Производство гранул и технология изготовления
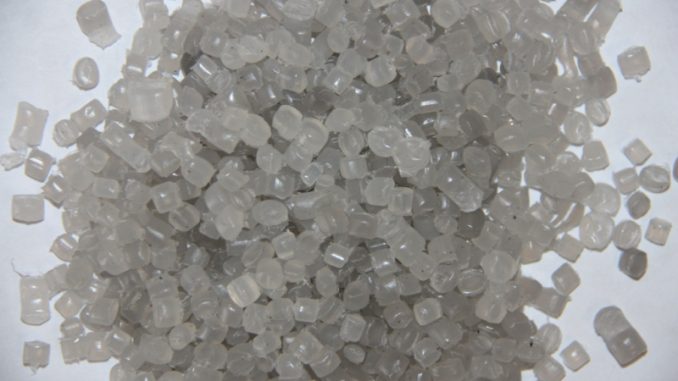
Производство гранул на сегодняшний день стало одним из популярных и прибыльных предприятий. И данное дело касается как производства гранулята из биологического материала, так и из искусственного.
Вторичная гранула или флекса – это результат переработки полиэтилена. Также под флексой понимают вторичное сырье, используемое для производства химического волокна.
В чистом виде – это хлопья различного цвета, из которых производят пластиковую тару. Это значит, что пластик можно бесконечное количество раз использовать повторно. Также химическое волокно, получаемое из переработанного пластика, идет на производство многих других товаров и изделий – черепица, пленка, упаковочная лента и так далее.
Получаемый из вторичного пластика продукт также классифицируется в зависимости от того, какой материал изначально использовался. Это могут быть гранулы пропилена PP, стрейча LLDPE, ПВД LDPE, ПНД HDPE, полистирола PS.
Гранулы LDPE, LLDPE используются для снижения стоимости производства упаковочных материалов для всех сфер. Они отличаются отсутствием токсинов, запаха, стойкостью к воздействию химических препаратов.
Полипропилен устойчив к влиянию высоких температур, механическим воздействиям. Также они устойчивы к влиянию химических средств, однако обладают низким уровнем морозоустойчивости. Данный вопрос решается путем добавки специальных компонентов, которые поднимают уровень устойчивости и устраняют данный недостаток. Широко применяется при производстве и изготовлении мебели, посуды, упаковки.
Гранулы ПВХ применяются практически во всех сферах благодаря своим свойствам. При их производстве отсутствует практически загрязнение пылью, они легко поддаются окрашиванию и дальнейшим технологическим операциям.
ПНД гранулы производится из полиэтилена различного уровня давления. Продукция из полиэтилена низкого давления обладает высоким показателем плотности, что повышает затраты на производство, и дает возможность получать продукцию с высокими эксплуатационными характеристиками. Чаще всего из данного материала производят упаковочный материал и полимерные трубы, бытовые емкости.
Сырьем для производства топливных гранул выступают отходы деревоперерабатывающей и торфоперерабатывающей промышленностей. Достаточно часто используются отходы из сельско-хозяйственного сектора – от отходов кукурузы и соломы до помета птицы.
Технология изготовления + видео как делают
По сути, технология производства гранул из полимеров очень простая – в дробилке рассортированное сырье измельчается, после чего масса нагревается и выдавливается из отверстия, благодаря чему получаются “нити”, которые затем сразу же погружаются в воду, где они охлаждаются. И на последней стадии уже остывшие нити разрезаются скоростными ножами на гранулы.
Видео как делают:
Кроме стационарных линий, существуют также мобильные или мини-установки по переработке пластика. Все агрегаты находятся в специальном контейнере, соединены между собой всеми необходимыми контактами еще на заводе-изготовителе. Для того чтобы установка работала, к месту ее расположения необходимо только подвести электричество, воду и канализацию для слива жидких отходов.
Переработка ПВХ-продукции проводится также на отдельном специальном оборудовании. Линия состоит из следующих агрегатов – дробилка, смеситель с двумя стадиями – холодный-горячий, с помощью которого перемешиваются пвх-композиции, и гранулятор, в состав которого входят экструдер, гранулятор и вибросито.

Как открыть производство травяных гранул
В сельском хозяйстве такой корм начал использоваться еще в 60-е годы прошлого века в СССР, и к тому были причины. Травяные гранулы содержат много белка, почти столько же, сколько и зерновые смеси, однако витаминов и минералов в них намного больше. При этом корм долгое время хранится, не теряя своих питательных свойств, в отличие от сена естественной сушки.
