Схема сварочного полуавтомата своими руками
Среди большого количества различных решений создания самодельных полуавтоматов, предложенная схема сварочного полуавтомата своими руками выглядит наиболее
интересной. Сварочный полуавтомат предназначен для мастеров, предпочитающих выполнять кузовной ремонт своих автомобилей самостоятельно.
Полуавтомат изготовлен для работы с подачей проволоки для сварки в автоматическом режиме в среде углекислого газа. Учитывая, что основная цель применения полуавтомата, это сварка кузовных деталей, которые имеют небольшую толщину. Тонкий металл предпочтительнее всего сваривать очень быстрым воздействием нагрева точки сварки. При этом работать нужно аккуратно, чтобы кузовные детали не успели подвергнуться деформации или же деформируются, но в очень малой степени.
Это очень важно при работе с кузовными деталями. Металл прогревается незначительно и если это не новый металл, а ремонтируемые детали кузова, то и краска выгорает незначительно.
Ускоряется и сам процесс ремонта кузова, благодаря быстрому расплавлению электродной проволоки, плюс к этому сварочный шов получается более качественным. Важно при этом и то, что нет необходимости очень точно подгонять детали перед произведением сварочных работ. Даже если свариваемые детали будут иметь разную толщину, то качество шва при этом не пострадает. Немаловажно и то, что по сравнению с ацетиленом или кислородом, углекислый газ не так дефицитен.
Освоить работу на таком полуавтомате можно очень быстро.
Особенности самодельного сварочного полуавтомата
Так как схема сварочного полуавтомата своими руками предлагает его работу с помощью углекислого газа, то при работе возникает одна проблема. Углекислый газ, с одной стороны, выполняет защиту ванну расплавленного металла от воздействия кислорода, действующего как окислитель металла.
Для защиты расплавленного металла от кислорода в полуавтомате применяется омедненная специальная проволока, в состав которой входит кремний и марганец. Диаметр проволоки может применяться, в зависимости от толщины металла свариваемых деталей, различного диаметра, это – 0.8, 1.0 и 1.2мм.
Базой для этого полуавтомата является мощный трансформатор, работающий от сети 220 В. Мощность трансформатора подобрана порядка 2.5-3 кВт.
Автор использовал для сборки распространенные детали автомобилей. Это двигатель для подачи проволоки, где применен электродвигатель от автомобиля «Камаз» с питанием на 24В и потребляемым током в районе 3А. От вазовской «восьмерки» взят клапан подачи воды к очистителю ветрового стекла, который в полуавтомате выполняет роль газового клапана. Сам держатель от обычного промышленного сварочного полуавтомата.
Читайте также
Схема управления электродвигателем подачи проволоки.
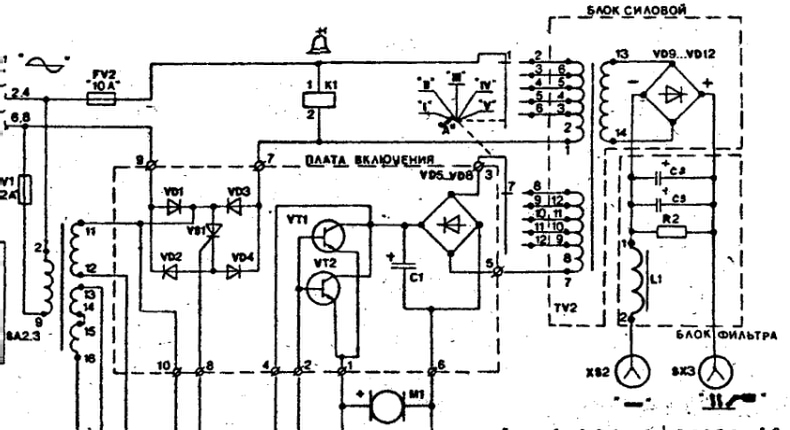
Некоторые задумываются над тем, что не стоит покупать дорогие сварочные установки, когда их можно собрать своими руками. При этом такие установки могут работать не хуже заводских и иметь достаточно хорошие качественные показатели. К тому же при поломке такого агрегата есть возможность самостоятельно и быстро устранить поломку. Но для того чтобы собрать такой прибор, следует хорошенько ознакомиться с основными принципами работы и составными элементами полусварочного автомата.
Трансформатор полусварочного автомата
В первую очередь необходимо определиться с типом сварочного полуавтомата и его мощностью. Мощность полуавтомата будет определяться работой трансформатора. Если в сварочном аппарате будут использоваться нити с диаметром в 0,8 мм, то ток, протекающий в них, может быть на уровне 160 ампер. Сделав некоторые подсчеты, принимаем решение сделать трансформатор с мощностью 3000 Ватт.
Если применять наиболее популярный Ш-образный сердечник, то полуавтомат станет значительно тяжелее, что будет являться минусом для сварочного аппарата в целом, который понадобится постоянно переносить на разные объекты. Для того чтобы сделать трансформатор с мощностью 3 киловатта, вам потребуется намотать обмотку на кольцевом магнитопроводе. Первоначально следует намотать первичную обмотку, которая начинается с напряжения в 160 B с шагом в 10 В и заканчивается на 240 В. При этом провод должен быть сечением не меньше 5 кв. мм.
После того как завершено наматывание первичной обмотки, следует поверх нее намотать и вторую, но на этот раз надо использовать проволоку с сечением 20 кв.мм. Значение напряжения на данной обмотке будет на показании в 20 В. Путем такого создания можно обеспечить 6 ступеней регулировки тока, один режим стандартной работы трансформатора и два типа пассивной работы трансформатора.
Регулировка полусварочного автомата
На сегодняшний день существует 2 вида регулировки тока по трансформатору: на первичной и вторичной обмотке. Первая — это регулировка тока на первичной обмотке, осуществляется при помощи тиристорной схемы, которая зачастую имеет множество недостатков. Одним из таких является периодическое повышение пульсации сварочного аппарата и переход фаз у такой схемы из тиристора в первичную обмотку. Регулировка тока по вторичной обмотке также имеет ряд недостатков при применении тиристорной схемы.
Для того чтобы их устранить, придется применять компенсирующие материалы, которые сделают сборку значительно дороже, да и к тому же аппарат станет значительно тяжелее. Проанализировав все эти факторы, можно прийти к выводу, что регулировку тока следует производить по первичной обмотке, а выбор схемы, которую следует применить, остается за создателем. Для обеспечения нужной регулировки по вторичной обмотке нужно установить сглаживающий дроссель, который будет сочетаться с конденсатором емкостью в 50 мФ. Эту установку следует делать вне зависимости от применяемой вами схемы, что обеспечит эффективную и бесперебойную работу сварочного автомата.
Регулировка подачи сварочной проволоки
Как и во многих других сварочных аппаратах, здесь лучше всего применять широтно-импульсную модуляцию с регуляцией обратной связи. Что дает ШИМ? Данный тип модуляции позволит нормализовать скорость проволоки, которая будет настраиваться и устанавливаться в зависимости от трения, которое создается проволокой и посадкой аппарата. При этом стоит выбор между подпиткой ШИМ-регулятора, которая может осуществляться путем отдельной намотки или же питать его от отдельного трансформатора.
При последнем варианте получится более дорогая схема, но эта разница в стоимости будет незначительной, но в то же время аппарат немного прибавит в весе, что является значительным минусом. Поэтому лучше всего применить первый вариант. Но если необходимо сваривать крайне аккуратно, на маленьком токе, то, следовательно, напряжение и ток, проходящие в проволоке, будут такие же маленькие.
Тем самым дополнительная обмотка может в полной мере удовлетворить потребности потенциального пользователя в максимальном значении тока. Ознакомившись с данной теорией, можно сделать вывод, что установка дополнительного трансформатора является лишней затратой денег, а нужный режим можно всегда поддерживать дополнительной обмоткой.
Подсчеты диаметра ведущего колеса для механизма подачи сварочной проволоки
Путем практики было определено, что скорость размотки сварочной проволоки может достигать значения от 70 сантиметров до 11 метров в минуту, при диаметре самой проволоки в 0,8 мм. Придаточное значение и скорость вращения деталей нам неизвестна, поэтому следует вести подсчеты по имеющимся данным по скорости разматывания. Для этого лучше всего сделать небольшой эксперимент, после выполнения которого есть возможность определить нужное количество оборотов. Включите аппаратуру на полную мощность и подсчитайте, какое количество оборотов она делает за минуту.
Чтобы точно уловить оборот, закрепите спичку или ленту на якорь, чтобы знать, где закончился и начался круг. После того как ваши расчеты сделаны, вы можете узнать радиус по знакомой со школы формуле: 2пиR=L, где L-длина круга, то есть, если аппарат сделает 10 оборотов, необходимо поделить 11 метров на 10, и получится размотка в 1.1 метр. Это и будет длиной размотки. R — радиус якоря, его и надо подсчитать. Число «пи» должно быть известно со школы, его значение равно 3,14. Приведем пример. Если насчитали 200 оборотов, то путем расчета определяем число L=5.5 cм. Далее делаем подсчет R=5.5/3.14*2= 0.87 см. Итак, необходимый радиус будет составлять 0,87 см.
Функциональность полусварочного автомата
Лучше всего делать его с минимальным набором функций, такими как:
- Первоначальная подача углекислого газа в трубку, что позволит сначала наполнить трубку газом и лишь потом подводить искру.
- После того как нажали кнопку, следует подождать около 2 секунд, после чего автоматически включается подача проволоки.
- Одновременное отключение тока с подачей проволоки, когда отпускаете кнопку управления.
- После всего проделанного выше необходимо с задержкой в 2 секунды прекратить подачу газа. Это делается для того, чтобы не позволить окислиться металлу после остывания.
Для того чтобы собрать двигатель подачи сварочной проволоки, можно применить редуктор стеклоочистителя от многих отечественных автомобилей. При этом не забывайте о том, что минимальное количество проволоки, которое должно выматываться за минуту, составляет 70 сантиметров, а максимальное — 11 метров. Этими значениями необходимо руководствоваться при выборе якоря для выматывания проволоки.
Клапан для подачи газа лучше всего выбрать среди механизмов подачи воды все из тех же отечественных автомобилей. Но очень важно следить за тем, чтобы данный клапан по истечении некоторого времени не начал пускать утечку, что очень опасно. Если выберете все верно и правильно, аппарат при нормальном режиме работы сможет прослужить около 3 лет, при этом не надо будет много раз ремонтировать его, так как он достаточно надежен.
Сварочный полуавтомат: схема
Схема сварочного полуавтомата обеспечивает все пункты функциональности и сделает сварочный полуавтомат очень удобным в работе. Для того чтобы установить ручной режим, реле переключателя SB1 должно быть замкнутым. После того как нажали на кнопку управления SA1, задействуете переключатель К2, который при помощи своих связей К2.1 и К2.3 включит первый и третий ключ.
Далее первый ключ задействует подачу углекислого газа, при этом ключ К1.2 начинает включать цепи питания сварочного полуавтомата, а К1.3 — полностью выключает тормоз двигателя. При этом во время этого процесса реле К3 начинает проводить процесс взаимодействия со своими контактами К3.1, который своим действием отключает цепь питания двигателя, а К3.2 разгибает К5. К5 в разомкнутом состоянии обеспечивает задержку включения аппарата на две секунды, которые нужно подобрать при помощи резистора R2. Все данные действия происходят с выключенным двигателем, и лишь газ подается в трубку. После всего этого второй конденсатор своим импульсом отключает второй ключ, который служит для задержки подачи тока сварки. После чего и начинается сам процесс сварки. Обратный процесс при отпускании SB1 аналогичен первому, при этом обеспечивается задержка в 2 секунды на отключение подачи газа сварочного полуавтомата.
Обеспечение автоматического режима сварочного полуавтомата
Для начала следует ознакомиться, для чего же нужен автоматический режим. Например, необходимо приварить прямоугольный пласт металлического сплава, при этом работа должна быть идеально ровной и симметричной. Если будете использовать ручной режим, то пластина по краям будет иметь шов с различной толщиной. Это вызовет дополнительные сложности, так как будет необходимо выравнивать его до нужного размера.
Если использовать автоматический режим, то тут возможности немного возрастают. Для этого необходимо настроить время сварки и силу тока, после чего попробуйте свою сварку на каком-либо ненужном объекте. После проверки можно удостовериться, что шов подходит для сварки конструкции. После снова включаем нужный режим и начинаем сварку вашего металлического листа.
При включении автоматического режима задействуете все ту же кнопку SA1, которая будет проводить все процессы подобно ручной сварке, с одним только несоответствием, что для ввода в работу потребуется не удерживать данную кнопку, а все включение будет обеспечиваться цепочкой С1R1. На полную работоспособность такого режима потребуется от 1 до 10 секунд. Работа данного режима очень проста, для этого необходимо нажимать кнопку управления, после чего включается сварка.
После того как время, заданное резистором R1, будет пройдено, сварочный аппарат сам выключит пламя.
часть также нередко дают сбои .
Неисправность этого узла приводит к существенным сбоям в работе с полуавтоматом, потере рабочего времени и нервотрепкой с заменой сварочной проволоки. Проволока на выходе из наконечника прихватывается, приходится снимать наконечник и чистить контактную часть для проволоки. Неисправность наблюдается при любом диаметре применяемой сварочной проволоки. Либо может происходить большая подача, когда проволока при нажатии на клавишу включения выходит большими порциями.
Неисправности вызваны часто и самой механической частью регулятора подачи проволоки. Схематично механизм состоит из прижимного ролика с регулируемой степенью прижима проволоки, подающий ролик с двумя канавками для проволоки 0.8 и 1.0 мм. За регулятором смонтирован соленоид, отвечающий за перекрытие подачи газа с задержкой 2 секунды.
Сам регулятор подачи очень массивный и часто просто закреплен на передней панели полуавтомата на 3-4 болтиках, по сути вися в воздухе. Это приводит к перекосам всей конструкции и частым сбоям в работе. Собственно «вылечить» этот недостаток довольно просто, установив под регулятором подачи проволоки какую-либо подставку, тем самым зафиксировав его в рабочем положении.
На полуавтоматах заводского изготовления в большинстве случаев (не зависимо от производителя) углекислый газ подается к соленоиду по сомнительному тонкому шлангу в виде кембрика, который от холодного газа просто «дубеет» и затем трескается. Это также вызывает остановку работы и требует ремонта. Мастера исходя из своего опыта советуют заменять этот шланг подачи, автомобильным шлангом, применяемым для подачи тормозной жидкости от бачка к главному цилиндру тормозов. Шланг прекрасно выдерживает давление и будет служить неограниченное время.
Промышленность выпускает полуавтоматы со сварочным током порядка 160 А. Этого бывает достаточно при работе с автомобильным железом, которое достаточно тонкое – 0,8-1.0мм. Если же приходится сваривать, например элементы из 4 мм стали, то этого тока недостаточно и провар деталей не полный. Многие мастера для этих целей приобретают инвертор, который вкупе с полуавтоматом может выдавать до 180А, чего вполне достаточно для гарантированного сварного шва деталей.
Многие пытаются своими руками, путем экспериментов, устранить эти недостатки и сделать работу полуавтомата более стабильной. Предложено достаточно много схем и возможных доработок механической части.
Одно из таких предложений. Это, доработанный и проверенный в работе регулятор скорости подачи проволоки сварочного полуавтомата схема предложена на интегральном стабилизаторе 142ЕН8Б. Благодаря предложенной схеме работы регулятора подачи проволоки выполняет задержку подачи на 1-2 секунды после срабатывания клапана газа и максимально возможное по быстроте срабатывания ее торможение в момент отпускания кнопки включения.
Минусом схемы является приличная мощность отдаваемая транзистором, разогревая радиатор охлаждения в работе до 70 градусов. Но все это плюсуется надежной работой как самого регулятора скорости подачи проволоки, так и всего полуавтомата в целом.
Технические данные нашего сварочного аппарата — полуавтомата:
Напряжение питающей сети: 220 В
Потребляемая мощность: не более 3 кВа
Режим работы: повторно-кратковременный
Регулирование рабочего напряжения: ступенчатое от 19 В до 26 В
Скорость подачи сварочной проволоки: 0-7 м/мин
Диаметр проволоки: 0.8 мм
Величина сварочного тока: ПВ 40% — 160 А, ПВ 100% — 80 А
Предел регулирования сварочного тока: 30 А — 160 А
Всего с 2003 года было сделано шесть подобных аппаратов. Аппарат, представленный далее на фото, работает с 2003 года в автосервисе и ни разу не подвергался ремонту.
Внешний вид сварочного полуавтомата
Вообще
Вид спереди
Вид сзади
Вид слева
В качестве сварочной проволоки используется стандартная
5кг катушка проволоки диаметром 0,8мм
Сварочная горелка 180 А вместе с евроразъемом
была куплена в магазине сварочного оборудования.
Схема и детали сварочника
Ввиду того что схема полуавтомата анализировалась с таких аппаратов как ПДГ-125, ПДГ-160, ПДГ-201 и MIG-180, принципиальная схема отличается от монтажной платы, т. к. схема вырисовывалась на лету в процессе сборки. Поэтому лучше придерживаться монтажной схемы. На печатной плате все точки и детали промаркированы (откройте в Спринте и наведите мышку).
