Навесной монтаж — Википедия
Материал из Википедии — свободной энциклопедии
Текущая версия страницы пока не проверялась опытными участниками и может значительно отличаться от версии, проверенной 19 февраля 2016; проверки требуют 11 правок. Текущая версия страницы пока не проверялась опытными участниками и может значительно отличаться от версии, проверенной 19 февраля 2016; проверки требуют 11 правок.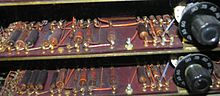
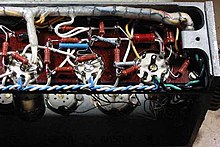
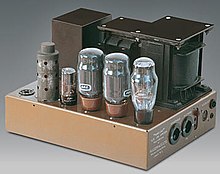
Недостаток навесного монтажа — плохо поддаётся автоматизации и обычно выполняется монтажниками вручную. В настоящее время в массовом производстве применяется редко и обычно только при монтаже крупногабаритных деталей.
Промышленные и любительские ламповые конструкции навесного монтажа используют металлические шасси (соединённые с общим проводом схемы или непосредственно выполняющие роль общего провода. Ламповые и релейные панели, трансформаторы, дроссели и прочие крупногабаритные детали крепятся непосредственно к шасси, мелкие резисторы и конденсаторы — распаиваются непосредственно к выводам панелей и крупных деталей, либо к контактным лепесткам (контактным колодкам), изолированным от шасси. При заводском изготовлении монтажники руководствуются технологическими картами, чтобы не пропустить элемент или перемычку. Надёжность промышленных изделий, выполненных навесным монтажом, в целом ниже, чем у аналогов на печатных платах. Ремонтопригодность — выше, в том числе за счёт меньшей плотности компонентов и простоты доступа к ним.
В массовой электронике навесной монтаж применялся до 50—60-х годов, впоследствии уступив место печатным платам; за навесным монтажом осталась ниша — коммутация трансформаторов и аналогичных крупногабаритных изделий.
Навесной монтаж остаётся наиболее уместным способом монтажа ламповой техники — как из-за конструктива ламповых панелей и крупногабаритных трансформаторов, так и из-за лучшего температурного режима отдельных компонентов, эффективной механической развязки ламп, возможности оптимального подбора сечения соединительных проводников и сокращения общего числа паяных соединений в цепях сигнала. Для лучшей механической развязки ламп соединительные провода (а также вывод резисторов и конденсаторов, распаиваемые непосредственно к ламповым панелям) формуются с S-образными изгибами, избегая прямых, жёстких перемычек.
В любительских конструкциях монтаж ведётся на изолированных (диэлектрических) шасси. К шасси крепятся металлические стойки либо пистоны, к стойкам — компоненты схемы, соединяемые непосредственно или перемычками из проводов. Мелкие элементы (например, резисторы) могут припаиваться прямо к выводам крупногабаритных компонентов. Микросхемы при навесном монтаже прикрепляют к плате вверх выводами. Такой стиль монтажа на жаргоне радиолюбителей называется «мёртвый жук»
В любительской полупроводниковой практике его применяют и сейчас для создания единичных простых конструкций, когда разрабатывать трассировку печатной платы и изготавливать её невыгодно по соображениям затрат времени. Также «мёртвым жуком» радиолюбители делают высокочастотные схемы, в которых проводники должны быть как можно более короткими. Если в схеме есть крупные детали (потенциометры, тумблеры, большие конденсаторы и т.д.), часть элементов может закрепляться навесным способом на их выводах, экономя пространство на печатной плате. В разводке печатных плат навес запрещён, однако на макетной плате, если на подходящей дорожке нет места, проще и надёжнее подпаяться к какому-то выводу, чем проводить перемычку на другую дорожку. Стараются паять на перемычку: её невозможно сломать или перегреть.
Монтажные провода. Марки. Применение
Изготавливаются из чистой электротехнической меди, применяются при объёмном монтаже для внутриблочных и межблочных соединений. Провода могут быть одножильными и многожильными. Большинство монтажных проводов для обеспечения быстрой и надёжной пайки и для зашиты от окисления выпускают с лужёными токоведущими жилами. Лужение производят припоями ПОС-40. ПОС- 61. для высокочастотных цепей радиоэлектронной аппаратуры лужение может быть выполнено серебром.
Если провода используют при температуре 250 градусов и более, то для защиты от окисления их покрывают никелем.
Сечение токоведущей жилы выбирают в зависимости от величины проходящего по ним тока. Сечение соответствует определенному ряду в соответствии со стандартом.
Изоляцию провода выбирают в зависимости от величины рабочего напряжения и условий эксплуатации. В условиях нормальной температуры и влажности используют провода с полихлорвиниловой и волокнистой (хлопчатобумажной) изоляций. В условиях повышенной температуры и влажности применяются провода с изоляцией из фторопласта, стекловолокна, резины. Для защиты от внешних электромагнитных полей используются экранированные провода. Экраны изготавливают из тонкой лужёной медной проволоки.
Маркировка проводов:
ПMB — провод монтажный в полихлорвиниловой изоляции(одножильный)
МГВ — провод монтажный гибкий в полихлорвиниловой изоляции многожильный)
МГШВ — провод многожильный монтажный в шёлковой виниловой изоляции
МГВЭ — провод монтажный гибкий в полихлорвиниловой изоляции (многожильный) экранированный
МГШВЭ — провод многожильный монтажный в шёлковой виниловой изоляции экранированный
МГТФ — провод монтажный гибкий термостойкий с изоляцией из фторопласта
МГТФЭ — провод монтажный гибкий термостойкий с изоляцией из фторопласта экранированный
МГСТ — провод многожильный термостойкий с изоляцией из стекловолокна
В конструкторской документации обязательно указать ГОСТ или технические условия, в соответствии с которыми изготавливают провод, марку провода, сечение токоведущей жилы, при необходимости – цвет.
Объемный монтаж.
Обеспечивает соединение различных электро и радиоэлементов, узлов, модулей РЭА в единую конструкцию при помощи проводов, кабелей, жгутов, разъемов и т.д. Микросхемы при объемном монтаже не применяются.
5.1.1Объемный монтаж выполняется в следующей последовательности:
1. Мерная резка провода в соответствии с технической документацией.
2. Удаление изоляции с жил монтажных проводов.
Изоляция монтажных проводов снимается методом электрообжига (электронож или паяльник). Применение кусачек и другого режущего инструмента не допускается во избежание обрыва отдельных проволок. Потемнение и оплавление изоляции при обжиге допускается не более чем на 1мм. Изоляцию снимают на расстоянии 10-15мм.
3. Заделка концов волокнистой изоляции провода или экранирующей оплетки при помощи нитяного бандажа, клея, изоляционной трубки.
4. Скрутка и лужение токоведущей жилы.
Жилы многожильных проводов скручивают под углом 15- 30 градусов к оси провода. После скрутки провод залуживают, отступая от изоляции 1мм. Лужение должно быть «скелетным».
5. Закрепление монтажных проводов.
Способ крепления провода зависит от типа контакта, к которому необходимо припаять провод:
1. Штырьковые контакты
2. Трубчатые контакты.Пайка производится без механического крепления. Провод заводят в контакт и запаивают так, чтобы расстояние от пайки до изоляции провода было 0.5-2мм
3. Лепестковые контакты. Маломощные контакты (легко гнутся) паяют без механического крепления. Провод заводят в отверстие, плотно зажимают к лепестку и запаивают по всей поверхности соприкосновения.
Мощные контакты. К ним провода припаивают с предварительным механическим креплением. На один лепесток крепят не более трёх проводов. Так же необходимо соблюдать основное требование при пайке проводов — расстояние от пайки до изоляции провода должно быть 0.5-2мм.
5.1.2. Обработка экранированных проводов.
Монтаж приборов и блоков производят экранированными проводами, если они подвержены воздействию электромагнитных помех или создают их сами.
Экранирующие оплётки должны быть заземлены в местах, указанных на чертеже или в монтажной схеме. Оплётка проводов длиной более 100мм должна быть заземлена с обеих сторон. Заземляющий вывод может быть выполнен самой оплёткой или гибким проводом соответствующего сечения, который соединяется с заземляющим лепестком или контактом. Экранирующая оплётка не должна касаться корпуса прибора. При необходимости её следует поместить в изоляционную трубку.
Заделка концов экранирующей оплётки и её заземление должны исключаться повреждения основной изоляции. Не допускаются надрезы и проколы основной изоляции, а так же обрыв проволок экрана в месте выхода из него провода. Если не требуется заземление, то оплётка убирается так, чтобы расстояние от торца экрана до токоведущей жилы было в пределах 10-25мм. Для закрепления экранирующей оплётки можно использовать изоляционную трубку, подобранную по внешнему диаметру провода, которую при необходимости закрепляют клеем. Для закрепления используют нитяной бандаж 5-10мм. Бандаж может быть так же выполнен медным лужёным проводом с последующей пайкой. В этом случае под экраном помещают теплоизоляционный диэлектрический материал (фторопластовая трубка или лакоткань). При необходимости заземления под проволочный бандаж помешают обработанный монтажный провод с изоляцией и пропаивают.
5.1.3 Вязка жгутов.
Два и более параллельно идущих провода длиной более 50мм должны быть связаны в жгут. Раскладку и вязку жгутов в целях идентичности изготовления и ускорения работы в условиях серийного производства осуществляется на шаблонах.
Шаблоны изготавливаются по монтажной схеме или по чертежам на жгут. Шаблон изготавливается на диэлектрическом основании, на котором наносят трассировку (рисунок, чертёж) жгута, в соответствии со схемой. Для выпуска проводов из жгута предусматривают отверстие в соответствии с чертежом, в местах перегиба жгута устанавливают шпильки. На разъёмах указывается маркировка разъемов и номера контактов, выход провода из жгута должен быть строго против места пайки. Провода на шаблоне раскладывают в соответствии с таблицей проводов, где указываются, откуда и куда идёт провод, сечение и цвет провода.
Провода в жгуте укладывают ровно без выступов и перекрещивания. Длинные провода укладывают в верхней части жгута с лицевой стороны, чтобы все ответвления выходили из под них. Провода малых сечений и экранированные провода укладывают внутри жгута. В жгуте предусматривают запасные провода, из расчета 10% от общего количества. Запасные провода укладывают одного цвета, их концы изолируют и закрепляют на видном месте.
Вязку жгутов производят хлопчатобумажными или льняными нитками, которые пропитывают влагоотталкивающим материалом. Также для вязки жгута используют тонкие изоляционные плёнки. В зависимости от количества проводов в жгуте и диаметра жгута, вязку выполняют в одну или более ниток с натяжением.
Шаг вязки (расстояние между узелками) примерно равно диаметру жгута, но не более 25мм. В местах разветвления жгута должны быть выполнены бандажи 5-10мм. В местах изгиба жгута шаг вязки должен быть уменьшен. На провода в жгуте надевают изоляционные трубки или бирки с указанием номеров контактов.
