Структура ПЛК (Лекция) | ПЛК
ЗАТРАГИВАЕМЫЕ ВОПРОСЫ
1. Обобщенная структура ПЛК
2. Дискретные входы
3. Аналоговые входы
4. Специальные входы
5. Дискретные выходы
6. Системное и прикладное программное обеспечение
7. Рабочий цикл ПЛК
8. Языки программирования ПЛК
1. Обобщенная структура ПЛК
ПЛК представляют из себя микропроцессорное (МПС) устройство, предназначенное для сбора, преобразования, обработки, хранения информации и выработки команд управления. Каждый из них представляет собой вычислительную машину, имеющую некоторое множество входов и выходов.
Рис. 1. Обобщенная структура программируемого контроллера
Контроллер отслеживает изменение входов и вырабатывает программно определенное воздействие на выходах. Обладая памятью, ПЛК в зависимости от предыстории событий, способен реагировать по-разному на текущие события. Такая модель соответствует широко известным конечным автоматам. Однако возможности перепрограммирования, управления по времени, развитые вычислительные способности, включая цифровую обработку сигналов, поднимают ПЛК на более высокий уровень.
Первоначально они предназначались для замены релейно-контактных схем, собранных на дискретных компонентах – реле, счетчиках, таймерах, элементах жесткой логики. Принципиальное отличие ПЛК от релейных схем заключается в том, что все его функции реализованы программно. На одном контроллере можно реализовать схему, эквивалентную тысячам элементов жесткой логики. При этом надежность работы схемы не зависит от ее сложности.
2. Дискретные входы
Один дискретный вход ПЛК способен принимать один бинарный электрический сигнал, описываемый двумя состояниями – включен или выключен. На уровне программы это один бит информации. Кнопки, выключатели, контакты реле, датчики обнаружения предметов и множество приборов с выходом типа «сухой контакт» или «открытый коллектор» непосредственно могут быть подключены к дискретным входам ПЛК.
Состояние некоторых первичных приборов систем промышленной автоматики определяется целым цифровым словом. Для их подключения используют несколько дискретных входов.
Системное программное обеспечение ПЛК включает драйвер, автоматически считывающий физические значения входов в оперативную память. Благодаря этому, прикладному программисту нет необходимости разбираться с внутренним устройством контроллера. С точки зрения прикладного программиста дискретные входы это наборы бит, доступные для чтения в ОЗУ.
Все дискретные входы (общего исполнения) контроллеров обычно рассчитаны на прием стандартных сигналов с уровнем 24 В постоянного тока. Типовое значение тока одного дискретного входа (при входном напряжении 24 В) составляет около 10 мА. В простейшем случае, для подключения нормально разомкнутого контакта, дискретный вход и сам контакт необходимо подключить последовательно к источнику питания в 24 В. Для питания таких внешних датчиков нужен отдельный источник питания. Иногда источник питания внешнего маломощного оборудования включают в состав ПЛК. Дискретные входы некоторых контроллеров рассчитаны на прием уровней сигналов с напряжениями высокого уровня, в том числе переменного тока (например, в 220… 240 В).
Все современные датчики, базирующиеся на самых разнообразных физических явлениях (емкостные, индуктивные, ультразвуковые, оптические и т.д.), как правило, имеют встроенные первичные преобразователи и не требуют дополнительного согласования при подключении к дискретным входам ПЛК.
3. Аналоговые входы
Аналоговый электрический сигнал отражает уровень напряжения или тока, соответствующий некоторой физической величине, в каждый момент времени. Это может быть температура, давление, вес, положение, скорость, частота и т. д.
Поскольку ПЛК является цифровой вычислительной машиной, аналоговые входные сигналы обязательно подвергаются аналого-цифровому преобразованию (АЦП). В результате, образуется дискретная переменная определенной разрядности. Как правило, в ПЛК применяются 8 — 12 разрядные преобразователи, что в большинстве случаев, исходя из современных требований по точности управления технологическими процессами, является достаточным. Кроме этого АЦП более высокой разрядности не оправдывают себя, в первую очередь из-за высокого уровня индустриальных помех, характерных для условий работы контроллеров.
Для аналоговых входов наиболее распространены стандартные диапазоны постоянного напряжения -10…+10 В и 0…+10 В. Для токовых входов – 0…20 мА и 4…20 мА. Особые классы аналоговых входов представляют входы, предназначенные для подключения термометров сопротивления и термопар. Здесь требуется применение специальных технических решений (трехточечное включение, источники образцового тока, схемы компенсации холодного спая, схемы линеаризации и т. д.). Для достижения хороших результатов измерений должно обеспечиваться высокое качество выполнения монтажа внешних аналоговых цепей.
Практически все модули аналогового ввода являются многоканальными. Входной коммутатор подключает вход АЦП к необходимому входу модуля. Управление коммутатором и АЦП выполняет драйвер системного программного обеспечения ПЛК. Прикладной программист работает с готовыми значениями аналоговых величин в ОЗУ.
Несоответствие физических значений напряжений и токов датчиков уровням входов/выходов контроллера решается применением нормирующих преобразователей или заменой нестандартных датчиков.
4. Специальные входы
Стандартные дискретные и аналоговые входы ПЛК способны удовлетворить большинство потребностей систем промышленной автоматики. Необходимость применения специализированных входов возникает в случаях, когда непосредственная обработка некоторого сигнала программно затруднена, например, требует много времени.
Наиболее часто ПЛК оснащаются специализированными счетными входами для измерения длительности, фиксации фронтов и подсчета импульсов.
Например, при измерении положения и скорости вращения вала очень распространены устройства, формирующие определенное количество импульсов за один оборот – поворотные шифраторы. Частота следования импульсов может достигать нескольких мегагерц. Даже если процессор ПЛК обладает достаточным быстродействием, непосредственный подсчет импульсов в пользовательской программе будет весьма расточительным по времени. Здесь желательно иметь специализированный аппаратный входной блок, способный провести первичную обработку и сформировать, необходимые для прикладной задачи величины.
Вторым распространенным типом специализированных входов являются входы способные очень быстро запускать заданные пользовательские задачи с прерыванием выполнения основной программы – входы прерываний.
5. Дискретные выходы
Один дискретный выход ПЛК способен коммутировать один электрический сигнал. Также как и дискретный вход, с точки зрения программы это один бит информации.
Нагрузкой дискретных выходов могут быть лампы, реле, соленоиды, силовые пускатели, пневматические клапаны, индикаторы и т. д.
Простейший дискретный выход ПЛК выполняется в виде контактов реле. Такой выход достаточно удобен в применении и прост. Однако он обладает характерными недостатками всех реле – ограниченный ресурс, низкое быстродействие, разрушение контактов при работе на индуктивную нагрузку. Альтернативным решением дискретного выхода является электронный элемент – например, схема с открытым коллектором. Наиболее широким спросом пользуются дискретные выходы средней мощности (до 1А, 24В).
Практика эксплуатации доказала нецелесообразность сосредоточения в корпусе ПЛК большого числа силовых коммутирующих элементов. При необходимости управления сильноточными нагрузками применяются выносные устройства коммутации. Таким образом, установка силовых коммутирующих приборов осуществляется максимально близко к нагрузке. В результате, сокращается длина силовых монтажных соединений, снижается стоимость монтажа, упрощается обслуживание, уменьшается уровень электромагнитных помех.
6. Системное и прикладное программное обеспечение
Программное обеспечение универсальных контроллеров состоит из двух частей. Первая часть это системное программное обеспечение. Проводя аналогию с программным обеспечением ЭВМ можно сказать, что оно выполняет функции операционной системы, т.е. управляет работой узлов контроллера, занимается организацией их взаимосвязи, внутренней диагностикой. Системное программное обеспечение ПЛК расположено в постоянной памяти в адресном пространстве центрального процессора и всегда готово к работе. По включению питания, ПЛК готов взять на себя управление системой уже через несколько миллисекунд.
Другая часть программного обеспечения универсальных контроллеров это прикладные программы управления конкретным процессом. Эти программы создаются разработчиком системы управления.
7. Рабочий цикл ПЛК
ПЛК работают циклически по методу периодического опроса входных данных. Рабочий цикл ПЛК включает 4 фазы:
1. опрос входов,
2. выполнение пользовательской программы,
3. установку значений выходов,
4. некоторые вспомогательные операции (диагностика, подготовка данных для отладчика, визуализации и т. д.).
Выполнение 1 фазы обеспечивается системным программным обеспечением. После чего управление передается прикладной программе, а по ее завершению управление опять передается системному уровню. За счет этого обеспечивается максимальная простота построения прикладной программы – ее создатель не должен знать, как производится непосредственное управление аппаратными ресурсами. Прикладная программа имеет дело с одномоментной копией значений входов в памяти. Внутри одного цикла выполнения программы, значения входов можно считать константами. Такая модель упрощает анализ и программирование сложных алгоритмов.
Очевидно, что время реакции на событие будет зависеть от времени выполнения одного цикла прикладной программы. Определение времени реакции – времени от момента события до момента выдачи соответствующего управляющего сигнала – поясняется на рис 1.19.