Вид на монтаж
Плата управления
В качестве выключателя питания и защиты применен однофазный автомат типа АЕ на 16А. SA1 — переключатель режимов сварки типа ПКУ-3-12-2037 на 5 положений.
Резисторы R3, R4 — ПЭВ-25, но их можно не ставить (у меня не стоят). Они предназначены для быстрой разрядки конденсаторов дросселя.
Теперь по конденсатору С7. В паре с дросселем он обеспечивает стабилизацию горения и поддержания дуги. Минимальная емкость его должна быть не менее 20000 мкф, оптимальная 30000 мкф. Были испробованы несколько типов конденсаторов с меньшими габаритами и большей емкостью, например CapXon, Misuda, но они себя проявили не надежно, выгорали.
В итоге были применены советские конденсаторы, которые работают по сей день, К50-18 на 10000 мкф х 50В в количестве трёх штук в параллель.
Силовые тиристоры на 200А взяты с хорошим запасом. Можно поставить и на 160 А, но они будут работать на пределе, потребуется применение хороших радиаторов и вентиляторов. Примененные В200 стоят на не большой алюминиевой пластине.
Реле К1 типа РП21 на 24В, переменный резистор R10 проволочный типа ППБ.
При нажатии на горелке кнопки SB1 подается напряжение на схему управления. Срабатывает реле К1, тем самым через контакты К1-1 подается напряжение на электромагнитный клапан ЭМ1 подачи кислоты, и К1-2 — на схему питания двигателя протяжки проволоки, и К1-3 — на открытие силовых тиристоров.
Переключателем SA1 выставляют рабочее напряжение в диапазоне от 19 до 26 Вольт (с учетом добавки 3 витков на плечо до 30 Вольт). Резистором R10 регулируют подачу сварочной проволоки, меняют ток сварки от 30А до 160 А.
При настройке резистор R12 подбирают таким образом, чтобы при выкрученном R10 на минимум скорости двигатель все же продолжал вращаться, а не стоял.
При отпускании кнопки SB1 на горелке — реле отпускает, останавливается мотор и закрываются тиристоры, электромагнитный клапан за счет заряда конденсатора С2 еще продолжает оставаться открытым подавая кислоту в зону сварки.
При закрытии тиристоров исчезает напряжение дуги, но за счет дросселя и конденсаторов С7 напряжение снимается плавно, не давая сварочной проволоке прилипнуть в зоне сварки.
Мотаем сварочный трансформатор
Берем трансформатор ОСМ-1 (1кВт), разбираем его, железо откладываем в сторону, предварительно пометив его. Делаем новый каркас катушки из текстолита толщиной 2 мм, (родной каркас слишком слабый). Размер щеки 147×106мм. Размер остальных частей: 2 шт. 130×70мм и 2 шт. 87×89мм. В щеках вырезаем окно размером 87×51,5 мм.
Каркас катушки готов.
Ищем обмоточный провод диаметром 1,8 мм, желательно в усиленной, стекловолоконной изоляции. Я взял такой провод со статорных катушек дизель-генератора). Можно применить и обычный эмальпровод типа ПЭТВ, ПЭВ и т. п.
Стеклоткань — на мой взгляд, самая лучшая изоляция получается
Начинаем намотку — первичка. Первичка содержит 164 + 15 + 15 + 15 + 15 витков. Между слоями делаем изоляцию из тонкой стеклоткани. Провод укладывать как можно плотнее, иначе не влезет, но у меня обычно с этим проблем не было. Я брал стеклоткань с останков всё того же дизель-генератора. Все, первичка готова.
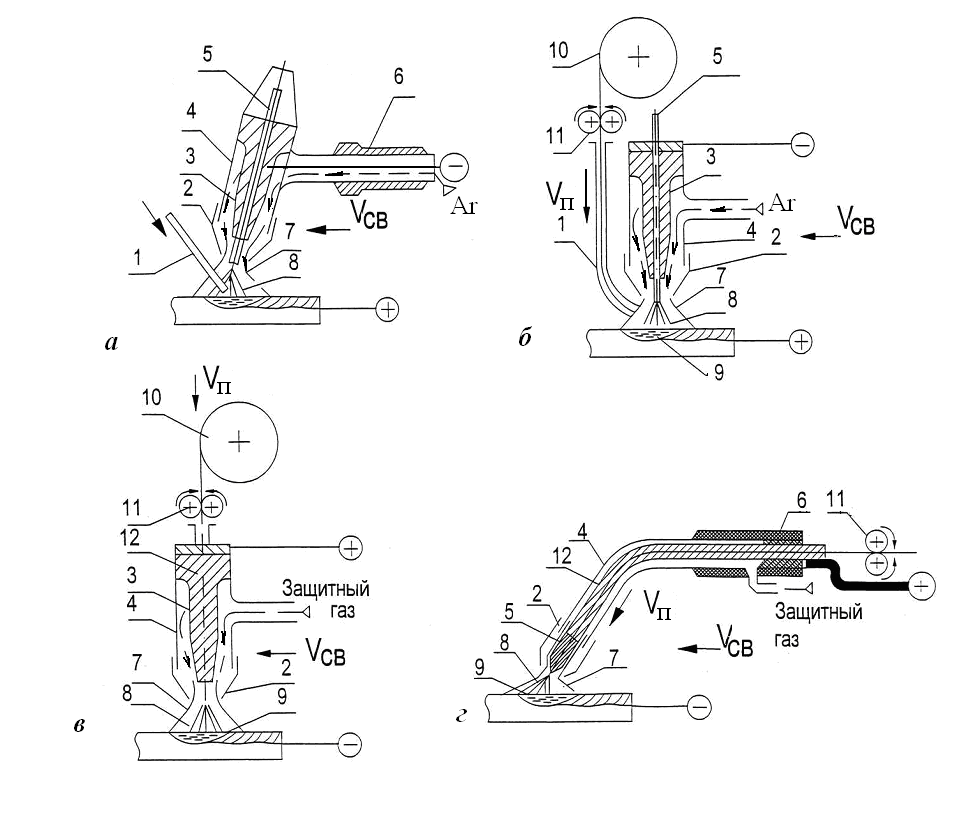
Продолжаем мотать — вторичка. Берем алюминиевую шину в стеклянной изоляции размером 2,8×4,75 мм, (можно купить у обмотчиков). Нужно примерно 8 м, но лучше иметь небольшой запас. Начинаем мотать, укладывая как можно плотнее, мотаем 19 витков, далее делаем петлю под болт М6, и снова 19 витков, Начала и концы делаем по 30 см, для дальнейшего монтажа.
Тут небольшое отступление, лично мне для сварки крупных деталей при таком напряжении было маловато току, в процессе эксплуатации я перемотал вторичную обмотку, прибавив по 3 витка на плечо, итого у меня получилось 22+22.
Обмотка влезает впритык, поэтому если мотать аккуратно, все должно получиться.
Если на первичку брать эмальпровод, то потом обязательно пропитка лаком, я держал катушку в лаке 6 часов.
Собираем трансформатор, включаем в розетку и замеряем ток холостого хода около 0,5 А, напряжение на вторичке от 19 до 26 Вольт. Если все так, то трансформатор можно отложить в сторону, он пока нам больше не нужен.
Вместо ОСМ-1 для силового трансформатора можно взять 4шт ТС-270, правда там немного другие размеры, и я делал на нем только 1 сварочный аппарат, то данные для намотки уже не помню, но это можно посчитать.
Будем мотать дроссель
Берем трансформатор ОСМ-0,4 (400Вт), берем эмальпровод диаметром не менее 1,5 мм (у меня 1,8). Мотаем 2 слоя с изоляцией между слоями, укладываем плотненько. Дальше берем алюминиевую шину 2,8×4,75 мм. и мотаем 24 витка, свободные концы шины делаем по 30 см. Собираем сердечник с зазором 1 мм (проложить кусочки текстолита).Дроссель также можно намотать на железе от цветного лампового телевизора типа ТС-270. На него ставится только одна катушка.
У нас остался еще один трансформатор для питания схемы управления (я брал готовый). Он должен выдавать 24 вольта при токе около 6А.
Корпус и механика
С трансами разобрались, приступаем к корпусу. На чертежах не показаны отбортовки по 20 мм. Углы свариваем, все железо 1,5 мм. Основание механизма сделано из нержавейки.
Мотор М применен от стеклоочистителя ВАЗ-2101.
Убран концевик возврата в крайнее положение.
В подкатушечнике для создания тормозного усилия применена пружина, первая попавшаяся под руку. Тормозной эффект увеличивается сжиманием пружины (т. е. закручиванием гайки).
В продаже можно увидеть множество сварочных полуавтоматов отечественного и зарубежного производства используемые при ремонте кузовов автомобилей.
При желании можно сэкономить на расходах, собрав сварочный полуавтомат в гаражных условиях.
В комплект сварочного аппарата входит корпус, в нижней части которого устанавливается силовой трансформатор однофазного или трёхфазного исполнения, выше располагается устройство протяжки сварочной проволоки.
В состав устройства входит электродвигатель постоянного тока с передаточным механизмом понижения оборотов, как правило здесь используется электродвигатель с редуктором от стеклоочистителя а/м УАЗ или «Жигули». Стальная проволока с медным покрытием с подающего барабана проходя через вращающиеся ролики поступает в шланг для подачи проволоки, на выходе проволока входит в контакт с заземлённым изделием, возникающая дуга сваривает металл. Для изоляции проволоки от кислорода воздуха сварка происходит в среде инертного газа. Для включения газа установлен электромагнитный клапан. При использовании прототипа заводского полуавтомата в них выявлены некоторые недостатки, препятствующие качественному проведению сварки: преждевременный выход от перегрузки из строя выходного транзистора схемы регулятора оборотов электродвигателя; отсутствие в бюджетной схеме автомата торможения двигателя по команде остановки – сварочный ток при отключении пропадает, а двигатель продолжает подавать проволоку некоторое время, это приводит к перерасходу проволоки, опасности травматизма, необходимости удаления лишней проволоки специальным инструментом.
В лаборатории «Автоматики и телемеханики» Иркутского областного Центра ДТТ разработана более современная схема регулятора подачи проволоки, принципиальное отличие которой от заводских – наличие схемы торможения и двукратный запас коммутационного транзистора по пусковому току с электронной защитой.
Характеристики устройства:
2. Мощность электродвигателя – до 100 ватт.
3. Время торможения 0,2 сек.
4. Время пуска 0,6 сек.
5. Регулировка оборотов 80 %.
6. Ток пусковой до 20 ампер.
В состав принципиальной схемы регулятора подачи проволоки входит усилитель тока на мощном полевом транзисторе. Стабилизированная цепь установки оборотов позволяет поддерживать мощность в нагрузке независимо от напряжения питания электросети, защита от перегрузки снижает подгорание щёток электродвигателя при пуске или заедании в механизме подачи проволоки и выход из строя силового транзистора.
Схема торможения позволяет почти мгновенно остановить вращение двигателя.
Напряжение питания используется от силового или отдельного трансформатора с потребляемой мощностью не ниже максимальной мощности электродвигателя протяжки проволоки.
В схему введены светодиоды индикации напряжения питания и работы электродвигателя.
Напряжение с регулятора оборотов электродвигателя R3 через ограничительный резистор R6 поступает на затвор мощного полевого транзистора VT1. Питание регулятора оборотов выполнено от аналогового стабилизатора DA1, через токоограничительный резистор R2. Для устранения помех, возможных от поворота ползунка резистора R3, в схему введён конденсатор фильтра C1.
Светодиод HL1 указывает на включенное состояние схемы регулятора подачи сварочной проволоки.
Резистором R3 устанавливается скорость подачи сварочной проволоки в место дуговой сварки.
Подстроечный резистор R5 позволяет выбрать оптимальный вариант регулирования оборотов вращения двигателя в зависимости от его модификации мощности и напряжения источника питания.
Диод VD1 в цепи стабилизатора напряжения DA1 защищает микросхему от пробоя при неверной полярности питающего напряжения.
Полевой транзистор VT1 оснащён цепями защиты: в цепи истока установлен резистор R9, падение напряжения на котором используется для управления напряжением на затворе транзистора, с помощью компаратора DA2. При критическом токе в цепи истока напряжение через подстроечный резистор R8 поступает на управляющий электрод 1 компаратора DA2, цепь анод-катод микросхемы открывается и снижает напряжение на затворе транзистора VT1, обороты электродвигателя М1 автоматически снизятся.
Для устранения срабатывания защиты от импульсных токов, возникающих при искрении щёток электродвигателя, в схему введен конденсатор C2.
К стоковой цепи транзистора VT1 подключен электродвигатель подачи проволоки с цепями снижения искрения коллектора С3,С4, С5. Цепь состоящая из диода VD2 с нагрузочным резистором R7 устраняет импульсы обратного тока электродвигателя.
Двухцветный светодиод HL2 позволяет контролировать состояние электродвигателя, при зелёном свечении – вращение, при красном свечении – торможение.
Схема торможения выполнена на электромагнитном реле К1. Ёмкость конденсатора фильтра С6 выбрана небольшой величины – только для снижения вибраций якоря реле К1, большая величина будет создавать инерционность при торможении электродвигателя. Резистор R9 ограничивает ток через обмотку реле при повышенном напряжении источника питания.
Принцип действия сил торможения, без применения реверса вращения, заключается в нагрузке обратного тока электродвигателя при вращении по инерции, при отключении напряжения питания, на постоянный резистор R8. Режим рекуперации – передачи энергии обратно в сеть позволяет в короткое время остановить мотор. При полной остановке скорость и обратный ток установятся в ноль, это происходит почти мгновенно и зависит от значения резистора R11 и конденсатора C5. Второе назначение конденсатора С5 – устранение подгорания контактов К1.1 реле К1. После подачи сетевого напряжения на схему управления регулятора, реле К1 замкнёт цепь К1.1 питания электродвигателя, протяжка сварочной проволоки возобновится.
Источник питания состоит из сетевого трансформатора T1 напряжением 12-15 вольт и ток 8-12 ампер, диодный мост VD4 выбран на 2х-кратный ток. При наличии на сварочном трансформаторе полуавтомата вторичной обмотки соответствующего напряжения, питание выполняется от неё.
Схема регулятора подачи проволоки выполнена на печатной плате из одностороннего стеклотекстолита размером 136*40 мм, кроме трансформатора и мотора все детали установлены с рекомендациями по возможной замене. Полевой транзистор установлен на радиатор размерами 100*50 *20.
Полевой транзистор аналог IRFP250 с током 20-30 Ампер и напряжением выше 200 Вольт. Резисторы типа МЛТ 0,125, R9,R11,R12 – проволочные. Резистор R3,R5 установить типа СП-3 Б. Тип реле К1 указан на схеме или №711.3747-02 на ток 70 Ампер и напряжение 12 Вольт, габариты у них одинаковые и применяются в автомобилях «ВАЗ».
Компаратор DA2, при снижении стабилизации оборотов и защиты транзистора, из схемы можно удалить или заменить на стабилитрон КС156А. Диодный мост VD3 можно собрать на российских диодах типа Д243-246, без радиаторов.
Компаратор DA2 имеет полный аналог TL431 CLP иностранного производства.
Электромагнитный клапан подачи инертного газа Em.1 – штатный, на напряжение питания 12 вольт.
Наладку схемы регулятора подачи проволоки сварочного полуавтомата начинают с проверки питающего напряжения. Реле К1 при появлении напряжения должно срабатывать, обладая характерным пощелкиванием якоря.
Повышая регулятором оборотов R3 напряжение на затворе полевого транзистора VT1 проконтролировать, чтобы обороты начинали расти при минимальном положении движка резистора R3, если этого не происходит минимальные обороты откорректировать резистором R5 – предварительно движок резистора R3 установить в нижнее положение, при плавном увеличении номинала резистора К5, двигатель должен набрать минимальные обороты.
Защита от перегрузки устанавливается резистором R8 при принудительном торможении электродвигателя. При закрытии полевого транзистора компаратором DA2 при перегрузке светодиод HL2 потухнет. Резистор R12 при напряжении источника питания 12-13 Вольт из схемы можно исключить.
Схема опробована на разных типах электродвигателей, с близкой мощностью, время торможения в основном зависит от массы якоря, ввиду инерции массы. Нагрев транзистора и диодного моста не превышает 60 градусов Цельсия.
Печатная плата закрепляется внутри корпуса сварочного полуавтомата, ручка регулятора оборотов двигателя – R3 выводится на панель управления вместе с индикаторами: включения HL1 и двуцветного индикатора работы двигателя HL2. Питание на диодный мост подается с отдельной обмотки сварочного трансформатора напряжением 12-16 вольт. Клапан подачи инертного газа можно подключить к конденсатору C6, он также будет включаться после подачи сетевого напряжения. Питание силовых сетей и цепей электродвигателя выполнить многожильным проводом в виниловой изоляции сечением 2,5-4 мм. кв.
В продаже можно увидеть множество сварочных полуавтоматов отечественного и зарубежного производства используемые при ремонте кузовов автомобилей. При желании можно сэкономить на расходах, собрав сварочный полуавтомат в гаражных условиях.