Для защиты жгутов от тепловых и механических воздействий применяют дополнительную изоляцию в соответствии с документацией на изготовление жгута.
От механических повреждений жгут обматывают киперной лентой, полихлорвиниловой или другой изоляцией. При необходимости крепления жгута скобами или хомутами под них ставят дополнительную эластичную изоляцию, так же от механических повреждений используют металлорукав.
От влияния высоких температур жгут, в соответствии с чертежами, обматывают теплоизоляционным материалом (лакотканью, стеклотканью, фторопластовой плёнкой)
При креплении подвижных жгутов их требуется закрепить так, чтобы провода работали на скручивание, а не на изгиб.
5.1.4.Требования к объемному монтажу.
1. Все соединения проводов должны выполняться только после механического закрепления.
2. Не допускается повреждение изоляции и токоведущей жилы проводов.
3. Гибкие провода при объемном монтаже должны иметь запас по длине на одну две перепайки. Наращивание проводов скруткой или пайкой запрещается. Соединение проводов между собой или с выводами элементов выполняется с помощью монтажных контактов (лепестки, штырьки, колодки).К одному штырьку или лепестку допускается пайка не более 3х проводов. Каждый провод закрепляется самостоятельно.
4. Монтажные провода, кабели и жгуты запрещается располагать на острых кромках узлов и приборов. Необходимо использовать защиту от механических повреждений (втулки, изоляционные ленты и т.д.)
5. Если расстояние между токоведущими контактами менее 2 мм, то на выводы необходимо надеть изоляционную трубку.
6. Подвижные части приборов не должны касаться проводов.
7. Расстояние между ними должно быть не менее 5 мм.
8. разъемы распаивают так, чтобы исключить повреждение провода (снизу вверх и слева направо)
9. При монтаже и ремонте следует правильно располагать провода, чтобы связь между отдельными цепями отсутствовала или была минимальной.
10. При выполнении объемного монтажа необходимо следить, чтобы обрезки проводов и кабелей не попадали в аппаратуру.
Недостатки: высокая трудоемкость, невозможность механизации, трудность в получении идентичных образцов, паразитные емкости и наводки на длинных проводах.
Проверка качества объемного монтажа заключается:
1. в визуальном осмотре качества паяных соединений (соблюдение требований с1-10)
2. в прозвонке проводов, кабелей и жгутов (измерение сопротивления )
Печатный монтаж.
Это электрическое соединение радиоэлементов с помощью плоских печатных проводников на печатной плате, которые получают методом металлизации поверхности, или травлением фольгированного материала. По количеству токопроводящих слоев печатный монтаж может быть односторонним, двусторонним, многослойным.
Печатный монтаж выполняется в следующей последовательности:
1.Проводят входной контроль печатных плат и радиоэлементов:
1.1 проверяется соответствие номиналов элементов с принципиальной схемой и перечнем элементов;
1.2 проводится визуальный осмотр платы и элементов на отсутствие повреждений.
2. Подготовка радиоэлементов к монтажу:
рихтовка и лужение выводов
формовка по месту пайки в соответствии с документацией
3. Установка элементов в соответствии со сборочным чертежом
а) При одностороннем монтаже допускается укладывать детали на поверхность платы, выводы подгибают, если их диаметр меньше, чем 0,7 мм.
б) При двухстороннем монтаже корпус детали должен быть поднят на расстояние 0,5-1,5мм над поверхностью платы.
в) Микросхемы устанавливают в соответствии с маркировкой первого вывода, который должен совпадать с «ключом» на печатной плате. Микросхема устанавливается параллельно поверхности платы до упора выводов. Выводы микросхем при печатном монтаже не подгибают и не подрезают.
г) Диоды и электролитические конденсаторы устанавливают в соответствии с полярностью.
д) транзисторы устанавливают в соответствии с маркировкой Э-Б-К
4. Пайка.
а) В процессе пайки не допускается перегрев печатной платы и элементов. Для этого пайку производить при температуре не более 250о и не более 5 сек.
б) если отверстия металлизированные, то они должны быть заполнены припоем на всю толщину платы.
в) Полупроводники и микросхемы чувствительны к воздействию статического электричества и высоких температур.
Для защиты микросхем и полупроводниковых деталей от влияния высоких температур необходимо:
· использовать паяльник мощностью не более 40 Вт (оптимально 20-25Вт )
· температура пайки должна быть не более 250 градусов.
· пайку выводов производят через один или в шахматном порядке.
· время пайки 2-Зс.
· повторную пайку производить только после остывания предыдущей через 10-15с.
· для пайки диодов и транзисторов применяются теплоотводы, которые устанавливают на вывод детали между корпусом и пайкой. В качестве теплоотвода можно использовать пинцет без насечки или зажимы с медными насадками
Для зашиты микросхем и полупроводниковых деталей от статического электричества необходимо:
· хранить микросхемы и полупроводники в таре завода изготовителя на заземлённых стеллажах. Так же переносить можно только в заводской таре или в фольге;
· рабочее место должно быть оборудовано антистатической пластиной;
· жало паяльника должно быть заземлено;
· прежде чем приступать к работе с микросхемами, монтажник должен надеть антистатический браслет. Провод заземления присоединяют к клемме заземления на рабочем месте (плотно прикручивается или используется штекер с фиксацией)
Антистатический браслет представляет собой металлическую пластину, которая плотно прижимается к руке кожаным или текстильным ремешком.
Металлическая пластина закрыта крышкой, под которой находится резистор 1Мом (устанавливается между проводом подсоединения и металлической пластиной). Браслет соединяется с клеммами заземления многожильным изолированным проводом. 1 раз в 6 месяцев браслеты аттестуют на пригодность. Проверяется величина сопротивления, исправность провода и надежность контактов.
· рабочие места периодически протирают антистатическими пастами
Преимущества печатного монтажа: уменьшение габаритов изделия, возможность автоматизации и механизации производства, устранение паразитных емкостей и наводок, повышение надежности, получение идентичных образцов.
В процессе контроля печатного монтажа визуально проверяется соответствие всем требованиям к формовке и установке элементов на плату, а также к качеству пайки.
Не должно быть:
· отслоения дорожек в результате перегрева
· разрыва дорожки в результате механического повреждения
· «ложных» паек
· замыканий между выводами элементов или контактами на печатной плате
5.3 Поверхностный монтаж.
Является разновидностью печатного монтажа. РЭ элементы устанавливаются на поверхности печатной платы, а не в отверстия, как при печатном монтаже. Для выполнения ПМ требуется специальная элементная база, освоение новых технологических процессов, высокая точность сборочно-монтажных работ.
Преимущества поверхностного монтажа:
1. уменьшаются габариты и масса изделия,
2. повышаются технические характеристики за счет уменьшения длины выводов РЭ и проводников печатной платы.
3. сборочно-монтажные работы полностью автоматизированы.
В основном применяется смешанный монтаж, когда с одной стороны устанавливаются штыревые компоненты, а детали для поверхностного монтажа- с одной или двух сторон.
К элементам ПМ относятся:
1. Печатные платы для ПМ, которые называются коммутационными.
Платы могут быть однослойными и многослойными.
2. компоненты для поверхностного монтажа, которые делят на 3 группы:
а) пассивные элементы
· резисторы, которые имеют прямоугольную или цилиндрическую форму с металлизированными торцами.
· конденсаторы, изготовленные по многослойной технологии из керамики и металла
· диоды
б) активные элементы
· транзисторы, которые имеют 3 или 4 вывода и корпус типа SOT (Smoll outlin транзишин)
· микросхемы в корпусах типа SOIC – малогабаритный; QFP –квадратный выводы с четырех сторон; BGA -с матричным расположением выводов.
в) нестандартные – это намоточные элементы, выключатели, розетки, соединители и т.д.
Технологический процесс пайки при ПМ состоит из следующих операций:
1. нанесение припойных паст и клея
2. монтаж компонентов (установка) – основная операция ПМ, которая должна отличаться высокой точностью
3. Пайка (ИК, волной припоя и т.д.)
4. очистка и промывка от флюса
5. контрольные операции. Визуальный контроль затруднен из-за малых габаритов и высокой плотности монтажа. Поэтому широко используют методы автоматического видеоконтроля на основе распознавания образцов или контроля качества пайки на основе лазерной техники.
Исправление брака при ПМ сводится к повторному выполнению части сборочно-монтажной операции.
Контроль качества монтажа.
Для обеспечения высокого качества продукции и повышения ее надежности осуществляется контроль изделий, т.е. проверка соответствия всех параметров продукции установленным требованиям, которые указаны в ГОСТ; ОСТ, ТУ, инструкциях и т.д.
В процессе изготовления РЭА наиболее часто используют следующие виды контроля:
1. Производственный контроль – контроль производственного процесса и его итога на стадии изготовления продукции.
2. визуальный контроль. Осуществляется внешним осмотром изделия для выявления внешних дефектов, которые могут быть на поверхности изделия
3. входной контроль – контроль продукции поставщика, предназначенной для использования в производстве.
4. Текущий контроль. Осуществляется после каждой или нескольких технологических операций. Позволяет выявить брак до момента окончательной сборки изделия.
5. Выходной (приемочный) контроль – окончательный контроль готовой продукции.
6. контроль может быть полным или выборочным.
Повышение качества и надежности продукции зависит от организации, осуществления и анализа итогов контроля. Выполнение указанных работ должно осуществляться в соответствии со следующей документацией:
· технические условия на изделие;
· инструкции по контролю, которая должна содержать цель контроля, вид контроля, порядок выполнения, предупреждение о наличии опасных напряжений и токов;
· маршрутно — контрольная карта, которая составляется на каждое изделие и содержит все операции контроля;
· ведомость операций технологического контроля.
Контролер должен провести проверку соответствия параметров изделия техническим требованиям. В случае несоответствия контролер обязан забраковать изделие, т.е вернуть на доработку или снять с производства.
Техническая документация.
Схемы.
Для РЭА основной технической документацией являются различные схемы.
Схема — это документ, на котором показаны в виде условных обозначений составные
части изделия и связи между ними.
В соответствии с ГОСТ2701-84 схемы в зависимости от элементов и связей между ними подразделяются на следующие виды:
Электрические (Э)
Кинематические (К)
Оптические (Л)
Комбинированные (С)
При изготовлении изделий РЭА, электрические и смешанные (электрические+кинематические).
Электрических схем, согласно требованиям ГОСТа, существует 7 типов со следующими чертежными номерами:
Структурные (1)
Функциональные (2)
Принципиальные (3)
Монтажные (4)
Подключения (5)
Общие (6)
Расположения (7)
Допускается разработка схем прочих типов (8) и объединенных (0)-схем двух типов на одном конструкторском документе. При этом присваивается наименование схемы, тип которой имеет наименьший порядковый номер. Наименование схемы определяется ее видом и типом. (Э4- электрическая монтажная схема).