Сырье, из которого прессуются гранулы, называется витаминно-травяная мука. За основу для данной смеси трав берутся однолетние и многолетние травы, луговые растения и бобовые культуры. Самые популярные растения для приготовления ВТМ — люцерна, вика, овес, клевер, козлятник, крапива и люпин. Их соотношение в смеси влияет на питательность и свойства корма. Для того, чтобы получить из растения максимум пользы, культуры скашивают на ранних стадиях вегетации: бобовые растения — до бутонизации, а злаки — до колошения.
Гранулирование травы — почему необходимо?
Процесс гранулирования травяной муки имеет большой смысл, ведь ценность продукта в перспективе во много раз повышается. Почему это происходит?
Быстрая сушка
Сырье высушивается в кратчайшие сроки, что (как и при быстрой заморозке) позволяет сохранить львиную долю ценных веществ
Высвобождение питательных веществ
При дроблении разрушаются стенки клеток травы, высвобождается больше их полезного содержимого, что делает сырье для гранул более питательным и легкоусвояемым. При этом в процессе гранулирования в результате ряда химических процессов питательность еще более возрастает.
Сыпучесть
Форма гранул делает их универсальными, компактными, они легко пересыпаются между бункерами и по путям распределения корма. Объем массы уменьшается в разы, а потери сырья во время транспортировки до «конечного потребителя» снижается.
В 2 раза питательнее сена
Пищевая ценность 1 кг травяных гранул составляет 0,8 корм. единиц в то время как на 1 кг сена приходится 0,4 кормовых единицы. При этом содержание каротина в гранулах может быть выше в 20 раз, ровно как витаминов и белка. При длительном сроке хранения разница в ценности кормов увеличивается.
Высокая стоимость
Спрос на травяные гранулы довольно высокий. Из-за своих достоинств гранулированный корм ценится выше сена и муки в свободном состоянии — от 14000 руб за кг. Цены различаются из-за состава смесей.
Производство травяной муки и травяных гранул
Для установки линии травяных гранул потребуется помещение площадью около 250 м2 с высотой потолка от 4 м. Производство травяной муки и травяных гранул можно совмещать, поскольку для них требуется одинаковое оборудование с той разницей что травяная мука готова уже после второго измельчения. Также можно гранулировать сухую солому в топливные пеллеты. Рядом с производством должен находиться затемненный, хорошо проветриваемый склад, достаточно просторный, чтобы хранить продукт равномерно распределенным по площади, а не большим скоплением в одном месте.
Заготовка сырья
Скашивают растения обычно ранним утром, когда в растении содержится больше всего каротина — до 10 часов утра. Бобовые культуры скашиваюся по достижении 50 см, в конце стеблевания, а луговые травы — на этапе выхода в трубку, тогда они достигают 30 см. За вегетационный период можно собрать 3-4 урожая бобовых культур.
Норма потери травы при покосе и транспортировке равна 2% от общей массы. Обычно для сбора используются кормоуборочные комбайны. Популярное оборудование для производства гранул из травы — комбайны Дон-680, Марал-125, КСК-100А, Полесье-3000, а также прицепные комбайны с тракторами. Такие устройства не только срезают, но и тут же измельчают зеленую массу.
После первого измельчения фракция травы должна быть не больше 11 см, а основной объем должен состоять из частей до 3 см длиной. Тщательная настройка работы комбайна окупается меньшим расходов топлива при сушке и повышает качество травяных пеллет.
Важно! Скошенную массу необходимо быстро — в течении 3-х часов после скоса, направить на сушку. Для этого у предприятия должна быть отлаженная система транспортировки сырья с полей к заводу. Нельзя допускать длительного хранения травы перед сушилкой, тк она имеет свойство преть, в процессе чего теряет свою пользу.
Перевозят массы травы тракторными прицепами и автосамосвалами, установка высоких бортов и ограничителей поможет не растерять сырье в пути.
Сушка
Самый распространенный метод сушки травяной сечки — сушильный барабан АВМ с производительностью от 0,5 до 1,5 тонны в час. Масса подается в него при помощи скребкового или шнекового транспортера. В барабан нагнетается горячий воздух из теплогенератора, который работает на газовом, жидком или твердом топливе. Относительно дешево тепло твердотопливных теплогенераторов, которые используют крупнокусковые древесные отходы и топлвные пеллеты.