В комплект сварочного аппарата входит корпус, в нижней части которого устанавливается силовой трансформатор однофазного или трёхфазного исполнения, выше располагается устройство протяжки сварочной проволоки.
В состав устройства входит электродвигатель постоянного тока с передаточным механизмом понижения оборотов, как правило здесь используется электродвигатель с редуктором от стеклоочистителя а/м УАЗ или «Жигули». Стальная проволока с медным покрытием с подающего барабана проходя через вращающиеся ролики поступает в шланг для подачи проволоки, на выходе проволока входит в контакт с заземлённым изделием, возникающая дуга сваривает металл. Для изоляции проволоки от кислорода воздуха сварка происходит в среде инертного газа. Для включения газа установлен электромагнитный клапан. При использовании прототипа заводского полуавтомата в них выявлены некоторые недостатки, препятствующие качественному проведению сварки: преждевременный выход от перегрузки из строя выходного транзистора схемы регулятора оборотов электродвигателя; отсутствие в бюджетной схеме автомата торможения двигателя по команде остановки — сварочный ток при отключении пропадает, а двигатель продолжает подавать проволоку некоторое время, это приводит к перерасходу проволоки, опасности травматизма, необходимости удаления лишней проволоки специальным инструментом.
В лаборатории «Автоматики и телемеханики» Иркутского областного Центра ДТТ разработана более современная схема регулятора подачи проволоки, принципиальное отличие которой от заводских — наличие схемы торможения и двукратный запас коммутационного транзистора по пусковому току с электронной защитой.
Характеристики устройства:
1. Напряжение питания 12-16 вольт.
2. Мощность электродвигателя — до 100 ватт.
3. Время торможения 0,2 сек.
4. Время пуска 0,6 сек.
5. Регулировка оборотов 80 %.
6. Ток пусковой до 20 ампер.
В состав принципиальной схемы регулятора подачи проволоки входит усилитель тока на мощном полевом транзисторе. Стабилизированная цепь установки оборотов позволяет поддерживать мощность в нагрузке независимо от напряжения питания электросети, защита от перегрузки снижает подгорание щёток электродвигателя при пуске или заедании в механизме подачи проволоки и выход из строя силового транзистора.
Схема торможения позволяет почти мгновенно остановить вращение двигателя.
Напряжение питания используется от силового или отдельного трансформатора с потребляемой мощностью не ниже максимальной мощности электродвигателя протяжки проволоки.
В схему введены светодиоды индикации напряжения питания и работы электродвигателя.
Напряжение с регулятора оборотов электродвигателя R3 через ограничительный резистор R6 поступает на затвор мощного полевого транзистора VT1. Питание регулятора оборотов выполнено от аналогового стабилизатора DA1, через токоограничительный резистор R2. Для устранения помех, возможных от поворота ползунка резистора R3, в схему введён конденсатор фильтра C1.
Светодиод HL1 указывает на включенное состояние схемы регулятора подачи сварочной проволоки.
Резистором R3 устанавливается скорость подачи сварочной проволоки в место дуговой сварки.
Подстроечный резистор R5 позволяет выбрать оптимальный вариант регулирования оборотов вращения двигателя в зависимости от его модификации мощности и напряжения источника питания.
Диод VD1 в цепи стабилизатора напряжения DA1 защищает микросхему от пробоя при неверной полярности питающего напряжения.
Полевой транзистор VT1 оснащён цепями защиты: в цепи истока установлен резистор R9, падение напряжения на котором используется для управления напряжением на затворе транзистора, с помощью компаратора DA2. При критическом токе в цепи истока напряжение через подстроечный резистор R8 поступает на управляющий электрод 1 компаратора DA2, цепь анод-катод микросхемы открывается и снижает напряжение на затворе транзистора VT1, обороты электродвигателя М1 автоматически снизятся.
Для устранения срабатывания защиты от импульсных токов, возникающих при искрении щёток электродвигателя, в схему введен конденсатор C2.
К стоковой цепи транзистора VT1 подключен электродвигатель подачи проволоки с цепями снижения искрения коллектора С3,С4, С5. Цепь состоящая из диода VD2 с нагрузочным резистором R7 устраняет импульсы обратного тока электродвигателя.
Двухцветный светодиод HL2 позволяет контролировать состояние электродвигателя, при зелёном свечении — вращение, при красном свечении — торможение.
Схема торможения выполнена на электромагнитном реле К1. Ёмкость конденсатора фильтра С6 выбрана небольшой величины — только для снижения вибраций якоря реле К1, большая величина будет создавать инерционность при торможении электродвигателя. Резистор R9 ограничивает ток через обмотку реле при повышенном напряжении источника питания.
Принцип действия сил торможения, без применения реверса вращения, заключается в нагрузке обратного тока электродвигателя при вращении по инерции, при отключении напряжения питания, на постоянный резистор R8. Режим рекуперации — передачи энергии обратно в сеть позволяет в короткое время остановить мотор. При полной остановке скорость и обратный ток установятся в ноль, это происходит почти мгновенно и зависит от значения резистора R11 и конденсатора C5. Второе назначение конденсатора С5 — устранение подгорания контактов К1.1 реле К1. После подачи сетевого напряжения на схему управления регулятора, реле К1 замкнёт цепь К1.1 питания электродвигателя, протяжка сварочной проволоки возобновится.
Источник питания состоит из сетевого трансформатора T1 напряжением 12-15 вольт и ток 8-12 ампер, диодный мост VD4 выбран на 2х-кратный ток. При наличии на сварочном трансформаторе полуавтомата вторичной обмотки соответствующего напряжения, питание выполняется от неё.
Схема регулятора подачи проволоки выполнена на печатной плате из одностороннего стеклотекстолита размером 136*40 мм, кроме трансформатора и мотора все детали установлены с рекомендациями по возможной замене. Полевой транзистор установлен на радиатор размерами 100*50 *20.
Полевой транзистор аналог IRFP250 с током 20-30 Ампер и напряжением выше 200 Вольт. Резисторы типа МЛТ 0,125, R9,R11,R12 — проволочные. Резистор R3,R5 установить типа СП-3 Б. Тип реле К1 указан на схеме или №711.3747-02 на ток 70 Ампер и напряжение 12 Вольт, габариты у них одинаковые и применяются в автомобилях «ВАЗ».
Компаратор DA2, при снижении стабилизации оборотов и защиты транзистора, из схемы можно удалить или заменить на стабилитрон КС156А. Диодный мост VD3 можно собрать на российских диодах типа Д243-246, без радиаторов.
Компаратор DA2 имеет полный аналог TL431 CLP иностранного производства.
Электромагнитный клапан подачи инертного газа Em.1 — штатный, на напряжение питания 12 вольт.
Наладку схемы регулятора подачи проволоки сварочного полуавтомата начинают с проверки питающего напряжения. Реле К1 при появлении напряжения должно срабатывать, обладая характерным пощелкиванием якоря.
Повышая регулятором оборотов R3 напряжение на затворе полевого транзистора VT1 проконтролировать, чтобы обороты начинали расти при минимальном положении движка резистора R3, если этого не происходит минимальные обороты откорректировать резистором R5 — предварительно движок резистора R3 установить в нижнее положение, при плавном увеличении номинала резистора К5, двигатель должен набрать минимальные обороты.
Защита от перегрузки устанавливается резистором R8 при принудительном торможении электродвигателя. При закрытии полевого транзистора компаратором DA2 при перегрузке светодиод HL2 потухнет. Резистор R12 при напряжении источника питания 12-13 Вольт из схемы можно исключить.
Схема опробована на разных типах электродвигателей, с близкой мощностью, время торможения в основном зависит от массы якоря, ввиду инерции массы. Нагрев транзистора и диодного моста не превышает 60 градусов Цельсия.
Печатная плата закрепляется внутри корпуса сварочного полуавтомата, ручка регулятора оборотов двигателя — R3 выводится на панель управления вместе с индикаторами: включения HL1 и двуцветного индикатора работы двигателя HL2. Питание на диодный мост подается с отдельной обмотки сварочного трансформатора напряжением 12-16 вольт. Клапан подачи инертного газа можно подключить к конденсатору C6, он также будет включаться после подачи сетевого напряжения. Питание силовых сетей и цепей электродвигателя выполнить многожильным проводом в виниловой изоляции сечением 2,5-4 мм. кв.
Список радиоэлементов
Обозначение | Тип | Номинал | Количество | Примечание | Магазин | Мой блокнот |
---|---|---|---|---|---|---|
DA1 | Линейный регулятор | MC78L06A | 1 | В блокнот | ||
DA2 | Микросхема | КР142ЕН19 | 1 | В блокнот | ||
VT1 | MOSFET-транзистор | IRFP260 | 1 | В блокнот | ||
VD1 | Диод | КД512Б | 1 | В блокнот | ||
VD2 | Выпрямительный диод | 1N4003 | 1 | В блокнот | ||
VD3 | Диодный мост | KVJ25M | 1 | В блокнот | ||
С1, С2 | 100мкФ 16В | 2 | В блокнот | |||
С3, С4 | Конденсатор | 0.![]() | 2 | на 63В | В блокнот | |
С5 | Электролитический конденсатор | 10 мкФ | 1 | на 25В | В блокнот | |
С6 | Электролитический конденсатор | 470мкФ | 1 | на 25В | В блокнот | |
R1, R2, R4, R6, R10 | Резистор | 1.2 кОм | 4 | 0,25Вт | В блокнот | |
R3 | Переменный резистор | 3.3 кОм | 1 | В блокнот | ||
R5 | Подстроечный резистор | 2.2 кОм | 1 | В блокнот | ||
R7 | Резистор | 470 Ом | 1 | 0,25Вт | В блокнот | |
R8 | Подстроечный резистор | 6.![]() | 1 | В блокнот | ||
R9 | Резистор прецизионный |
РадиоКот :: Сварочный полуавтомат 30А
РадиоКот >Схемы >Аналоговые схемы >Бытовая техника >Сварочный полуавтомат 30А — 160А
Ввиду того что схема полуавтомата анализировалась с таких аппаратов как ПДГ-125, ПДГ-160, ПДГ-201 и MIG-180, принципиальная схема отличается от монтажной платы, т. к. схема вырисовывалась на лету в процессе сборки. Поэтому лучше придерживаться монтажной схемы. На печатной плате все точки и детали промаркерованы.
В качестве выключателя питания и защиты применен однофазный автомат типа АЕ на 16А. SA1 -переключатель режимов сварки типа ПКУ-3-12-2037 на 5 положений. Резисторы R3, R4 — ПЭВ-25, но их можно не ставить, (у меня не стоят) предназначены для быстрой разрядки конденсаторов дросселя. Теперь по конденсатору С7, В паре с дросселем он обеспечивает стабилизацию горения и поддержания дуги, минимальная емкость должна быть не менее 20000мкф, оптимальная — 30000мкф. Были применены наши советские конденсаторы К50-18 на 10000х50в в количестве 3 штук в параллель.
Силовые тиристоры взяты с запасом на 200А, хотя можно поставить и на 160 А, но они будут работать на пределе, и уже необходимо применение радиаторов и вентилятора. В200 стоят без радиаторов на не большой алюминиевой пластине.
Реле К1 типа РП21 на 24в, переменный резистор R10 проволочный типа ППБ, При нажатии кнопки SB1 на горелке подается напряжение на схему управления. Срабатывает реле К1, тем самым через контакты К1-1 подает напряжение на электромагнитный клапан ЭМ1 подачи кислоты, К1-2 — на схему питания двигателя протяжки проволоки, и К1-3 на открытие силовых тиристоров. Переключателем SA1 выставляют рабочее напряжение в диапазоне от 19 до 26 вольт ( с учетом добавки 3 витков на плечо до 30вольт). Резистором R10 регулируют подачу сварочной проволоки, тем самым меняя ток сварки от 30А до 160 А. При настройке резистор R12 подбирают таким образом, чтобы при выкрученном R10 на минимум скорости двигатель все же продолжал вращаться, а не стоял.
При отпускании кнопки SB1 горелки при размыкании контактов реле останавливается мотор, и закрываются тиристоры, электромагнитный клапан за счет заряда конденсатора С2 еще продолжает оставаться открытым подавая кислоту в зону сварки. При закрытии тиристоров исчезает напряжение дуги, но за счет дросселя и конденсаторов С7 напряжение снимается плавно не давая сварочной проволоке прилипнуть в зоне сварки.
Мотор М применен без переделок от стеклоочистителя ВАЗ-2101. Единственное что нужно сделать, так это убрать концевик возврата в крайнее положение.
Для подкатушечника для создания тормозного усилия применена пружина, первая попавшаяся под руку, Тормозной эффект увеличивается сжиманием пружины (т. е. закручиванием гайки )
Теперь по намотке трансформаторов.
Берем трансформатор ОСМ-1 (1кВт), разбираем его, железо откладываем в сторону, предварительно пометив его. Делаем новую катушку из текстолита толщиной 2мм, (родная слишком слабая) размер щеки 147х106мм. Размер остальных частей 2 шт 130х70мм и 2 шт 87х89мм. В щеках вырезаем окно размером 87х51,5мм
Все. катушка готова. Ищем провод желательно в стеклянной изоляции диаметром 1,8мм, (я взял с дизель-генератора статорные катушки). Но можно и обычный эмаль провод. (Стеклянный надежнее) Начинаем намотку.
Первичка содержит 164 + 15 + 15 + 15 + 15. Между слоями делаем изоляцию из тонкой стеклоткани. Провод укладывать как можно плотнее, иначе не влезет, но у меня обычно с этим проблем не было. (Я брал с того же дизель-генератора, там слюдованная стеклоткань, слюду соскабливаешь а саму стеклоткань расщепляешь на отдельные лоскуты, Кстати на мой взгляд самая лучшая изоляция получается.) Все, первичка готова.
Дальше берем алюминиевую шину в стеклянной изоляции размером 2,8х4,75мм, (Можно купить у обмотчиков) Нужно примерно 8м. может чуть больше, но лучше иметь небольшой запас. Начинаем мотать укладывая как можно плотнее, мотаем 19 витков, далее делаем петлю под болт М6, и снова 19 витков, Началы и концы делаем по 30см, для дальнейшего монтажа. ( тут небольшое отступление, лично мне для сварки крупных деталей при таком напряжении было маловато току, в процессе эксплуатации я перемотал вторичную обмотку прибавив по 3 витка на плечо, итого у меня получилось 22+22) Обмотка влезает только-только впритык, поэтому если мотать аккуратно, все должно получиться.
Если на первичку брать эмаль провод то потом обязательно пропитка лаком, ( я держал в лаке 6 часов)
Собираем трансформатор, включаем в розетку и замеряем, ток холостого хода около 0,5 А, напряжение на вторичке от 19 до 26 вольт. Если все так, то его можно отложить в сторону, он пока нам больше не нужен. Будем мотать дроссель.
Берем трансформатор ОСМ-0,4 (400Вт), берем эмаль провод диаметром не менее 1,5мм.( у меня 1,8) Мотаем 2 слоя с изоляцией между слоями, укладываем плотненько. Дальше берем алюминиевую шину 2,8х4,75мм. и мотаем 24 витка. концы шины делаем по 30см. Собираем трансформатор с зазором 1мм (куски текстолита). Дроссель также можно намотать на железе от цветного лампового телевизора, ТС-270) На нем ставится только одна катушка. Вместо ОСМ-1 для силового трансформатора можно взять 4шт ТС-270, правда там немного другие размеры, и я делал на нем только 1 аппарат, то данные для намотки уже не помню, но это можно посчитать. Ну и наконец у нас остался еще один трансформатор для питания схемы управления.(я брал готовый) Он должен выдавать 24 вольта при токе около 6А.
Чертежи корпуса в приложении, Лист перед и зад, на чертеже не показаны отбортовки по 20 мм, углы свариваем, все железо 1,5 мм. Основание механизма сделано из нержавейки.
Монтажная и принципиальная схема могут отличаться, придерживаться стоит монтажной схеме.
Файлы:
Дно и верх
Крышки
Основание механизма
Перед и зад
Перегородка
Подкатушечник
Протяжный механизм
Конденсатор
Плата полуавтомата
Плата управления
Подкатушечник
Подкатушечник в разобранном виде
Протяжка со снятым роликом
Протяжка в сборе
Силовой трансформатор с дросселем
Тиристоры
Вид на монтаж
Принципиальная схема
Все вопросы в
Форум.
Как вам эта статья? | Заработало ли это устройство у вас? |
Принципиальная схема и особенности полуавтоматической сварки
Современные производители выпускают много разного оборудования для сварки. Но, независимо от производителя и марок, принцип работы у всех полуавтоматов один: они дают сварочный ток, подают проволоку и регулируют поток газа.
Сварочные полуавтоматы бывают компактными или универсальными. У компактного устройства источник питания, управление и устройство подачи проволоки размещены в одном корпусе (рис. 37). Радиус действия равен длине пакета шлангов горелки и составляет 3–5 м в зависимости от диаметра используемого проволочного электрода. У универсального полуавтомата устройство подачи проволоки размещается отдельно в кожухе и связано с источником тока и устройством управления с помощью промежуточного кабеля. Его можно установить рядом с изделием, благодаря чему радиус действия увеличится на 10–20 м по сравнению с компактным устройством. Подающий проволоку механизм может быть тянущим, толкающим или универсальным, т. е. выполнять сразу две функции.
