РПР = const и tПР = const ;
5′′ — 7 — переохлаждение жидкости в змеевике ПС при РK = const ;
7 — 8 — дросселирование в РВ2 от РK до Р0 при i = const ;
8 — 1′′ — кипение в испарителе при Р0 = const , t0 = const .
Массовая подача компрессора высокого давления M2 больше, чем компрессора низкого давления M1 , так как, кроме пара, поступающего из компрессора низкого давления в количестве M1 в него поступает еще и пар, образуемый при кипении жидкости в промежуточном сосуде. Объемная холодопроизводительность компрессора высокого давления меньше примерно в три раза из-за уменьшения объема пара при сжатии в компрессоре низкого давления. Массовая подача ЦНД, кг/с, определяется по формуле M1 = Q0 / q0, где Q0 — холодопроизводительность, кВт; q0 — удельная холодопроизводительность, кДж/кг: q0 = i1′ — i8 .
Массовая подача ЦВД, кг/с, находится из соотношения M2 = M1 (i2 — i7)(i3 — i6) .
Удельная работа сжатия ЦНД, кДж/кг, равна l1 = i2 — i1 ;
удельная работа сжатия ЦВД, кДж/кг, l2 = i4 — i3;
удельная нагрузка на конденсатор, кДж/кг, qK = i4 — i5 ;
холодильный коэффициент равен ε = q0/(l1 + l2) .
Иногда применяют цикл двухступенчатого сжатия с двойным дросселированием и полным промежуточным охлаждением (рис. 60). Такая схема применена, например, на холодильных установках для зверосовхозов, поставляемых финской фирмой «Хуурре». В отличие от схемы, представленной на рис. 59, вся жидкость после конденсатора (состояние точки 5) дросселируется в РВ1 до промежуточного давления РПР и поступает в ПС в состоянии точки 6. Паро-жидкостная смесь этого состояния разделяется в сосуде на насыщенный пар состояния точки 3′′, который отсасывается ЦВД, и насыщенную жидкость, которая частично выкипает в ПС (процесс 6 — 3′′). Оставшаяся насыщенная жидкость состояния точки 7 поступает к РВ2 , где дросселируется от промежуточного давления РПР до давления кипения Р0 и поступает в испаритель. Изображение цикла с двукратным дросселированием в диаграмме показано на рис. 60. В этой схеме к вентилю РВ2 поступает насыщенная жидкость, а не переохлажденная. Это является недостатком таких схем и позволяет их использовать только в небольших установках. Поэтому схема со змеевиковым промежуточным сосудом более предпочтительна. Массовый расход хладагента через ЦНД определяется как, кг/с, M1 = Q0 / q0 . Массовый расход хладагента на полное промежуточное охлаждение, кг/с, m′ = M1 (i2 — i3)(i3′′ — i6) ; массовый расход пара через ЦВД, кг/с, M2 = (M1 + m′ )(1 — x6 ) , где x6 — паросодержание хладагента в точке 6 после первого дросселирования.
Остальные характеристики цикла определяются по формулам, указанным выше.
В связи со все расширяющимся применением на холодильных установках винтовых агрегатов интерес представляют схема и цикл двухступенчатого сжатия с одноступенчатым винтовым компрессором с промежуточным отбором пара (рис. 61). Холодильный агент в состоянии точки 1 поступает в винтовой компрессор КМ, заполняя его полость всасывания. Затем давление в компрессоре повышается за счет уменьшения объема рабочей полости, и, когда оно достигает промежуточного значения РПР (процесс 1 — 2 ), в полость сжатия через специальное окно поступает пар хладагента состояния 3» из теплообменника ТО. В результате смешения получается пар, соответствующий состоянию точки 3, который далее сжимается до конечного давления РK (процесс 3 — 4 ). Следует отметить, что процессы 1 — 2 и 3 — 4 не являются адиабатическими, так как охлажденное масло, впрыскиваемое в полость сжатия винтового компрессора, отводит часть теплоты сжатия, и процесс сжатия становится политропным. Значение температуры нагнетания при этом находится в пределах 50…80°С и зависит от количества и температуры вспрыскиваемого масла. Для сравнения показано изображение адиабатического сжатия точки 2′ и 4′. После конденсатора КД жидкий холодильный агент состояния 5′ разделяется на два потока: меньшая часть дросселируется во вспомогательном регулирующем вентиле РВ1 (процесс 5′ — 6 ) и поступает в межзмеевиковое пространство ТО, большая часть жидкости идет по его змеевику, где переохлаждается (процесс 5′ — 7 ) в результате теплообмена с кипящим в межзмеевиковом пространстве при промежуточных параметрах РПР и tПР хладагентом, пар которого затем поступает в специальное окно компрессора. Состояние в точке 7 определяется из условий недорекуперации тепла на холодном конце теплообменника на 3…5°С, т. е. t7 = tПР + (3…5 °С). Переохлажденная жидкость дросселируется в основном регулирующем вентиле РВ2 и поступает в испаритель И. Таким образом, в данной схеме двухступенчатое сжатие рабочего вещества с промежуточным охлаждением за счет холодного пара, поступающего из теплообменника, происходит в одном компрессоре. Она отличается от обычной схемы двухступенчатого сжатия с однократным дросселированием и промежуточным отбором пара тем, что пар между ступенями сжатия в теплообменнике не охлаждается.