Сеченая трава высушивается очень быстро — в течение нескольких секунд, поэтому необходима тонкая настройка сушильного комплекса. Влажность травяной муки должна быть в пределах 8-12%, а травяной сечки — 10-15%. Пересушенная трава, в которой не более 6% влаги, становится пожароопасной и теряет белок и каротин (допускается потеря не более 5% в процессе сушки). Слишком влажная трава перегружает дробилку и забивает ее сита.
Дробление
После просушивания сырья травяная масса направляется на дополнительное измельчение к дробилкам роторного или молоткового типа. Десятки молотков на вращающемся валу разбивают сырье на мельчайшие части до того момента, пока частицы не смогут пройти через установленное внизу сито с заданной крупностью ячейки. Выгрузка материала из поддона сита происходит через пневматический шланг или же при помощи транспортера. Мелкие частицы травы переносятся в бункер-накопитель, где сырье накапливается перед процессом гранулирования. Внутри профессионального бункера – ворошителя есть мешалка, которая предотвращает слеживание травы. Устройство не только служит хранилищем, но и дозирует массу для подачи в гранулятор.
Гранулирование
Партии сырья равномерно подаются в приемный бункер гранулятора ОГМ, там измельченная трава подается шнеком в смеситель, пропаривается и поступает в прессовочный узел. Рабочие органы камеры – это вращающаяся кольцевая матрица и пресс-вальцы. Сырье попадает в клин между внутренней поверхностью матрицы и прокручивающимся вальцом, создается давление, и сырье проходит через отверстия матрицы (фильеры). Правильный подбор матрицы с нужной длиной фильер и качественной шлифовкой важен для получения качественных гранул. Они выходят со внешней стороны матрицы и обрезаются статичным ножом. Самый распространенный размер для гранул – 6 или 8 мм в диаметре.
Колонна охлаждения гранул
Процесс прессования происходит при высокой температуре и давлении. Для получения прочных гранул их необходимо сразу же охладить после выхода из гранулятора, чтобы избежать больших потерь каротина. Поэтому оборудование для производства травяных гранул всегда включает колонну охлаждения, куда травяные пеллеты переносятся с помощью конвейера. Там с помощью продува холодным воздухом продукт охлаждается до температуры окружающей среды. Там же ведется отсев мелких неспрессованных частиц, которые впоследствии направляются на гранулирование повторно. Процент отсева измеряет эффективность гранулирования.
Требования к травяным гранулам (согласно ГОСТу 18691-88):
-
диаметр — 3–25 мм;
-
длина — до 2-х диаметров;
-
плотность — 600–1 300 кг/м3;
-
процент крошения — до 12%;
-
процент сухого вещества — 85–90%.
Взвешивание и фасовка
Конечная станция – весовой дозатор и упаковка. Чаще всего для упаковки используются трехслойный крафтовые мешки по 30-50 кг – для розницы и мелкого опты, или же биг-бэги, вмещающие 1 тонну продукта – для среднего опта. Для крупных оптовых поставок гранулы обычно не пакуются, а загружаются в бункер транспортного средства. Для транспортировки тары с гранулами на склад и других погрузочных работ обычно приобретается универсальный погрузчик.
Складирование
Для хранения травяных гранул подходят затемненные помещения с хорошей циркуляцией воздуха. Наилучшая температура для склада – 2-4 °С, а уровень влажности воздуха – 65-75%. Такая же среда обычно бывает в зернохранилищах. Между штабелями необходимо соблюдать пространство: проходы и отступы от стен шириной 0,7 -1,25 м. Если предполагается хранить гранулы насыпью, хорошее решение для этого – силос с консервацией в среде инертных газов.
Спрос на травяные гранулы
Производство витаминно-травяных гранул рассчитано на животноводческие комплексы, зоопарки, заповедники, частные хозяйства. Если для крупного коровника, конной базы вам нужно отгружать товар десятками тонн, то более мелкие хозяйства могут закупать у вас продукт мешками в качестве витаминной добавки в рацион. Поэтому для полного удовлетворения спроса на травяные гранулы необходимо иметь разные виды упаковок и различные составы корма (базовые или дополнительно обогащенные, из ценных культур).
Для сбыта необходимо получить сертификацию. Ожидаемое время получения сертификата – 1 месяц. Для этого кормозаводчику нужны:
-
Анализы партий корма;
-
Ветеринарное свидетельство;
-
Пакет уставных документов;
-
Заявление в Роспотребнадзор.