При выполнении работ по монтажу, регулировке, и ремонту изделия, а также при разработке схем применяются следующие термины:
ЭЛЕМЕНТ- это составная часть схемы, которая выполняет определенную функцию в изделии и не может быть разделена на части.
УСТРОЙСТВО- совокупность элементов, представляющая собой единую конструкцию (плата, блок).
ФУНКЦИОНАЛЬНАЯ ГРУППА-совокупность элементов, выполняющих в изделии определенные функции и не объединенных в одну конструкцию.
ФУНКЦИОНАЛЬНАЯ ЦЕПЬ- линия, канал, тракт определенного назначения.
(канал звука, изображения и т.д.)
ЛИНИЯ ВЗАИМОСВЯЗИ — отрезок линии, указывающий на наличие связи между функциональными частями изделия.
1.Схема электрическая структурная.
Определяет основные функциональные части изделия, их назначение и взаимосвязь. Функциональные части изображаются в виде прямоугольников, а связи между ними показывают линиями, стрелки на конце которых указывают направление прохождения сигналов. Внутри прямоугольников вписывают наименования, обозначения и типы узлов или частей устройства. Используются для общего ознакомления с изделием, они дают наглядное представление о принципе работы и взаимодействии всех узлов.
2.Схема электрическая функциональная.
Определяет функциональные части изделия, их взаимодействие. При этом на ней детально показывают те части, которые необходимы для понимания процессов работы, второстепенные узлы и элементы изображают в виде прямоугольников. Допускается показывать конкретные соединения (провода, кабели), приводятся позиционные обозначения и наименования элементов, поясняющие надписи и таблицы, параметры в характерных точках (значения токов, напряжений, формы и значения переменных и импульсных сигналов). Используются для более полного изучения принципа работы и при ремонте РЭА.
3. Схема электрическая принципиальная.
Определяет полный состав элементов и связей между ними. Элементы на схеме изображаются в виде условных графических обозначений в соответствии с ЕСКД, также указываются их типы и номиналы. На принципиальной схеме изображаются элементы, которыми заканчиваются входные и выходные цепи (разъемы, зажимы).
Все элементы на принципиальной схеме имеют позиционное буквенно-цифровое обозначение, которое располагают рядом с элементом с правой стороны или над ним. Все элементы, изображенные на схеме и данные о них записывают в «перечень элементов», помещенный на отдельном листе или рядом со схемой.
На схеме могут указываться параметры входных и выходных цепей (частота, сила тока, величина напряжения, сопротивления и т.д.)
Если на схеме изображены элементы, которые подбираются при регулировке, то их условное обозначение отмечают звездочкой.
Марки проводов и кабелей на схеме не указываются.
Принципиальная схема является основным документом для проверки настройки и ремонта БРЭА.
4.Схема электрическая монтажная (соединений).
Показывает соединения составных частей изделия и определяет провода, жгуты, кабели, печатные проводники, а также места их присоединения и ввода.
Устройства и элементы на схеме изображаются в истинном виде. Допускается упрощенное изображение в виде прямоугольников или внешних очертаний. Их расположение и габариты должны соответствовать действительным размерам и размещению. Около элемента ставят позиционное обозначение, присвоенное на принципиальной схеме.
Для упрощения изображения допускается объединять отдельные провода, идущие в одном направлении, в общую линию с присвоением порядкового номера в пределах изделия. К монтажной схеме обязательно прилагается таблица проводов, в которой указывают:
1. № цепи
2. откуда и куда идет провод
3. сечение и цвет провода
Схема используется при монтаже, проверке и ремонте изделия, т.к. значительно уменьшается время поиска цепей и радиоэлементов.
5.Схема электрическая подключений.
Содержит сведения о внешних подключениях изделия. Изображены входные и выходные элементы, расположение которых должно соответствовать их действительному размещению в изделии, также указывают провода и кабели внешнего монтажа. Допускается указывать марки, сечения, расцветку проводов. На схеме также указывают места подключения КИА.
6.Общая схема.
Определяет составные части комплекса и соединения их между собой на месте эксплуатации. Приводятся изображения устройств и элементов, а также проводов, жгутов, кабелей их соединяющих.
7.Схема электрическая расположения.
Определяет относительное расположение составных частей изделия. Допускается условные графические изображения элементов и упрощенные внешние очертания.
Используются при разработке других конструкторских документов, при ремонте и эксплуатации.
Сборочный чертеж.
Основным конструкторским документом для любой сборочной единицы являются
сборочный чертеж и спецификация.
В сборочном чертеже указывается расположение и взаимная связь составных частей изделия, соединяемых по данному чертежу в единую конструкцию.
Спецификация определяет полный состав сборочной единицы.
Сборочный чертеж разрабатывается по принципиальной и монтажной схеме. Содержит сведения о расположении и креплении элементов на плате или другой конструкции.
На чертеже указывают:
1. Габаритные размеры изделия (размеры для справки обозначаются *)
2. Номера позиций всех элементов, которые изображаются в истинном виде
3. Технические требования, которые располагаются на поле чертежа и содержат ссылку на технические документы, в соответствии с которыми производится установка и монтаж радиоэлементов. Так же указываются специальные требования по маркировке, покрытию, пайке.
4. В штампе указывается: наименование изделия, фамилия разработчика, децимальный номер.
5. Радиоэлементы на сборочном чертеже изображаются по наибольшим габаритным размерам. У диодов и электролитических конденсаторов указывается знак полярности (+). У транзисторов указывается эмиттер, база, коллектор. У микросхем и разъемов указывается первый вывод.
6. К сборочному чертежу прилагается спецификация, которая определяет полный состав сборочной единицы и элементов. В нее входят следующие разделы: документация, сборочный чертеж, комплексы, сборочные единицы, детали, стандартные изделия, прочие изделия, материалы.
По спецификации производится набор комплектующих элементов
7.Технологическая документация.
Технологическая документация предназначена для отражения всей последовательности технологического процесса с указанием режимов, норм времени, расхода материалов и т.д. Разрабатывается на предприятии в соответствии с требованиями ЕСТД.
Технологический процесс — часть производственного процесса непосредственно изменяющая продукт производства
При составлении технологической документации используются следующие понятия и термины:
1. Технологический процесс сборки – это процесс соединения в определенной последовательности отдельных деталей в сборочные единицы для получения готового изделия.
2. Деталь – изделие, сделанное из одного материала без применения сборочных операций.
3. Сборочная единица – ее составные части соединены при помощи разъемных или неразъемных соединений.
4. Узел – простейшая сборочная единица из двух или нескольких деталей.
5. Операция – часть технологического процесса, которая выполняется одним рабочим на одном рабочем месте.
6. переход – часть операции, выполняемая одним инструментом.
К основным технологическим документам относятся:
1.Маршрутная карта.
Применяется в мелкосерийном и серийном производстве. Определяет последовательность прохождения изготавливаемого изделия по цехам или участкам.
2 Карта технологического процесса.
Содержит описание всех операций в процессе изготовления изделия без выделения каждой в отдельный документ. Операции нумеруются двузначными числами по порядку их выполнения (10, 20, 30 и т.д.). В карте указывается оборудование, приспособления, инструмент, необходимая аппаратура и нормы времени.
3. Операционная карта.
Разрабатывается в условиях серийного производства. В ней даётся подробное описание последовательности выполнения каждой операции В ее состав входит полный перечень всех переходов с подробными данными о инструментах и приспособлениях, режимах и методиках изготовления изделия, о способах контроля, так же указываются нормы времени . Переходы каждой операции обозначаются двузначными числами (01,02, 03 и т.д.).
Технологическая инструкция
В ней приводятся физические обоснования и требования ко всем процессам, которые применяются при монтаже, настройке и испытании РЭА.
5. Ведомость материалов.
Содержит данные о подетальных нормах расхода материала.
Типовой технологический процесс сборки и монтажа РЭА состоит из следующих операций:
1. Подготовка ЭРЭ к установке на печатные платы.
2. Подготовка печатных плат к монтажу (установка изоляционных прокладок, монтажных лепестков, теплоотводящих шин ит.д.)
3. Установка ЭРЭ на ПП.
4. Пайка ЭРЭ.
5. Установка и пайка разъемов штекеров и других соединительных деталей.
6. Защит печатных узлов от влаги.
7. Установка печатной платы на каркас ячейки.
8. Объемный монтаж жгутом или перемычками для внутриблочного соединения.
9. Контроль монтажа.
10. Регулировка.
11. Выходной (окончательный) контроль.
Каждая операция состоит из отдельных переходов, определяющих последовательность ее выполнения.
Печатный монтаж. Преимущества — Студопедия.Нет
Технология монтажа РЭА.
1. Технологический процесс пайки.
Для получения качественного соединения пайку необходимо производить в следующей последовательности:
1.1 Очистить соединяемые поверхности от окислов и загрязнений
1.2 Покрыть место пайки флюсом дня зашиты поверхности от окисления
1.3 Залудить место соединения металлических поверхностей, то есть покрыть тонким слоем припоя. Луженая поверхность должна быть ровной, блестящей, без наплывов припоя и непролуженных мест. Oт качества лужения зависит качество пайки.
При необходимости закрепить провода и выводы радиодеталей в соответствии с требованиями к формовке и установке деталей и проводов при печатном и объёмном монтаже
1.4 Непосредственное выполнение пайки, как разъёмного соединения. Место пайки необходимо прогреть до температуры на 50 градусов выше, чем температура плавления припоя. Припой должен хорошо растекаться по месту пайки, количество припоя должно быть минимальным. Пайка должна быть ровной, глянцевой, без пор и посторонних вкраплений. Пайка должна быть «скелетной», то сеть под припоем должен быть виден контур соединяемых выводов или проводов. Должна быть полностью исключена возможность получения «ложной» пайки, при которой существует видимость пайки, но отсутствует электрический контакт. Такие пайки получаются в результате некачественной подготовки поверхностей.
2. Требования к пайке проводов и радиоэлементов.
Провода должны быть залужены и закреплены в соответствии с технологической документацией, но так, чтобы расстояние от изоляции до пайки было 0,5 – 2 мм. Выводы элементов должны быть залужены и отформованы. Детали устанавливают в соответствии со сборочным чертежом. Высота выводов над поверхностью платы должна быть в пределах 0,5 – 2 мм. Затем выполняют пайку.
Место пайки необходимо прогреть до температуры на 50 градусов выше, чем температура плавления припоя. Припой должен хорошо растекаться по месту пайки, количество припоя должно быть минимальным. Пайка должна быть ровной, глянцевой, без пор и посторонних вкраплений. Пайка должна быть «скелетной», то есть под припоем должен быть виден контур соединяемых выводов или проводов. Должна быть полностью исключена возможность получения «ложной» пайки, при которой существует видимость пайки, но отсутствует электрический контакт. Такие пайки получаются в результате некачественной подготовки поверхностей.
3. Подготовка паяльника к работе.