Рис. 2. Рабочий цикл программы ПЛК
В технических характеристиках ПЛК приводится типовое время рабочего цикла. При его измерении пользовательская программа должна содержать 1К логических команд (на языке IL (STL) МЭК 61131-3). Сегодня ПЛК имеют типовое значение времени рабочего цикла, измеряемое единицами миллисекунд и менее. События, требующие быстрой реакции, выделяются в отдельные задачи – задачи обработки прерываний, приоритетность и период выполнения которых можно изменять.
8. Языки программирования ПЛК
На сегодняшний день ПЛК на 90 % являются программным продуктом. Для их программирования в настоящее время используются специализированные языки. Специализация языков ПЛК заключена в упрощении их применения и приближении к предметной области. Контроллеры обеспечиваются средствами визуального прикладного проектирования.
Программируемые логические контроллеры (плк). Принципы работы плк сканирующего типа. Рабочие циклы и время реакции плк.
Программи́руемый логи́ческий контро́ллер(сокр.ПЛК;англ.programmable logic controller, сокр.PLC; более точный перевод на русский — контроллер с программируемой логикой),программируемый контроллер— электронная составляющаяпромышленного контроллера, специализированного (компьютеризированного) устройства, используемого дляавтоматизации технологических процессов. В качестве основного режима работы ПЛК выступает его длительное автономное использование, зачастую в неблагоприятных условиях окружающей среды, без серьёзного обслуживания и практически без вмешательства человека.
Иногда на ПЛК строятся системы числового программного управлениястанков.
ПЛК являются устройствами реального времени. ПЛК имеют ряд особенностей, отличающих их от прочих электронных приборов, применяемых в промышленности:
в отличие от микроконтроллера (однокристального компьютера) — микросхемы, предназначенной для управления электронными устройствами — областью применения ПЛК обычно являются автоматизированные процессы промышленного производства в контексте производственного предприятия;
в отличие от компьютеров, ориентированных на принятие решений и управление оператором, ПЛК ориентированы на работу с машинами через развитый ввод сигналов датчиков и вывод сигналов на исполнительные механизмы;
в отличие от встраиваемых систем ПЛК изготавливаются как самостоятельные изделия, отдельные от управляемого при его помощи оборудования.
В системах управления технологическими объектами логические команды, как правило, преобладают над арифметическими операциями над числами с плавающей точкой, что позволяет при сравнительной простоте микроконтроллера (шинышириной 8 или 16 разрядов), получить мощные системы, действующие в режимереального времени. В современных ПЛК числовые операции в языках их программирования реализуются наравне с логическими. Все языки программирования ПЛК имеют лёгкий доступ к манипулированию битами в машинных словах, в отличие от большинства высокоуровневых языков программирования современных компьютеров.
ПЛК сканирующего типа работают циклически по методу периодического опроса входных данных. Именно такая модель обеспечивается в среде программирования CoDeSys. Рабочий цикл ПЛК включает 4 фазы:
опрос входов,
выполнение пользовательской программы,
установку значений выходов и
некоторые вспомогательные операции (диагностика, подготовка данных для отладчика, визуализации и т.д).
Прикладная программа имеет дело с одномоментной копией значений входов. Внутри одного цикла выполнения программы, значения входов можно считать константами. Такая модель упрощает анализ и программирование сложных логических и последовательностных алгоритмов. Очевидно, что время реакции на событие будет зависеть от времени выполнения одной итерации прикладной программы.
Рис.14.1
Рабочий цикл для ПЛК работающего по
методу периодического опроса входных
данных.
В технических характеристиках ПЛК приводится типовое время рабочего цикла. При его измерении пользовательская программа должна содержать 1К логических команд (на языке IL МЭК 61131-3). Сегодня ПЛК имеют типовое значение времени рабочего цикла, измеряемое единицами миллисекунд и менее. События, требующие быстрой реакции, выделяются в отдельные задачи, приоритетность и период выполнения которых можно изменять.
Рабочие циклы и время реакции ПЛК.
Задачи управления требуют непрерывного циклического контроля. В любых цифровых устройствах непрерывность достигается за счет применения дискретных алгоритмов, повторяющихся через достаточно малые промежутки времени. Таким образом, вычисления в PLC всегда повторяются циклически. Одна итерация, включающая замер, обсчет и выработку воздействия, называется рабочим циклом PLC.
Выполняемые действия зависят от значения входов контроллера, предыдущего состояния и определяются пользовательской программой.
По включению питания PLC выполняет самотестирование и настройку аппаратных ресурсов, очистку оперативной памяти данных (ОЗУ), контроль целостности прикладной программы пользователя. Если прикладная программа сохранена в памяти, PLC переходит к основной работе, которая состоит из постоянного повторения последовательности действий, входящих в рабочий цикл.
Рабочий цикл PLC состоит из нескольких фаз.
1. Начало цикла.
2. Чтение состояния входов.
3. Выполнение кода программы пользователя.
4. Запись состояния выходов.
5. Обслуживание аппаратных ресурсов PLC.
6. Монитор системы исполнения.
7. Контроль времени цикла.
8. Переход на начало цикла.
Абсолютное большинство PLC работают по методу периодического опроса входных данных (сканирования). PLC опрашивает входы, выполняет пользовательскую программу и устанавливает необходимые значения выходов. Для математических систем характеристикой качества работы является правильность найденного решения. В системах реального времени помимо правильности решения определяющую роль играет время реакции. Логически верное решение, полученное с задержкой более допустимой, не является приемлемым.
Время реакции — это время с момента изменения состояния системы до момента выработкисоответствующей реакции. Если изменение значений входов произошло непосредственно перед фазой чтения входов, то время реакции будет наименьшим и равным времени сканирования. Худший случай, когда изменение значений входов происходит сразу после фазы чтения входов. Тогда время реакции будет наибольшим, равным удвоенному времени сканирования минус время одного чтения входов. Иными словами, время реакции PLC не превышает удвоенного времени сканирования (Рис. 14.2).
Рис.14.2. Время сканирования
Помимо времени реакции PLC, существенное значение имеет время реакции датчиков и исполнительных механизмов, которое также необходимо учитывать при оценке общего времени реакции системы.
Существуют PLC, которые реализуют команды непосредственного доступа к аппаратуре входов и выходов, что позволяет обрабатывать и формировать отдельные сигналы с длительностью меньшей длительности рабочего цикла.
Для уменьшения времени реакции сканирующих контроллеров алгоритм программы разбивается на несколько задач с различным периодом исполнения. В наиболее развитых системах пользователь имеет возможность создавать отдельные программы, исполняемые по прерыванию, помимо кода, исполняемого в рабочем цикле. Такая техника позволяет PLC существенно форсировать ограничение реакции временем сканирования при небольшом количестве входов, требующих сверхскоростной реакции. Время цикла сканирования является базовым показателем быстродействия PLC. Программа PLC может рассматриваться как постоянно бегущая замкнутая цепь. Инструкция пользователя считывается непрерывно и когда считывается последняя инструкция, операция начинается снова. Это называется сканированием программы, а период – временем сканирования. Время зависит от размера программы и скорости процессора.
Программируемые логические контроллеры (ПЛК) — Control Engineering Russia
Различий в программном обеспечении гораздо больше, чем в аппаратных средствах, говорят респонденты. Участников проведенного опроса также интересуют сетевые возможности контроллеров
Мало приятного в том, что при разработке системы управления, в поиске необходимых компонентов приходится проводить много времени в кипе каталогов производителей или поставщиков. Даже сравнительно небольшая система управления требует большого количества выбранных, рекомендованных и заказанных элементов простейшей системы управления, особенно использующей стандартную релейную логику. Реле, базы реле, таймеры, конечные выключатели, провода, кабельные каналы, сигнальные лампы, кнопки и прочее. Последнее, но не менее важное – шкаф для установки оборудования. Это только часть того, что необходимо для начала проекта.
Используйте программируемый логический контроллер (ПЛК) или его преемника – программируемый контроллер автоматизации (PAC). Эти устройства совмещают функции множества других изделий и могут использоваться в большинстве разрабатываемых систем управления. Согласно опросу, проведенному Control Engineering в этом году, производители контроллеров предлагают инженерам автоматизации продукты, позволяющие работать проще и эффективнее при меньшей стоимости.
В последнем анкетировании, организованном совместно с Reed Research, 548 ответчиков заявили, что современный ПЛК вполне оправдывает их надежды. Из них 57 % используют ПЛК для собственного производства, и 22 % для OEM приложений. Оставшиеся 21 % приобретают и используют контроллеры для обоих приложений. Используемые ПЛК значительно различаются по количеству точек ввода/вывода. Классификация по типу контроллера, показывает, что инженеры управления используют главным образом микроПЛК – от 15 до 128 точек ввода/вывода, 38.7 % используемых контроллеров. PLC среднего размера, 128 – 512 точек ввода/вывода, применяется в 32.7 % случаев, большие ПЛК, более 512 точек ввода/ вывода – 18.4 %. Реже используются наноПЛК, менее 15 точек ввода/вывода, около 10.4 %. В целом, в диапазон от 15 до 512 точек попадают почти три четверти проданных приборов.
