Алатырский механический завод. Официальный сайт
Алатырский механический завод. Официальный сайтМы являемся одними из лидеров на рынке продукции для вагонов
22 декабря 1893 года — дата основания завода (открытие железнодорожных мастерских)
ноябрь 1927 года — преобразование мастерских в Алатырский паровозоремотный завод
Мы предлагаем широкий спектр продукции и услуг
АО «АМЗ» выпускает оборудование для сортировочных горок, замедлители для горочных и парковых тормозных позиций, управляющей аппаратуры, а также запасные части, вагонные котлы и кипятильники, для ремонта пассажирских и грузовых вагонов. Основным потребителем на рынке является ОАО «РЖД»
Мы производим оборудование для механизации процесса регулирования скорости вагонных отцепов на действующих и вновь создаваемых сортировочных горках КНЗ-5пк, КНЗ-3пк, РНЗ-2Мпк, а также воздухосборники с электронным блоком управления ВУПЗ-05М/07АF (А)
Мы производим комбинированные отопительные котлы черт. 19.022.00.000; 19.092.00.000, кипятильник КВ-1М (50В, 110В) и запасные части к ним, детали для формирования колесной пары грузового вагона.
Мы осуществляем ремонт вагонных замедлителей, а также предоставляем токарные, фрезерные и иные работы по металлу.
Высочайшее качество нашей продукции и услуг оценили потребители по всей Роcсии
За годы работы мы доказали потребителям, что можем производить качественную и конкурентоспособную продукцию, которая получила распространение по всей России, начиная от вагонных замедлителей и заканчивая кипятильниками в вагонах. Это подтверждается тем, что одним из наших клиентов является РЖД.
Наши достижения
45%
Доля на рынке вагонных замедлителей
85%
Доля на рынке вагонных котлов
72%
Доля на рынке кипятильников
Наши клиенты
Нашими клиентами являются крупные и небольшие компании
Последние новости
13. 10.2017 Алатырский механический завод произвёл отгрузку вагонного замедлителя КНЗ-5.
Сетевой семинар «Результаты эксплуатации горочного оборудования и аппаратуры торможения сортировочных горок, выпускаемых на базе ЗАО Концерн «ТРАНСМАШ» и АО «Алатырский механический завод».
Наша продукция
Контакты
Россия, 429826, Чувашская Республика, г. Алатырь, Больничный переулок, 14
8 (83531) 2-03-85
Пн-Пт: с 7 до 16
Потомки самовара
Промышленные водонагреватели (кипятильники) относятся к самому распространенному электрооборудованию, используемому на предприятиях питания. Кипяченая и горячая вода необходима во всех ресторанах, барах, кафе и фаст-фудах. Они могут иметь разный ассортимент предлагаемых блюд, но чай, кофе или другие горячие напитки практически всегда присутствуют в их меню.
Профессиональный водонагреватель (электрический кипятильник) — это электроприбор, предназначенный для приготовления питьевой воды до температуры в пределах от 30 до 100 °C.
Источником тепла для водонагревателей является твердое топливо, газ, горячий пар или электричество. Наибольшее распространение получили электрические модели.
Виды профессиональных водонагревателей
Водонагреватели различаются по объему резервуара для воды, мощности, материалу изготовления и функциональности. Одни из них способны только нагревать воду до заданной температуры, после чего она постепенно остывает, а другие – постоянно поддерживают определенную температуру воды после ее кипячения. Более сложные современные модели имеют защиту от так называемого «сухого хода», — при отсутствии воды в баке нагреватель автоматически выключается, а некоторые из них оборудованы индикатором уровня воды.
По принципу действия все водонагреватели (кипятильники) делятся на две большие группы – аппараты периодического действия, которые иногда называют аккумуляционными или наливными, и непрерывного, т.е. проточные.