Гранулированный витаминно-травяной корм является универсальным, он подходит для всех видов крупного рогатого скота, а также для некоторых других с/х животных.
-
Коровы, быки, телята;
-
Лошади, пони;
-
Волы, овцебыки;
-
Овцы, козы;
-
Кролики;
-
Свиньи;
-
Ламы, верблюды и многие другие мохнатые потребители травяного корма.
В зависимости от вида животных травяные гранулы могут использоваться как основной корм или как дополнительный источник питательных веществ. Так для лошадей и овец трава может составлять до 80% рациона, а для свиней – 10-15%.
Универсальность продукта, удобство в использовании, долгое время хранения и питательность обусловили высокий спрос на гранулы. В течение 2018 года постоянно объявляются тендеры на крупные поставки продукта. При этом спрос ограничивается не только российскими хозяйствами, особо выгодно поставлять такие гранулы за рубеж. Поэтому при должной организации логистики производство гранул из люцерны, овса, клевера, козлятника и др. никогда не будет убыточным.
Оборудование для производства травяных гранул
Приобретение правильной техники для завода грануляции – половина успеха. Если вам необходимо надежное оборудование для изготовления травяных гранул и экспертная помощь– компания АЛБ Групп готова организовать готовую линию линия производства травяных гранул под ключ. Мы ведем собственное производство основных агрегатов, в том числе центрального элемента линии – гранулятора ОГМ.
Почему выгодно работать с нами?
-
Мы предлагаем оборудование по средне-рыночным ценам, однако качество нашей техники сравнимо с востребованными европейскими аналогами.
-
Глубокая экспертиза в вопросах гранулирования различного органического сырья помогает нам скомпоновать эффективную линию для травы и комбикорма различных составов. Линии можно перепрофилировать под изготовление другого типа корма или же древесных пеллет.
-
Гарантия выхода на заявленную производительность.
-
Мы находимся в России, в Нижнем Новгороде, это означает, что вы всегда будете вовремя получать поддержку, а также необходимые комплектующие для линии. Каждый клиент становится нашим долгосрочным партнером.
-
Компания АЛБ Групп реализовала уже более десятка комбикормовых линий различной сложности.
-
Множество задокументированных положительных отзывов о работе наших комплексов.

Какое оборудование для производства травяной муки и гранул мы предлагаем?
Линия гранулирования травы состоит из следующих основных узлов:
1. Молотковая дробилка для первичного измельчения;
2. Сушильный барабан АВМ + теплогенератор/топочный блок;
3. Роторная дробилка ДРП для финального измельчения травы;
4. Смеситель кормов с возможностью ввода БМВД/ бункер-ворошитель;
5. Пресс-гранулятор ОГМ с кольцевой матрицей;
6. Ручная/автоматическая колонна охлаждения гранул;
7. Транспортеры для сырья: шнековые, ленточно-роликовые и ленточно-скребковые конвейеры;
8. Весовой дозатор и другое фасовочное оборудование.
Узнайте прямо сейчас, какое оборудование потребуется вам для организации производства витаминно-травяных гранул!
Наши консультанты разберут конкретно ваш случай и назовут примерную стоимость готовой линии и техники по отдельности.
Позвоните нам по телефону +7 (831) 410-85-25 или напишите нам в контактной форме сайта.
Оборудование для производства пеллет из опилок: пеллетная линия, технология
Развитие рынка пеллет – достойной альтернативы традиционным видам топлива – началось в нашей стране относительно недавно. Увеличение на данном рынке числа потребителей, использующих данное топливо для работы твердотопливных котлов высокой мощности, применяемых для обогрева промышленных объектов и крупных жилых строений, привело к тому, что все большее количество компаний, работающих в различных сферах, задумывается над приобретением оборудования для производства пеллет. По прогнозам специалистов, спрос на пеллеты в России будет только расти. Прежде всего это относится к топливным гранулам из опилок.
Мини-линия для изготовления топливных гранул состоит из нескольких технологических участков
При организации пеллетного производства (впрочем, как и любого другого) следует в первую очередь изучить все его нюансы, а также познакомиться с оборудованием, которое применяется для его практической реализации.
Технологический процесс производства пеллетного топлива
Для того чтобы изготовить пеллеты из опилок, с исходным материалом необходимо совершить целый перечень технологических манипуляций, каждая из которых решает определенные задачи.