При пайке радиоэлектронной аппаратуры применяются паяльники мощностью 40 ватт и меньше. Рабочее напряжение паяльника должно быть не более 42 вольт. Изоляция соединительного шнура и вилка должны быть без повреждений. Жало паяльника должно быть неподвижно закреплено.
Для качественного выполнения монтажа необходимо следить, чтобы на жале паяльника не образовывались раковины и сколы. Рабочая поверхность жала всегда должна быть ровная и блестящая, при наличии неровностей жало паяльника обрабатывают и затачивают напильником под углом 45о— 60о . Нагар, образующийся в процессе выгорания канифоли, необходимо убирать хлопчатобумажной салфеткой через 3-4 пайки.
Необходимо следить за температурой жала паяльника, которая на 50-60 градусов должна быть выше температуры плавления припоя. При пайке припоем ПОС-61 с температурой плавления 190о жало должно иметь температуру 240о-250о.
Для измерения температуры используют термопару. При ее отсутствии, степень нагрева можно определить визуально: если канифоль очень быстро сгорает на жале паяльника с выделением большого количества дыма и припой скатывается с рабочей части, значит, паяльник перегрет; если припой долго плавиться и в процессе пайки тянется за паяльником, то имеет место недогрев. Температуру можно регулировать, изменяя величину рабочего напряжения.
4. Монтажные провода. Марки. Применение
Изготавливаются из чистой электротехнической меди, применяются при объёмном монтаже для внутриблочных и межблочных соединений. Провода могут быть одножильными и многожильными. Большинство монтажных проводов для обеспечения быстрой и надёжной пайки и для зашиты от окисления выпускают с лужёными токоведущими жилами. Лужение производят припоями ПОС-40. ПОС- 61. для высокочастотных цепей радиоэлектронной аппаратуры лужение может быть выполнено серебром.
Маркировка проводов:
ПMB — провод монтажный в полихлорвиниловой изоляции(одножильный)
МГВ — провод монтажный гибкий в полихлорвиниловой изоляции многожильный)
МГШВ — провод многожильный монтажный в шёлковой виниловой изоляции
МГВЭ — провод монтажный гибкий в полихлорвиниловой изоляции (многожильный) экранированный
МГШВЭ — провод многожильный монтажный в шёлковой виниловой изоляции экранированный
МГТФ — провод монтажный гибкий термостойкий с изоляцией из фторопласта
МГТФЭ — провод монтажный гибкий термостойкий с изоляцией из фторопласта экранированный
МГСТ — провод многожильный термостойкий с изоляцией из стекловолокна
В конструкторской документации обязательно указать ГОСТ или технические условия, в соответствии с которыми изготавливают провод, марку провода, сечение токоведущей жилы, при необходимости – цвет
5. Правила выбора и обработки монтажных проводов.
Сечение токоведущей жилы выбирают в зависимости от величины проходящего по ним тока. Изоляцию провода выбирают в зависимости от величины рабочего напряжения и условий эксплуатации. В условиях нормальной температуры и влажности используют провода с полихлорвиниловой и волокнистой (хлопчатобумажной) изоляций. В условиях повышенной температуры и влажности применяются провода с изоляцией из фторопласта, стекловолокна, резины. Для защиты от внешних электромагнитных полей используются экранированные провода. Экраны изготавливают из тонкой лужёной медной проволоки.
Изоляция монтажных проводов снимается методом электрообжига (электронож или паяльник). Применение кусачек и другого режущего инструмента не допускается во избежание обрыва отдельных проволок. Потемнение и оплавление изоляции при обжиге допускается не более, чем на 1мм. Изоляцию снимают на расстоянии 10-15мм. Жилы многожильных проводов скручивают под углом 15- 30 градусов к оси провода. После скрутки провод залуживают, отступая от изоляции на 1мм. Лужение должно быть «скелетным».
6. Правила крепления проводов к контактам различного типа.
Способ крепления провода зависит от типа контакта:
1. Штыковые контакты. К ним провода сечением 0.35мм и меньше крепят полным оборотом вокруг штыка. Провода большего сечения крепят на три четверти оборота. Крепить провода нужно так, чтобы расстояние от пайки до изоляции провода было 0.5-2мм (I мм). На I штырёк допускается крепить не более трёх проводов, каждый провод закрепляется самостоятельно.
2. Трубчатые контакты пайка производится без механического крепления. Провод заводят в контакт и запаивают так, чтобы расстояние от пайки до изоляции провода было 0.5-2мм
3. Лепестковые контакты. Маломощные контакты (легко гнутся) паяют без механического крепления. Провод заводят в отверстие, плотно зажимают к лепестку и запаивают по всей поверхности соприкосновения.
Мощные контакты. К ним провода припаивают с предварительным механическим креплением. маломощном контакте. На один лепесток крепят не более трёх проводов. Так же необходимо соблюдать основное требование при пайке проводов — расстояние от пайки до изоляции провода должно быть 0.5-2мм.
7. Виды монтажа радиоэлектронной аппаратуры. Их отличия
При изготовлении радиоаппаратуры используются следующие виды монтажа:
1.Объёмный монтаж. Обеспечивает соединения различных электро и радиоэлементов, узлов и модулей радиоэлектронной аппаратуры в единую конструкцию при помощи проводов, жгутов, разъёмов, кабелей и т.д. Элементы устанавливаются на платах со штырьками, микросхемы при объёмном монтаже не применяются.
Недостатки: высокая трудоёмкость, невозможность автоматизации и механизации, трудность получений идент ичных образцов, наличие паразитных ёмкостей и наводок на длинных проводах.
2. Печатный монтаж. Это электрическое соединение радиоэлементов с помощью плоских печатных проводников на плате, которые получают методом металлизации поверхности или травлением фольгированных материалов, плоские
медные проводники заменяют монтажные провода. Печатный монтаж может быть односторонним, двухсторонним и многослойным. Преимущества: уменьшение габаритов и веса изделий. Возможность автоматизации и механизации производства. Устранение паразитных ёмкостей и наводок. Повышение надёжности, получение идентичных образцов.
3. Поверхностный монтаж. Является разновидностью печатного монтажа. Радиоэлементы устанавливаются на поверхности печатной платы, а не в отверстие как при печатном монтаже. Для выполнения поверхностного монтажа требуется специальная элементная база, освоение новых технологических процессов, высокая точность сборочно-монтажных работ. При поверхностном монтаже дополнительно уменьшаются габариты и массы изделия, повышаются технические характеристики.
Объёмный монтаж. Недостатки.
Объёмный монтаж обеспечивает соединения различных электро и радиоэлементов, узлов и модулей радиоэлектронной аппаратуры в единую конструкцию при помощи проводов, жгутов, разъёмов, кабелей и т.д. Элементы устанавливаются на платах со штырьками, микросхемы при объёмном монтаже не применяются. Объёмный монтаж выполняется в следующей последовательности:
· мерная резка провода
· удаление изоляции с жил монтажных проводов
· заделка концов волокнистой изоляции или экранирующей оплётки при помощи нитяного бандажа, клея или изоляционной трубки
· скрутка и лужение токоведущей жилы
При выполнении объёмного монтажа необходимо соблюдать ряд требований:
· все соединения проводов должны выполняться только после механического крепления,
· не допускается повреждение изоляции провода
· монтажные провода должны иметь запас на 1,2 перепайки
· если расстояние между токоведущими контактами менее 2мм. то на выводы надевают изоляционную трубку
· расстояние между проводами и подвижными частями изделия должно быть не менее 5 мм.
Недостатки: высокая трудоёмкость, невозможность автоматизации и механизации, трудность получений идентичных образцов, наличие паразитных ёмкостей и наводок на длинных проводах.
Печатный монтаж. Преимущества
Печатный монтаж — это электрическое соединение радиоэлементов с помощью плоских печатных проводников на плате, которые получают методом металлизации поверхности или травлением фольгированных материалов, плоские медные проводники заменяют монтажные провода. Печатный монтаж может быть односторонним, двухсторонним и многослойным.
Печатный монтаж выполняют в следующей последовательности:
· Осуществляется входной контроль печатной платы и радиоэлементов
· Производится формовка и установка радиоэлементов на плату в соответствии со сборочным чертежом.
· Производится пайка
Преимущества: уменьшение габаритов и веса изделий. Возможность автоматизации и механизации производства. Устранение паразитных ёмкостей и наводок. Повышение надёжности, получение идентичных образцов.
Двухсторонний и многослойный печатный монтаж позволяет дополнительно уменьшить габариты и вес изделия.
Объемный и поверхностный монтаж. История развития технологии монтажа
Подробности Автор: EngineerDeveloper®При использовании корпусов типа DIP и пассивных выводных корпусов, в первую очередь требуется наличие посадочных отверстий для их монтажа. Такой тип компонентов используется в тех случаях, когда нет требований к размерам печатной платы разрабатываемого устройства. Обычно подобный монтаж применяется с целью удешевления разработки. Но цена, как правило, становится дешевле, но разница с планарным монтажом остается не большая. Это объясняется большим количеством сверловочных отверстий.
В случае использования навесного монтажа существенно увеличивается габаритные размеры платы и длина проводников, что не позволит работать устройству на высоких частотах. Поэтому навесной монтаж не рекомендуют использовать при разработке высокочастотных устройств, а так же аналоговых устройств расположенных поблизости с высокоскоростными логическими схемами.
Некоторые разработчики с целью уменьшения длины проводников располагают резисторы вертикально. Но при таком включении компонента увеличивается путь прохождения тока через резистор, а сам резистор представляет собой петлю (виток индуктивности). В этом случае способность излучения у этого компонента возрастает. Так же компонент с подобным включением наводится большое количество помех и шумов.
При использовании планарного (поверхностного) монтажа отверстия под посадку не требуются. Однако возникают трудности при наладке и тестировании, монтаже. Т.е. возникает необходимость в установке дополнительных контрольных точек. Но при поверхностном монтаже взаимное влияние компонентов на ВЧ возможно свести к минимуму. Так же существенно д\возрастает трудоемкость монтажа при использовании малого типоразмера компонентов.
Общая тенденция развития электроники на протяжении последних 50 лет — увеличение сложности и удешевление. Если в 1950 году радиоприемник стоил так дорого, что месячной зарплаты инженера могло не хватить на его покупку, то сегодня на среднюю зарплату можно купить сотню радиоприемников. Удешевление возможно только благодаря изменению конструкции таким образом, что количество ручного труда сводится к минимуму. Попробуем посмотреть как же изменялся вид электронных блоков.
Исторически самой первой технологией является так называемый объемный монтаж или навесной монтаж . Радиоэлементы припаиваются к рядам специальных лепестков, и соединяются между собой проводами, объединенными в жгуты.
Сборка полностью вручную, автоматизировать процесс такой сборки затруднительно. Возможен другой вариант, когда лепестки расположены иначе:
Плотность упаковки минимальная, стойкость к ударам и вибрациям также невысокая.