Аккумуляционные водонагреватели
Принцип работы и использование
Аккумуляционный водонагреватель представляет собой емкость, которую периодически необходимо наполнять водой. Он имеет цилиндрическую форму и выглядит как бак из нержавеющей стали. Пар, образующийся при кипении, и излишки воды удаляются при помощи дренажного патрубка. После нагрева воды, когда требуется лишь поддерживать её определенную температуру, водонагреватель переходит в режим экономии электроэнергии.
Такие водонагреватели получили распространение в заведениях с невысокой проходимостью, к примеру, в небольших фаст-фудах, столовых или кафе, где они ставятся на барную стойку или в пределах досягаемости персонала, обслуживающего линию раздачи.
Проточные водонагреватели
Конструкция
Водонагреватель непрерывного действия (проточный промышленный водонагреватель) имеет более сложную конструкцию и принцип работы. Он подключается к системе водоснабжения через специальный смеситель, и получает воду из неё.
Проточный кипятильник состоит из сварного металлического корпуса в форме цилиндра, сигнальной трубки уровня, индикаторов, крышки, ручек, поплавкового клапана, автоматического пускового устройства и водоразборного крана. Внутри корпуса устанавливается питательная коробка, поддерживающая постоянный уровень воды во всем объеме бака, а также кипятильный объем с переливной трубкой, работающие как сообщающиеся сосуды. Вода в кипятильном объеме нагревается ТЭНами. На передней панели устройства расположены индикаторы уровня нагрева и кипения воды.
Холодная вода поступает в кипятильник из водопровода при помощи подающей трубы и клапана в питательную коробку. Она образует совместно с кипятильным объемом единое пространство, которое разделяется переливной трубкой на две части. Во время работы кипятильника уровень воды в зоне рядом с трубкой выше, чем в питательной коробке, поэтому кипяток поднимается вверх, попадая в переливную трубку, и поступает в специальный сборник, откуда его разливают через кран. Для защиты от переполнения питательной коробки кипятильник имеет сигнальную трубку, которая в случае необходимости сливает избыток воды в канализацию.
Использование
Диапазон температур, в пределах которого может осуществляться нагрев, достаточно широк и составляет от 30 до 100 °С, а их производительность составляет от 50 до 100 литров в сутки. Поэтому их целесообразно использовать тогда, когда горячая вода необходима постоянно и в больших количествах, к примеру, в популярных фаст-фудах или кафе.
Уровень воды в кипятильнике не должен опускаться ниже 60-80 мм от кромки переливной трубки. Если он оказывается выше, то в сборник кипятка будет поступать некипяченая теплая вода, а если ниже – то в сборнике окажется много пара, а не вода, поэтому производительность кипятильника понизится.
Чае- и кофераздатчики
Профессиональные чае- и кофераздатчики служат для приготовления и раздачи чая, кофе и других горячих напитков. Они используются практически всеми предприятиями общественного питания – барами, ресторанами, кафетериями, буфетами, а также отелями. Могут применяться и на разных выездных мероприятиях (кейтеринг).
Конструкция
Конструкция чае- и кофераздатчиков внешне схожа с конструкцией водонагревателей. Как и они, чае- и кофераздатчики состоят из металлического корпуса, крышки, одного или двух кранов для воды, индикаторов, сигнальных лампочек и ТЭНа. Кроме того, чаераздатчики включают в себя резервуар для заварки и емкость для воды. После того, как резервуар заполняется необходимым количеством чайной заварки, а бак — водой, можно приступать к приготовлению чая. Производительность некоторых чаераздатчиков достигает 120 стаканов чая в час. От перегрева ТЭН защищает специальная контрольная система, которая при отсутствии воды в баке отключает аппарат. Кофераздатчики работают по такому же принципу. Профессиональные чае- и кофераздатчики могут поддерживать приготовленный напиток в горячем состоянии при наличии такой опции.