Как обстоят дела у возможного приемника ПЛК, программируемого контроллера автоматизации (PAC)? Согласно прошлогоднему обзору, 44 % пользователей рассматривали возможность использования этих высокозащищенных PC в форм-факторе ПЛК. Даже, несмотря на растущие возможности PAC, число инженеров, планирующих использовать эти устройства, снизилось до 31 %. По всей вероятности, инженеры управления хотели бы установить PAC на новых или модернизируемых установках. Из тех участников, которые планируют использовать это оборудование в будущем, большинство (75 %) будут применять их как дополнение к ПЛК. Остальные заменят ПЛК на PAC.
Сетевые опции
Сферы использования ПЛК в полной мере отражают отрасли применения систем автоматизации. Как и ожидалось, управление станками (82 %) все еще самая распространенная сфера применения. Управление процессом (74 %), управление движением (55 %), управление периодическими процессами (31 %), диагностические приложения (25 %). Реже всего PLC используются для обеспечения безопасности производства (1 %).
Методы коммуникации с другими системами управления являются главным показателем гибкости современного ПЛК. Как говорят участники, сетевые протоколы используются в 69 % установленных ПЛК, оставшиеся 31 % используются как автономные приборы. Большинство подключенных к сети контроллеров обменивается информацией с персональными компьютерами и PAC-контроллерами и столько же связано с другими ПЛК. Чуть больше 5 % устройств используется в распределенных системах управления.
Сетевые протоколы ПЛК обеспечивают очень большую гибкость системы управления. Несмотря на то, что существуют очевидные фавориты, такие как Ethernet, последовательный RS232/RS-485 и 4-20 мА, список доступных протоколов гораздо шире и разнообразнее. После трех вышеуказанных лидеров, в порядке популярности:
DeviceNet
Allen-Bradley Remote I/O
Modbus
ControlNet
Wireless protocol
Profibus
HART.
В ПЛК используются различные языки программирования, но обзор выявил явные предпочтения. Релейная схема (96 %) и функциональные блоки (50 %) возглавляют список. Этот порядок не изменился с 2005 (см. сопроводительную диаграмму). Ясно, что сместить релейную схему с вершины будет очень трудно, но программирование с использованием функциональных блоков достигло большого прогресса за последние два года. Структурный текст поднялся с шестого места в 2005 году с 13 % на третье в 2007 с 24 %. Худший результат у языка программирования C, который опустился с четвертого места в 2005 на шестое. Программирование списком инструкций за это же время переместилось с пятого на шестое место.
Процесс выбора ПЛК не так прост. Тем не менее, некоторые свойства и функции были названы очень важными при определении, рекомендации и/или покупке ПЛК. На первое место в своем хит-параде участники опроса поставили встроенные коммуникационные возможности. Другими характеристиками, выстроенными в порядке убывания значимости, являются: возможности ПИД-регулирования, малое время цикла, объем доступной памяти, поддержка функций управления перемещением, съемные картриджи памяти и беспроводные технологии.
Считают ли инженеры, что поставщики ПЛК выполняют все требования? Вполне довольны 95 % респондентов, оставшиеся 5 %, столкнулись с проблемами, которые повлияют на дальнейшие решения при покупке оборудования. Два самых часто встречающихся комментария к процессу выбора ПЛК участников опроса отражают отношение специалистов. Для этих инженеров, «стандартизация» и «отказ от закупки более сложного ПЛК, чем это необходимо» являются ключевыми критериями при выборе.
На что обращать внимание при покупке
Несмотря на то, что лишь 53 % опрошенных полагают, что объем приобретаемых ПЛК в следующем году будет тем же, рынок остается достаточно здоровым. ПЛК для производств будут приобретаться в таком же объеме и 38 % полагают, что объем закупок в ближайшее время вырастет. Какие же функции должно реализовывать приобретаемое оборудование? Важнейшие указаны ниже (в порядке убывания значимости):
Универсальная среда программирования для различных аппаратных платформ
ПЛК с системами распределенного ввода/вывода
ПЛК со встроенными модулями ввода /вывода
Связь ПЛК с ПК
Дублирование процессора и модулей ввода/вывода
Микро ПЛК
ПЛК с поддержкой web-технологий, включая оповещение по телефону/электронной почте
ПЛК со встроенными микропроцессорами PC
нано ПЛК
высоконадежные PC-контроллеры с открытой архитектурой
Переносные устройства программирования
Доступность и важность самой главной характеристики в этом списке неоднократно проявлялась в ответе на вопрос, как выбрать ПЛК: «Не пытайтесь найти самое дешевое оборудование; переподготовка специалистов для работы с новым программным обеспечением сведет всю экономию к нулю. Выберите одного-двух производителей и работайте только с ними», + вот типичный ответ.
Другой инженер управления утверждает: «Самое главное – программное обеспечение для программирования контроллеров. Различий в удобстве использования программного обеспечения гораздо больше, чем в железе». Наконец, некоторые респонденты резюмируют: «стандартизированный язык программирования крайне необходим». В любом случае, такой список пожеланий позволяет производителям ПЛК/PAC сконцентрироваться на действительно необходимых функциях.
Продукты
Используя предоставленный список, участники проведенного Control Engineering опроса, назвали следующих производителей ведущими поставщиками ПЛК. Продукция этих компаний представлена ниже. Дополнительные данные обзора, включающие вопросы пользователей, стенограмму комментариев и информацию еще о 25 компаниях-производителях ПЛК представлены в отчете, доступном на Control Engineering Resource Center. Найдите «PLCs» на сайте www.controleng.com, с последними новостями и продуктами.
Больше продуктов и производителей
Следующие поставщики также представлены в исследовании рынка продукции. Найдите «PLC» на сайте www.controleng.com, с отчетом об исследовании в Resource Center, и дополнительные описаниях продуктов в разделах Archive и New Products.
ABB (Bristol Babcock)
Advanced Micro Controls
B&R Industrial Automation
Baldor Electric
Beckhoff Automation
BoschRexroth
Control Technology Corp.
Eaton (Cutler-Hammer)
Emerson Process Management
Fuji Electric
Hitachi
IDEC
Keyence
Mitsubishi Electronics
Moeller Electric
National Instruments
Omega Engineering
Omron Electronics
Opto 22
Panasonic Electric Works
Phoenix Contact (Entivity)
Toshiba
Wago
Yaskawa Electric
Yokogawa
Гибкость, стандартизация
Для разработчиков оборудования, пытающихся стандартизировать используемые платформы управления, контроллер Allen-Bradley CompactLogix L45 является решением с гибкой масштабируемостью и встроенными функциями управления перемещением. Контролируя до восьми осей перемещения, контроллер L45 является расширением платформы Logix Control, обеспечивающей интегрированное управление движением и возможность организации распределенного управления для небольших приложений. Платформа расширила возможности процессора, среды разработки, сетевые и операторские технологии, обеспечивая полноценную интеграцию и расширяемость для использования в дискретных и серийных производствах, приложениях безопасности и перемещения.
www.rockwellautomation.com.
Rockwell Automation
Модули с высоким разрешением
AutomationDirect расширил линейку модулей DirectLogic, добавив 16-разрядные аналоговые платы, разработанные для контроллеров DL05 и DL06. Восьмиканальный модуль токовых входов F0-08ADH-1 работает с диапазоном 0-20 мА. F0-08ADH-2 имеет перемычку для выбора типа входного сигнала 0-5 В или 0-10 В. Четырехканальный F0-04DAH-1 и восьмиканальный F0-08DAH-1 модули вывода работают с диапазоном 4-20 мА, а четырехканальный F0-04DAH-2 и восьми канальный F0-08DAH-2 с диапазоном 0-10 В. Начальная цена – 129 $ (модуль F0-08ADH-1).
www.automationdirect.com
Automation Direct
Распределенный монтаж в поле
По заявлению компании Siemens Energy & Automation, впервые появилась возможность организовать распределенную сеть Ethernet, использующую периферию бесшкафного монтажа Simatic ET200pro CPU. Степень защиты IP-65/67 позволяет устанавливать контроллер непосредственно на управляемый агрегат. Монтаж дополнительного процессора на полевом уровне уменьшает нагрузку на центральный CPU и допускает использование процессора в тяжелых эксплуатационных условиях с широким температурным диапазоном. Контроллер имеет обширные коммуникационные возможности, включая совмещенный MPI/Profibus-DP порт и три встроенных порта Ethernet. Помимо возможности работать в режиме Profibus master/slave, CPU поддерживает протокол Profinet через встроенный Ethernet порт, реализующий дополнительные возможности сети, такие как работа в детерминированном реальном времени.
www.usa.siemens.com.