Для примера измерительный прибор выполненный по технологии навесного монтажа:
Трудоёмкость сборки таких приборов можно представить.
Затем у инженеров появилась идея. Если радиодетали соединены особым образом в устройстве, то можно каким-нибудь массовым способом изготавливать заранее этот рисунок соединения деталей меж собой из проводника, и просто закреплять детали в нужных местах, они соединятся между собой в правильном порядке автоматически. Так появились печатные платы.
Печатная плата — это пластинка из гетинакса или стеклотекстолита, на которой нанесен рисунок из медной фольги с отверстиями для выводов радиоэлементов. Радиодетали просто вставляются в отверстия и припаиваются к рисунку из фольги. Прелесть такого способа в том, что во-первых сами платы с рисунком можно изготавливать массово травлением, а во вторых что при определенных доработках можно припаивать все элементы к плате разом, окуная в расплавленный припой всю плату.
Вот пример радиоприемника с печатной платой. Можно увидеть, что детали упакованы довольно плотно.
Измерительный прибор при переходе на печатный монтаж стал внутри компактнее:
А в следующем поколении еще компактнее:
Параллельно с развитием технологии печатных плат стала развиваться микроминиатюризация. Сами элементы стали компактнее благодаря появлению полупроводниковых элементов и переходу на низкое напряжение питания. Затем сами элементы стали на заводах собираться в микросборки, микромодули, и в конце концов появились микросхемы. С ростом плотности упаковки элементов в корпусах сборок сам рисунок соединения деталей на плате стал плотнее и в конце концов стало невозможным уместить его на плоскости без пересечений. Вот пример блока, построенного на микросборках, в котором помимо печатного рисунка используются перемычки:
Но перемычки требуют напайки вручную. Следующим этапом стало размещение проводящего рисунка из медной фольги с двух сторон. Вот пример с микросхемами:
Внимательные читатели могли заметить что при создании печатной платы с двухсторонним рисунком появились дорожки, которые через отверстие «ныряют» на другую стороны. Это так называемые переходные отверстия . Их создание не так просто, и если просто печатную плату одностороннюю можно изготовить в домашних условиях то изготовить двухстороннюю печатную плату с переходными отверстиями затруднительно, так как стенки отверстия должны быть покрыты слоем меди, который выращивают гальванически. Подробнее процесс изготовления плат будет рассмотрен в другой статье.
В дальнейшем элементы становились еще мельче, их упаковка становилась еще плотнее. Появилась технология поверхностного монтажа , когда деталь напаивалась на дорожки всем своим телом, а не через проволочные выводы продетые через отверстия в плате и припаянные к проводникам с обратной стороны. В таком случае элементы устанавливаются в нужное место роботом и печатная плата может быть изготовлена полностью автоматически.
Для удешевления и уменьшения габаритов кристаллы микросхем стали крепить непосредственно к плате, заливая компаундом. Вы могли видеть такие черные капли на печатной плате. Вот кристалл микросхемы не залитый компаундом:
Стало невозможным выполнить все необходимые соединения пользуясь всего двумя слоями проводников, поэтому стали делать многослойные печатные платы . Они дороже, сложнее в изготовлении, стараются обойтись без них, но не всегда это возможно.Фотография разреза материнской платы компьютера:
Видно, что помимо наружных слоев с проводниками есть два внутренних. А отверстия имеют металлизацию.
В итоге что мы можем наблюдать — электронные блоки становятся дешевле, компактнее благодаря переходу от ручного труда к технологиям автоматической групповой сборки. Автоматизация — это единственный способ повысить благосостояние каждого человека за счет существенного удешевления производства вещей. Размещение сборочных производств в странах с дешевым трудом дадут лишь временный, несущественный эффект.
Изготавливаются из чистой электротехнической меди, применяются при объёмном монтаже для внутриблочных и межблочных соединений. Провода могут быть одножильными и многожильными. Большинство монтажных проводов для обеспечения быстрой и надёжной пайки и для зашиты от окисления выпускают с лужёными токоведущими жилами. Лужение производят припоями ПОС-40. ПОС- 61. для высокочастотных цепей радиоэлектронной аппаратуры лужение может быть выполнено серебром.
Если провода используют при температуре 250 градусов и более, то для защиты от окисления их покрывают никелем.
Сечение токоведущей жилы выбирают в зависимости от величины проходящего по ним тока. Сечение соответствует определенному ряду в соответствии со стандартом.
Изоляцию провода выбирают в зависимости от величины рабочего напряжения и условий эксплуатации. В условиях нормальной температуры и влажности используют провода с полихлорвиниловой и волокнистой (хлопчатобумажной) изоляций. В условиях повышенной температуры и влажности применяются провода с изоляцией из фторопласта, стекловолокна, резины. Для защиты от внешних электромагнитных полей используются экранированные провода. Экраны изготавливают из тонкой лужёной медной проволоки.
Маркировка проводов:
ПMB — провод монтажный в полихлорвиниловой изоляции(одножильный)
МГВ — провод монтажный гибкий в полихлорвиниловой изоляции многожильный)
МГШВ — провод многожильный монтажный в шёлковой виниловой изоляции
МГВЭ — провод монтажный гибкий в полихлорвиниловой изоляции (многожильный) экранированный
МГШВЭ — провод многожильный монтажный в шёлковой виниловой изоляции экранированный
МГТФ — провод монтажный гибкий термостойкий с изоляцией из фторопласта
МГТФЭ — провод монтажный гибкий термостойкий с изоляцией из фторопласта экранированный
МГСТ — провод многожильный термостойкий с изоляцией из стекловолокна
В конструкторской документации обязательно указать ГОСТ или технические условия, в соответствии с которыми изготавливают провод, марку провода, сечение токоведущей жилы, при необходимости – цвет.
Виды монтажа.
Объемный монтаж .
Обеспечивает соединение различных электро и радиоэлементов, узлов, модулей РЭА в единую конструкцию при помощи проводов, кабелей, жгутов, разъемов и т.д. Микросхемы при объемном мо
Конвекционная пайка
Конвекционная пайкаМощные контакты. К ним провода припаивают с предварительным механическим креплением. маломощном контакте. На один лепесток крепят не более трёх проводов. Так же необходимо соблюдать основное требование при пайке проводов — расстояние от пайки до изоляции провода должно быть 0.5-2мм.
7. Виды монтажа радиоэлектронной аппаратуры. Их отличия
При изготовлении радиоаппаратуры используются следующие виды монтажа:
1.Объёмный монтаж. Обеспечивает соединения различных электро и радиоэлементов, узлов и модулей радиоэлектронной аппаратуры в единую конструкцию при помощи проводов, жгутов, разъёмов, кабелей и т.д. Элементы устанавливаются на платах со штырьками, микросхемы при объёмном монтаже не применяются.
Недостатки: высокая трудоёмкость, невозможность автоматизации и механизации, трудность получений идент ичных образцов, наличие паразитных ёмкостей и наводок на длинных проводах.
2. Печатный монтаж. Это электрическое соединение радиоэлементов с помощью плоских печатных проводников на плате, которые получают методом металлизации поверхности или травлением фольгированных материалов, плоские
медные проводники заменяют монтажные провода. Печатный монтаж может быть односторонним, двухсторонним и многослойным. Преимущества: уменьшение габаритов и веса изделий. Возможность автоматизации и механизации производства. Устранение паразитных ёмкостей и наводок. Повышение надёжности, получение идентичных образцов.
3. Поверхностный монтаж. Является разновидностью печатного монтажа. Радиоэлементы устанавливаются на поверхности печатной платы, а не в отверстие как при печатном монтаже. Для выполнения поверхностного монтажа требуется специальная элементная база, освоение новых технологических процессов, высокая точность сборочно-монтажных работ. При поверхностном монтаже дополнительно уменьшаются габариты и массы изделия, повышаются технические характеристики.
8. Объёмный монтаж. Недостатки.
Объёмный монтаж обеспечивает соединения различных электро и радиоэлементов, узлов и модулей радиоэлектронной аппаратуры в единую конструкцию при помощи проводов, жгутов, разъёмов, кабелей и т.д. Элементы устанавливаются на платах со штырьками, микросхемы при объёмном монтаже не применяются. Объёмный монтаж выполняется в следующей последовательности:
· мерная резка провода
· удаление изоляции с жил монтажных проводов
· заделка концов волокнистой изоляции или экранирующей оплётки при помощи нитяного бандажа, клея или изоляционной трубки
· скрутка и лужение токоведущей жилы
При выполнении объёмного монтажа необходимо соблюдать ряд требований:
· все соединения проводов должны выполняться только после механического крепления,
· не допускается повреждение изоляции провода
· монтажные провода должны иметь запас на 1,2 перепайки
· если расстояние между токоведущими контактами менее 2мм. то на выводы надевают изоляционную трубку
· расстояние между проводами и подвижными частями изделия должно быть не менее 5 мм.
Недостатки: высокая трудоёмкость, невозможность автоматизации и механизации, трудность получений идентичных образцов, наличие паразитных ёмкостей и наводок на длинных проводах.
9.Печатный монтаж. Преимущества
Печатный монтаж — это электрическое соединение радиоэлементов с помощью плоских печатных проводников на плате, которые получают методом металлизации поверхности или травлением фольгированных материалов, плоские медные проводники заменяют монтажные провода. Печатный монтаж может быть односторонним, двухсторонним и многослойным.
Печатный монтаж выполняют в следующей последовательности:
· Осуществляется входной контроль печатной платы и радиоэлементов
· Производится формовка и установка радиоэлементов на плату в соответствии со сборочным чертежом.
· Производится пайка
Преимущества: уменьшение габаритов и веса изделий. Возможность автоматизации и механизации производства. Устранение паразитных ёмкостей и наводок. Повышение надёжности, получение идентичных образцов.
Двухсторонний и многослойный печатный монтаж позволяет дополнительно уменьшить габариты и вес изделия.
10.Технология выполнения поверхностного монтажа.
Является разновидностью печатного монтажа. РЭ элементы устанавливаются на поверхности печатной платы, а не в отверстия, как при печатном монтаже. Для выполнения ПМ требуется специальная элементная база, освоение новых технологических процессов, высокая точность сборочно-монтажных работ.
Преимущества поверхностного монтажа:
1. уменьшаются габариты и масса изделия,
2. повышаются технические характеристики за счет уменьшения длины выводов РЭ и проводников печатной платы.
3. сборочно-монтажные работы полностью автоматизированы.
В основном применяется смешанный монтаж, когда с одной стороны устанавливаются штыревые компоненты, а детали для поверхностного монтажа- с одной или двух сторон.
К элементам ПМ относятся:
1. Печатные платы для ПМ, которые называются коммутационными.
2. Платы могут быть однослойными и многослойными.
2. компоненты для поверхностного монтажа, которые делят на 3 группы:
а) пассивные элементы
· резисторы, которые имеют прямоугольную или цилиндрическую форму с металлизированными торцами.