Рис. 37. Схема подключения сварочного полуавтомата:
1 – баллон с защитным газом; 2 – регулятор давления и расхода газа; 3 – рукав газовый; 4 – сварочный полуавтомат; 5 – сварочная проволока; 6 – пакет шлангов; 7 – горелка; 8 – провод массы с зажимом; 9 – изделие
Источник питания понижает высокое напряжение сети и обеспечивает подачу требуемого тока высокой силы даже в случае короткого замыкания. Так как при сварке MIG/MAG используется только постоянный ток, в качестве источников тока применяются только выпрямители и инверторы (принцип их действия был описан выше в главе «Источники сварочного тока»).
Для того чтобы соответствовать особым требованиям различных производственных задач, источники питания должны быть регулируемыми. У простых устройств для сварки MIG/MAG регулирование производится с помощью расположенного с первичной стороны трансформатора ответвления обмотки и переключателя ступеней обмоток трансформатора. В более дорогих источниках питания установка тока происходит в выпрямительной части с помощью управляемых вентилей (тиристоров). Некоторые аппараты сварки MIG/MAG оснащаются инверторами в качестве источников питания.
Качество сварки MIG/MAG в значительной мере зависит от правильности выбора режимов работы сварочного аппарата (напряжение дуги, ток – скорость подачи проволоки, скорость сварки), а также от правильности выбора и расхода защитного газа (скорость подачи газа через сопло). Для регулировки расхода защитного газа целесообразно использовать редукторы с расходомерами поплавкового вида.
В устройстве подачи проволоки проволочный электрод с помощью подающих роликов подается к месту сварки в соответствии со скоростью его расплавления. При этом электрод вытягивается с катушки и проводится по пакету шлангов, на конце которого расположена горелка. Для этого перед подающими роликами расположен направляющий мундштук, приводящий проволоку в нужное положение, а позади роликов, в начале пакета шлангов, – приемный мундштук для проволоки. Установки механизированной сварки оснащаются еще и промежуточным направляющим устройством, устраняющим предварительный изгиб проволоки, возникающий вследствие наматывания ее на катушку.
Подающие ролики приводятся в движение электродвигателем постоянного тока с плавно регулируемой установкой скорости вращения. В современных устройствах для регулируемой сварки скорость подачи проволоки измеряется тахометром и регулируется вне зависимости от нагрузки. При сварке MIG/MAG скорость подачи проволоки, как правило, составляет от 2 до 20 м/мин, а в высокопроизводительных аппаратах и больше.
В пакет шлангов входят все необходимые виды проводки, т. е. электропроводка, шланг для подачи защитного газа, шланг подачи проволоки, управляющая линия, а у устройств, рассчитанных на высокие значения силы тока, – также подача и отвод охлаждающей жидкости. У аппаратов с водяным охлаждением электропроводка находится в линии рециркуляции воды. Поэтому сечение проводки может быть меньше, чем в аппаратах без охлаждения, а пакет шлангов становится более гибким.
Шланг подачи проволоки при сварке нелегированных и низколегированных сталей представляет собой стальную спираль. При использовании проволочных электродов из хромоникелевой стали или из алюминия и других металлов для подачи используется шланг из износостойкого синтетического материала (например, тефлона) с лучшим коэффициентом трения, чем у стали.
Благодаря линии управления управляющие сигналы передаются от горелки к системе управления. Для этого на держателе горелки находится переключатель, с помощью которого можно управлять необходимыми при сварке функциями. Например, включать низкую скорость подачи проволочного электрода при зажигании и настройку времени затухания дуги при завершении сварки. Благодаря настраиваемой низкой скорости подачи проволочного электрода при зажигании процесс зажигания становится надежнее, так как еще слабо горящая дуга на холодном изделии не тушится быстро подаваемой проволокой.
Настраиваемое время затухания, т. е. отключение подачи проволоки чуть раньше, чем сварочного тока, предотвращает пригорание электрода в кратере в конце шва. Другая программа предотвращает образование слишком большой капли на конце проволоки при окончании сварки, которая могла бы помешать при новом зажигании. Есть возможность плавного пуска тока в начале и соответствующего понижения тока при окончании сварки.
На конце пакета шлангов находится сварочная горелка. Горелки выпускаются нескольких типов. Чаще всего применяют S-образные горелки (рис. 38). Они обладают небольшим весом, благодаря чему обеспечивается очень хороший доступ дуги к месту сварки. Вместо такой горелки можно приобрести горелку для скоростной сварки или сварочный пистолет (двухтактную горелку). Для цифровой сварочной установки производятся специальные горелки с жидкокристаллическим дисплеем и дистанционным регулятором, при работе с которыми можно считывать параметры сварочного процесса с дисплея и регулировать их с горелки. Бывают и горелки, непосредственно на которых расположена мини-катушка для очень мягкой и тонкой проволоки. Двигатель подачи проволоки у таких горелок находится в держателе.
Рис. 38. Горелка для сварки MIG/MAG:
а – общий вид S-образной горелки; б – сечение пакета шлангов; в – сечение головки; 1 – пакет шлангов; 2 – рукоятка; 3 – кнопка «Пуск»; 4 – гусак; 5 – сопло; 6 – сварочная проволока; 7 – спираль; 8 – силовой кабель; 9 – кабель управления; 10 – газовый шланг; 11 – изолятор; 12 – внешний диффузор; 13 – внутренний диффузор; 14 – защитный газ; 15 – наконечник
Как сделать сварочный полуавтомат — Легкое дело
Многие задаются вопросом, как же сделать сварочный полуавтомат своими руками и что бы он обладал хорошими характеристиками, имел достаточно функционала и работал надёжно долгие годы.
На в самом деле всё просто. Для этого нужно знать немного о принципе работы сварочного полуавтомата и немного терпения.
Итак начнем.
Для начала определимся с типом и мощностью сварочного трансформатора применяемого в сварочных полуавтоматах.
Как нам известно при использовании сварочной проволокой диаметром 0,8 мм сварочный ток достигает
160 ампер. Отсюда следует, что трансформатор должен быть мощностью от 3000 вт.
Далее определяемся с типом трансформатора. Самыми лучшими характеристика обладают сварочные трансформаторы намотанные на тороидальном сердечнике (кольцо, бублик, тор)
Выбираем этот тип сварочного трансформатора, в отличии от П и Ш образных трансформаторов при одинаковой мощности они имеют меньший вес, что важно для такой конструкции, как сварочный полуавтомат.
Далее определяемся с регулированием сварочного тока. Есть два способа регулирования, по первичной и вторичной обмотке сварочного трансформатора.
Регулирование сварочного тока по первичной обмотке трансформатора с использованием тиристорной схемы регулирования имеет ряд недостатков, такие как повышенная пульсация сварочного напряжения в момент перехода фаз через тиристоры в первичной обмотке. (лечится установкой дросселя и конденсатора большой емкости в цепь сварочного тока)
Регулирование тока по первичной обмотке с использованием коммутирующих элементов (реле, галетные переключатели) не имеет таких недостатков, как тиристорная схема управления, и предпочтительней для использования в подобных схемах сварочных аппаратов.
Регулирование тока по вторичной обмотке сварочного трансформатора имеет также повышенную пульсацию сварочного напряжения в схемах с применением тиристоров. Применение коммутирующих схем (переключатели, мощные реле) ведет к дороговизне элементов и утяжелении конструкции сварочного аппарата в целом.
Отсюда следует, что регулировку тока нужно реализовывать по первичной обмотке (какую именно, решать вам)
В цепи питания сварочной дуги (вторичная обмотка) нужно обязательно устанавливать сглаживающий сварочный дроссель и конденсатор повышенной емкости от 50000 Мкф. для сглаживания пульсаций сварочного тока, не зависимо от применяемой схемы регулирования сварочного напряжения.
Дальше определяемся с регулятором подачи сварочной проволоки. Для сварочного полуавтомата рекомендуется использовать ШИМ регулятор с обратной связью.
Для чего нужен ШИМ? Во первых он стабилизирует скорость проволоки(на заданном уровне) в зависимости от нагрузки оказываемой трением проволоки в рукаве и реагирует на просадку (уменьшение) сетевого напряжения во время сварки.
Откуда запитать ШИМ регулятор, от отдельного трансформатора или намотать дополнительную обмотку на сварочный трансформатор? Тут разницы особой нет, если запитывать от отдельного трансформатора, то это увеличит вес аппарата. А если намотать дополнительную обмотку на сварочный трансформатор, то вы выиграете в весе и немного с экономите.
Возьмем к примеру такую ситуацию, вы варите на самом маленьком токе, значит и скорость проволоки тоже маленькая и напряжение нужное для регулирования двигателя подачи проволоки тоже незначительное, если варите на максимальном токе, то и напряжение нужное для двигателя максимальное, тем самым намотав обмотку запитывающую цепь регулятора подачи проволоки на сварочном трансформаторе, мы обеспечим нужный режим работы для регулятора. И отсюда следует, что потребности в дополнительном трансформаторе для двигателя подачи сварочной проволоки нет.
Какой выбрать редуктор для подачи сварочной проволоки? Вариантов много, самый распространенный это редуктор стеклоочистителя от автомобилей семейства ВАЗ.
Расчет диаметра ведущего колеса механизма подачи сварочной проволоки. Как нам известно, что скорость подачи сварочной проволоки в сварочном аппарате должна быть в пределах 0,7…11 метров в минуту при сварке проволокой 0.8 мм .
Так как передаточное отношение выбранного редуктора и скорость вращения якоря двигателя нам не известна, нужно рассчитать диаметр ведущего колеса механизма подачи проволоки, что бы он обеспечивал необходимую скорость подачи проволоки.
Делается это опытным путем. На вал редуктора с помощью пластилина прикрепляется спичка. Потом на двигатель редуктора подается максимальное напряжение, которое выдает ШИМ регулятор, например 20 вольт. Подсчитываем количество оборотов, которые сделал двигатель за 1 минуту.
Например двигатель сделал 100 оборотов, подставив в формулу, мы рассчитаем нужный размер (радиус) ведомого колеса механизма подачи проволоки:
100 – количество оборотов двигателя, сделанных за 1 минуту.
1100 – 11 метров переведенные в см.
Или упрощенная формула для скорости 11 м/мин:
где N количество оборотов двигателя, сделанных за 1 минуту.
Таким образом у нас получилось, что радиус ведомого колеса равен 1.75 см или диаметр равен 3,5 см, при котором обеспечивается нужная максимальная скорость подачи проволоки (11 метров в минуту) при данном напряжении (20 вольт).
В качестве клапана газа для нашего сварочного аппарата. рекомендуем использовать клапан подачи воды на омыватель заднего стекла ВАЗ2108, так как он зарекомендовал себя очень надежным.
Каким должен быть функционал сварочного полуавтомата. Сварочный полуавтомат должен обязательно иметь самый минимум функций, а именно:
- при нажатии кнопки управления сначала должен податься углекислый газ, это делается для того, что бы горелка наполнилась газом.
- после задержки 1..3 секунды автоматически включается ток сварки и подача проволоки.
- после отпускания кнопки управления отключается подача проволоки и сварочный ток (одновременно).
- затем через 1…3 сек отключается подача углекислого газа, это нужно для того, что бы расславленный метал не окислился при остывании.
Как видите, из выше изложенного видно, что сварочный полуавтомат – это просто, было бы желание и возможность реализовать все это в домашних условиях.
P.S. На нашем сайте опубликовано много схем сварочных полуавтоматов. Все они разные и различаются по принципу регулирования сварочного тока, функциональности, простоте (сложности) повторения.
В связи с этим хотелось бы добавить, что каждый сам для себя может выбрать, что ему действительно нужно, и сделать, что то свое на основе приведенных здесь схем сварочных аппаратов.
Ответ на комментарий :
Регулятор подачи сварочной проволоки на TL494
Схема из журнала «Радиоаматор-Электрик» №3 2006 г. стр 28-29 Схема похоже не рабочая.
Схема торможения двигателя.
Реле К1 подключаем в цепь коммутации подачи проволоки.
Еще одна схема регулятора подачи проволоки на TL494 (доработанный вариант схемы из журнала «Радиоаматор-Электрик»)
Повторил эту схему. не работает. © Admin
У кого работает, пишите в комментарии.
31. Комментарий написал: Вова — 14.06.2011 в 5:12 Цитировать
Доброва времени суток недавно собирал регулятор оборотов для сварочного полуавтомата Широтно – Импульсный модулятор с обратной связю по току работает прекрасно под нагрузкой оборты не падают (чтобы не падали обороты нужно подобрать резистор р9)и соответствено выходной транзистор поставить на хароший радиатор с термопастой.Вот сылка на форум где я ево нарыл http://www.foar.ru/topic.php?forum=30&topic=5&p=1 .Удачи в повторении.
32. Комментарий написал: Вова — 14.06.2011 в 5:16 Цитировать
Да и ещо в место указаного транзистора ставил IRF640 тоже нормально работал все детали мне обошлись около 35 гривен дешево и по надежности хорошо .
33. Комментарий написал: Dev — 22.08.2011 в 18:02 Цитировать
А кто-нибудь пробовал использовать в качестве привода – шаговые двигатели? Думаю, какой выбрать. Основная характеристика как мне видится – крутящий момент, хватит ли 6 кг/см?
34. Комментарий написал: idea — 12.09.2011 в 16:10 Цитировать
народ помогите! хочу собрать углекислотку на основе инвертора
есть инвертор ARC160, рукав, балон с редуком, протяжку сделаю из механизма дворников.
хочется иметь универсал — отсоединил и пошол варить электродами +сэкономить финансы
вопрос получится ли добиться жосткой характеристики (сеичас круто падающая)
если поставить кандеры?
протяжку клапан и кандеры если да то поставлю в отдельную коробку
35. Комментарий написал: Botos — 10.11.2011 в 21:02 Цитировать
Доброва времени суток недавно собирал регулятор оборотов для сварочного полуавтомата Широтно – Импульсный модулятор с обратной связю по току работает прекрасно под нагрузкой оборты не падают (чтобы не падали обороты нужно подобрать резистор р9)и соответствено выходной транзистор поставить на хароший радиатор с термопастой. Вот сылка на форум где я ево нарыл http://www.foar.ru/topic.php?forum=30&topic=5&p=1.Удачи в повторении.
А какой номинал р9 для мотора от жигулёского стеклоочистителя?
36. Комментарий написал: Botos — 04.12.2011 в 21:37 Цитировать
Собрал сегодня схему но регулирует напряжение только до 17 вольт.Как сделать регулировку до 25 вольт?
37. Комментарий написал: admin — 05.12.2011 в 16:37 Цитировать
Botos
Собирал 2 схемы на TL494 и ни одна как положено не работала.
Возможно нужно прибавить сопротивление переменного резистора, также поиграться с номиналами R14, C13, С15
С13 у вас 100n? Может по запарке 10n поставили.
Если поможет, напишите какие номиналы установили.
38. Комментарий написал: Сергей — 16.03.2012 в 17:02 Цитировать
Здравствуйте! Имеется 3х фазный сварочный полуавтомат, как известно в 3х фазных сварочных аппаратах применяют питание без рабочего нуля. Вопрос, как мне подключить диодные мосты кврс5010, если имеется только подвод фаз. Заранее благодарен
39. Комментарий написал: Вова — 20.04.2012 в 6:16 Цитировать
Всем добрый вечер скажыте кто делал ету схему и укаво есть печатка тоже хочу сделать)))
40. Комментарий написал: admin — 20.04.2012 в 21:00 Цитировать
41. Комментарий написал: Вова — 26.04.2012 в 2:34 Цитировать
42. Комментарий написал: and — 05.05.2012 в 2:23 Цитировать
В цепи питания сварочной дуги (вторичная обмотка) нужно обязательно устанавливать сглаживающий сварочный дроссель и конденсатор повышенной емкости от 50000 Мкф. для сглаживания пульсаций сварочного тока, не зависимо от применяемой схемы регулирования сварочного напряжения Это всё есть в любом трансформаторном сварочнике для ручной дуговой (ДУГА-315например)как переделать?
43. Комментарий написал: admin — 05.05.2012 в 19:11 Цитировать
and
Что передалать, во что?
44. Комментарий написал: and — 06.05.2012 в 1:45 Цитировать
ДУГА-315напримерв полуавтомат,или тут тема другая?
45. Комментарий написал: admin — 06.05.2012 в 2:07 Цитировать
and
Тема та, только я не могу вам посоветовать что и как переделывать, потому что эту дугу315 я в глаза не видел, понимаете?
46. Комментарий написал: and — 11.05.2012 в 5:13 Цитировать
Понимаю,но в любом сварочном аппарате постоянного тока,это всё есть-сглаживающий сварочный дроссель и конденсатор ,но не варит.