Технологический процесс производства пеллетов из опилок – это последовательность определенных действий, выполняемых при помощи соответствующего оборудования.
Такими действиями, в частности, являются:
- очистка опилочной массы от посторонних примесей;
- предварительное измельчение очищенного материала;
- сушка сырья для пеллет;
- финишное измельчение уже высушенных опилок;
- доведение уровня влажности подготовленного материала до требуемого значения;
- процесс гранулирования опилочной массы;
- охлаждение готовой продукции и ее упаковка.
Промышленная схема производства пеллет
Поскольку все вышеперечисленные этапы технологического процесса производства топливных гранул осуществляются с определенной целью и имеют большое значение для получения качественной продукции, на каждом из них следует остановиться более подробно.
Оценка качества исходного сырья
Основное влияние на качество пеллет оказывают характеристики сырья. Важными в данном случае являются такие параметры, как тип древесины, из которой были получены опилки, степень их загрязненности посторонними примесями, влажность и размер фракций.
Хранилище для опилок должно быть сухим, вместительным и соответствовать нормам пожарной безопасности
Качественные характеристики материала для изготовления пеллет и степень его подготовки к производственному процессу определяют технологию получения готовой продукции, а также выбор оборудования. При этом необходимо учитывать следующие нюансы.
- В том случае, если влажность исходного материала достаточно высокая, для приведения ее к нормальным показателям потребуются мощные сушилки. Применение такого оборудования в процессе производства пеллет приведет к увеличению как энерго-, так и трудозатрат при реализации технологического процесса.
- Если в составе исходного сырья содержится много древесных частиц крупного размера, то в составе производственной линии по изготовлению пеллет должна присутствовать не только дробилка, но и оборудование для сепарации измельченной массы. Эксплуатация такой производственной линии также будет связана с повышенными энергозатратами.
- Эффективность технологического процесса и стабильность работы линии по производству пеллет во многом зависят от того, насколько однородным по породе древесины является исходный материал.
- Оценивая качество опилочной массы, которую планируется использовать для производства пеллетного топлива, следует обращать внимание на наличие в ее составе древесной коры, гнили и отходов от переработки старой древесины. Большое количество подобных включений в общей массе для производства топливных гранул снижает их энергетическую ценность и, соответственно, уменьшает стоимость готовой продукции.
- В составе исходного сырья могут содержаться такие посторонние примеси, как песок и камни. В этом случае пеллетная линия должна быть оснащена специальными улавливающими устройствами. Решает проблему с такими примесями и предварительная промывка материала, но в любом случае это увеличивает производственные расходы и, соответственно, себестоимость готовой продукции.
Таким образом, следует оценить характеристики опилочной массы, прежде чем пустить ее на производство пеллетов.
Для измерения влажности опилок используются влагомеры, состоящие из электронного блока и датчика, зонд которого размещается на конвейере или в бункере
Процесс предварительного измельчения опилок
В большинстве случаев для производства пеллет используются отходы деревообрабатывающих предприятий, которые поступают на пеллетное производство без предварительной сортировки. Естественно, что в таких отходах, кроме самих опилок, содержатся и другие составляющие – древесная кора, крупные щепки, бруски, горбыль и др.
Рабочими органами дробилок, используемых для грубого измельчения материала, являются вращающиеся молотки
Для того чтобы привести сырьевую опилочную массу в однородное состояние по размеру содержащихся в ней фракций, используется измельчитель. В качестве такого оборудования на стадии предварительного дробления сырьевой массы применяются молотковые дробилки, относящиеся к дековому типу. Дробилка данного типа может успешно использоваться для опилок, влажность которых доходит до 80 %, при этом практически не происходит их налипания на элементы внутренней конструкции оборудования.
Устройство молотковой дробилки для древесины
Процесс сушки
На пеллетное производство может поступать сырьевая масса с различной степенью влажности, при этом непосредственно при прессовании значение данного параметра не должно превышать 8–12 %. Таким образом, линия по производству пеллет должна содержать в своем составе установку для сушки сырья, в качестве которой, как правило, используется сушильный барабан. Для подачи влажного сырья в такое оборудование используются транспортеры шнекового типа, что является наиболее экономичным вариантом решения данного вопроса.