· конденсаторы, изготовленные по многослойной технологии из керамики и металла
· диоды
б) активные элементы
· транзисторы, которые имеют 3 или 4 вывода и корпус типа SOT (Smoll outlin транзишин)
· микросхемы в корпусах типа SOIC – малогабаритный; QFP –квадратный выводы с четырех сторон; BGA -с матричнам расположением выводов.
в) нестандартные – это намоточные элементы, выключатели, розетки, соединители и т.д.
Технологический процесс пайки при ПМ состоит из следующих операций:
1. нанесение припойных паст и клея
2. монтаж компонентов (установка) – основная операция ПМ, которая должна отличаться высокой точностью
1. Пайка (ИК, волной припоя и т.д.)
2. очистка и прмывка от флюса
5. контрольные операции. Визуальный контроль затруднен из-за малых габаритов и высокой плотности монтажа. Поэтому широко используют методы автоматического видеоконтроля на основе распознавания образцов или контроля качества пайки на основе лазерной техники.
Исправление брака при ПМ сводится к повторному выполнению части сборочно-монтажной операции.
11. Методы групповой пайки для выполнения печатного монтажа со штыревыми компонентами.
При групповой пайке одновременно производится пайка большого количества контактов.
Групповые методы пайки печатных плат со штыревыми компонентами производятся на автоматических или полуавтоматических приспособлениях. . При выполнения автоматической пайки большое значение имеют подготовительные процессы: подготовка плат и выводов элементов, правильный подбор флюсов т припоев. Т.е. платы и выводы должны быть хорошо зачищены и залужены.
1. Наиболее простой способ полуавтоматической пайки – погружение платы в расплавленный припой, при котором происходит одновременная пайка множества соединений. Но при этом способе не всегда обеспечивается качественная пайка: остаются не пропаянные соединения и сосульки припоя. Для устранения этих недостатков осуществляют вибрацию ванны или платы.
2. Метод погружения в расплавленный припой с защитной маской во избежание перегрева платы.
3. Пайка волной припоя, при котором плата проходит над волной, созданной принудительной подачей сжатого воздуха
Применяется для пайки печатных плат со штыревыми компонентами. Принцип метода – плата прямолинейно проходит через гребень волны припоя.
Этапы пайки:
а) входной контроль собранного узла
б) закрепление платы в технологическую рамку, фиксация рамки на конвейере
в) покрытие платы флюсом и сушка флюса
г) предварительный подогрев платы
д) пайка волной припоя
е) изъятие платы с конвейера, охлаждение, изъятие из рамки
ж) передача на промывку.
12. Методы групповой пайки для выполнения поверхностного монтажа.
При групповой пайке поверхностного монтажа одновременно производится пайка всех контактов. Наиболее часто применяются :
1. Инфракрасная пайка.
Применяется для выполнения поверхностного монтажа.
Для ИК нагрева используют специальные трубчатые лампы накаливания с вольфрамовыми и нихромовыми нитями, рефлекторы. В настоящее время широко применяются керамические панели, которые исключают перегрев отдельных участков платы. Режим работы нагревателей, скорость движения конвейера может регулироваться в каждой. Типовая установка для пайки ИК излучением состоит из колпака и 4 зон нагрева.
Этапы пайки:
а) постепенный предварительный нагрев изделия (зона 1и2)
б) пайка при помощи ИК(3)
в) охлаждение изделия (4)
г) передача на промывку
Конвекционная пайка
Для нагрева используют мощные калориферы, но можно использовать и ИК излучатели. Тепло в печах переносится за счет принудительного движения воздуха вентиляторами. В конвекционной печи плата проходит 4 температурные зоны:
а) зона предварительного нагрева (25-150 градусов)
удаляются летучие компоненты из флюса, плата и компоненты плавно нагреваются
б) зона прогрева (150-180 градусов)
смачиваются выводы компонентов и контактные площадки платы, уравновешивается температура компонентов разной массы и размеров. Нагревается до температуры плавления паяльной пасты.
в) зона пайки (200-210 градусов)
оплавление паяльной пасты
г) зона охлаждения (50-30гр)
д) передача на промывку
4. Конденсационная пайка.
Монтируемый узел или плату нагревают в парофазной среде за счет конденсации пара рабочей жидкости (фторуглероды с температурой кипения 210- 260). Для пайки используются паяльные пасты.
Достоинства метода;
а) невозможность перегрева ( температура не может выше, чем температура кипения жидкости)
б) пайка производится практически в бескислородной среде
в) не требуется промывка после пайки.
Недостатком является большой расход рабочей жидкости, что повышает себестоимость изделия.
13. Способы локальной пайки.
Нагрев производится от точки к точке. При этом все элементы и монтажное изделие остаются холодными. Локальная пайка производится следующими способами:
1. Контактная пайка паяльником. Передача тепла к месту пайки производится за счет прижима жала паяльника. Пайка может осуществляться вручную. Также применяются методы избирательной пайки на автоматических линиях с принудительной подачей припоя к месту соединения.
2. Струйная пайка горячим газом. В качестве газа-теплоносителя используют аргон, гелий, азот при температуре около 300 градусов. Широко применяется направленное пламя, температуру которого можно изменять, используя различные смеси газов. Струйная пайка применяется для соединения проводов большого сечения и контактов с повышенной теплоемкостью или для пайки высокотемпературными припоями.
3. Лучевая пайка. Нагрев сфокусированным световым лучом. (диаметр пайки 1-15мм) используются газоразрядные ксеноновые лампы и галогенные лампы.
4. Лазерная пайка. Нагрев места пайки производится лазерным лучом. Луч проходит по диэлектрику и не нагревает его (не поглощается диэлектриком), но интенсивно поглощается металлом и плавит припой. Лазерную пайку иногда совмещают с системой контроля качества паяных соединений. Непропай может быть идентифицирован по темпу остывания места пайки и установка может вернуться к этой точке и повторить операцию. Применяется для пайки ответственных изделий. При изготовлении бытовой аппаратуры не применяется, т.к. метод дорогой и сложный в работе.
14. Типичные дефекты пайки.
Дефекты пайки приводят к неустойчивому электрическому контакту или к его полному исчезновению.
Виды дефектов:
1. «Холодная» или «ложная» пайка. При визуальном осмотре это может быть: зернистая или матовая поверхность, неполное смачивание или скатывание припоя со спаиваемых поверхностей. Для распознания некачественной пайки припой дозируют так, чтобы образовалась «скелетная», а не заливная пайка.
2. Растворение покрытий соединяемых деталей. Припой загрязняется примесями и снижается его смачиваемость.
3. Отсутствие смачивания. Припой не прилипает к поверхности. Причиной могут быть низкое качество припоя, неправильно подобранный флюс, загрязнение соединяемых поверхностей.
4. Эффект «надгробного камня» — это поднятие одного вывода чип – компонента над поверхностью платы. Это происходит из-за несоответствия размеров контактных площадок, расстояний между ними и расстояний между выводами элемента.
5. Сдвиг компонентов относительно контактных площадок на печатной плате.
6. Отток припоя. Припой поднимается по выводу, ослабляя место соединения.
7. Образование перемычек между контактными площадками. Происходит в основном из-за избытка припоя или паяльной пасты. При установке поверхностных элементов из-за чрезмерного давления на элементы.
8. Отслоение контактной площадки от основания платы.
9. Отсутствие электрического контакта. Это может быть при наличии «ложной» пайки, при отсутствии смачивания, при сдвиге компонентов, при эффекте «надгробного камня»и при отслоении дорожек.
15.Входной контроль печатных плат и радиоэлементов
Входной контроль производится до установки радиоэлементов на печатные платы. Необходимо проверить:
· На печатных платах не должно быть отслоений, окисления, вздутия и механического повреждения токоведущих дорожек, так же не должно быть механических повреждений основания печатной платы (сколов, трещин).
· На радиоэлементах должна быть чёткая маркировка номинала. Не должно быть вмятин и сколов на корпусах радиоэлементов. Эмалевое покрытие корпусов должно быть без повреждений. Выводы элементов должны быть хорошо залужены и не должны иметь механических повреждений.
· При необходимости производится контроль соответствия номиналов радиоэлементов технической документации.
· При пайке проводов необходимо проверить качество лужения, не должно быть повреждений изоляции и надломов жил проводов.
16. Правила формовки выводов радиоэлементов
Перед установкой и креплением элементов их выводы необходимо отформовать в соответствии со стандартом и технической документацией. При этом необходимо соблюдать следующие требования:
· Формовку производить так, чтобы при установке деталей на плату номиналы элементов и знак полярности у диодов и электролитических конденсаторов были хорошо видны
· Изгиб выводов радиоэлементов должен производиться на расстоянии не менее 2мм от корпуса.
· Радиус изгиба примерно равен двум диаметрам вывода
· Выводы элементов в стеклянных корпусах (диоды) формовать на расстоянии не менее З мм от корпуса.. Некоторые виды транзисторов допускается формовать на расстоянии не менее 5 мм.
17.Правила установки радиоэлементов на печатную плату.
Элементы устанавливаются в соответствии с технической документацией так, чтобы было видно номинал и маркировку полярности. Элементы устанавливаются параллельно и перпендикулярно друг другу. Расстояние от корпуса элемента до места пайки в процессе установки должны быть 3-5мм (по выводу). Расстояние между корпусами соседних элементов должно быть не менее 0.5мм. Корпуса радиоэлементов не должны выходить за габариты печатной платы. При установке транзисторов соблюдать маркировку эмиттер-база-коллектор. Микросхемы устанавливают в соответствии с маркировкой первого вывода. При установке элементов на односторонние печатные платы их можно располагать непосредственно на поверхности вплотную к плате. Выводы диаметром 0,7мм и меньше подгибают по дорожке на 1.5-2мм. Многовыводные и регулировочные элементы устанавливают без подгибки выводов. Для установки регулировочных элементов предусматриваются места для многоразовой пайки. Документация регулировочного элемента обозначается звёздочкой (•). При монтаже двухсторонних печатных плат элементы устанавливаются так. чтобы расстояние от корпуса до дорожек было в пределах 0.5-1,5мм. При установке можно использовать диэлектрический материал. В этом случае элементы можно укладывать на поверхность двухсторонней платы. Микросхемы и транзисторы должны быть установлены до упора вывода. Высота выводов элементов (пайки) должна быть 0,5-2мм. Выводы микросхем не подрезают.
18.Контроль монтажа печатных плат.
В процессе проверки необходимо проверить:
· Качество пайки. Пайка должна быть ровной, глянцевой, без пор и посторонних вкраплений. Пайка должна быть «скелетной», то сеть под припоем должен быть виден контур соединяемых выводов или проводов. Должна быть полностью исключена возможность получения «ложной» пайки, при которой существует видимость пайки, но отсутствует электрический контакт.
· Качество формовки и установки элементов на печатную плату.