Кипятильник 2.0 | Компьютерра
Николай Маслухин
29 октября 2014
Большинство электрических чайников работают по очень энергозатратной схеме: чтобы, например, вскипятить чашку чая, нужно налить воды в большем количестве – то есть заметная часть энергии уходит впустую. По подсчетам авторов сегодняшнего концепта, такой «холостой» энергии, собранной от чайников за сутки, хватило бы, чтобы все фонари Лондона светили целую ночь. Решение проблемы предложили дизайнеры Нильс Чуди (Nils Chudy) и Жасмина Грейс (Jasmina Grase) из Нидерландов, разработавшие индукционный кипятильник MIITO. Главная задача устройства — поменять привычки людей и способствовать более экономному и бережному отношению к энергии.
Кипятильник MIITO состоит из индукционной базы и нагревательного стержня. На базу помещается емкость любых размеров с любой жидкостью (от воды до супа), а после в жидкость погружается стержень. Система активируется автоматически и начинает нагревать содержимое. Так же автоматически она распознает, когда жидкость кипит и переходит в режим ожидания. После того, как пользователь забирает емкость и устанавливает стержень на базу, MIITO выключается.
Помимо явной экономии энергии у MIITO есть еще пара очевидных плюсов – легкий уход (никакой накипи) и тихая работа.
В настоящее время Miito представляет собой лишь прототип устройства. Однако изобретение уже удостоилось национальной голландской премии James Dyson Award 2014 и было представлено на выставке работ выпускников Академии дизайна Эйндховена.
Комментарии
Mogilevtorgtehnika — Mogilevtorgtehnika
Кипятильники периодического действия
Кипятильники периодического действия могут работать на любом виде обогрева, но выпускались промышленностью только для работы на твердом топливе.
В наливных кипятильниках периодического действия воду нагревают до кипения, после чего топку прекращают и начинают разбор кипятка. Кипятильник периодического действия состоит из зольника, двухстенной топки, межстенное пространство которой служит водонагревателем, и сборника кипятка; последний соединяется с помощью циркуляционных трубок с нагревателем.
В процессе нагревания вода непрерывно движется по циркуляционным трубкам между сборником воды и водонагревателем. Происходит это за счет разности плотности воды, имеющей различную температуру. Как только вода нагреется до кипения по всему объему, кипяток можно разбирать, прекратив топку кипятильника. В нижней части сборника воды установлен водоразборный кран.
Принципиальные схемы кипятильниковКипятильники непрерывного действия
Кипятильники непрерывного действия на любом виде обогрева работают по одному и тому же принципу и различаются производительностью, размерами и конструкцией теплогенерирующих устройств; последняя зависит от вида энергоносителя.
Кипятильник имеет следующие основные части: питательную коробку, водонагреватель с переливной трубой и сборник кипятка. Кипятильники снабжены крышкой, которая надевается на укрепленный в корпусе болт и завинчивается специальной гайкой. В сборнике кипятка над переливной трубой установлен отражатель, направляющий капельки кипятка, выбрасываемые из переливной трубы, в сборник. В нижней части сборника кипятка находится водоразборный кран, в верхней — патрубок (отверстие) для соединения сборника кипятка с питательной коробкой. В питательной коробке установлена сигнальная трубка, верхний конец которой выведен выше уровня воды, а нижний присоединяется разрывом к канализации. На подводящей водопроводной трубе установлен запорный вентиль для отключения кипятильника от водопроводной сети при его ремонте, а также в ночное время.
Работа кипятильников непрерывного действия основана на том, что уровень воды сообщающихся сосудах, одним из которых является питательная коробка, другим — водонагреватель с переливной трубой, всегда одинаковый.
Вода из городского водопровода или водонапорного бака поступает по трубе через поплавковый клапан в питательную коробку, соединенную с подводящей водопроводной трубой. Поплавок обеспечивает автоматическое открывание клапана при понижении уровня воды в питательной коробке. Из питательной коробки по питательной трубе вода попадает в нижнюю часть водонагревателя. Здесь она нагревается, поднимается вверх, доводиться до кипения и по переливной трубе перебрасывается в сборник кипятка, из которого разбирается через водоразборный кран.