Siemens Energy & Automation
PAC добавлены к линейке PLC
В линейке PLC Modicon, представленной в 1968 году, появился контроллер Modicon M340 PAC, платформа, реализующая функции коммуникаций, управления перемещением и сбора данных в различных средах программирования. Семейство M340 упрощает установку и эксплуатацию, используя один программный продукт: Unity Pro, полностью соответствующий стандарту IEC 61131-3. Предлагая на выбор любой из 5 языков IEC, графическое программирование, и расширенную online-поддержку, M340 обеспечивает быстрое выполнение, как логических, так и математических операций. Контроллер имеет 4 Мбайт внутренней памяти (расширяемой до 16 Мбайт), 256 Кбайт данных, и способен выполнять до 70 Кбайт программного кода.
www.us.telemecanique.com
Schneider Electric
Микроконтроллер с низкими эксплуатационными расходами
Новая система VersaMax Micro 64 от GE Fanuc Automation является частью линейки контроллеров VersaMax Micro и спроектирована с учетом необходимости уменьшения стоимость обслуживания. Удобный модуль памяти подключается к контроллеру для загрузки программы без персонального компьютера. Программа Proficy Machine Edition Logic Developer PDA позволяют использовать карманный компьютер для просмотра/изменения данных, диагностики, установки значений, и конфигурирования. Micro 64 соответствует международным стандартам, поддержка осуществляется офисами продаж и распространения GE Fanuc Automation.
www.gefanuc.com
GE Fanuc Automation
Вконтакте
Google+
ПЛК становятся миниатюрными, производительными, интеллектуальными
Интеграция модулей ввода/вывода и универсальное программное обеспечение являются ключевыми возможностями ПЛК
По этим и ряду других причин подписчики Control Engineering, судя по недавнему опросу Reed Research Group, планируют покупку большего числа ПЛК в наступившем году. Среди 202 респондентов, занимающихся составлением спецификаций или покупкой ПЛК, 59% делают это для конечных потребителей, 19% – для изготовителей оборудования и 22% – для обоих применений.
45% респондентов сообщили, что они увеличат затраты на ПЛК, 49% – оставят на прежнем уровне и 6% предполагают уменьшить; в 2002 г. только 29% планировали увеличить покупки, 64% оставить на прежнем уровне и 7% уменьшить.
Опрос показал также, что в наступившем году ожидается существенное увеличение беспроводных соединений с ПЛК. Возрастет также иx использование Ethernet.
Популярность емкости ПЛК (выраженной числом входов/выходов) в 2004 г. осталась на уровне 2002 г.; но использование систем управления на базе ПК и систем soft-logic немного увеличилось. Микро ПЛК (от 16 до 128 входов/выходов) использовали 27%, ПЛК среднего размера (от 129 до 512 входов/выходов) – 27%, большие ПЛК (>512 входов/выходов) – 18%, контроллеры на базе ПК 10%, нано ПЛК (менее 15 входов/выходов) – 7%, soft-logic – 7% и встроенные – 4%.
Майк Миклот, менеджер по маркетингу Rockwell Automation, заявляет, что некоторое увеличение использования систем управления на основе ПК и систем soft-logic „не удивительно и в большей степени характерно для организаций, переходящих от традиционных „доморощенных“ систем управления к реализации и внедрению готовых решений“.
Большая часть ПЛК используется в технологических процессах или в дискретном производстве, и эту тенденцию Миклот также не находит неожиданной, поскольку „потребители начали понимать, что распределенные системы управления (DCS) являются избыточными для операций с партиями продуктов“.
Респонденты в 2004 г. Используют ПЛК в равной степени (72% случаев) для управления как процессами, так и механизмами, для управления движением – 45%, для управления партиями 36%, для диагностики – 19% и в других случаях – 6%. Эти показатели в сущности такие же, как и в 2002 г., за исключением управления движением (было 79%) и управления партиями – 31%.
Большая часть ПЛК подключается к ПК и лишь немногие используются в автономных приложениях. Возможно, это две стороны одной и той же тенденции увеличившегося распределения информации. Отвечая на вопрос: „Как большинство ПЛК взаимодействует с другими системами?“ респонденты заявили следующее: соединены сетью с персональным компьютером – 30%, работают автономно – 29%, через сеть с другими ПЛК – 24%, соединены сетью распределенной системы управления 18%.
В 2002 г. автономно работали 34%, были включены в сети с ПК – 26%, в сети с другими ПЛК – 24% и в сети распределенной системы управления 16%.
Ник Инфелис, торговый менеджер продукции ПЛК в Omron Electronics, говорит, что развитые коммуникации „облегчают изготовителю распределение данных и получение единой точки доступа к уровню предприятия“. Рассматривая текущее состояние и перспективы применения протоколов коммуникации с ПЛК, пользователи ожидают уменьшения роли последовательного интерфейса, роста Ethernet и еще большего роста беспроводных соединений. Ведущими способами связи с ПЛК являются: последовательный RS-232/RS-485 89%, Ethernet – 86%, и 4-20 мА/0-10 В постоянного тока – 81%.
Коммуникации ПЛК обеспечивают повышение качества предупредительного ремонта за счет „возможностей оценки текущего состояния и диагностики, встроенных в удаленные устройства сетей ввода/вывода, сетей безопасности и прямого доступа к удаленным сетям из одной точки для ускорения отладки“ – добавляет Инфелис.
В 2004 г. среди всех, кто сообщает об использовании Ethernet, 79% применяют его для решения задач контроля. Около двух третей (65%) используют его для объединения в сеть ПЛК; 44% – дляуправления устройствами ввода/вывода.
Среди тех, кто использует Ethernet, 83% применяют TCP/IP; EtherNet/IP 54% и Profinet – около 7%.
Среди ведущих языков программирования доминирующим остается язык релейно-контактных схем. Даже приэтих условиях, отмечает Конни Чик, бизнес-менеджер по контроллерам GE Fanuc Automation, „развитие таких программных инструментов, как функцио нальные блоковые диаграммы и последовательные функциональные схемы, увеличивает возможности выбора функциональности приложения разработчиками систем управления и сводит к минимуму время выполнения проекта“.
ПРОДУКЦИЯ ПЛК
Контроллер разнородных сетей
Контроллер RX3i системы PACSystems работает на базе высокоскоростной шины PCI и процессора Intel Pentium 300 МГц. Один или несколько эффективных источников питания могут быть сконфигурированы таким образом, что бы обеспечить достаточную мощность или избыточность в одной стойке. RX3i также характеризуется большей скоростью ввода/вывода с расширенной диагностикой, прерываниями и горячей заменой. Система поддерживает широкий диапазон модулей ввода/вывода и включает дискретные, универсальные аналоговые, аналоговые с высокой плотностью размещения, высокоскоростные счетчики и управление перемещением. Расширенные коммуникационные возможности обеспечивают модули Ethernet и Profibus.Также обеспечивается поддержка сетей DeviceNet и Genius. RX3i позволяет объединить новую технологию с аппаратурой существующих систем, обеспечивая непрерывный путь развития потребителей GE Fanuc. Программное обеспечение Proficy Machine Edition предоставляет универсальную среду проектирования для программирования, конфигурирования и диагностики всего семейства оборудования PACSystems. Proficy имеет тэговое программирование, библиотеку повторно используемого кода и режим редактирования тестов для улучшения оперативного поиска неисправностей.
www.gefanuc.com
GE Fanuc Automation
ПЛК для управления перемещением
CPU S7-317 T Integrated Technology объединяет как стандартные функции контроллера, так и технологию управления перемещением в одном ПЛК SIMATIC. За счет использования системы программирования STEP 7 концерна SIEMENS устройству требуется только одна программа для ПЛК и системы управления перемещением, что упрощает конфигурирование и программирование, уменьшая также затраты на обучение и оборудование. CPU 317 T может контролировать до 16 осей. Доступные функции управления перемещением включают позиционирование в абсолютных, относительных координатах. Другие функции включают синхронное движение с коэффициентом редукции, режим управления по путевым сигналам/уставкам, режим работы с датчиком касания.
www.siemens.ru/ad/as
SIEMENS
Контроллеры интегрируют ControlNet
Контроллеры CompactLogix 1769 L35CR и 1769-L32C фирмы Allen Bradley предлагают функцию подключения к сети ControlNet, которая устраняет необходимость применения коммуникации модулей, упрощает программирование и уменьшает затраты на инсталляцию и конфигурацию. CompactLogix1769-L32C будет доступен в начале 2005 г. Применяя один программный пакет, пользователи могут конфигурировать сеть ControlNet и переходить из ControlNet в DeviceNet, чтобы настраивать устройства в DeviceNet из одной точки доступа. При включении питания контроллера устройство ControlNet конфигурируется автоматически, исключая выполняемые ранее шаги по установке, конфигурированию и добавлению модуля просмотра к программному дереву.
CompactLogix 1769-L35CR предлагает резервные средства для обеспечения большей надежности в сложных приложениях. Он поддерживает до 30 локальных модулей ввода/вывода и предоставляет 1,5 MB программируемой памяти для обеспечения высокой производительности в малом объеме. CompactLogix 1769-L32C сконструирован для простых компактных приложений, поддерживая до 16 локальных модулей ввода/вывода и предоставляя 750 KB программируемой памяти.
www.rockwellautomation.com
Rockwell Automation
ПЛК DirectLOGIC для систем автоматизации
По результатам опроса читателей журнала Control контроллеры DirectLOGIC, на Североамериканском континенте не уступают по популярности контроллерам фирмы Siemens. В России эти контроллеры, а также графические и текстовые операторские панели, модули удаленного ввода/вывода Terminator I/O, блоки питания, модемы и другое оборудование поставляет компания „ПЛКСистемы“. Контроллеры DirectLOGIC хорошо зарекомендовали себя во многих системах внедренных в нефтегазовой, горнодобывающей, металлургической, машиностроительной отраслях промышленности, в энергетике, жилищно-коммунальном хозяйстве, в системах для „интеллектуальных“ зданий.