· Отсутствие отслоения дорожек в результате перегрева основания платы
· Отсутствие замыкания между печатными проводниками в результате разбрызгивания припоя
· При двухстороннем монтаже детали должны быть подняты на 0,5 – 1,5 мм над поверхностью платы.
· Плата должна быть хорошо промыта. Не допускается вытекание флюса и промывочной жидкости на лицевую сторону платы.
19. Пайка радиоэлементов. Требования к пайке
Для получения качественной пайки радиоэлементов монтажник должен:
1.При необходимости очистить выводы элементов от окислов и загрязнений
2. Залудить выводы элементов Лужёная поверхность должна быть ровной, блестящей, без наплывов припоя и непролуженных мест. От качества лужения зависит качество пайки
3. Произвести формовку в соответствии со стандартами или технической документацией
4. Установить элементы в соответствии со сборочным чертежом
5. Произвести пайку. Пайка должна быть ровной, глянцевой, без пор и посторонних вкраплений. Пайка должна быть «скелетной», то сеть под припоем должен быть виден контур соединяемых выводов или проводов. Должна быть полностью исключена возможность получения «ложной» пайки, при которой существует видимость пайки, но отсутствует электрический контакт.
20. Традиционные припои. Требования. Марки.
К традиционным относятся оловянно-свинцовые припои с добавлением легирующих примесей.
Припои используются для выполнения пайки. Пайка — это процесс получения неразъемного соединения металлов и металлизированных поверхностей при помощи легкоплавких сплавов, называемых припоями.
Требования к припоям:
1.Температура плавления припоя должна быть ниже температуры плавления соединяемых металлов.
2. Должен быть малый интервал кристаллизации
3. Припои должны обладать хорошими антикоррозийными свойствами, жидкотекучестью, смачиваемостью.
4. У припоя должна быть достаточная электропроводность, малое переходное сопротивление соединений
5. В процессе пайки не должны выделяться токсичные вещества
6.Припои не должны оказывать химического воздействия на металлы
Все припои делятся на 2 вида:
Твёрдые — температура плавления 450-950 градусов. Изготавливают на основе меди, цинка, серебра. Применяются для пайки конструкционных изделий
Мягкие — температура плавления до 450 градусов. Изготавливаются на основе олова, свинца, индия, кадмия, висмута. Для пайки элементов радиоэлектронной аппаратуры применяются легкоплавкие припои с температурой плавления до 300градусов.
При маркировке припоев используются следующие обозначения: П — припой, О — олово. С — свинец. К — кадмий. Ви — висмут. Ин — индий. Су — сурьма. Ср -серебро. М — медь. Ц — цинк. Мц — марганец
Цифры в марке припоя обозначают % содержания компонентов
Марки припоев
Мягкие припои: ПОС- 61; ПОС — 40. ПОСК 50- 18; ПОСВи 36-4, сплав Розе, сплав Вуда
Твёрдые припои: ПСр — 40. ПСр — 70. ПМЦ — 62.
21. Бессвинцовые припои
Решение экологических проблем при утилизации электронной аппаратуры потребовало изъятия из обращения припоев, содержащих свинец.
Основным недостатком бессвинцовых припоев является большая температура плавления (по сравнению с припоем ПОС-61) и плохая смачиваемость. Поэтому ответственную аппаратуры паяют припоем олово-свинец, а бессвинцовыми- бытовую РЭА.
Самые дешевые заменители ПОС – сплавы на основе олова и меди,
Sn99,3 Cu0,7 – toплавления 227о используется для пайки волной припоя. Обладает плохой смачиваемостью, низкой прочностью и высокой toплавления.
Лучшими свойствами обладают сплавы на основе олова и серебра
Sn96,5Ag3,5 – toплавления 221о применяется в Японии более 15лет,
Sn95,5Ag3,8 Cu0,7 — toплавления 217о признан наилучшим сплавом для замены ПОС в массовом производстве.
Sn93,5Ag3,5 Bi3 toплавления 206о-213о в применении ограничен из-за содержания дорогостоящего висмута
Применяются припои с содержанием цинка. Стоимость меньше, чем у серебросодержащих, но соединение не высокого качества.
Sn89Zn8Bi3 – toплавления 189-199о
Для низкотемпературной пайки до 200о используют припои на основе олова, висмута, индия. Имеют высокую стоимость, но не обеспечивают достаточной надежности паек. Применяются для пайки элементов чувствительных к перегреву.
Sn 42Bi58 — toплавления 135-140о
Sn48 In52 — toплавления 115-120о
22.Паяльные пасты.
Паяльная паста – это однородная смесь мелкогранулированного припоя и флюса-связки. Свойства паяльной пасты зависят от процентного содержания металлической составляющей, типа сплава, размеров частиц припоя и типа флюса.
К паяльным пастам предъявляются следующие требования:
1. не должно происходить разбрызгивания припоя в процессе пайки.
2. хорошая смачиваемость, способность к капилярному подъему и растеканию;
3. остатки флюса в составе паяльной пасты должны легко отмываться после пайки;
4. минимальное расслоение пасты за счет высокой плотности припоя;
5. хорошая формоустойчивость порций пасты, нанесенных на плату;
6. хорошая клейкость для фиксации элементов на плате;
7. стабильность свойств пасты в течение определенного времени.
Дата добавления: 2015-08-05; просмотров: 436 | Нарушение авторских прав
mybiblioteka.su — 2015-2020 год. (0.033 сек.)
Пайка радиодеталей, нюансы в монтаже радиоэлементов
Пайка радиодеталей позволяет собрать множество радиоэлементов в электронную схему определенного функционального назначения. Корректность по отношению к принципиальной схеме, аккуратность, последовательность в работе избавят Вас от необходимости еще раз переделывать то, что можно было сделать с первого раза.
При всей кажущейся новичку сложности — нет в процессе пайки радиодеталей ничего сложного, и при всей кажущейся самоуверенному новичку простоте – руку все-таки придется «набить».
А чтобы это было проще сделать немного теории и практических советов…
Что такое пайка
Пайка – это процесс соединения двух или более деталей посредством образования молекулярной связи между ними и более легкоплавким металлом – припоем.
Для соединения радиокомпонентов: диодов, конденсаторов, светодиодов используют обычно припой, состоящий из 61% олова и 39% свинца. Сплав свинца и олова в таком соотношении плавится при температуре 190ОС, а маркируется как ПОС-61 (Припой Оловянно-Свинцовый, 61% олова)
Процентное соотношение содержания свинца и олова определяют тугоплавкость припоя. Большее содержание свинца – более высокая температура плавления.
ПОС-61 еще называют «третник» из-за 1/3 доли свинца в нем.
Припой в «удобном» для пайки виде можно приобрести в виде мотка тонкой трубочки, внутри которой находится флюс, то есть канифоль.
Существует несколько видов флюса для пайки различных металлов, но для монтажа радиодеталей обычно используется именно канифоль.
Предназначение флюса в освобождении поверхностей, которые будут спаиваться, от окислов, а также способствовать лучшему растеканию припоя по поверхности металла.
Инструмент
Пайка невозможна без паяльника. Они бывают разные, но нас сейчас интересует одно их отличие – мощность. Паяльник мощностью от 20 до 40 Вт оптимально подойдет для большинства радиотехнических работ.
Внимание! Большинство радиоэлементов очень чувствительны к чрезмерному перегреву. Поэтому время касания их паяльником необходимо свести к минимуму.
Подготовка деталей к пайке
Для качественной пайки деталей их выводы предварительно необходимо очистить и залудить. Луженый проводник или место спая – это гарантия получения качественного соединения.
Вариант 1. Проводник или вывод детали чистый без окислов
Берем на жало паяльника немного припоя, касаемся канифоли, легко проводим жалом по выводу, лежащему на деревянной дощечке (желательно). Результат – тонкий слой припоя на поверхности.
Вариант 2. Вывод детали или проводник окисленный
Кладем вывод на таблетку аспирина (она плавится) и прогреваем. Затем лудим обычным способом на дощечке.
Если на выводе или проводнике остались излишки припоя, его можно удалить. Располагаем вывод вертикально, нагреваем паяльником снизу, припой перетечет на жало паяльника.
Монтаж радиодеталей
Невозможно в рамках одной статьи осветить все нюансы монтажа или демонтажа радиодеталей. Поэтому мы рассмотрим несколько типичных примеров пайки радиоэлементов.
Пайка проводников
Например, при монтаже различных участков светодиодной ленты необходимо припаивать проводники к ней. Для RGB-ленты это четыре проводника, для светодиодной ленты монохромного свечения по два.
Технология действий при пайке светодиодной ленты такова:
- отрезаем участок светодиодной ленты;
Внимание! Лента режется секциями по 3 светодиода необходимой длины по контактным площадкам!
- лудим контактные площадки;
Внимание! Делайте это паяльником мощностью 25Вт с тонким жалом. Перегрев контактных площадок светодиодной ленты грозит выходом из строя «близ-сидящих» светодиодов: одного от перегрева, остальные 2 из секции «за компанию»!
- Отрезаем проводники необходимой длины;
- Зачищаем на 3-5 мм и лудим их на деревянной дощечке;
- Прикладываем поочередно к контактным площадкам светодиодной ленты и жалом паяльника прогреваем место пайки.
Навесной монтаж деталей с выводами
К деталям с выводами мы можем отнести обычные резисторы, диоды,, конденсаторы и др.
При пайке радиодеталей навесным монтажом удобна такая технология:
- зачищаем выводы;
- лудим;
- прикладываем выводы друг к другу, по возможности фиксируем пинцетом или скручиваем;
- проглаживаем плоскостью жала паяльника с предварительно набранным припоем и флюсом;
- убираем жало паяльника, сохраняя неподвижность деталей,
- забираем пинцет после остывания места пайки.
Внимание! Процесс пайки должен быть быстротечным – детали боятся перегрева! В случае неудачной попытки (5-10 с) прогрева даем деталям возможность остыть. При пайке светодиодов, диодов желательно удерживать их пинцетом между местом пайки и корпусом. Пинцет в этом случае будет играть роль теплоотвода.
Монтаж элементов с выводами на печатную плату
- подгибаем пинцетом или тонкими плоскогубцами выводы, например, диодов до совпадения их с необходимыми отверстиями.
Внимание! Нельзя гнуть выводы диодов, конденсаторов, светодиодов непосредственно у их корпуса – необходимо отступать 2-5 мм.
- желательно залудить выводы диодов до вставки их на место пайки;
- вставляем деталь на свое место на плате;
- набрав на жало паяльника немного припоя и канифоли (жидкий флюс можно нанести кисточкой непосредственно на место пайки), прикасаемся плоскостью жала к выводу детали;
- в нормальной ситуации припой фактически мгновенно перетечет с жала на контактную площадку платы;
- забираем паяльник, место спая остывает чуть более секунды-двух;
- выступающие выводы диодов откусываем кусачками;
- после монтажа всех элементов (кроме реле, подстроечных резисторов, тумблеров, кнопок и прочей механики) протираем остатки флюса спиртом.