47. Комментарий написал: александр — 04.06.2012 в 4:52 Цитировать
возвращаясь к регулятору РА-ЭЛЕКТРИК 2006 N3 стр28 то мной он был повторен,двигатель шел рывками пока я неизменил кондер толи с4 толи с2,было давно непомню причем уменьшил намного.Подобрал и дело пошло ,стабилизация отличная.напряжение питания 28в-непревышать так как вылетает кп103. поэтому рекомендую питать от отдельного транса.схема работает с 2008 г по сей день
48. Комментарий написал: admin — 04.06.2012 в 15:21 Цитировать
александр
Сколько я не пытался запустить этот регулятор так и не получилось. Возможно микросхема была не исправной. В общем больше не возвращался к этой схеме.
49. Комментарий написал: belopolyy — 10.08.2012 в 22:02 Цитировать
Собрал больше двух десятков схем управления двигателем из журнала Радиоаматор-электрик. Первая не заработала. Устранил неточности, теперь всё ОК.
50. Комментарий написал: admin — 10.08.2012 в 23:47 Цитировать
belopolyy
Какие схемы и какие не точности?
http://svapka.ru/sampoluavtom/kak-sdelat-svarochnyj-poluavtomat-net-ni-chego-proshhe.htm
Автоматическая сварка — обзор
Те, кто читал эту главу, возможно, пришли к выводу, что ручная сварка TIG считалась лучшей за рассматриваемый период. Нет ничего более далекого от правды. На протяжении более двадцати лет участок сварки труб на верфи Барроу стремится получить подходящий и надежный комплект оборудования для автоматической орбитальной сварки труб. Многие поставщики предложили оборудование, которое, по их мнению, подходило для судостроительных целей, но большинство из них не соответствовало особым требованиям, предъявляемым к изготовлению трубопроводов для судов.
Испытания и развитие оборудования
Первые работы по установке оборудования для орбитальной сварки проводились на участке разработки сварки труб на судостроительном заводе Виккерс в начале 1970-х годов. К сожалению, конструкция и / или характеристики оборудования оказались в значительной степени неадекватными для производственного использования, особенно там, где были условия строго ограниченного доступа, рис. 5.5 и 5.6.
5.5. Головка для орбитальной сварки Astromatic AM11 показывает требуемый чрезмерный радиальный зазор и несбалансированное распределение веса.
5.6. Головка для орбитальной сварки с указанием необходимого радиального зазора.
Совсем недавно Vickers приобрела три станка новейшей конструкции с самыми компактными размерами, доступными на момент покупки, и охватывающими диапазон диаметров 3–220 мм. Оборудование может использоваться с присадочной проволокой или без нее и обеспечивает плавную регулировку силы тока от 8 до 250 А, возможность дистанционного управления, автоматическое регулирование расхода и пульсирование тока. Колебания горелки не предусмотрены, что может вызвать некоторые проблемы с трубами большего размера.
Когда машина была куплена, было известно, что французские военно-морские верфи используют этот тип оборудования для сварки труб из нержавеющей стали малого диаметра. Кроме того, в то время как ранее мы искали комплект для автоматической сварки труб для стыковых сварных швов среднего размера, 76–200 мм, акцент начал меняться, поскольку мы столкнулись с потребностью в стыковой сварке труб в диапазоне 20–200 мм. 38 мм, которые ранее были соединены с помощью механических муфт или сварных швов. Кроме того, введение клапанов того же размера, которые можно было ремонтировать на месте, привело к большему количеству стыковой сварки и меньшему количеству механических соединений.Эти два изменения касались материала медного сплава, который не является самым простым материалом для сварки в фиксированном положении — конечно, в другой категории по сравнению с нержавеющей сталью, свариваемой французами.
Первоначальные процедурные работы были выполнены на диаметре 33,4, стенке 4,5 мм для корневого проплавления, как аутогенных сварных швов, так и со вставками из ЭП. Это было связано с тем, что многие из уже имеющихся в наличии фитингов были подготовлены со стандартом V для ручной сварки, а предыдущие работы показали, что упрощенная подготовка к сварке с 2.Толщина носа 5 мм, дает приемлемые результаты без использования расходной вставки. Были выполнены работы с диаметром 21,3 мм и стенкой 3,7 мм, процедуры были одобрены заказчиком.
Затем возникла проблема, которая вернула программу процедуры к исходному состоянию. Когда машины 2 и 3 были установлены на значения, используемые на машине 1, которая использовалась для выполнения разработки процедуры, ни одна из них не дала приемлемого сварного шва. Фактически, не было никакого сравнения настроек трех машин для достижения успешных сварных швов.После нескольких дней, проведенных в Барроу, пытаясь откалибровать машины в допустимых пределах, все машины были возвращены поставщику.
После этой первоначальной проблемы были снова выполнены процедурные испытания, и все машины были утверждены с аналогичными настройками; После утверждения процедуры две машины регулярно работали в производственном цехе с показателем успеха 99%. Конечно, уместно отметить, что только 44% сварных швов, выполненных с момента внедрения оборудования, были выполнены из-за доступности.Используемая сварочная головка требует длины поперечного прямого участка 55–60 мм и минимального радиального зазора 57 мм. Это дает некоторое представление о доступности сварных швов даже для заводских сборочных работ. По результатам проведенных исследований ожидается, что примерно 20% сварных швов будет доступно на борту судов класса, строящегося в настоящее время.
Дальнейшие разработки привели к утвержденным процедурам для трубопровода из низкоуглеродистой стали с малым внутренним диаметром, и было показано, что трубы из монеля и медно-никелевого сплава 70/30 аналогичного размера можно сваривать с использованием одних и тех же параметров.
Несмотря на то, что блоки присадочной проволоки были приобретены вместе с оборудованием, раннее использование показало, что согласованность не может быть гарантирована, поэтому было принято решение сначала принять корневую сварку с помощью автоматических машин и продолжить ручное заполнение TIG.
Последние модификации, выполненные в отделе разработки, привели к значительному повышению производительности устройств подачи проволоки, а также были проведены процедурные работы в отношении нержавеющей и низкоуглеродистой стали.
Как выбрать типы сварочных аппаратов
Устройство и работа.
Сварочный аппарат — это электрическое устройство, с помощью которого выполняется сварка. Именно этот процесс обеспечивает долговечное и надежное крепление металлических деталей. С помощью сварки выполняется огромное количество работ в самых разных областях, начиная от микроэлектроники и заканчивая созданием многотонных конструкций.
Среди основных преимуществ электросварки — надежное и быстрое соединение материалов при минимальных затратах.
При необходимости с помощью этого приспособления можно даже резать металл.В последние десятилетия они производятся с использованием электронных компонентов.
Благодаря этому были значительно уменьшены их вес и габариты, что позволило расширить область их применения.
Типы и типыСварочное оборудование отличается большим разнообразием, что обусловлено постоянным развитием сварочного производства, созданием новых технологий и способов сварки.
Исходя из конструктивных особенностей, в том числе принципа действия устройств, можно выделить следующие типы:
Выпрямитель сварочный.Он оснащен блоком полупроводниковых диодов, в результате чего ток переходит из переменного в постоянный.
Основные преимущества — минимальное разбрызгивание, качественная сварка швов. Применяется для сварки черных и цветных металлов, чугуна, алюминия, стали.
Сварочный трансформатор. Работает благодаря переменному току. Есть несколько типов — с повышенным и стандартным магнитным рассеянием. Процесс сварки довольно трудоемок из-за большого веса.
Сварочный полуавтомат . Применяется для сварочных работ в газовой отрасли. Сварочный инвертор. Это легкие и компактные установки.
Аппарат для аргонодуговой сварки.
Оборудование для сварки плавлением недрагоценных металлов может выполнять следующие операции: Fusion
- Дуговая сварка и наплавка.
- Газовая сварка.
- Электрошлаковая сварка и наплавка.
- Электронно-лучевая сварка.
- Наплавка и резка.
- Специальные виды сварки.
По степени механизации сварочные аппараты могут быть:
- Ручные.
- Полуавтомат.
Сварочные аппараты классифицируются следующим образом:
- Предметы обихода: Отличаются низкой производительностью, не приспособлены к длительной работе. Однако сфера их применения очень широка, такой агрегат применяется для сварки арок, котлов, труб и так далее;
- Professional: Отличаются большим весом и габаритами, работают от сети 220 или 380 Вт.Большинство этих моделей оснащено специальными колесами для облегчения передвижения. Они используются во многих областях строительства, в мастерских, при установке газопроводов, на заводах и т. Д.
Устройство каждой модели инвертора может иметь ряд функций, но большинство технических компонентов повторяются. Плата оборудования в основном состоит из следующих элементов:
Каждый сварочный аппарат — это своего рода преобразователь энергии. Агрегат получает электрический ток от сети, затем снижает его напряжение, увеличивает ток до необходимого значения.
В этом случае происходит изменение частоты тока или из переменного тока образуется постоянный ток.
Исключение составляют только устройства, в которых электрическая дуга образуется за счет энергии генераторов с двигателем внутреннего сгорания или аккумуляторов.
Сварочный полуавтомат имеет следующее устройство:
- Газовый баллон (аргон или углекислый газ).
- Шланг подачи газа.
- Кассета с проволокой.
- Механизм подачи проволоки.
- Линия подачи проволоки.
- Блок питания.
- Горелка газовая.
- Газовое оборудование.
- Блок управления.
- Провод цепи управления.
Сварочный аппарат: Принцип работы
Рассмотрим сварочный инвертор . Вся суть инверторной техники заключается в выпрямлении переменного тока сети в постоянный сварочный ток с промежуточным изменением частоты.
Выпрямитель — это обычный диодный мост. Это устройство получает переменный ток промышленной частоты 50 Гц.
Фильтр состоит из конденсатора и дросселя. Выпрямленный ток направляется к фильтру, где он сглаживается.
В результате появляется постоянный ток, инвертор преобразует его в переменный с частотой 20-50 кГц. На данный момент существуют технологии, вырабатывающие ток частотой 100 кГц.
Силовой трансформатор снижает высокочастотное переменное напряжение до 25-40В. Кроме того, этот элемент увеличивает значение тока до необходимого для сварки.
За счет преобразования токов высокой частоты сварочный ток достигает необходимой силы. Благодаря многоступенчатому преобразованию тока можно использовать небольшой трансформатор.
Итак, чтобы получить в сварочном аппарате ток 160 А, нужно поставить медный трансформатор весом 18 кг. В инверторе достаточно поставить трансформатор массой 0.25 кг.
Высокочастотный выпрямитель обеспечивает выравнивание переменного тока. Затем он поступает на фильтр высоких частот, что позволяет получить постоянный сварочный ток.
Эти процессы преобразования энергии контролируются микропроцессорным блоком управления. Эта часть сварочного аппарата — самый дорогой элемент.
Сегодня инверторные сварочные аппараты производятся с использованием двух различных полупроводниковых технологий:
МОП-транзистор.
БТИЗ.
Их основное отличие заключается в транзисторах, которые различаются током переключения.MOSFET-транзисторы по сравнению с IGBT отличаются большими размерами и массой, но их стоимость ниже. В то же время для обеспечения такой же производительности им потребуется на порядок больше.
В полуавтоматическом режиме сварочный аппарат работает следующим образом:
Защитный газ направляется в зону электрической дуги, что позволяет защитить металл от воздействия воздуха от окисления и проникновения.
Защитный газ в этом случае может быть активным в виде диоксида углерода или инертным в виде гелия и аргона.Работа с металлом в среде инертного газа называется MIG. Работа с металлом в активной газовой среде называется МАГ.
Сварочная проволока подается в зону сварки с помощью электродвигателя, редуктора и подающих роликов.
Универсальное соединение получается в газовой среде под действием электрической дуги путем плавления электродной проволоки, которая входит в горелку.
Необходимые поверхности склеиваются с помощью расплавленного металла, создаваемого тепловой энергией.В результате получается прочный, долговечный шов.
Метод полуавтоматической сварки получил название из-за того, что проволока подается автоматически, а управление подачей, как и процессом сварки, сварщик осуществляет вручную.
Наконечник действует как сварочный контакт, питание на него подается от основного блока. Сила тока подбирается исходя из характеристик обрабатываемого материала. Скорость подачи устанавливается с помощью шестерни или редуктора.
Преимущества и недостатки сварочных аппаратов:Сварочный аппарат широко применяется. Его часто используют в повседневной жизни, а также в профессиональной деятельности.
Без такого устройства не обойтись во многих сферах производства, производствах и специализированных мастерских, например, при ремонте автомобилей.
Эти устройства используются для надежной сварки металлических каркасов и других ответственных конструкций в строительстве. Монтаж нефтепроводов и газопроводов также невозможен без использования профессионального сварочного оборудования .
Трансформаторы — очень тяжелые и громоздкие устройства. Они очень чувствительны к колебаниям напряжения и потребляют много электроэнергии.
Это недешевый аппарат. Вы можете готовить их как встык, так и внахлест. Опытный сварщик умеет хорошо сварить даже критический шов с помощью трансформатора.
Переменным током обычно сваривают только определенные марки чугуна и сталь «ходовых» марок.
Полуавтоматическая сварка идеальна как для дома, так и для производства.В нашей стране около 70% всех сварочных работ выполняется на сварочных полуавтоматах.
Это связано с простотой эксплуатации, высоким качеством сварки и широкими функциональными возможностями оборудования.
Полуавтоматический сварочный аппарат удобен для сварки тонких металлов, особенно кузовов автомобилей. Полуавтоматы почти всегда можно найти в автосервисах.
Выпрямители обладают высокой стабильностью электрической дуги, что позволяет сваривать качественные герметичные швы одинаковой глубины.Это значительно уменьшает разбрызгивание.
Соединение, благодаря защите от дуги, довольно прочное и равномерное. Нет необходимости в дополнительной очистке изделий от капель «брызгающего» расплава. В этом случае можно работать со всеми типами электродов.
Сфера применения выпрямителей намного шире: цветные металлы (никель, титан, медь, их сплавы), а также сталь (в том числе высоколегированная), чугун.
Инверторы. В последнее время они очень популярны.Они отличаются своей функциональностью, мощностью, компактностью и малым весом. Этот сварочный аппарат оптимален для начинающих.
Специалисты могут использовать их для увеличения своей производительности. Их используют везде, потому что позволяют сваривать даже тонкостенный металл.
С помощью инверторов можно варить цветные и черные металлы любой толщины в разных местах в пространстве. Используются все типы электродов.
Как выбрать сварочный аппаратСварочный аппарат может быть трехфазным или однофазным.Для бытового использования понадобится прибор на 220 В. Вы также можете выбрать универсальный блок «220/380».
Напряжение холостого хода: Определяет способность устройства инициировать и повторно зажигать электрическую дугу, в том числе поддерживать ее силу. Считается, что чем выше напряжение холостого хода, тем лучше.
Мощность: Следует выбирать устройства хотя бы с небольшим запасом мощности, порядка 30%.
Класс защиты: Сварочный аппарат должен быть стандартизирован и иметь двузначный IP-код, например, IP23.Двойка — внутрь корпуса не попадут предметы толщиной более 12 мм.
Вторая цифра — защита от влаги: Цифра 3 означает, что вода даже под углом 60 градусов не сможет попасть в корпус агрегата.
Многие современные устройства оснащены дополнительными опциями: «Защита от залипания при выключении», «Форсирование дуги» или «Горячий старт». Они помогут со сваркой, особенно новичку.
Нестандартное приложение
Сварочный аппарат можно использовать как зарядное устройство для автомобильного аккумулятора .Однако необходимо учитывать, что такое устройство обязательно должно иметь регулировку понижения ампер и вольт.
Если у вас есть такое устройство, вам необходимо перевести его в режим старт-зарядка. Вы должны установить на выходе 12 вольт, а токи от 1 до 20 от мощности батареи (если мощность 60 А, мы заряжаем 3 А).
Заряжайте аккумулятор примерно 40-60 минут. Этого вполне достаточно для запуска двигателя. Для полноценной зарядки потребуется уменьшить ток вдвое и увеличить время в 3 раза.
КАКОЙ ГАЗ ИСПОЛЬЗУЕТСЯ ДЛЯ ПОЛУАВТОМАТИЧЕСКОЙ СВАРКИ |
Сварочный полуавтомат позволяет повысить производительность и качество работы.
В оборудовании не используются традиционные электроды. Вместо этого используется специальная присадочная проволока, которая наматывается на катушку.
Преимущество такого подхода в том, что специалисту не нужно рвать шов для смены стержня.Операция выполняется непрерывно, сохраняя целостность шва и экономя время.
Кроме того, оборудование позволяет сваривать заготовки разной толщины: от 0,2 мм до нескольких сантиметров. При этом сварщик может работать с заготовками из разных материалов или сплавов.
Чтобы воспользоваться всеми этими преимуществами, для полуавтоматической сварки требуется газ. Это предотвратит проникновение атмосферной влаги и других элементов, содержащихся в воздухе, в сварочную ванну.
СОДЕРЖАНИЕ
- Какой газ нужен для полуавтоматической сварки
- Сварочная смесь для полуавтомата
- Технология выполнения работ
- Особенности сварки под газом
- Основные преимущества полуавтомата газовой сварки
Технологический регламент на эксплуатацию полуавтоматической сварки предусматривает использование в качестве флюса инертного или активного газа.