Схема многоконтурной аэродинамической сушилки
Аэродинамическая сушилка опилок, основу которой составляет сушильный барабан с возможностью регулирования скорости вращения, включает в свой состав несколько технических устройств:
- источник генерации и подачи горячего воздуха, работающий на природном газе или на любом другом виде топлива;
- циклон, в который опилочная масса поступает после сушки;
- бункер-накопитель, из которого опилки подаются в рабочую камеру сушильного барабана;
- циклоны, в задачи которых входит очистка топочных газов от пыли, а также улавливание частиц мелкой фракции, содержащихся в просушиваемом сырье;
- дымосос, обеспечивающий проход горячего воздуха с определенной скоростью через камеру сушильного барабана и воздушные каналы циклонов;
- шнековые транспортеры – оборудование, обеспечивающее подачу влажного сырья в камеру сушильного барабана и транспортировку уже высушенных опилок в бункер-накопитель.
Сушильный комплекс производительностью до 1000 кг/час с печью, работающей на дровах, опилках или щепе
Процесс сушки опилок, для осуществления которой используется сушилка аэродинамическая, выглядит следующим образом.
- Опилочная масса, которую необходимо просушить, подается в камеру сушильного барабана, ось вращения которого расположена в горизонтальной плоскости. При вращении такого барабана контролируется равномерность распределения в его рабочей камере загруженной сырьевой массы. Чтобы обеспечить безопасность процесса сушки опилок в барабане, в его конструкции предусмотрен специальный взрывной клапан.
- Ворошение опилок в сушильном барабане, что позволяет более оперативно и равномерно просушить их в потоке горячего воздуха, обеспечивают специальные лопатки, закрепленные на стенках рабочей камеры устройства.
- После просушивания до требуемого уровня влажности опилки из барабана поступают в циклон, где происходит их осаждение и дозированная подача в накопительный бункер.
- Очистка использованного горячего воздуха от древесной пыли также обеспечивается при помощи циклонного оборудования.
- За соблюдение всех режимов работы сушильного оборудования отвечает блок автоматики.
Технология дробления
Технология производства пеллет из опилок предусматривает, что сырье, поступающее в гранулятор, не должно содержать в своем составе частиц, длина которых превышает 4 мм. Большинство современных моделей оборудования для производства топливных пеллет работает на сырье, размеры частиц которого составляют не более 1,5 мм, а насыпная масса находится в пределах 150 кг/м3. Для достижения таких параметров сырья перед его подачей в прессовальное оборудование используется измельчитель. Как правило, это дробилка молоткового типа, которая способна работать с опилочной массой, имеющей влажность не выше 25 %.
Измельчитель, при помощи которого выполняется финишное дробление опилочного сырья, должен соответствовать определенным показателям производительности как по перерабатываемому сырью, так и по создаваемому воздушному потоку.
Объясняется это тем, что измельчитель, которым оснащается линия для производства пеллет, не только выполняет функции дробления, но и формирует воздушный поток, удаляющий измельченное сырье из рабочей камеры оборудования. Именно поэтому, выбирая измельчитель, следует ориентироваться на характеристики управляющего циклона.
Роторно-молотковая дробилка, предназначенная для измельчения древесной массы в процессе производства топливных пеллет
Подача сырья в накопительный бункер
Подача в циклонное оборудование измельченного в молотковой дробилке опилочного сырья, как уже говорилось выше, обеспечивается за счет давления воздуха, создаваемого при вращении молотков в рабочей камере. Задача циклона, которым оснащается практически любая современная линия производства пеллет, заключается в том, чтобы отделить опилки от потока воздуха, транспортирующего их из измельчительного устройства. Работает такая установка следующим образом.
- Поток воздуха, поступающий в циклон вместе с измельченными опилками, закручивается по спирали.
- Под действием центробежной силы опилки, двигающиеся вместе с потоком воздуха, прижимаются к стенкам рабочей камеры оборудования.
- Постепенно теряя скорость, опилки под действием силы тяжести осаждаются в нижней части камеры циклона, а воздух, вместе с которым они перемещались, выходит через выхлопную трубу.
- Накапливающиеся в нижней части камеры оборудования опилки выгружаются в накопительный бункер.
В состав линии производства пеллет входит входит циклон отвода сухой биомассы
Доведение влажности опилочной массы до требуемого уровня
После нескольких этапов предварительной подготовки опилки могут стать слишком сухими, что не позволит сформировать из них гранулы с плотной и однородной внутренней структурой. Производство пеллет из опилок предполагает, что их влажность непосредственно перед прессованием должна находиться в пределах 8–12 %. Если данное требование не выдерживается, прессуемое сырье необходимо дополнительно увлажнить.