Интересно! Удаление остатков канифоли уменьшит риск нарушения электрического контакта места спая, так как входящая в состав канифоли абиетиновая кислота со временем приводит к окислению металла.
Монтаж smd компонентов без выводов
Примером монтажа SMD компонентов может служить размещение светодиодов на светодиодной ленте. Особенность подобных SMD элементов в том, что они не имеют выводов, а только контактные площадки на корпусе.
Осторожно! Перегрев таких элементов грозит их немедленным выходом из строя.
Пайка чипов, smd диодов, smd светодиодов и др. элементов происходит на подготовленные площадки на плате путем поочередного прогрева маломощным пальником каждой контактной площадки. Это несложно.
Сложнее безопасно демонтировать, например, SMD светодиод с платы. Он очень хрупкий, боится перегрева, контактные площадки SMD элемента легко отпадают, а припаян он на противоположных гранях. Задача – одновременно прогреть два контакта SMD светодиода.
Это может быть реализовано путем использования специально сделанного двойного жала паяльника (намотка из проволоки диаметром 1 мм на основное жало паяльника), для одновременного прогрева SMD светодиодов или диодов с двух сторон.
Демонтаж вздувшихся конденсаторов с материнской платы
Для демонтажа вздувшихся конденсаторов должна выполняться очень аккуратно – материнская плата многослойная, контактные дорожки очень тонкие. Паяльник ля выпаивания конденсаторов желательно использовать 40- ватный с заточенным до ширины 3 мм жалом.
Выводы конденсаторов выпаиваем поочередно:
прогреваем один, одновременно отгибая корпус конденсатора так, чтобы вывод немного сдвинулся;
прогреваем второй с аналогичными действиями;
вновь возвращаемся к первому и т.д.
Пайка исправных конденсаторов происходит в подготовленные посадочные отверстия. Для этого следует удалить из отверстий для ножек конденсаторов припой. Для этого контактную площадку нагреваем паяльником и вставляем в отверстие зубочистку. Затем вместо зубочистки вставляем швейную иглу (0,5 мм) и прогревая контактную площадку с другой стороны просовываем иголку, вращая ее, чтобы не прилипла.
Монтаж конденсаторов заканчивается установкой их на место с соблюдением полярности, прогревом контактов и откусыванием излишков.
Пусть эти несколько примеров монтажа радиоэлементов помогут Вам «стартануть» в занимательный мир радиоэлектроники.
Похожие статьиПечатная плата и навесной монтаж: в чем разница? / g.a.s. / Jablog.Ru
Вопрос, который уже не одно десятилетие занимает музыкальную общественность: что лучше раскрывает тональные характеристики усилителя? Ручная сборка и навесной монтаж деталей или автоматизированная установка компонентов на печатных платах? Мы решили привлечь к этой дискуссии трех гуру из мира создания усилителей, чтобы узнать ответ.Некоторые пуристы утверждают, что усилители, схема которых собрана вручную способом навесного монтажа электроники, всегда звучат лучше, чем те, электронные компоненты которых монтируются на используемых в массовом производстве печатных платах (в англ. – PCB — printed circuit board).
Конечно, по нашим собственным ощущениям хорошая ручная сборка всегда должна быть лучше машинной штамповки. Однако усилители, собранные на печатных платах по своим характеристикам могут превосходить усилители ручной сборки, при условии продуманной и проработанной конструкции. В частности, в новой линейке усилителей Astoria от Marshall используется как навесной монтаж, так и печатные платы.
Навесной монтаж
Начнем с навесного монтажа. Что он, собственно, из себя представляет? В него входит множество различных методов конструирования.
Усилители Fender до 1986 года использовали монтажные панели (так называемые eyelet board) из диэлектрического материала с проделанными отверстиями, компоненты же продевались сквозь эти отверстия и соединялись друг с другом.
Разъемы для ламп, а также передняя и задняя панели всегда монтируются навесным способом. Также в конструкции многих ранних британских усилителей применялись бакелитовые полоски с двухсторонними рядами клемм-башенок (turret board), на которые и монтировали компоненты.
Все это в совокупности является навесным монтажом – когда каждый электронный компонент монтируется вслед за предыдущим на одной или нескольких монтажных панелях.
Этот способ установки компонентов является самым простым, но также и самым трудоемким. Все компоненты должны быть не только вручную припаяны и правильно расположены, но также каждое звено схемы должно максимально соответствовать оригиналу по своим параметрам и характеристикам.
Ранние усилители Hiwatt и оригинальные Matchless создавались с навесным монтажом. На сегодняшний день очень мало серийных усилителей производятся с навесным монтажом, хотя усилители Carr являются одним из известных примеров. Также некоторые компании используют в усилителях обновленные версии «фендеровских» монтажных панелей с отверстиями.
Печатные платы
Первоначально идея сделать токопроводящие медные дорожки на одном куске непроводящего электрический ток материала (диэлектрика) восходят к 20-м годам XX века, но только после Второй Мировой войны их начали изготовлять в больших объемах.
Есть десятки различных видов печатных плат, от самых простых односторонних с медными дорожками на стеклотекстолите (или подобном диэлектрическом материале), до комплексных многослойных и технически сложных плат, используемых в компьютерной и космической технике.
В большинстве случаев в гитарных усилителях стоят односторонние или двухсторонние платы, в которых с одной стороны припаиваются электронные компоненты, а с другой стороны проходят маленькие металлические дорожки, соединяющие все детали схемы в единую конструкцию.
Когда электронный компонент запаивается в плату, он надежно фиксируется в ней, что дополнительно повышает надежность конструкции.
Наиболее важным моментом для производителей в производстве печатных плат является возможность полностью автоматизировать паяльный процесс. Вместо трудозатратного последовательного запаивания каждого компонента, автомат на конвейере может сразу вставить все компоненты в одну плату и опустить ее в ванну с расплавленным припоем, что сокращает временные затраты на производство каждой схемы в сотни раз. Однако, не все так просто. Некоторые типы печатных плат не переносят повторное нагревание и охлаждение – они могут привести к появлению трещин, что увеличивает электрическое сопротивление токопроводящих дорожек, влияя на звуковые характеристики аппаратуры. Увеличение сопротивления в сильноточных местах может привести к тому, что дорожка может попросту сгореть.
Есть еще одно преимущество печатных плат – их однотипность и возможность многократного точного воспроизведения изначального образца. Дело в том, что каскады хай-гейн аппаратуры очень чувствительны – малейшие сдвиги компонентов даже на 1мм могут иногда повлиять на звуковые характеристики усилителя. При ручной сборке схемы невозможно достичь абсолютно одинакового расположения компонентов, по этой причине многие производители Hi-End аппаратуры, в частности, такие как Bogner и Soldano используют печатные платы высокого качества, с большой толщиной платы и толстыми медными проводниками.
Навесной монтаж и печатные платы часто соседствуют друг с другом, используя преимущества обеих технологий. В таких высококлассных усилителях как Royalist от Tone King или Astoria от Marshall используются качественные печатные платы с ручной установкой компонентов и переключателей.
По нашему опыту, лучший результат всегда достигается, когда достоинства обеих методов конструирования сочетаются вместе.
Спросим у экспертов
Все описанное выше наиболее часто встречается в подобных спорах. Но что думают профи? Мы решили узнать у троих именитых проектировщиков звукоусилительной техники, что они думают по этому поводу…
Адриан Эмсли (Adrian Emsley) – проектировщик всех усилителей Orange, от коммерчески успешной серии Crush до ограниченных изданий Custom Shop ручной сборки, которые зачастую собираются при участии самого Эмсли.
«Печатные платы и навесной монтаж имеют несколько главных отличий. Что хорошо в навесном монтаже – можно применять в конструкции большие полиэстровые конденсаторы и достойные резисторы. Эти компоненты оказывают большое влияние на звук создаваемого усилителя. К тому же, навесной монтаж проще обслуживать.
В то же время, нет ничего плохого в использовании качественных печатных плат. Хорошо продуманное расположение компонентов на печатной плате, в отличие от навесного монтажа, позволяет экономить место, это имеет особенное значение в больших и сложных схемах. Толщина медных дорожек в две унции (в метрических размерах – 2,8 мм – прим. переводчика) позволит сделать хорошо звучащий и простой в обслуживании усилитель на печатной плате. Я всегда делаю изогнутые дорожки, без прямых углов или срезов углов – таким образом достигается больше музыкальности и меньше шума.»
Марк Бартел (Mark Bartel) – основатель и разработчик бутиковых усилителей Tone King, которые являются одними из самых желанных в мире, и также известный исследованиями и разработками, применяемыми в усилителях Tone King.
«За последние 25 лет я спроектировал множество усилителей как на печатных платах, так и с использованием разных способов навесного монтажа. Я предпочитаю комбинацию из печатных плат и навесного монтажа для достижения лучшего качества звука и эксплуатационной надежности.
Надлежащее использование хорошо спроектированных печатных плат позволяет получить реальные преимущества над собранными вручную монтажными панелями с точки зрения расположения компонентов, размеров и направления, которые позволяют улучшить звучание и повысить надежность
Важнее всего на стадии проектирования свести к минимуму длину проводов и оптимизировать расположение компонентов. Многие собранные с использованием навесного монтажа схемы выглядят прекрасно, с расположенными в ряд компонентами и длинными линиями проводов с красивыми прямыми углами, но эстетическая сторона зачастую совершенно противоположна тому, что является действительно важным для технической составляющей усилителя.
За прошедшие 23 года мы построили тысячи усилителей с печатными платами, большая часть которых ездит по всему миру на постоянных гастролях. На сегодняшний день не возникло ни одной проблемы с платами в этих усилителях.»
Фил Тейлор (Phil Taylor) — признанный эксперт из Mullard Valve Company, разработчик и основатель компании Effectrode, чьи уникальные педали эффектов нашли свое место в педалбордах таких музыкантов, как Дэвид Гилмор, Питер Фремптон, Билли Корган и других.
«Если вы загляните внутрь старого усилителя Hiwatt, то вы увидите прекрасный пример навесного монтажа, где маленькие компоненты – резисторы и конденсаторы – смонтированы на платах с монтажными лепестками.
Хорошо сделанный навесной монтаж деталей выглядит красиво, однако это трудоемкая и высококвалифицированная работа. Каждый компонент припаивается вручную с осторожностью, чтобы избежать его повреждения. Сравните это с печатными платами, где все медные дорожки химически протравлены в плате. Печатная плата позволяет установить компоненты точно и без повреждений, а также упрощает и ускоряет сборку, позволяя автоматизировать процесс.
Есть также еще несколько преимуществ печатных плат: они позволяют проектировку с дополнительным заземлением, позволяя оптимизировать схему и уменьшить ее размер, а также сводя к минимуму шумы. Вдобавок это позволяет уменьшить длину проводников, а иногда и сократить количество точек пайки, гарантируя высокую целостность сигнала и надежность».
musicradar.com