5.1.2. Принципиальная схема паровой холодильной машины и ее изображение в диаграмме
При описании принципа действия паровой холодильной машины различают теоретический и действительный циклы.
Теоретическим считается цикл, при котором пар хладагента из испарителя засасывается в компрессор в состоянии насыщения при температуре и давлении кипения, а жидкость из конденсатора поступает в регулирующий вентиль в состоянии насыщения при температуре и давлении конденсации. Кроме того, считается, что в системе нет потерь давления из-за сопротивления трубопроводов и аппаратов, а процесс сжатия в компрессоре — адиабатический (без теплообмена с окружающей средой).
Для эксплуатации холодильных установок интерес представляет действительный цикл холодильной машины, который и будет рассмотрен ниже.
На рис. 57 показаны принципиальная схема и цикл паровой холодильной машины, состоящей из четырех основных элементов, которые соединены трубопроводами в замкнутую герметичную систему. В основе искусственного охлаждения лежит процесс кипения хладагента в испарителе И, в результате чего он превращается из жидкости в пар и поглощает определенное количество теплоты от объекта охлаждения. По техническим требованиям необходимо, чтобы хладагент имел постоянную и строго определенную температуру кипения t0, что достигается поддержанием в испарителе определенного и постоянного давления кипения P0. Кроме того, t0 хладагента должна быть ниже конечной температуры охлаждаемого объекта.
Пар, образующийся в результате кипения, отсасывается из испарителя компрессором КМ. В теоретическом цикле считается, что из испарителя в компрессор поступает насыщенный пар, в действительности из испарителя может поступать влажный, насыщенный или перегретый пар, в зависимости от интенсивности теплопритока к испарителю и количества находящегося в нем жидкого хладагента. Во всасывающем трубопроводе перед компрессором пар дополнительно перегревается за счет теплопритока от окружающего воздуха и поступает в компрессор в перегретом состоянии. Перегрев пара перед компрессором несколько снижает эффективность работы установки, но является необходимой мерой для защиты компрессора от работы в режиме «влажного хода» и связанного с этим явлением гидравлического удара. В компрессоре пар сжимается, t и Р его повышаются, и горячий пар высокого давления нагнетается через нагнетательный трубопровод в конденсатор КД.
В конденсаторе пар хладагента в результате конденсации снова превращается в жидкость, и цикл становится замкнутым. При этом теплота от хладагента отводится в конденсаторе водой или воздухом. Хладагент охлаждается до температуры насыщения и конденсируется при постоянных температуре tк и давлении конденсации Рк.
В теоретическом цикле из конденсатора в регулирующий вентиль РВ поступает насыщенная жидкость. В действительном цикле в РВ может поступать как насыщенная, так и переохлажденная жидкость, которая дополнительно переохлаждается в самом конденсаторе либо в специальных аппаратах. В любом случае переохлаждение является положительным процессом, так как при этом увеличивается холодопроизводительность установки. Жидкость с высоким давлением в насыщенном или переохлажденном состоянии поступает к РВ, где дросселируется в проходном сечении соответствующего размера от Рк до Р0.
При дросселировании температура хладагента снижается до t0 за счет мгновенного испарения части жидкости. Теплота испарения отводится от остальной массы хладагента, температура которого снижается. Так как теплота отводится и передается внутри системы, без теплообмена с окружающей средой, то теплосодержание (энтальпия) вещества в процессе дросселирования остается постоянным. Поскольку часть жидкости испаряется, то после РВ хладагент представляет собой парожидкостную смесь (влажный пар). Парообразование при дросселировании называют дроссельными потерями, поскольку, попадая затем вместе с жидкостью в испаритель, пар не производит в нем эффекта охлаждения. Регулирующий вентиль предназначен не только для дросселирования хладагента, но и для регулирования его подачи в испаритель.
Холодильную систему можно условно разделить на два участка, давления хладагента в которых разные. Сторона высокого давления начинается от нагнетательной полости компрессора, проходит через конденсатор и заканчивается в регулирующем вентиле. Все трубопроводы и сосуды, находящиеся на этом участке установки, относятся к стороне высокого давления. Манометры, установленные на аппаратах и трубопроводах высокого давления, показывают Рк (или Р нагнетания). Сторона низкого давления начинается от РВ, проходит через испаритель и заканчивается во всасывающей полости компрессора. Все трубопроводы и сосуды, находящиеся в этой части системы, относятся к стороне низкого давления. Мановакуумметры, установленные на них, показывают Р0 или РBC.