Активный реагирует химически во время сварки и изменяет физико-химические свойства сварного шва.
Защитный газ не вступает в реакцию, но защищает рабочую среду от окислительных процессов. Этот метод особенно актуален при сварке деталей из алюминиевого сплава , которые быстро окисляются.
Наиболее распространенными инертными газами являются гелий и аргон. В активную группу входят общие элементы: углекислый газ (СО2), кислород, азот.
Самые популярные соединения:
- Смесь аргона и диоксида углерода. Инертно-активная среда сводит к минимуму количество брызг
- Состав гелия и аргона. Инертная среда, позволяющая повысить температуру дуги
- газовая среда аргон-кислород. Инертное активное соединение, которое используется при работе с легированной и низколегированной сталью .
- углекислый газ в сочетании с кислородом. Активная среда используется для повышения производительности полуавтоматического оборудования.
При выборе смеси для полуавтомата специалист учитывает следующие критерии:
- вид материала заготовки
- диаметр используемой проволоки
- Оптимальная толщина сварного шва.
На практике для выбора смеси достаточно сравнить данные, приведенные в специальных таблицах. Здесь уже подобраны оптимальные варианты составов для работы с конкретными материалами с учетом технологических особенностей процесса.
Опытный сварщик также принимает во внимание сопутствующие эффекты от использования определенной газовой смеси. Например, использование углекислого газа позволяет уменьшить разбрызгивание. Поэтому их часто выбирают для формирования стыков потолка.
Технология выполнения работПринципиального отличия от дуговой сварки нет, так как в ее основе лежат те же физические и химические процессы.
Между электродом и рабочей поверхностью создается разность потенциалов, что позволяет образовывать электрическую дугу.
Нагревается до температуры, достаточной для плавления металлов. Расплавленная присадочная проволока связывается с телом детали на атомарном уровне. После охлаждения образуется прочный конструктивный элемент.
Прочность соединения добавки и тела заготовки составляет примерно 90% от показателя основного конструкционного материала.
Необходимо учитывать особенности, характерные для полуавтоматической сварки:
Присадочная проволока подается в рабочую зону непрерывно через специальный электропроводящий мундштук.
В этом случае расход материала можно регулировать вручную, удерживая или отпуская кнопку подачи.
Вместо обычного флюса в твердом виде, от плавления которого образуется газовое облако, сюда подается готовая газовая смесь или чистая среда.
Газ поступает постоянно: как с активной, так и с потухшей электрической дугой.
Благодаря такому решению уменьшается количество брызг, более стабильная работа дуги, повышается производительность труда сварщика и, соответственно, снижается трудоемкость сварочных процессов.
Особенности сварки под газом
Техника сварки полуавтоматами практически не отличается от техник, которые используются при традиционной электродуговой сварке.
С помощью полуавтоматов можно формировать горизонтальные или вертикальные швы, делать «прихватки», герметизировать стыки, выполнять стыковые стыки или стыки внахлест.
Способы формирования остаются такими же, как и при использовании классических устройств серии MMA.
Причем по общей схеме определяется оптимальный ток и режим сварки — исходя из данных о толщине шва и диаметре электрода.
Единственная особенность, которую отмечают почти все пользователи, — это простота соединения тонких листов металла. Поэтому полуавтоматы чаще всего используются при кузовном ремонте и при сварке металлоконструкций из тонких листов.
Основные преимущества полуавтомата газовой сварки- Высокая температура влияет на ограниченную область заготовки.Следовательно, металлы не меняют своих физических свойств.
- Нет дыма в рабочей зоне. Это значительно облегчает визуальный контроль процесса сварки.
- Универсальность. Технология отлично подходит для соединения разных металлов: от алюминия и титана до высоколегированной конструкционной стали.
- Нет ограничений по пространственному расположению заготовки. Достаточно отрегулировать мощность конфорки, чтобы поставить наклонный или потолочный шов.
- Нет ограничений по минимальной толщине.Технология дает возможность работать с листами толщиной 0,2 мм. Максимальная толщина заготовки зависит от навыков специалиста.
- Нет необходимости постоянно чистить швы даже при многослойной сварке. Газовый поток испаряется сразу после прекращения перемешивания.
- Высокая монтажная производительность.
% PDF-1.4 % 392 0 объект > эндобдж xref 392 176 0000000016 00000 н. 0000005050 00000 н. 0000005182 00000 н. 0000005359 00000 п. 0000005850 00000 н. 0000005988 00000 н. 0000006576 00000 н. 0000006613 00000 н. 0000007385 00000 н. 0000008078 00000 н. 0000008211 00000 н. 0000008357 00000 н. 0000008713 00000 н. 0000010893 00000 п. 0000013559 00000 п. 0000013649 00000 п. 0000021594 00000 п. 0000021820 00000 н. 0000022068 00000 п. 0000022429 00000 п. 0000022533 00000 п. 0000040216 00000 п. 0000040432 00000 п. 0000040993 00000 п. 0000041087 00000 п. 0000054488 00000 п. 0000054709 00000 п. 0000055182 00000 п. 0000055280 00000 п. 0000070413 00000 п. 0000070638 00000 п. 0000071129 00000 п. 0000071739 00000 п. 0000071824 00000 п. 0000073741 00000 п. 0000073968 00000 п. 0000074227 00000 п. 0000074367 00000 п. 0000074507 00000 п. 0000114929 00000 н. 0000137389 00000 н. 0000163119 00000 н. 0000207173 00000 н. 0000242561 00000 н. 0000267887 00000 н. 0000294350 00000 н. 0000341633 00000 н. 0000350065 00000 н. 0000381562 00000 н. 0000382704 00000 н. 0000405246 00000 н. 0000425998 00000 н. 0000465930 00000 н. 0000477238 00000 п. 0000483379 00000 н. 0000486183 00000 н. 0000537556 00000 н. 0000569809 00000 н. 0000604606 00000 н. 0000708427 00000 н. 0000723957 00000 н. 0000769448 00000 н. 0000816123 00000 н. 0000816172 00000 н. 0000816248 00000 н. 0000816354 00000 н. 0000816571 00000 н. 0000816668 00000 н. 0000816905 00000 н. 0000816993 00000 н. 0000817089 00000 н. 0000817326 00000 н. 0000817414 00000 н. 0000817680 00000 н. 0000818003 00000 н. 0000818091 00000 н. 0000818189 00000 н. 0000818506 00000 н. 0000818594 00000 н. 0000818692 00000 н. 0000818991 00000 н. 0000819079 00000 н. 0000819175 00000 н. 0000819438 00000 п. 0000819526 00000 н. 0000819624 00000 н. 0000819935 00000 н. 0000820023 00000 н. 0000820147 00000 н. 0000820488 00000 н. 0000820576 00000 н. 0000820672 00000 н. 0000821017 00000 н. 0000821105 00000 н. 0000821201 00000 н. 0000821480 00000 н. 0000821568 00000 н. 0000821686 00000 н. 0000821947 00000 н. 0000822035 00000 н. 0000822153 00000 н. 0000822412 00000 н. 0000822500 00000 н. 0000822618 00000 п. 0000822852 00000 н. 0000822939 00000 п. 0000823057 00000 н. 0000823363 00000 н. 0000823450 00000 н. 0000823567 00000 н. 0000823737 00000 н. 0000823824 00000 н. 0000823917 00000 н. 0000824081 00000 н. 0000824172 00000 н. 0000824335 00000 н. 0000824483 00000 н. 0000824557 00000 н. 0000824673 00000 н. 0000824849 00000 н. 0000825027 00000 н. 0000825189 00000 н. 0000825373 00000 н. 0000825557 00000 н. 0000825701 00000 н. 0000825887 00000 н. 0000826111 00000 п. 0000826229 00000 н. 0000826343 00000 п. 0000826463 00000 н. 0000826563 00000 н. 0000826671 00000 н. 0000826811 00000 н. 0000826995 00000 н. 0000827109 00000 н. 0000827233 00000 н. 0000827344 00000 н. 0000827465 00000 н. 0000827590 00000 н. 0000827701 00000 н. 0000827828 00000 н. 0000827965 00000 н. 0000828086 00000 н. 0000828203 00000 н. 0000828312 00000 н. 0000828429 00000 н. 0000828570 00000 н. 0000828721 00000 н. 0000828830 00000 н. 0000828941 00000 п. 0000829074 00000 н. 0000829201 00000 н. 0000829316 00000 н. 0000829441 00000 н. 0000829550 00000 н. 0000829667 00000 н. 0000829794 00000 н. 0000830031 00000 н. 0000830146 00000 н. 0000830273 00000 н. 0000830390 00000 н. 0000830515 00000 н. 0000830630 00000 н. 0000830771 00000 н. 0000830898 00000 н. 0000831013 00000 н. 0000831138 00000 н. 0000831253 00000 н. 0000831390 00000 н. 0000831517 00000 н. 0000831632 00000 н. 0000831757 00000 н. 0000831884 00000 н. 0000831999 00000 н. 0000832124 00000 н. 0000003816 00000 н. трейлер ] / Назад 1161268 >> startxref 0 %% EOF 567 0 объект > поток hԘ} LeǿB_91t [, n, A DSt / pK |) NH: 2 @ d / Ҙ-Q!, b5d! 5? lR {[iks> i @ d% و l (4H˹ƦA &;> ZM2;}} » ٸ h5mSu6Rx: 2D].IA «, R` = hkX, X; ~ EC8мм 囗 Z! XĜ @ 6m ؔ Xm-W21 & BaKA ߊ q0 & ӐPtDS`۸ (lDO / «} / K + b ,. 鷩! ImM9- ] .0ƕ4a`n,
SH7 = 9s> b5l «4» m \ Ԧ # bw; XJ6byL` ZXd, ± yAIxNp cIINA r $ @ ʖsHƒfZRX lFzSp $ Kv ֙ # 9 V $ Y> $ & ‘td + w! 53ZR [; rZv ek ԑfZ.ͻ / 㘱 iJ Թ. _OŠ ݏ I? 0S ݮ 6; y — C & Ut W Y9Cg ~ B # Ǧ5m * 37 + a6NGgYy6E] jAMP> sg $
Автоматический и полуавтоматический аппарат для орбитальной сварки, 1600000 рупий / штука
О компании
Год основания 1968
Юридический статус фирмы Партнерство Фирма
Характер бизнеса Дистрибьютор / торговый партнер
Количество сотрудников от 11 до 25 человек
Годовой оборот10–25 крор
IndiaMART Участник с июня 2010 г.
GST27AAEFM5114F1ZL
Основанная в 1968 году, Mehta Sanghvi & Company является известным торговцем, дистрибьютором и поставщиком широкого спектра оборудования для промышленной безопасности, а также сварочного оборудования и принадлежностей. Наш обширный ассортимент включает в себя ручные плазменные сварочные горелки , устройства подачи холодной проволоки TIG, сварочные аппараты и источники питания, сварочные аппараты Orbimat 300 Caorbimat 300 CA и TIG, защитные очки для сварочных очков .Эти продукты произведены, используя сырье высшего качества и передовые технологии. Наши машины известны своими особенностями, такими как простая установка, плавная работа, низкое энергопотребление, более длительный срок службы и удобство в использовании.Нас поддерживает команда профессионалов, специализирующихся в различных областях. Эти профессионалы работают в координации друг с другом, чтобы избежать путаницы при планировании поставок. Они осведомлены о методах использования машин, необходимых в производственном процессе.Кроме того, у нас есть команда квалифицированных контролеров качества, которые следят за производственным процессом и следят за разумным использованием ресурсов. Они также проверяют продукцию по различным параметрам, чтобы не оставлять камня на камне. Благодаря нашим качественным продуктам и своевременной доставке грузов мы смогли создать огромную клиентскую базу по всей стране.
Видео компании
Программа сварочных технологий
Добро пожаловать
Mt.Программа SAC по сварке — это комплексная программа обучения и подготовки, разработанная дать студентам навыки и знания, необходимые для получения работы в различных отраслей, связанных со сваркой и производством. Студенты Mt. SAC Welding в настоящее время работает в строительной, аэрокосмической, светотехнической и послепродажной отраслях.
Большинство классов сварки на Mt.Функция SAC Welding 1 час лекции для обсуждения безопасность и правильная наладка и работа сварочных процессов и оборудования. Остаток Классного времени 3 часа или 6 часов посвящены практическим лабораторным упражнениям. У нас есть классы для каждого уровня подготовки. Пожалуйста, ознакомьтесь с описанием наших курсов , чтобы узнать о классах, которые мы предлагаем. Большинство наших сварочных классов делают не иметь предварительных условий для курса, поэтому студенты могут записаться на курсы, которые соответствуют их интересам или потребности.
Mt. SAC Welding предлагает оборудование A.S. диплом по сварке, а также четыре академических сертификата доработки в сварке. Сварка колледжа Маунт-Сан-Антонио является лицензированным испытательным центром. для Департамента строительства и безопасности города Лос-Анджелес. Предлагаем сертификацию для конструкционной стали — ручное и полуавтоматическое, согласно AWS D1.1, а также Light Gage Сталь по AWS D1.3.
Параметрическое исследование микроструктуры, характера разрушения и свойств низкого динамического сдвига при растяжении
Резюме
Точечная сварка сопротивлением (RSW) двухфазных сталей (DP) является сложной задачей из-за образования хрупкой мартенситной структуры в зоне плавления (FZ) , что приводит к низкой энергоемкости соединения при высокоскоростном нагружении.В настоящем исследовании термическая обработка на месте после сварки (PWHT) была проведена с использованием схемы двойной импульсной сварки с целью улучшения механических характеристик точечной сварки сопротивлением стали DP590. Метод Тагучи использовался для оптимизации параметров PWHT на месте для получения максимальной пиковой нагрузки и энергии отказа. Эксперименты были разработаны на основе ортогональной матрицы (OA) L16. Механические характеристики оценивались с точки зрения пиковой нагрузки и энергии разрушения после проведения испытания на низкий динамический сдвиг при растяжении (TS).Микроструктурные характеристики были выполнены с использованием сканирующего электронного микроскопа (SEM). Результаты показывают, что улучшение пиковой нагрузки и энергии отказа на 17 и 86% соответственно было достигнуто при двухимпульсной сварке (DPW) в оптимальных условиях по сравнению с традиционной одноимпульсной сваркой (SPW). Улучшение механических характеристик стало результатом (i) увеличения FZ и (ii) улучшенной ударной вязкости сварного шва за счет отпуска мартенсита в FZ и докритической зоне термического влияния (SCHAZ).На эти факторы влияет подвод тепла, которое, в свою очередь, зависит от параметров PWHT на месте.
Ключевые слова: двухфазная сталь , контактная точечная сварка, термообработка на месте после сварки, испытание на сдвиг при растяжении, зона плавления, мартенсит, конструкция Тагучи
1. Введение
Двухфазные стали (DP) являются представителями передовой высокой из высокопрочных сталей (AHSS), которые широко используются в конструкции кузова транспортных средств из-за их большого потенциала для одновременного повышения топливной эффективности и сопротивления столкновению, предлагая при этом тонкие листы для снижения веса транспортного средства [1].Стали DP обладают высокой прочностью и отличной пластичностью. Помимо этого, высокая скорость деформационного упрочнения, непрерывная податливость и низкое отношение предела текучести к пределу прочности являются другими важными особенностями сталей DP. Комбинация этих превосходных механических свойств является синергетическим эффектом их уникальной микроструктуры, состоящей из мягкой ферритовой матрицы, залитой твердыми мартенситными островками [2,3].
Компоненты кузова автомобиля изготовлены из тонких листовых деталей, соединенных точечной контактной сваркой.На современном автомобиле выполняется несколько тысяч точечных сварных швов [4]. В случае аварии безопасность пассажиров от травм во многом зависит от структурной целостности автомобиля, которая, в свою очередь, зависит от качества точечной сварки. Во время аварии точечная сварка действует как место возникновения складок и передает нагрузку на автомобильные сборки. Следовательно, для безопасной конструкции транспортных средств необходимо учитывать производительность и качество контактной точечной сварки [5,6].
Одной из ключевых характеристик качества, влияющих на механические характеристики точечной сварки, является режим разрушения.Как правило, точечная сварка выходит из строя в двух режимах: режиме разрыва (PF) и режиме межфазного разрушения (IF). Режим PF, при котором разрушение происходит из-за отрыва сварного шва от листов, проявляет наиболее удовлетворительные механические свойства. Напротив, режим IF (в котором трещина распространяется через FZ) вреден для аварийной устойчивости транспортного средства, и его следует избегать. Во время аварии режим PF может передавать высокий уровень силы и увеличивать рассеяние энергии деформации, вызывая тем самым сильную пластическую деформацию в соседних компонентах [7,8].