Поставляются 4 серии ПЛК с различной производительностью для оптимального выбора и минимизации расходов. Наиболее популярна серия DL205. Она включает в себя 6 типов процессоров, в том числе два с установленной ОС Windows CE. Модель D2-260 имеет 30.4КСлов памяти, 16 ПИД-регуляторов с самонастройкой и поддерживает до 8192 каналов ввода/вывода. В нем располагаются два встроенных порта RS232/485 для работы с человеко-машиным интерфейсом, последовательными сетями, удаленным вводом/выводом и устройствами, поддерживающими протокол обмена ASCII – весами, считывателями штрих-кодов. Имеются также свыше 35 различных модулей входа/выхода (аналоговый 12/16-битный, для терморезисторов и термопар), специальные модули (высокоскоростного ввода/вывода, Basic-сопроцессора) и коммуникационные модули (Ethernet, MODBUS RTU, Profibus).
Самые маленькие моноблочные контроллеры серии DL05 имеют 14 дискретных I/O, 2 порта RS232/485, 4 ПИД-регулятора.
Удобное программное обеспечение под Windows позволяет значительно сократить время программирования и отладки, настройки ПИД-регулятора.
Тел/факс (095) 105-77-98
995-49-00
www.plcsystems.ru
ПЛКСистемы
Контроллеры SCADAPack для систем телемеханики
Надежные контроллеры SCADAPack с 3-летней гарантией пред назначены для построения систем телемеханики и для работы в необслуживаемых условиях при температуре от –40 до + 70°С.
Четыре серии контроллеров
позволяют подобрать оптимальный вариант для решения конкретной задачи. Наиболее мощная модель SCADAPack 32 имеет процессор 120МГц, 8Мб SDRAM, 4 Мб Flash и 1 Мб CMOS RAM, 4 порта RS-232/RS-485, встроенный Ethernet порт и до 1132 каналов ввода вывода.
Контроллеры устойчивы к воздействию электромагнитных и импульсных помех, имеют малое энергопотребление и тепловыделение. При отключении электропитания данные сохраняются в течение 2-х лет.
Коммутационные средства контроллеров SCADAPack служат для организации надежных каналов передачи данных через интерфейсы RS232/RS485, Ethernet, выделенные и коммутируемые телефонные линии, радио- и сотовую связь. Имеется функция ретранслятора.
Программирование на языке релейной логики, С/С++, IEC 61131-3 (ISaGRAF). Многозадачность. Дистанционная диагностика и программирование.
Протоколы – Modus ASCII/RTU, TCP/UDP, DNP3, DF1, HART.
В России контроллеры SCADAPack успешно эксплуатируются нанефтепромыслах „ЛУКОЙЛа“, „Сибнефти“, ТНК-ВР, „ЮКОСа“, в энергетике, в теплосетях и водоснабжении.
www.plcsystems.ru
ПЛКСистемы
Программное обеспечение для програмирования ПЛК
Версия 2 Unity Pro от Telemecanique призвана обеспечить универсальное программирование ПЛК в соответствии со стандартом МЭК 61131, отладку и выполнение программы для ПЛК Modicon на уровне микропрограмм, а также добавляет ряд эргономических улучшений с целью уменьшения сроков проектирования. Сейчас доступны лицензии, как на одно рабочее место, так и на несколько мест, которые позволяют работать совместно группе от 3 до 100 пользователей при конструировании систем управления, их запуске и эксплуатации. Программа облегчает междисциплинарную интеграцию, предоставляя возможность отдельным разработчикам и их группам обмениваться идеями и информацией визуально. Другие черты Unity Pro версии 2 включают уменьшенные размеры файлов для более быстрой обработки, новые возможности горячего резервирования, встроенныйинтерактивный экран оператора для упрощения эксплуатации, полнофункциональный имитатор для выполнения лабораторных испытаний приложений и определяемые пользователем функциональные блоки для упрощения программирования. Определяемые пользователем протоколы Ethernet разрешают прямое подключение к оборудованию радио частотной идентификации, считывателям штрих-кода, а также другим ПЛК, устраняя необходимость в добавлении шлюзов.
www.schneider-electric.ru
www.modicon.ru
Schneider Electric
Сдвоенный ПЛК обеспечивает резервируемость и скорость
Сдвоенный программный контроллер CS1D создается на высокоскоростном и надежном контроллере CS1 путем добавления избыточности. При появлении проблем в основном процессоре CS1D автоматически переключает управление на второй блок в течение одного программного опроса без остановки работы. Отключенный процессор может быть заменен во время продолжения работы. Резервный источник питания и коммуникационные модули могут быть удалены и заменены без прерывания операций управления. Непрерывная работа расширяется за счет „горячей замены“ входов/выходов и специальных модулей. Контроллер конфигурируется только как резервный процессор или как полная сдвоенная система с резервным блоком питания и модулями коммуникации.
www.omron.ru
Omron Electronics
Вконтакте
Google+
контроллеры — это что такое?
У истоков промышленной автоматики стояли релейно-контактные схемы управления производственными функциями. Такие устройства имели специфический неприятный звук работы. Логика работы была фиксированной, и при малейшем отклонении от заданного алгоритма действий приходилось в корне менять всю цепочку монтажа.
С развитием технологий в данной области процессоры сильно эволюционировали. Это послужило катализатором к созданию систем управления производственными процессами на основе промышленных ПЛК-контроллеров.
Первые такие программируемые контроллеры были использованы в Соединенных Штатах. Они послужили для организации автоматики на конвейерном сборочном производстве в изготовлении автомобилей. Применившей эту технологию была фирма «Модикон» в 1968 году.
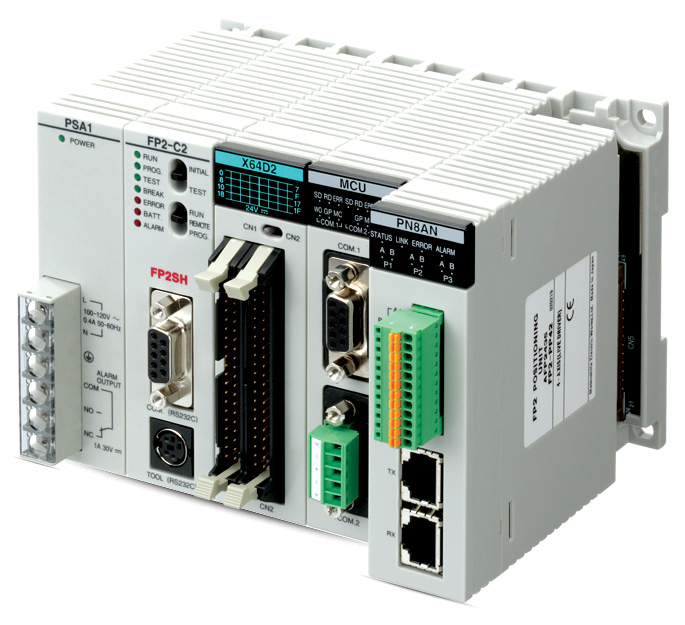
Описание устройства
Программируемые логические контроллеры ПЛК – это автомат, управляемый программой, с множеством входов, которые подключены к объекту с помощью датчиков управления. Выходы подключены к устройствам исполнения команд. В конструкции контроллера важным составляющим элементом является микропроцессор. Его задача — собирать информацию, преобразовывать и хранить ее для возможности дальнейшей выработки команд управления. Одним из главных достоинств программируемого контроллера становится то, что он функционирует в режиме реального времени!
Ранее релейные контроллеры имели громоздкие габаритные размеры, выполняли простейшие операции переключения. Их логическая структура была монолитной, не изменяемой. Пришедшие на смену ПЛК-контроллеры отличались компактными размерами, алгоритм управления поднялся на новый, сложный уровень исполнения. Появился процесс свободного программирования.
Возможности логических контроллеров
При разработке ПЛК создателями преследовалась цель возможности управления логическими функциями в последовательной цепи. В настоящее время программируемые контроллеры могут не только производить логические операции, но и обрабатывать сигналы в цифровом представлении, управлять различными приводами, заниматься регулировкой и приобрели электронные навыки операторского управления.