Современное оборудование для производства пеллет из опилок оснащается шнековыми смесителями, в которых повышение влажности сырья осуществляется при помощи подаваемого в них под давлением пара. При выполнении такого технологического процесса следует постоянно мониторить уровень влажности опилочного сырья, чтобы вовремя прекратить обработку паром.
Формирование топливных гранул
Основная технологическая операция, которую выполняет для производства пеллет оборудование, – это формирование из рассыпчатого опилочного сырья гранул с плотной и однородной внутренней структурой. Для осуществления такой процедуры на современных линиях по производству пеллет устанавливают устройства с матрицами круглого или плоского типа. Оборудование, оснащенное матрицами круглого типа, больше подходит для того, чтобы прессовать материалы, не отличающиеся высокой твердостью. На таком оборудовании, в частности, производят не топливные гранулы, а пеллеты из более упругих и мягких материалов, которые применяются в химической, комбикормовой и пищевой промышленности.
Пресс-гранулятор с матрицей кольцевого типа
Изготовление древесных пеллет, оборудование для производства которых по принципу своего действия мало чем отличается от устройств, предназначенных для прессования более мягкого сырья, осуществляется при помощи матриц плоского типа. Производственный процесс по формированию пеллет, выполняемый на оборудовании как с круглыми, так и с плоскими матрицами, выглядит следующим образом. Катки с ребристой рабочей поверхностью, перекатываясь по поверхности матрицы, продавливает через отверстия в ней рассыпчатое сырье, формируя из него плотные гранулы цилиндрической формы. Длина готовых пеллет, выходящих с обратной стороны матрицы, регулируется при помощи специального ножа, совершающего возвратно-поступательные движения.
Толщина стенки матрицы зависит от диаметра рабочих отверстий
Заключительные этапы технологического процесса
Поскольку пеллеты, выходящие из прессового оборудования, разогреты до значительной температуры, их необходимо принудительно охладить, чтобы не допустить их «запаривания» в герметичной упаковке, что приведет к их насыщению влагой. Пелетами, которые подвергнутся такому процессу, нельзя будет пользоваться в качестве топлива. На современных производственных линиях по производству пеллетного топлива для осуществления технологической операции охлаждения применяется специальное оборудование, представляющее собой прямоточные колонны, в которых через готовые гранулы пропускается поток охлажденного воздуха.
Гранулы из охладительной колонны по транспортеру поступают в бункер готовой продукции, а затем отправляются на фасовку
Современные мини-линии по производству топливных гранул и линии более высокой производительности также комплектуются дозирующими устройствами и оборудованием, позволяющим оперативно упаковывать готовую продукцию в тару требуемого объема и веса.
Оценка статьи:
Загрузка…Поделиться с друзьями:
cуть вопроса значения топлива из древесных отходов тепловых гранул и где используют +Видео
Топливные пеллеты и чем они удобны? На всех производствах, использующих природное сырьё, решение проблемы переработки отходов является актуальной темой. В ряду таких промышленных отраслей стоит деревообработка. Производство мебели, строительных материалов, а изначально лесозаготовки производят большое количество материала не подходящего для прямого назначения.
Ненужная древесина скапливаясь, занимает территории, гниёт, залежи отходов создают пожарную опасность.
В чем удобство?
Использовать её как топливо в таком состоянии не представляется возможным по причинам неудобства доставки. Сучки занимают большой объём, но по количеству материала помещается мало в транспорт. Опилки рассыпаются под действием ветра и горят они плохо.
Удобство состоит в том, что переработка данного материала в необходимый формат позволит добиться хороших результатов в использовании отходов деревообрабатывающей промышленности.
Технология производства топливных пеллет решает с успехом большую часть данной проблемы.
Суть вопроса значения производства топлива из отходов
Как топливо, отходы из древесины легче всего применять после переработки их в более удобную форму. Топливные пеллеты представляют собой сформированные гранулы. Они имеют небольшую по размерам форму, диаметром 10-15 мм и в длину составляет до 50 мм. При формировке в состав не добавляются искусственные вредные вещества. Пыль на поверхности материала не образуется. На выходе получается настолько плотный материал, что имеет способность тонуть в воде.
Перевозить его можно автомобильным транспортом и железнодорожным путём. Грузить его удобно. Занимают гранулы мало места, но перевозятся в большом объёме.