Как правило, поведение при разрыве точечного сварного соединения определяется на основе процесса статического разрушения с использованием условий статической нагрузки посредством лабораторных испытаний, т. Е. Испытания на отслаивание кузова, испытания на растяжение при сдвиге внахлест и испытания на поперечное растяжение. Однако в реальной аварийной ситуации поведение соединения может сильно отличаться от поведения статически нагруженного образца, испытанного в лаборатории. Во время аварии на конструкцию транспортного средства внезапно передается большая нагрузка, и чрезвычайно высокое напряжение концентрируется на границе раздела сварной крупицы и основного металла (BM).Следовательно, разрушение точечной сварки может произойти до выхода из строя BM [9]. Чтобы выполнить критический анализ ударопрочности элементов конструкции транспортного средства, необходимо понимать поведение разрушения точечной сварки при динамических нагрузках. Для этой цели используются быстрые испытания на нагрузку, такие как испытание падающим грузом, испытание на ускоренный сдвиг и поперечное растяжение (CT) и испытание на модифицированный ударный маятник [10,11,12]. Chao et al. В работе [13] изучалась чувствительность к скорости деформации соединений, выполненных контактной точечной сваркой, в образцах с растягивающим сдвигом и поперечным растяжением при растягивающей нагрузке.Были записаны данные динамических и статических испытаний для широкого диапазона марок стали, включая обычную низкоуглеродистую сталь, высокопрочную низколегированную (HSLA) сталь и сталь DP с различной толщиной листов и размерами сварных швов. Они показали, что (а) образец TS демонстрирует более высокую чувствительность к скорости деформации и более жесткий, чем образец CT, (b) более высокая скорость удара приводит к более высокой скорости нагружения, (c) более высокая скорость удара дает более высокую нагрузку на разрушение и (d) более высокая скорость нагружения. может быть достигнута в образце TS. Берч и Алвес [14] также провели квазистатические и динамические испытания на сдвиг при растяжении листов, сваренных точечной сваркой.Результаты показали, что нагрузка на разрыв увеличивалась с увеличением скорости испытания, в то время как энергия разрушения зависела от режима разрушения в дополнение к скорости испытания. Song et al. [9] исследовали поведение динамического разрушения точечной сварки при комбинированной осевой и сдвигающей нагрузке с использованием специального приспособления для удержания образца LS. Применялись различные испытательные скорости (т.е. 1 × 10 −5 , 0,01, 0,1 и 1,2 м / с) и углы нагрузки (т.е. 0, 15, 30, 45, 60, 75 и 90 °). Было обнаружено, что пиковая нагрузка снижалась, когда угол нагружения был меньше 30 °, тогда как пиковая нагрузка увеличивалась в интервале от 45 до 90 ° условий.Кроме того, сообщалось о максимальном увеличении пиковой нагрузки на 13% при увеличении скорости испытания от самой низкой (квазистатической) до максимальной (динамической) скорости нагружения.
Хорошо известно, что термический эффект контактной точечной сварки разрушает тщательно разработанную многофазную микроструктуру современных высокопрочных сталей (AHSS), включая сталь DP. В результате высокой прокаливаемости из-за повышенного содержания легирующих элементов и высоких скоростей охлаждения (порядка 2000–4000 K с –1 ) сварного шва во время RSW образуется твердая мартенситная микроструктура в FZ и крупнозернистый нагрев. -зона поражения (CGHAZ) [15,16,17].Более того, разупрочнение происходит в SCHAZ из-за отпуска мартенсита, уже присутствующего в основном металле [18]. Из-за вышеуказанных фазовых превращений между FZ, HAZ и BM возникает значительное несоответствие свойств (прочности и ударной вязкости). Следовательно, механические свойства ухудшаются локально, что приводит к плохим характеристикам соединения. Хан и др. [11] изучали влияние микроструктуры сварного шва на пиковую нагрузку и поглощение энергии разрушения при точечной сварке обычной стали HSLA, стали 590R, DP600, DP980 и TRIP780 с использованием статических, промежуточных и динамических скоростей испытаний.Они заметили, что точечная сварка стали DP600 не удалась в режиме IF для всех трех скоростей испытания. Они сообщили, что низкая вязкость разрушения FZ и HAZ из-за образования мартенситной структуры, наряду с концентрацией напряжений на границе раздела, приводит к низким разрушающим нагрузкам при всех скоростях испытания.
Сообщалось, что микроструктура внутри точечной сварки может быть изменена термообработкой на месте после сварки с использованием схемы двойной импульсной сварки, и могут быть получены улучшенные механические свойства [15,16,17,19,20,21,22].В этом методе сварной шов образуется после первичного / первого импульсного тока из-за тепла, выделяемого на границе раздела лист / лист, которое, в свою очередь, плавит листы. Затем дается некоторое время для охлаждения, чтобы сварочный стержень затвердел. После этого сварную деталь повторно нагревают путем подачи второго импульсного тока в течение определенного времени с целью снижения твердости FZ в достаточной степени, а затем снова охлаждают. Помимо изменения микроструктуры, улучшенный диапазон свариваемости и увеличенный размер сварных швов могут быть получены с помощью точечной контактной сварки с многоимпульсной схемой тока [23,24].Сообщалось, что правильное количество подводимого тепла является ключом к получению желаемой микроструктуры в сварном изделии, которой можно управлять, используя соответствующие параметры PWHT на месте, то есть ток второй импульсной сварки, время второй импульсной сварки и время охлаждения (время между первым и вторым импульсами) [16]. Поглощение тепла зависит от сварочного тока и времени сварки, а на рассеивание тепла (то есть скорость охлаждения) влияет время охлаждения во время RSW. В предыдущих исследованиях, посвященных двойному импульсному RSW, влияние тока и времени второго импульса на микроструктуру и механические свойства при статической нагрузке было изучено, в то время как влияние времени охлаждения изучено недостаточно.Однако сообщалось, что время охлаждения оказывает значительное влияние на микроструктуру сварного шва и механические свойства точечной сварки сопротивлением AHSS [25]. Следовательно, для получения наилучшего сочетания механических свойств требуется оптимизация всех трех параметров импульса PWHT, включая сварочный ток, время сварки и время охлаждения.
В данной работе исследуется влияние параметров сварки на месте сварки, т. Е. Сварочного тока второго импульса, времени сварки второго импульса и времени охлаждения, на микроструктуру, механические свойства и режимы отказа RSW из стали DP590.Механические свойства с точки зрения пиковой нагрузки и энергии разрушения были получены с использованием испытания на низкий динамический сдвиг при растяжении (TS) (скорость нагружения 500 мм / мин). Метод плана эксперимента Тагучи (DOE) используется для определения оптимальных уровней параметров для достижения максимальной пиковой нагрузки TS и энергии отказа. Кроме того, важные параметры процесса, влияющие на механические свойства сварных швов, были проанализированы с использованием метода дисперсионного анализа (ANOVA).
3. Результаты и обсуждение
3.1. Микроструктура и микротвердость SPW
показывает среднюю микротвердость и показывает оценку микроструктуры SPW. Как правило, точечная сварка сопротивлением имеет неоднородную микроструктуру в соответствии с термическим циклом сварки. Таким образом, сварной шов можно разделить на три области: BM, FZ и HAZ. Хорошо известно, что микроструктура RSW существенно влияет на микротвердость. Таким образом, изменение твердости сварного изделия объясняется развитием микроструктуры.a показывает общую макроструктуру SPW, указывающую, что размер FZ составляет 6,71 мм, что соответствует минимальному требованию к размеру сварного шва, основанному на D = √5t. б представлена микроструктура ОМ, состоящая из двух фаз — феррита и мартенсита, со средней твердостью ~ 205 HV. c показывает микроструктуру FZ, состоящую из крупных столбчатых зерен из-за направленного затвердевания жидкого металла по направлению к центральной линии сварного шва. Столбчатые зерна состоят в основном из реечного мартенсита (твердость ~ 410 HV). Образование мартенсита в FZ можно объяснить высокой скоростью охлаждения процесса RSW из-за наличия водоохлаждаемых медных электродов и высокой прокаливаемости BM (т.е.е., C.E = 1.19) [4]. В зависимости от размера зерна, температуры и распределения микротвердости микроструктура HAZ подразделяется на крупнозернистую зону термического влияния (CGHAZ), мелкозернистую зону термического влияния (FGHAZ) и подкритическую зону термического влияния (SCHAZ). Микроструктура CGHAZ состоит из крупных зерен мартенсита, как показано на d. Во время сварки максимальная температура в CGHAZ достигает значений, значительно превышающих Ac3 (область 100% аустенита). При охлаждении как высокая скорость охлаждения, так и богатый углеродом аустенит способствуют образованию крупнозернистого мартенсита внутри крупных предшествующих аустенитных зерен (PAG) (твердость ~ 420 HV).д показывает, что микроструктура FGHAZ состоит из мелких пакетов мартенсита (твердость ~ 440 HV). Во время сварки пиковые температуры в FGHAZ достигают немного выше Ac3, что способствует зарождению аустенита, в то время как короткое время нагрева и быстрое охлаждение ограничивают рост зерна. f показывает интерфейс между BM и HAZ. g показывает, что микроструктура SCHAZ состоит из феррита и слегка отпущенного мартенсита (твердость ~ 202 HV). Пиковая температура становится меньше температуры Ac1 с увеличением расстояния от границы плавления, что приводит к отпуску мартенситной фазы, присутствующей в BM [6].Однако существенного смягчения на SCHAZ не наблюдалось. Это можно объяснить меньшим содержанием мартенсита в ОМ и меньшим тепловложением тока первого импульса.
Средняя микротвердость различных зон сварки СПС.
Эволюция микроструктуры SPW. ( a ) общая структура сварного шва, ( b ) основной металл (BM), ( c ) зона плавления (FZ), ( d ) крупнозернистая зона термического влияния (CGHAZ), ( e ) мелкозернистая зона термического влияния (FGHAZ), ( f ) граница раздела BM и HAZ ( г ) SCHAZ (примечание F — феррит, M — мартенсит, STM — мартенсит слабого отпуска).
показывает график нагрузки-смещения, полученный после испытания TS. Видно, что пиковая нагрузка и энергия отказа составили 23,2 кН и 56,7 Дж соответственно. также иллюстрирует режим отказа SPW после испытания TS, указывая режим IF (также подтверждается внезапным падением нагрузки на кривой нагрузка-смещение). Режим IF в SPW можно объяснить образованием хрупкой мартенситной микроструктуры в FZ и HAZ. Режим IF SPW подразумевает, что критерий минимального размера, основанный на правиле D = 5√t, не гарантирует PF.Таким образом, создается впечатление, что помимо толщины листа микроструктурные характеристики сварного шва влияют на режим разрушения.
График зависимости нагрузки от смещения SPW с указанием пиковой нагрузки (PL) и энергии отказа (FE).
3.2. Анализ отношения сигнал / шум для DPW
В общем, метод Тагучи использует отношение сигнал / шум (S / N) для оценки рабочих характеристик. Отношение сигнал / шум — это логарифмическая функция желаемых характеристик производительности, которая служит целевой функцией для оптимизации [28].Для оценки рабочих характеристик используются три подхода: чем больше, тем лучше, чем меньше, тем лучше и номинально лучше. Для получения максимальной пиковой нагрузки и энергии отказа используется подход «чем больше, тем лучше» для расчета отношения сигнал / шум с использованием уравнения (1).
(SN) отношение = −10log (1n∑i = 1n1yi2)
(1)
где yi представляет собой значение отклика i-го эксперимента в ортогональном массиве, а n — количество экспериментов. Каждый тест повторялся один раз, и средние значения характеристик ответа (т.е., пиковая нагрузка и энергия отказа). Экспериментальные результаты характеристик отклика вместе с соответствующими отношениями сигнал / шум приведены в.
Таблица 5
Экспериментальные результаты характеристик отклика, то есть средней пиковой нагрузки и средней энергии отказа с соответствующими отношениями сигнал / шум.
Номер образца | Отклик 1: Средняя пиковая нагрузка (кН) | Отношение сигнал / шум | Отклик 2: Средняя энергия разрушения (Дж) | Отношение сигнал / шум | 24.63 | 27,83 | 68,35 | 36,70 |
---|---|---|---|---|
2 | 24,64 | 27,83 | 74,23 | 37,41 |
3 | ||||
3 | 90525,58 | 28,16 | 81,71 | 38,25 |
5 | 24,67 | 27,84 | 77,57 | 37,79 |
6 | 1128,00 | 81,20 | 38,19 | |
7 | 26,00 | 28,30 | 87,51 | 38,84 |
8 |
В методе Тагучи кривые отклика используются для изучения влияния входных параметров на характеристики отклика. В настоящем исследовании наиболее благоприятные условия (оптимальные настройки) для параметров процесса с точки зрения средних характеристик отклика устанавливаются путем анализа кривых отклика. Более того, дисперсионный анализ (ANOVA) был выполнен с уровнем достоверности 95% для количественной оценки относительной значимости и процентного вклада факторов входного контроля в характеристики ответа [28].
3.2.1. Оптимальные параметры PWHT на месте для максимальной пиковой нагрузки
показывает, что оптимальными параметрами для максимальной пиковой нагрузки являются A4B4C1, то есть WC (7,5 кА), WT (560 мс) и CT (400 мс). Здесь следует отметить, что оптимальные условия для пиковой нагрузки совпадают с образцом 16. показывает ранжирование уровней, основанное на отношениях S / N трех параметров. Чем выше значение дельты параметра, тем выше рейтинг и тем более важным будет этот параметр. Согласно, максимальное значение дельты равно 0.61, что указывает на то, что сварочный ток оказывает большее влияние на пиковую нагрузку по сравнению со временем сварки и временем охлаждения. Результаты ANOVA представлены в. Согласно ANOVA, сварочный ток и время сварки оказывают значительное влияние на пиковую нагрузку. Более того, исходя из процентного соотношения, наиболее доминирующим параметром является сварочный ток, за которым следуют время сварки и время охлаждения.
График, представляющий основные эффекты для пиковой нагрузки.
Таблица 6
Ранжирование параметров для отношения сигнал / шум пиковой нагрузки.
Уровень | A | B | C |
---|---|---|---|
1 | 27,92 | 27,95 | 28,26 |
Таблица 7
Параметры / факторы | DF | Adj5DF | Seq SS48 905 F | P | Вклад (%) | |||
---|---|---|---|---|---|---|---|---|
A | 3 | 0,78314 | 0,78314 | 0,261048 | 11,28 | 0,007 * | 0,007 * | 34 |
B | 3 | 0,65401 | 0,65401 | 0,218003 | 9,42 | 0,011 * | 41,2 | |
C 0,02 | 0,920 | 0,7 | ||||||
Остаточная ошибка | 6 | 0,13886 | 0,13886 | 0,023144 | 8,7 | |||
Всего | 15 | 1.58707 | 100 | |||||
R-Sq = 91,25%, R-Sq (прил.) = 78,13% |
3.2.2. Оптимальные параметры PWHT для максимальной энергии отказа
Для максимальной энергии отказа оптимальными уровнями параметров являются A4B4C2, то есть WC (7,5 кА), WT (560 мс) и CT (460 мс), как показано на рис. показывает ранжирование параметров для отношения сигнал / шум энергии отказа. Согласно наибольшему значению дельты 2,33, что указывает на то, что сварочный ток имеет большее влияние на энергию отказа по сравнению со временем сварки и временем охлаждения.представляет собой среднее значение отношения сигнал / шум всех экспериментальных значений энергии отказа, а q — количество параметров, которые существенно влияют на энергию отказа (два параметра, т. е. WC и WT). Согласно уравнению (2), прогнозируемое значение энергии отказа в A4B4C2 составляет ~ 106,07 (Дж).
График, представляющий основные эффекты энергии отказа.
Таблица 8
Ранжирование параметров для S / N энергии отказа.
Уровень | A | B | C |
---|---|---|---|
1 | 37.58 | 37,91 | 38,81 |
2 | 38,52 | 38,61 | 38,86 |
3 | 39,24 | 39,22 |
Таблица 9
ANOVA для энергии отказа.
Параметры / факторы | DF | Seq SS | Adj MS | F | P | Вклад (%) |
---|---|---|---|---|---|---|
A | 3,95 | 0,000 * | 65,82 | |||
B | 3 | 5,9487 | 1,98290 | 52,32 | 0,000 * | 32,72 | C0361 | 0,01202 | 0,32 | 0,813 | 0,19 |
Остаточная ошибка | 6 | 0,2274 | 0,03790 | 1,25 | ||
Итого | 15 | 18,1781 | 100 | |||
R 2 = 98,75%, R 2 (прил.) = 96,87% |
3.3. Влияние параметров сварки на месте на механические свойства DPW
Обычно механические свойства точечной сварки описываются в терминах пиковой нагрузки и энергии разрушения.Три показателя качества влияют на пиковую нагрузку и энергию разрушения, включая прочность и пластичность в месте разрушения, которые, в свою очередь, зависят от микроструктуры FZ / HAZ, геометрических характеристик сварного шва (в основном размера FZ) и режима разрушения (зависит от обоих FZ). размер и сила места разрушения) [29]. Согласно результатам экспериментов (см.), DPW показывает более высокие значения пиковой нагрузки и энергии отказа по сравнению с SPW. На основе средних значений было обнаружено, что максимальное улучшение пиковой нагрузки на 17% и энергии отказа на 86% достигается в образце 16 по сравнению с SPW.Таким образом, улучшение механических свойств объясняется на основе трех вышеуказанных критериев качества.