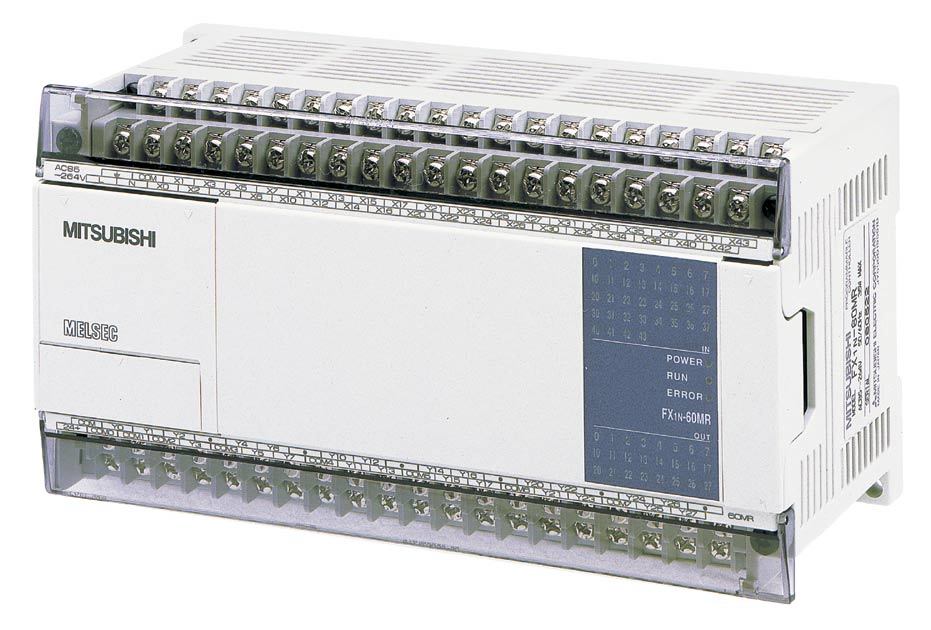
На данный момент приборы получили широкое применение в различных направлениях. Например, контроллер ПЛК 100 разработан для создания систем автоматизированного управления производственным оборудованием в промышленности, сельском и жилищно-коммунальном хозяйстве. Также ПЛК применяются в энергетической сфере, в области связи, химической промышленности. Устройства нашли свою нишу использования в процессе добычи и транспортировки нефти и газа, в системах обеспечения безопасности, принимают участие в автоматизации складских помещений, в производстве продуктов питания, в транспортном хозяйстве, строительстве и во многих других отраслях жизнедеятельности человека.
Отличительные особенности
ПЛК-контроллерам присущи некоторые характерные отличия для электронных приборов, которые используются в промышленности.
Во-первых, от параллельно функционирующих микроконтроллеров программируемые логические приборы отличаются использованием в сфере автоматизированных процессов на предприятиях с промышленным уклоном.
Во-вторых, программируемые контроллеры направлены на взаимодействие с устройствами посредством развитого ввода сигналов датчика и выводом их же на исполнительные механизмы, в отличие от компьютеров, которые приспособлены на принятие решений за счет управления оператором.
В-третьих, от встраиваемых систем ПЛК-контроллеры отличает самодостаточность в плане их изготовления как самостоятельного продукта, отдельного от управляемого при его помощи оборудования.
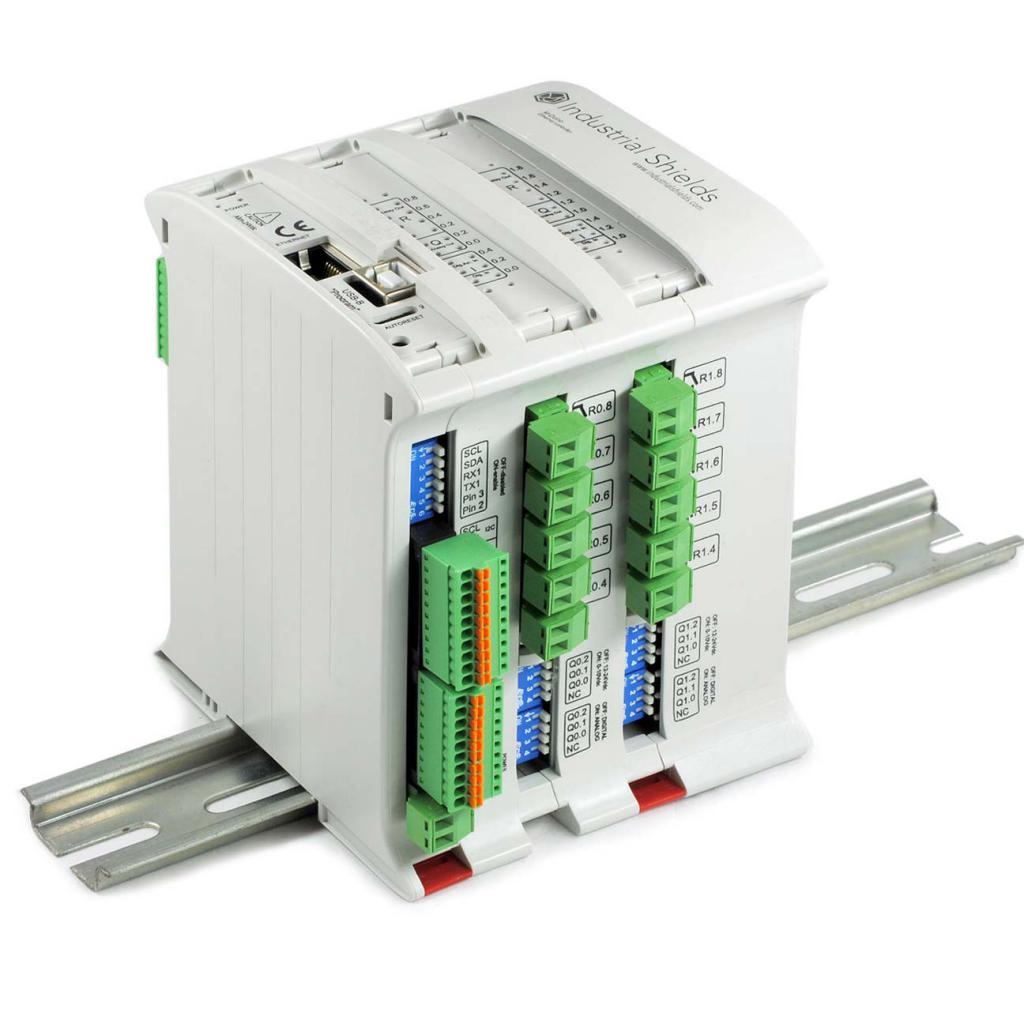
Преимущества ПЛК
Также программируемый контроллер ПЛК характеризуется простотой в контакте с пользователем. Это выражается в действиях по программированию самого ПЛК по принципиальной схеме, по логическим уравнениям и при помощи базового алгоритмического языка.
Прибор адаптирован для функционирования в негативных условиях производства, используя в своем активе оптическую электронную развязку входов/выходов от внешних электроцепей. Это стало возможно благодаря наличию приспособленности контроллера к более широкому спектру условий эксплуатации.
В достоинства программируемых контроллеров входят мобильность программного обеспечения за счет унифицирования языков программирования, широкие функциональные возможности, оперативная смена модульных узлов, рабочий режим в реальном времени, возможность ремонта и системной интеграции.
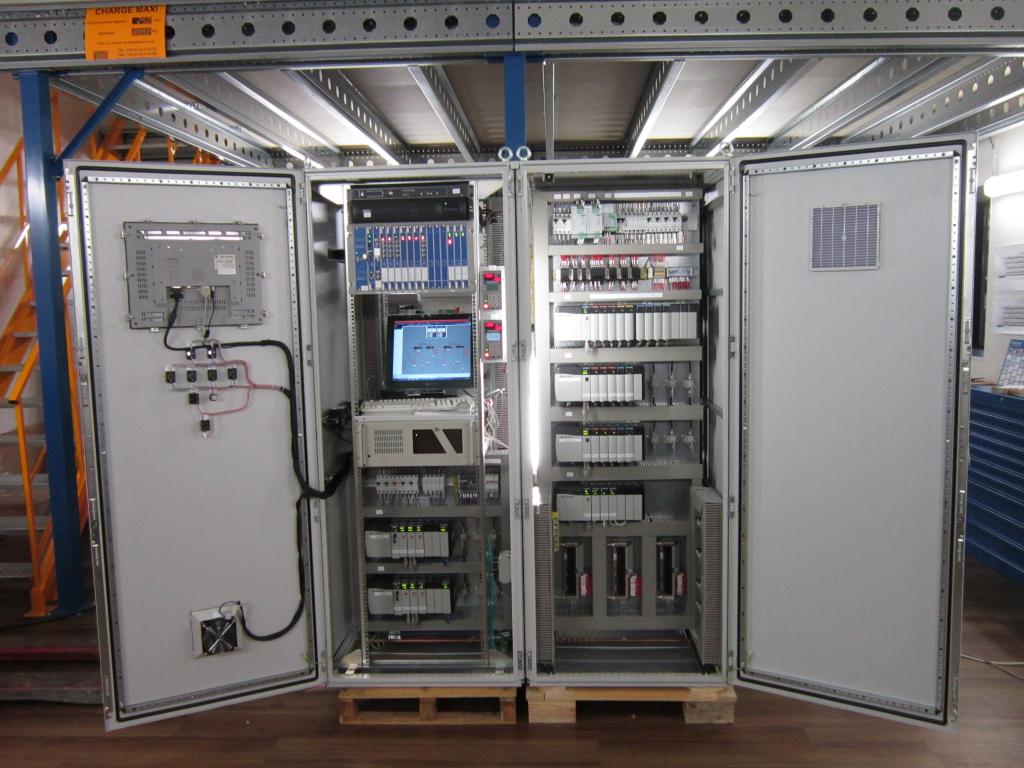
Выбор устройства
При выборе ПЛК руководствуются такими основными критериями, как соответствие технических возможностей поставленной задаче и, конечно же, стоимость прибора.