Материалы
Для производства подходят:
Отходы при лесозаготовках. Сучки и ветки, вершинки, сухостой испорченный короедом, мелкая растительность, вырубаемая для очистки заимки.
- Подходит кора, обзольные части, комлевая обрезка при производстве пиломатериалов для строительства.
- Не используемые части древесины идущей на изготовление беловых товаров.
- Как дополнение к массе используется лузга семечек, отходы торфяной промышленности, отходы переработки на семя кукурузы, сосновых и еловых шишек, подсолнечника.
- Природный торф как самостоятельное сырьё для изготовления пеллет.
Важно! В любом составе необходимо присутствие материала хвойных пород, ввиду наличия смолы в древесине. Она является основным склеивающим веществом для выработки гранул.
Производство пеллет имеет большое значение для поддержания на хорошем уровне экологической обстановки. Освобождаются участки лесонасаждений для восполнения их запасов. Снижается уровень угрозы возникновения пожаров по вине скопления валежника.
Производство тепловых гранул
Процесс производства пеллет из древесины можно условно разделить на промышленное и кустарное изготовление.
Фабричное производство
Технологический процесс выпуска топливных гранул в заводских условиях заключается в нескольких этапах с использованием специальных станков:
Сырьё поступает в измельчитель крупных частей для получения щепы.
- Данный материал в сушильной камере, под действием горячего воздуха, освобождается от лишней влаги. В норме необходимо добиться 10% насыщения влагой для дальнейшего производства.
- Подсушенная масса поступает в аппарат для измельчения её в древесную муку.
- Помол древесины доставляется в прессовочный агрегат. Он представляет собой механизм, состоящий из двух барабанов вращающихся в разных направлениях с перфорированными стенками и прессовочного вала, который выдавливает содержимое камеры через отверстия стенок. Весь процесс получения качественного материала происходит под действием высокой температуры, достигающей значений 3000С. Такая температура необходима для выделения из сырья смолы лингина. Она производит склеивание состава.
- Полученные гранулы на следующем этапе проходят процесс охлаждения при помощи холодного воздуха. Сопутствующим образом этот воздушный поток очищает материал от несвязанной древесной муки и направляет её на повторную переработку. Гранулы в своей массе получаются чистыми предметами.
- Завершающим этапом производства топливных пеллет является их упаковка в герметичную полиэтиленовую упаковку.
Самостоятельное производство
Древесные гранулы своими руками можно получать посредством двух станков:
- Преобразователя крупных частей дерева в опилки.
- Прессовочного станка. Он состоит из тяжёлого вала, имеющего на концах зубчатые шестерни и прессовочной камеры. В её основании располагается перфорированный лист металла. Вал в движение приводится посредством электрического двигателя. Шестерни при вращении дополнительно измельчают сырьё. Под давлением через перфорированный лист выдавливается материал в виде гранул. Трение, производимое шестернями по опилкам, вызывает нагревание древесины и выделение смолы для склеивания субстанции.
Где используют древесные гранулы
Основным направлением применения пеллет остаётся получение тепловой энергии при их сгорании. КПД при этом у данного материала больше чем у каменного угля и природного газа и составляет 95%. Даже остающаяся зола идёт для снижения кислотности почвы в сельском хозяйстве. Это свойство применяется для отопления помещений и нагрева воды в твёрдотопливных бойлерах.
Для автоматизации процесса поступления очередной порции гранул в камеру сгорания, производятся специальные пеллетные котлы. Принцип его работы основан на постоянной подаче топлива из накопительного бункера в камеру сгорания посредством вращающегося шнека. Скорость вращения рассчитана по времени сгорания порции в камере. Такой механизм необходим при организации отопления помещения как непрерывного процесса.
Гранулы из древесной муки используются не только для тепла. Они обладают высокой способностью к абсорбции жидких сред. Поэтому их применяют в других отраслях:
- В животноводстве, как экологически чистый подстилочный материал.
- В производстве топлива как абсорбент.
- Для ликвидации ЧС для сбора загрязняющих веществ.
- Для наполнителя фильтров очистки газа от серы.
- Для топлива мангалов.
- Как наполнитель кошачьих туалетов.
Заключение
Гранулы, произведённые из древесины, являются частью углеродного обмена в природной среде. При сгорании пеллет выделяется количество CO равное поглощённому объёму. Равное количество углекислоты выделяется при полном разложении древесины. Изготавливаются они из сырья, относящегося к возобновляемым источникам углеродного топлива.