Для построения рабочего цикла в диаграмме обычно задаются конкретными параметрами, а именно:
t0 — температурой кипения;
tк — температурой конденсации;
tBС — температурой всасывания;
tП — температурой переохлаждения.
Этих параметров достаточно для построения на диаграмме полного цикла холодильной машины. Прежде всего следует определить по диаграмме (см. рис. 53) Р0 и Рк по соответствующим температурам и провести на диаграмме две горизонтальные прямые — изобары Рк и Р0 (рис. 57).
Пересечение изобары давления кипения Р0 с кривой насыщенного пара показывает состояние хладагента на выходе из испарителя (точка 1» на диаграмме). Перегрев пара во всасывающем трубопроводе перед компрессором происходит при Р0 до tВС. Поэтому точка всасывания 1 лежит на пересечении изобары Р0 и изотермы tВС в области перегретого пара. При сжатии в компрессоре давление пара повышается до Рк, а сам процесс сжатия считается адиабатическим, поэтому точка конца сжатия 2 лежит на пересечении адиабаты, проведенной из точки 1, и изобары Рк. Температуру этой точки называют температурой нагнетания компрессора. Из компрессора перегретый пар поступает в конденсатор, где сначала охлаждается до состояния насыщения (точка 2»), а затем конденсируется при постоянной температуре до состояния насыщенной жидкости (точка 3′). Если в цикле имеет место переохлаждение жидкости, то состояние хладагента определяется в точке пересечения изобары Рк и изотермы tП в области переохлажденной жидкости (точка 3). Переохлажденная или насыщенная жидкость поступает в РВ и дросселируется до давления кипения Р0 при i = const. Линии изоэнтальпий проходят вертикально, поэтому точку 4 (5) — состояние перед испарителем — находят как пересечение вертикали, опущенной из точки 3 (3′) и изобары Р0. В состоянии влажного пара 4 (5) хладагент поступает в испаритель, где кипит при постоянных температуре и давлении кипения до состояния насыщенного пара (точка 1»). На этом цикл замыкается и повторяется. Таким образом, действительный цикл холодильной машины состоит из отдельных, следующих друг за другом процессов:
1» — 1 — перегрев пара на всасывании в компрессор при Р0 = const;
1 — 2 — адиабатическое сжатие в компрессоре от Р0 до Рк при S = const;
2 — 2» — сбив перегрева в конденсаторе при Рк = const;
2» — 3′ — конденсация пара в конденсаторе при Рк = const, tк = const;
3′ — 3 — переохлаждение жидкости в конденсаторе или ином аппарате при Рк = const;
3 — 4 — дросселирование в регулирующем вентиле от Рк до Р0 при t = const;
4 —1» — кипение жидкости в испарителе при Р0 = const и t0 = const.
Соответствующие точки цикла расставлены на схеме. После построения цикла холодильной машины в диаграмме можно определить все термодинамические параметры каждой точки цикла. На практике интерес представляют узловые точки, проставленные на диаграмме и схеме.
Зная параметры узловых точек цикла, можно определить следующие показатели:
удельную холодопроизводительность хладагента, кДж/кг, q0 = i1» — i4;
удельную работу сжатия в компрессоре, кДж/кг, l = i2 — i1 ;
удельную тепловую нагрузку на конденсатор, кДж/кг, qк = i2 — i3(3′) ; в зависимости от того, где происходит переохлаждение;
холодильный коэффициент цикла ε = q0/l = (i1» — i4) / (i2 — i1).
Холодильный коэффициент цикла — это КПД цикла, который выражается в виде отношения поглощенной от охлаждаемого объекта теплоты к энергии, израсходованной при этом компрессором. Чем больше е, тем выше эффективность цикла.
Пример. Определить параметры узловых точек цикла для аммиака при t0 = — 10 °С, tк = +30°С, tВС = 0°С, tП0 = +25°С и основные показатели цикла.
Определяем параметры узловых точек по диаграмме:
q0 = i1» — i4 = 1670 — 530 = 1140 кДж/кг;
l = i2 — i1 = 1900 — 1693 = 207 кДж/кг;
qк = i2 — i3 = 1900 — 530 = 1370 кДж/кг;
ε = q0/l = 1370/207 = 6,61.
Параметры узловых точек после построения цикла в диаграмме сведены в табл. 48.
Схемы автоматизации холодильных установок
Холодильные машины и установки могут быть автоматизированы частично или полностью. Частично автоматизированные установки требуют постоянного присутствия обслуживающего персонала и его активного участия в управлении. В полностью автоматизированных установках обслуживающий персонал только наблюдает за их работой.