Выпуском данных контроллеров занимается огромное количество предприятий-изготовителей. В перечень входят как зарубежные фирмы, так и отечественные. Например, российская фирма «Овен» предлагает контроллер ПЛК 150, соответствующий всем необходимым техническим условиям. Также в этом списке отмечены фирмы-изготовители «Элемер», «Эмикон», «Текон», «Фаствел», НИЛ АП и многие другие.
Именитыми зарубежными производителями являются компании Siemens, Mitsubishi, ABB, Omron, Schneider Electric и др.
С течением времени наблюдается тенденция в эволюции программируемых логических контроллеров. Они теряют в габаритных размерах, расширяется набор функциональных возможностей, прибавляется количество совместимых сетей и интерфейсных оболочек, входит в повсеместное использование идея «открытых систем», стандартизируется язык программирования, снижается реализуемая цена.
Стоит отметить, что сохраняются выгодные отличительные особенности программируемых контроллеров от персональных компьютеров в виде назначений и присутствия технологического кода программирования.
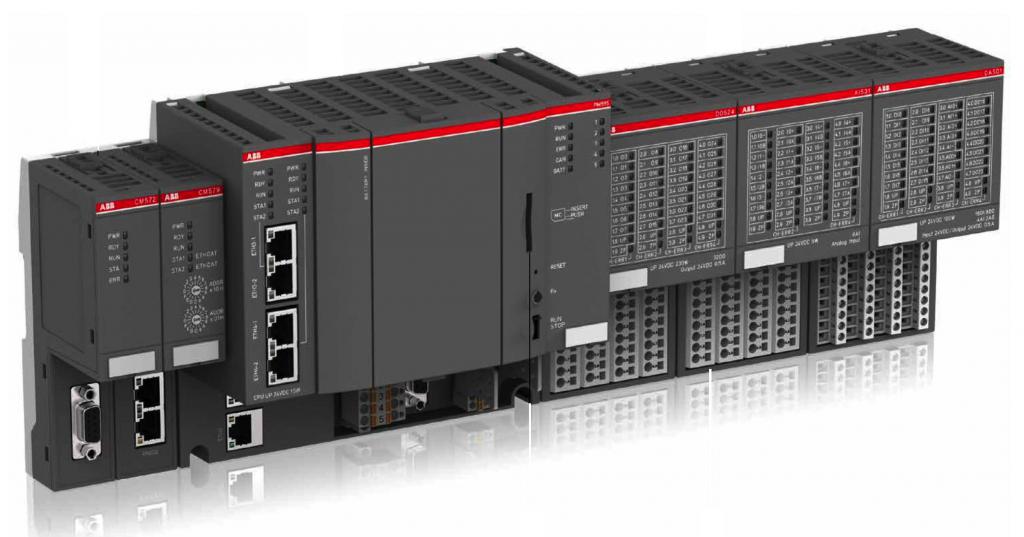
Принцип работы
Рабочее функционирование ПЛК-контроллеров имеет небольшое отличие от стандартных приборов с микропроцессором. Программная оболочка данных логических контроллеров включает в себя две части. Наподобие компьютерной операционной системы программное обеспечение контроллера управляет рабочими узлами, связывает составные части и занимается внутренней диагностикой. Системная оболочка ПЛК находится в постоянном запоминающем устройстве центрального микрочипа и всегда готова к работе.
Программируемый контроллер функционирует в циклическом режиме способом периодического сбора входной информации. Данный цикл имеет 4 этапа:
- Опрос входов.
- Исполнение задач, поставленных пользователем.
- Установка выходных параметров.
- Другие процессы вспомогательных операций.
Классификация контроллеров
Относительно магистралей ввода/вывода ПЛК-контроллеры классифицируются на:
- наноконтроллеры;
- микроконтроллеры;
- средние контроллеры;
- большие контроллеры.
Относительно нахождения модулей ввода/вывода различают:
- моноблочные;
- модульные;
- распределенные.
В зависимости от метода монтажа и конструкции ПЛК бывают:
- панельные;
- для крепления внутрь на специальную рейку;
- для монтажа на стену;
- для крепления в стойке;
- не имеющие корпуса (одна плата).
Критерии выбора ПЛК для промышленной автоматизации
Большинство промышленных контроллеров, таких как программируемые логические контроллеры (ПЛК) и программируемые контроллеры автоматизации (ПКА), могут выполнять все основные функции, в том числе управление в реальном времени дискретными и аналоговыми соединениями ввода/вывода (I/O). Фактически данный тип функциональности присущ большинству контроллеров, при этом основной проблемой является их способность обрабатывать необходимое количество точек ввода/вывода, что, как правило, несложно установить.
Однако при определении достаточности тех или иных промышленных контроллеров к применению для решения определенного круга задач в конкретных приложениях проблемы часто возникают при определении других их возможностей, таких как обработка данных, связь и высокоскоростное управление. Помочь в определении функций контроллеров, необходимых для выбора под конкретную задачу, поможет знание того, как эти функции улучшают конечное решение системы автоматизации.
Обработка данных
Современные контроллеры с расширенным программированием на основе имен тегов (признаков) имеют различные возможности в части обработки данных, включая встроенную регистрацию. Некоторые усовершенствованные контроллеры также могут взаимодействовать со стандартными базами данных в системах уровня предприятия, например в системе планирования ресурсов предприятия (enterprise resource planning, ERP). Запись данных непосредственно в запоминающее устройство в виде USB флэш-накопителя, подключенного к контроллеру, тоже важная функция, часто необходимая для целого ряда приложений. Контроллеры с функциями регистрации данных часто поддерживают отформатированный USB-накопитель или карту MicroSD, которые имеют до 32 Гбайт дискового пространства.
Регистрация данных обычно основана на откликах на те или иные события или может быть запланирована. Отклик на события инициируется изменениями состояния, такими как переход границы булевого тега. В отличие от этого подхода запланированная регистрация данных настроена так, чтобы осуществлять действия, например регистрацию состояния или считывание счетчика, через заданные регулярные интервалы — каждую минуту, час, день или месяц.
Хотя количество тегов, которые могут быть зарегистрированы, часто ограниченно, но для каждого запланированного или инициированного события должно быть сохранено не менее 50 значений тегов. Системные ошибки также должны храниться с указанием времени и даты возникновения такой ошибки или события. Имя файла журнала должно быть настраиваемым или автоматически генерироваться в зависимости от предпочтений пользователя.
Помимо локальной регистрации данных, некоторые контроллеры могут взаимодействовать с корпоративными системами информационных технологий — ИT-системами. Одним из примеров является OPC-сервер (Open Platform Communications, ранее OLE for Process Control — семейство программных технологий, предоставляющих единый интерфейс для управления объектами автоматизации и технологическими процессами), подключенный к контроллеру. Это позволяет серверу собирать данные в режиме реального времени от контроллеров на производственной площадке или на уровне цеха и извлекать, добавлять, удалять и обновлять записи данных в стандартной базе. Это достигается поддержкой подключений к базе данных, совместимой с Microsoft Access, сервером на языке структурированных запросов (structured query language, SQL — декларативный язык программирования, применяемый для создания, модификации и управления данными в реляционной базе данных, управляемой соответствующей системой управления базами данных) или подключением к открытой базе данных (open database connectivity, ODBC — программный интерфейс доступа к базам данных, созданный компанией Microsoft в сотрудничестве с Simba Technologies на основе спецификаций Call Level Interface, который разрабатывался организациями SQL Access Group, X/Open и Microsoft).
Установить соединение между ИТ-системой предприятия и ПЛК помогают несколько доступных на рынке программных инструментов. Они позволяют собирать сведения из ПЛК и сохранять их в базе данных. Конфигурационные усилия для этих серверов часто минимальны, и пользователь может собирать только те данные, которые ему необходимы для определенного производственного или технологического процесса.
Возможности баз данных предоставляют практические решения для отслеживания движения материалов и фиксации показателей производства. Контроллер, выполняющий производственные или технологические задачи, чтобы обеспечить оптимальное время процессов, может отслеживать ход работ на уровне завода, а также расход материалов. Эта информация может быть использована для корректировки складских запасов, что позволяет обеспечить наличие материалов и их поступление по мере их необходимости, избегая накопления сверхнормативных запасов.
Эти возможности также можно использовать для отслеживания путем регистрации производственных данных при изготовлении детали или продукта, его состояния от начала до конца всего производственного цикла. Статус конечного продукта сохраняется, а встроенные в базу данных функции отметки даты/времени могут использоваться для удовлетворения требований по обеспечению заданного уровня качества или для аудита.
Коммуникационные возможности
Другая важная особенность, которую следует учитывать при выборе контроллера автоматизации, — возможность связи, или, как мы говорим, возможности коммуникации. Здесь, для того чтобы обеспечить простую интеграцию с человеко-машинными интерфейсами (ЧМИ), приводами двигателей и другими устройствами, должно быть доступно несколько портов Ethernet и портов последовательной связи (рис. 1).

Рис. 1. Эффективность производства зависит от сбора данных. Коммуникационные возможности и возможности обработки данных этого контроллера серии AutomationDirect Productivity позволяют подключаться ко многим различным устройствам.