3.3.1. Микроструктура и микротвердость
иллюстрирует влияние тепловложения на среднее распределение микротвердости всех сварных швов. Можно заметить, что микротвердость увеличивается с SCHAZ, FZ, CGHAZ и FGHAZ. Здесь следует отметить, что SPW демонстрирует самую высокую микротвердость во всех зонах сварного шва по сравнению со всеми образцами DPW. В DPW микротвердость субструктур FZ и HAZ зависит от микроструктурных фаз, на которые, в свою очередь, влияет тепловложение во время термического цикла RSW.Подвод тепла для DPW был рассчитан с использованием уравнения (3), описанного в разделе 3.3.2. Согласно данным, образец 16 испытал максимальное тепловложение во время термообработки на месте. Более того, согласно статистике DOE, образец 16 показал самые высокие значения пиковой нагрузки и энергии отказа. Поэтому для простоты изменение твердости в образце 16 объясняется развитием микроструктуры. показывает эволюцию микроструктуры различных зон сварного шва образца 16. Можно заметить, что микроструктура FZ (см. a) показывает сломанные планки мартенсита внутри крупных столбчатых зерен, что приводит к снижению твердости (16.На 5% ниже ФЗ СПЗ). Более того, микроструктуры субструктур HAZ, то есть CGHAZ (см. B), FGHAZ (см. C) и SCHAZ (см. D), также демонстрируют сильно отпущенные мартенситные структуры, что указывает на морфологию сломанной реечной рейки в пределах предшествующих зерен мартенсита, что приводит к твердости. сокращение на 20,4, 20,2 и 20,2%, соответственно, по сравнению с CGHAZ, FGHAZ и SCHAZ для SPW. Морфология сломанных реек в различных зонах точечной сварки образца 16 может быть объяснена частичным восстановлением реек мартенсита из-за высокого тепловложения в процессе быстрого отпуска.О частичном восстановлении мартенситных планок во время быстрого отпуска стали DP также сообщили Hernandez et al. [18,30]. Частичное восстановление во время быстрого отпуска является комбинированным эффектом (i) замедления границы реек из-за мелкого и плотного осаждения цементита на дислокациях и (ii) недостаточного времени для аннигиляции дислокаций путем полного восстановления [27,30,31]. Как упоминалось ранее, микроструктура и характеристики твердости различных зон RSW оказывают значительное влияние на поведение при разрушении.Поэтому подробное обсуждение влияния микротвердости на механизмы разрушения приведено в разделе 3.3.3.
Профиль средней твердости SPW и DPW.
Оценка микроструктуры DPW16 RSW. ( a ) FZ, ( b ) CGHAZ, ( c ) FGHAZ и ( d ) SCHAZ.
3.3.2. Увеличение размера ФЗ
ФЗ является одной из важнейших качественных характеристик, влияющих на механические характеристики точечного сварного соединения [8]. Макроструктура, показывающая размер ЗО образцов 1, 8, 12 и 16, показана на рис.Можно заметить, что размер FZ образцов, подвергнутых схеме DPW, больше по сравнению с SPW. По мере увеличения размера FZ площадь соединения между двумя листами увеличивается, что, в свою очередь, улучшает пиковую нагрузку и энергию разрушения сварных швов [8]. В соответствии с графиком основных эффектов (см. И) по мере увеличения сварочного тока и времени сварки второго импульса пиковая нагрузка и энергия отказа увеличиваются. Размер FZ зависит от количества тепла, выделяемого во время RSW. Физический принцип достижения тепловыделения в процессе RSW определяется уравнением нагрева Джоуля, приведенным ниже [32].
где Q — выделяемое тепло (Дж), I — приложенный ток (А), R — полное сопротивление (Ом), а t — время, в течение которого прикладывается ток (с). Уравнение (3) указывает, что количество выделяемого тепла увеличивается с увеличением тока и времени. Кроме того, ток вносит больший вклад в тепловыделение из-за его квадратного значения в уравнении (3). Сварочный стержень образуется после подачи первого импульсного тока по схеме SPW, что приводит к размеру FZ 6,71 мм. В схеме DPW сварная деталь повторно нагревалась с использованием различных комбинаций тока второго импульса и времени после обеспечения определенного времени охлаждения между двумя импульсами.Экспериментальное определение погонной энергии в сварном изделии во время режима PWHT на месте затруднено из-за невидимых сварных швов и короткого цикла сварки RSW. Taniguchi et al. [24] рассчитали коэффициент тепловложения (Q) импульса нагрева после сварки во время RSW, используя уравнение, приведенное ниже.
где Q — коэффициент подвода тепла, IS — ток второй импульсной сварки (кА), IF — ток первой импульсной сварки (кА), tS — время второй импульсной сварки (мс) и tF — время сварки первого импульса (мс). показывает коэффициент тепловложения для всех графиков DPW, как определено в.Из этого видно, что значение Q увеличивается с увеличением IS и tS. Следовательно, изменение размера FZ может быть объяснено на основе тепловложения во время второго импульсного тока. показывает влияние тепловложения на размер FZ. Можно заметить, что размер FZ увеличивается с увеличением подводимого тепла. Более того, и показывают, что оптимальное время охлаждения для максимальной пиковой нагрузки и энергии отказа составляет 400 и 460 мс соответственно (то есть более низкие уровни времени охлаждения). Это указывает на то, что в конце охлаждения в сварном изделии сохраняется определенное количество тепла, которое дополняет общее количество подводимого тепла.Агаджани и др. [21] и Ли и др. [33] сообщили о подобных наблюдениях, что размер FZ увеличивается при использовании двойного импульса RSW.
Макроструктура, иллюстрирующая размер FZ. ( a ) образец 1, ( b ) образец 8, ( c ) образец 12 и ( d ) образец 16.
Коэффициент тепловложения DPW. (Перепечатано из [26] с разрешения Elsevier)
Влияние тепловложения на размер ЗО.
3.3.3. Режим отказа
Сообщалось, что точечные сварные швы, которые выходят из строя в режиме PF, обладают более высокой способностью выдерживать нагрузку и поглощать энергию разрушения по сравнению со сварными швами, которые выходят из строя в режиме IF [6,7].После проведения испытаний с низким динамическим TS для DPW наблюдались четыре различных режима отказа, как показано на рис. Механизм отказа в каждом случае режима отказа обсуждается следующим образом.
Типичные виды отказов, наблюдаемые после испытаний с низким динамическим TS. ( a ) режим межфазного разрушения (IF), ( b ) режим разрушения с отрывом (PF), ( c ) режим частичного разрушения поверхности раздела (PIF) и ( d ) режим частичного разрушения толщины с частичным разрывом (PTPP) режим.
Режим отказа интерфейса (IF).В этом режиме трещина распространяется через FZ, и нагрузка внезапно падает до нуля из-за быстрого продвижения трещины через осевую линию сварного шва.
Режим отказа от вытягивания (PF). В этом режиме выход из строя происходит за счет отрыва сварочного шва с обоих листов. Во время нагружения, когда имеется определенная величина вращения, растягивающие напряжения, образующиеся вокруг ядра, вызывают пластическую деформацию в направлении толщины листа. Наконец, образование шейки происходит в ЗТВ по мере увеличения силы натяжения, что приводит к полному разрыву и срезанию ОМ.
Режим частичного межфазного отказа (PIF). В этом режиме трещина сначала распространяется в FZ, а затем перенаправляется по направлению толщины.
Частичная толщина — частичный вырыв (режим PTPP). В этом режиме наклонная трещина сначала распространяется в FZ, а затем трещина перенаправляется через толстый лист в направлении толщины, что приводит к удалению некоторой части стыковочного листа.
Сообщалось, что существует критический размер FZ, выше которого режим PF возникает во время загрузки TS [34,35].Критический размер FZ зависит от толщины листа и механических свойств BM / HAZ / FZ. При нагрузке TS для режима IF прочность FZ (которая зависит от твердости) важна для прогнозирования механической прочности сварного шва, а для режима PF прочность места разрушения (т. Е. SCHAZ или BM) определяет механические свойства точечной сварки [35]. Следовательно, при нагрузке TS разрушение точечной сварки представляет собой конкуренцию между сдвиговой пластической деформацией FZ и образованием шейки в месте разрушения.Образование шейки происходит в самой мягкой области сварного шва. показывает, что самая низкая твердость имеет место в ЩАЗе. Более того, усадочные пустоты / пористость в FZ влияют на режим разрушения [34,35]. Чтобы обеспечить режим PF при нагрузке TS, Pouranvari et al. Разработали простую аналитическую модель. [34] и приведен ниже.
где Dc — критический размер FZ, P — коэффициент пористости, рассчитанный с использованием уравнения (6), f — отношение прочности на сдвиг к пределу прочности при растяжении FZ и согласно критерию Tresca равно 0.5, t — толщина листа, а HFZ и HPFL — твердость зоны сплавления и твердость места разрушения на вырыв (т.е. SCHAZ) соответственно.
P = Atotal − AporosityAtotal
(6)
где Atotal — это общая площадь FZ, а Aporosity — это прогнозируемая площадь пористости в FZ ( P = 1, если пористость отсутствует). Согласно этой модели, точечные сварные швы с Dc Взаимосвязь между критической FZ, фактическим размером FZ и режимом отказа SPW и всех DPW. Хорошо известно, что оборудование для позиционирования может помочь сварщикам маневрировать большими сборками и протирать их полотенцем.Например: сварочный вращатель . Однако многие небольшие узлы также могут быть механически позиционированы, чтобы обеспечить те же преимущества. Цех сварочных ротаторов Независимо от размера сварного изделия, принципы позиционирования остаются неизменными. Базовый продукт должен быть прикреплен к устройству позиционирования. Как только он будет установлен, машина будет маневрировать с помощью механических средств для наилучшего выполнения сварки или сборки.Чтобы упростить доступ к сварным швам, можно добавлять детали и узлы. Полуавтоматическая и ручная сварка. Операторы могут больше сосредоточиться на том, чтобы удерживать сварочную ванну в стыке, чем беспокоиться о перемещении горелки или электрододержателя. Сварочный вращатель можно использовать для необходимого позиционирования или в качестве платформы для создания всей сварочной станции. склад сварочного ротатора Уменьшите беспорядок и увеличьте производительность Сварочный полуавтомат состоит из сварочного вращателя, источника сварочного тока и подставки для горелки.Он может производить полуавтоматическую сварку, что является одновременно производительным и эргономичным. Вращатель удерживает деталь и перемещает ее под неподвижной горелкой. Горелку можно прикрепить к ткацкому устройству, которое позволяет колебанием заполнять значительные зазоры и V-образные канавки. Качество сварки повышается за счет постоянной скорости и положения горелки. Коммуникационный кабель соединяет встроенный ротатор с источником сварочного тока. Оператору необходимо указать точку старта, нажав кнопку или ножную педаль.Цикл сварочного вращателя будет продолжаться до тех пор, пока не будет отправлен сигнал о его завершении. Этот метод используется для кольцевых сварных швов. Последняя часть удаляется, и начинается другая. Введение сварочного вращателя Помните центр тяжести При выборе подходящего устройства позиционирования необходимо учитывать не только вес и размер сварного шва, но и его центр тяжести (COG), а также расстояние от устройства.Точка, в которой все оси уравновешиваются одинаково, называется COG. Спецификации производителя для обычного сварочного вращателя помогут выбрать двигатель и систему управления. Сварщикам необходимо убедиться, что спецификации верны для горизонтальной и вертикальной нагрузки. Это обеспечит правильное обращение со сварной конструкцией. Вращатель должен выдерживать максимальную нагрузку. 20 тонн обычных токарных роликов Используйте поворотные ролики для поворота цилиндров Если сварная деталь имеет цилиндрическую форму, ее можно прокатывать.Небольшое, либо натяжное колесо, либо вращающееся колесо с приводом может вращать трубу или сосуд для ручной сварки вниз. Приводные ролики обеспечивают равномерное вращение, что обеспечивает однородный кольцевой сварной шов. Натяжные ролики можно использовать для поддержки более длинных труб и сосудов. Они не питаются. Их можно использовать для соединения труб или концов труб, а также для крепления фланцев. Держать сварочный вращатель в горизонтальном положении Даже для небольшого оборудования для позиционирования блок необходимо устанавливать на плоской и ровной поверхности во избежание опрокидывания.Монтажные отверстия, предусмотренные для обычного сварочного вращателя, должны использоваться для его крепления на устойчивой поверхности. Это предотвратит его опрокидывание в случае неожиданной силы. Также необходимо закрепить ротатор, когда он установлен на верстаке. Подключите ток заземления к вращателю Когда сварка закончена, ток заземления должен быть подключен к вращающему устройству. Ток заземления передается от стола к шасси. Это позволяет избежать частой замены и снятия сварочного зажима.Пренебрежение заземлением электрических компонентов может привести к повреждению и образованию некондиционных отложений при сварке. Электрический ток, возникающий при сварке, должен быть совместим с любым вращателем. Все заземляющие кабели также должны быть надежно закреплены, удалив всю краску перед тем, как прикрепить их к каретке. Идеальные решения для автоматического сварочного оборудования Вам может повезти, потому что современные новаторы разработали автоматизированные машины, которые вращают трубы или резервуары во время сварки или других чистовых операций.Независимо от того, насколько мала ваша компания или насколько велика ваша мастерская, знайте, что производительность является ключом к выживанию на глобальном конкурентном рынке. Вы ищете свое автоматическое сварочное оборудование? Теперь, когда вы видите, как простой на вид сварочный вращатель / поворотный валок может повысить эффективность вашего сварочного оборудования, важно помнить, что не все оборудование создано одинаково. Вот некоторые факторы, которые следует учитывать при поиске этих устройств: Международная сертификация: Только лучшая тяжелая техника должна быть сертифицирована.Сертификат CE является важнейшей сертификацией продукта на этом рынке. Важно убедиться, что продукты, которые вы покупаете, имеют одобрение CE. Подгонка трубы для поворота валков Репутация: Вы хотите купить оборудование, произведенное инновационной компанией, и у вас есть опыт, чтобы прослужить ему долгие годы. Кроме того, договоритесь с производителем о посещении его завода для проверки автоматического ротатора и поворотного ролика перед отправкой. Вы можете рассчитывать на то, что вас встретит надежная компания.Однако, если они не хотят этого делать, вам следует поискать другого поставщика. Для автоматики очень важно иметь послепродажное обслуживание. Вы должны убедиться, что ваш поставщик может предложить гарантию на все продукты, которые вы покупаете. Настройка: Вы должны найти поставщика, который может разработать токарные валки и ротаторы в соответствии с вашими требованиями. Ознакомьтесь с политикой отгрузки и сроками поставки: Надежная компания предложит благоприятную политику отгрузки вместе с разумным сроком поставки, чтобы оборудование было доступно для вас как можно скорее. Безопасность — важный аспект работы сварщика. Независимо от того, какой метод вы используете, безопасность должна быть проблемой номер один. Даже если безопасность какое-то время не является вашей главной заботой, несчастные случаи все равно могут произойти. Безопасность жизненно важна при сварке. Было бы полезно, если бы вы были защищены от жары, ядовитых паров, огня и ударов. Если у вас нет подходящего оборудования, высока вероятность получения травмы. Пожарная безопасность: При использовании обычного сварочного вращателя возникает серьезная опасность возгорания.Перед резкой и сваркой горелкой важно проверить зону, в которой вы работаете, на предмет потенциальных горючих материалов. Переместите любые горючие материалы на расстояние не более 35 футов от того места, где вы будете работать. Было бы неплохо, если бы у вас всегда был под рукой огнетушитель. Химическая безопасность: Вам необходимо убедиться, что все предметы, которые вы режете или свариваете резаком, не содержат легковоспламеняющихся или взрывоопасных материалов, кислоты, смолы или жира. Персональная защита: Поскольку сварка излучает ультрафиолетовое излучение, вы должны носить защитные очки, защитные очки и каски.Перед началом сварки вам следует полностью снять кожух. Это предотвратит обычные травмы от сварочной вспышки. Во время сварки могут выделяться газы, такие как оксид азота или оксид углерода. Защитите себя от них, а также от металлов, таких как медь, ванадий и цинк, а также от фтора и кадмия. Поворачивающие валки для труб можно использовать для точного позиционирования и поворота в сварочных устройствах, таких как ветряные мачты или масляные трубы. Их можно изготовить в соответствии с индивидуальными потребностями клиента и, следовательно, настроить.Ролики можно настроить, добавив колеса для крепления гусениц или другие аксессуары. Несколько оборотов с регулируемой скоростью позволяют вам вращаться быстро или медленно, в зависимости от того, что вы делаете. Вы можете выбрать колеса Micarta, Steel или Rubber. Было бы неплохо, если бы вы хорошо разбирались в сварке. Очень важно сочетать точность и скорость с качеством. В этом вам поможет машина. Позиционирование системы имеет решающее значение, и валки для обточки труб необходимы как для легких, так и для тяжелых работ при сварке. Как эффективно использовать сварочный вращатель для повышения производительности? _Fengwei Machinery