В схемах автоматизации холодильных установок применяют помимо описанных систем регулирования, защиты и сигнализации следующие виды автоматического управления: пуск агрегатов в заданной последовательности; автоматическое включение рассольных насосов, вентиляторов воздухоохладителей, вентилей и задвижек с электроприводом;
полуавтоматическое управление, при котором после автоматического выключения машин приборами защиты и регулирования их включение производится вручную;
дистанционное управление отдельными узлами и механизмами со щита управления.
На рис. 100 показана расстановка средств автоматизации в схеме аммиачной двухступенчатой холодильной машины.
Рис. 100. Принципиальная схема аммиачной двухступенчатой холодильной машины с элементами автоматизации:
МО — маслоотделитель, ОК — обратный клапан, РТ — реле температуры, РД — реле давления, СВ — соленоидный вентиль, ПС — промежуточный сосуд, РУ — регулятор уровня, ОЖ — отделитель жидкости, КМНС и КМВС — компрессоры низкой и высокой ступени, РР — реле расхода, РКС — реле контроля смазки, РВ — регулирующий вентиль, Д — двигатель, ПР — поплавковый регулятор
Объектами регулирования в таких машинах являются: заполнение испарителей и ресиверов; температура испарения; температура конденсации, проток воды; давление масла; уровень в промсосуде.
Холодильные турбоагрегаты выпускают с автоматическим регулированием холодопроизводительности в зависимости от изменений тепловой нагрузки. Работа отдельных узлов турбоагрегата также автоматизирована. Подача хладагента в испарители с одновременным дросселированием производится поплавковым регулирующим вентилем ПРВ, получающим импульс от поплавкового датчика.
В большинстве случаев в системе смазки турбокомпрессоров имеются два насоса с приводом от разных источников — рабочий, приводимый в движение от вала машины или сети переменного тока, и резервный, работающий на постоянном токе (от аккумуляторной батареи или от выпрямителя тока). При пуске машины автоматически включается пусковой насос, и лишь после того, как он создаст необходимое давление, включается двигатель компрессора. Когда машина разовьет полное число оборотов, пусковой насос автоматически выключается и смазка начинает подаваться рабочим насосом.
Автоматизируются и другие элементы, обеспечивающие безопасную работу турбокомпрессоров: противопомпажная защита, защита двигателя от перегрузки и других нарушений режима, создающих аварийную ситуацию. Турбокомпрессоры оборудуются также устройствами автоматического выключения при чрезмерном увеличении давления нагнетания, недопустимом падении давления смазки, перегреве подшипников и сильном падении температуры кипения хладагента. Для этого в различных точках турбоагрегатов ставятся специальные датчики. Импульсы от них передаются на реле, срабатывание которого приводит к остановке агрегата.
Автоматическая противоаварийная защита поршневого компрессора включает защиту от попадания жидкого хладагента во всасывающий трубопровод компрессора и от недопустимых отклонений параметров компрессоров от нормальных рабочих значений.
Защиту от попадания жидкого хладагента во всасывающий трубопровод компрессора обеспечивает автоматический контроль уровней в аппаратах стороны низкого давления; при достижении недопустимых уровней предусматривается аварийная остановка компрессоров и подача сигнала в схему автоматизации.
Защита компрессора одноступенчатого сжатия от недопустимых отклонений рабочих параметров должна предусматривать отключение его электродвигателя при отклонениях ниже допустимого значения давления всасывания и разности давлений в системе смазки, выше допустимого значения давления нагнетания и температуры нагнетания, а также при прекращении протока воды через охлаждающие рубашки компрессора.
Защита компрессора двухступенчатого сжатия должна предусматривать отключение компрессора при отклонениях ниже допустимого значения: давления всасывания низкой ступени, разности давлений в системе смазки; выше допустимого значения: давлений нагнетания низкой и высокой ступеней, температур нагнетания низкой и высокой ступеней, уровня жидкого хладагента в промежуточном сосуде, а также при прекращении протока воды через охлаждающие рубашки компрессора.
Система автоматической защиты не должна допускать самозапуск машины до устранения причины, вызвавшей срабатывание защиты.
Автоматизация работы испарительного узла имеет целью регулирование заполнения испарителей жидким хладагентом, автоматическое регулирование температуры хладоносителя, управление работой насосов для его циркуляции, а также защиту испарителей от замерзания хладоносителя.
Система автоматизации конденсаторной группы предусматривает: контроль за уровнем жидкого хладагента в линейном ресивере, управление работой водяных насосов, регулирование уровня воды в бассейнах или резервуарах, управление вентиляторами испарительных конденсаторов и вентиляторных градирен.