Все рисунки предоставлены компанией AutomationDirect
Высокоскоростные порты Ethernet также используются для организации одноранговой (peer-to-peer, P2P — («равный к равному»), оверлейная компьютерная сеть, основанная на равноправии участников, каждый узел (peer) как является клиентом, так и выполняет функции сервера) или сетевой бизнес-системы. Именно здесь важна поддержка протоколов EtherNet/IP (ODVA) и Modbus TCP/IP Ethernet. Также должны быть предусмотрены и другие порты связи, в том числе для подключения USB In/USB, Mini USB, MicroSD, удаленного ввода/вывода (Remote I/O), RS-232 и RS-485.
Эти подключения обеспечивают простой доступ к программированию и подключение к высокоскоростным устройствам, например приводам, а также интеграцию ЧМИ для мониторинга системы оператором. Наряду с другими функциями связи для удаленного доступа они также обеспечивают исходящую электронную почту, соединения сканера/клиента и адаптера/сервера. Кроме того, доступны приложения для удаленного мониторинга, позволяющие подключаться к контроллерам с помощью Wi-Fi (беспроводная связь IEEE 802.11x) или через сотовую сеть. Удаленный пользователь может контролировать локальный контроллер с помощью пользовательских тегов, настроенных для удаленного доступа внутри общей базы данных тегов.
Очень важным является тот факт, на который необходимо обратить самое пристальное внимание, что современные контроллеры должны иметь встроенную защиту, при которой в конфигурации оборудования, связанной с удаленным доступом, должны быть включены удаленные функции, причем каждый тег в базе данных должен быть выбран для обеспечения удаленного доступа к нему. Помимо этого, как и для любого устройства, к которому можно получить доступ из Интернета, настоятельно рекомендуется использовать в целях безопасности брандмауэр. Несмотря на то что функция удаленного доступа для контроллера может и должна быть настроена с защитой паролем, из-за постоянно растущих угроз кибербезопасности в Интернете наилучшей практикой является безопасное и зашифрованное VPN-соединение (рис. 2).

Рис. 2. Как удаленно получить данные из контроллера. Некоторые современные контроллеры, такие как этот Productivity3000 от AutomationDirect, включают до семи встроенных коммуникационных портов, что является критически важной возможностью для подключения как к устройствам на уровне предприятия, так и к корпоративным сетям уровня предприятия
Еще одна функция защиты, связанная с доступом к удаленному контроллеру, — разделение учетных записей и IP-адресов, настроенное таким образом, чтобы пользователи могли безопасно выгружать, загружать или редактировать программу через удаленный доступ. Однако, в целях обеспечения безопасности, одна и та же учетная запись не должна разрешать как удаленный мониторинг, так и изменения программы.
Должны быть приняты все необходимые меры, чтобы контроллер мог поддерживать приложения удаленного мониторинга, обеспечивая необходимую безопасность. При этом только авторизованные пользователи с помощью Wi-Fi или сотовой связи должны иметь возможность подключить свой смартфон или планшет к контроллеру для удаленного мониторинга в режиме реального времени.
Кроме того, в контроллере должны быть предусмотрены дополнительные функции веб-сервера, которые позволяют удаленно устранять проблемы с помощью системных тегов, журналов ошибок и истории событий, а также просматривать файлы данных, записанные на флэш-накопитель контроллера или карту MicroSD.
Управление высокоскоростным движением
К особенностям выбора современного контроллера следует отнести и возможность управления движением и другими высокоскоростными приложениями. Для выполнения этих функций требуется высокоскоростной ввод/вывод, а также достаточно мощный процессор и возможность определения приоритетов при выполнении таких высокоскоростных задач.
Хотя некоторые контроллеры предлагают координацию между несколькими осями движения, но даже скоординированное движение между двумя осями обычно требует специального оборудования и специфических функций, встроенных непосредственно в сам контроллер. Для запуска необходим модуль высокоскоростного вывода (high-speed output, HSO) и модуль высокоскоростного ввода (high-speed input, HSI). Модуль HSO генерирует команды импульса и направления для управления сервоприводами, работающими от двух или более серводвигателей. Эти команды импульса и направления могут контролировать различные приложения, например разрезание по длине, сшивание или скоординированные перемещения по оси Х-У. Также для команд перемещения, генерируемых модулем HSO, может быть доступна и функция их регистрации.
Функция регистрации, используя встроенный модуль ввода/вывода, может запускаться как ответ от нескольких внутренних и внешних событий, связанных с позицией. Вход от датчика через модуль HSI может использоваться для старта или остановки движения, захвата позиции по обратной связи от датчика, для включения/выключения или подачи импульса на выход.
Дополнительные возможности высокоскоростного управления предлагают программируемый барабанный переключатель (programmable drum switch, PDS) и программируемый концевой выключатель (programmable limit switch, PLS). PDS обеспечивает мониторинг на частотах до 1 МГц нескольких устройств, таких как кодеры. Эти входные сигналы применяются для координации и управления выходами со скоростью подачи до десятков тысяч раз в секунду. Такой тип конфигурации оборудования обеспечивает точное управление движением независимо от времени сканирования контроллера, которое может варьироваться в зависимости от степени загрузки его процессора.
Инструкция PLS работает как механический вращающийся кулачок с концевыми выключателями, но таким виртуальным устройством можно управлять в режиме реального времени. Поскольку эта функция часто действует в сочетании с HSI, она совершенно не зависит от загрузки процессора и времени сканирования, что приводит к точной и повторяемой синхронизации для высокоскоростных приложений.
Заключение
При выборе ПЛК, ПКА и других промышленных контроллеров пользователи должны думать не только о базовых требованиях к управлению и числу доступных портов ввода/вывода. Во многих приложениях контроллеры (рис. 3) также нуждаются в широких возможностях в части регистрации данных и связи, в управлении высокоскоростными приложениями, такими как скоординированное движение.

Рис. 3. Возможности программируемых логических контроллеров расширяются, например, с этим Productivity2000 от компании AutomationDirect. В процессе выбора ПЛК для улучшения функционирования конечного приложения следует учитывать такие его особенности, как обработка данных, связь и высокоскоростное управление
Вконтакте
Google+
Программируемый логический контроллер — Вики
Модульный программируемый логический контроллерПрограмми́руемый логи́ческий контро́ллер (сокр. ПЛК; англ. programmable logic controller, сокр. PLC; более точный перевод на русский — контроллер с программируемой логикой), программируемый контроллер — специальная разновидность электронной вычислительной машины. Чаще всего ПЛК используют для автоматизации технологических процессов. В качестве основного режима работы ПЛК выступает его длительное автономное использование, зачастую в неблагоприятных условиях окружающей среды, без серьёзного обслуживания и практически без вмешательства человека.
Иногда на ПЛК строятся системы числового программного управления станков.
ПЛК — устройства, предназначенные для работы в системах реального времени.
ПЛК имеют ряд особенностей, отличающих их от прочих электронных приборов, применяемых в промышленности:
- в отличие от микроконтроллера (однокристального компьютера) — микросхемы, предназначенной для управления электронными устройствами — ПЛК являются самостоятельным устройством, а не отдельной микросхемой.
- в отличие от компьютеров, ориентированных на принятие решений и управление оператором, ПЛК ориентированы на работу с машинами через развитый ввод сигналов датчиков и вывод сигналов на исполнительные механизмы;
- в отличие от встраиваемых систем ПЛК изготавливаются как самостоятельные изделия, отдельные от управляемого при его помощи оборудования.
В системах управления технологическими объектами логические команды, как правило, преобладают над арифметическими операциями над числами с плавающей точкой, что позволяет при сравнительной простоте микроконтроллера (шины шириной 8 или 16 разрядов), получить мощные системы, действующие в режиме реального времени. В современных ПЛК числовые операции в языках их программирования реализуются наравне с логическими. Все языки программирования ПЛК имеют лёгкий доступ к манипулированию битами в машинных словах, в отличие от большинства высокоуровневых языков программирования современных компьютеров.
История
Первые логические контроллеры появились в виде шкафов с набором соединённых между собой реле и контактов. Эта схема не могла быть изменена после этапа проектирования и поэтому получила название — жёсткая логика. Первым в мире, программируемым логическим контроллером, в 1968 году стал Modicon 084 (1968) (от англ. modular digital controller), имевший 4 кБ памяти.
Термин PLC ввел Одо Жозеф Стругер (англ.)русск. (Allen-Bradley) в 1971 году. Он также сыграл ключевую роль в унификации языков программирования ПЛК и принятии стандарта IEC61131-3. Вместе с Ричардом Морли (англ.)русск. (Modicon) их называют ‘отцами ПЛК’. Параллельно с термином ПЛК в 1970-е годы широко использовался термин микропроцессорный командоаппарат.
В первых ПЛК, пришедших на замену релейным логическим контроллерам, логика работы программировалась схемой соединений LD. Устройство имело тот же принцип работы, но реле и контакты (кроме входных и выходных) были виртуальными, то есть существовали в виде программы, выполняемой микроконтроллером ПЛК. Современные ПЛК являются свободно программируемыми.
Виды ПЛК
Контроллер на базе персонального компьютера
Именно это направление существенно развивается в последнее время, и это обусловлено определенными причинами. Таковыми причинами являются:
- Повышение надежности ПК.
- Наличие разных модификаций ПК в обы