После перебрасывания кипятка в сборник уровень воды в переливной трубе понижается, одновременно понижается и уровень воды в питательной коробке. В результате поплавок опускается и питательный клапан автоматически открывает отверстие для прохода воды из водопровода в питательную коробку. Вода будет поступать до тех пор, пока уровень ее в питательной коробке и в переливной трубе не достигнет заданного, тогда поплавок поднимется и клапан закроет отверстие для прохода воды из водопроводной трубы.
При монтаже кипятильника уровень воды в переливной трубе устанавливается на 0,06 — 0,08 метра ниже края переливной трубы, что гарантирует переброс в сборник кипятка только кипяченой воды. Если поплавок клапана отрегулирован так, что вода в переливной трубе находится на уровне кромки трубы, то в связи с расширением воды при нагревании в сборник кипятка будет попадать некипяченая вода. При установке поплавка питательного клапана ниже кромки переливной трубы (для кипятильников производительностью ниже кромки 25-50 кг/ч на 0,06 метра, а для кипятильников производительностью 100–200 кг/ч на 0,08 метра) в сборник кипятка будет перебрасываться только кипяченая вода.
При кипении воды часть ее превращается в пар, который намного легче воды. Обладая большой подъемной силой, пар захватывает с собой капельки кипящей воды и перебрасывает их через кромку переливной трубы. Таким образом кипяток попадает в сборник кипятка. Пар, образующийся при кипении воды, а также лишний кипяток (при отсутствии его разбора) через соединительный патрубок или отверстие в верхней части сборника кипятка (в кипятильниках, у которых питательная коробка находится в корпусе) поступает в питательную коробку, где происходит конденсация пара.
Уровень воды регулируется изменением положения поплавка питательного клапана. Для этого рычаг, на котором закреплен поплавок, поворачивают вверх или вниз в зависимости от уровня воды. Для поворота рычага необходимо отпустить контргайку на ниппеле и, установив ключ на основную гайку, повернуть ниппель, затем закрепить его в выбранном положении, затянув контргайку.
Технические характеристики кипятильников
Технические характеристики кипятильниковОт описанных выше кипятильников несколько отличаются кипятильники-водонагреватели. Эти аппараты могут использоваться для приготовления как кипятка, так и горячей воды. Для отбора горячей воды в верхней части водонагревателя предусмотрен водоразборный кран. Поскольку наиболее интенсивное выпадение солей и отложение накипи начинается при температуре воды выше 70 градусов, разбор горячей воды с температурой ниже 70 градусов (для целей горячего водоснабжения) уменьшает процесс образования накипи и увеличивает срок службы аппарата. Использование для горячего водоснабжения кипятка, получаемого в кипятильниках вызывает значительный перерасход тепла за счет расхода его на процесс частичного парообразование. Такие потери оправданы при использовании кипятка по прямому назначению, т.е. для приготовления горячих напитков, ибо за счет этих потерь гарантируется переброс в сборник кипятка только кипяченой воды.
Во всех кипятильниках, работающих на твердом топливе или горючем газе, водонагреватель выполняется в виде двухстенного цилиндрического сосуда, между стенками которого находится нагреваемая вода. Внутренняя часть водонагревателя служит камерой сгорания кипятильника. Дно камеры сгорания кипятильника, работающего на твердом топливе, представляет собой колосниковую решетку, под которой расположен зольник — цилиндрическая коробка. Зольник и камера сгорания воздуха под колосниковую решетку и удаления золы, дверца камеры сгорания — для загрузки топлива.
В камере сгорания газового кипятильника устанавливается газовая инжекционная горелка. Конструкция насадки горелки должна обеспечивать равномерное распределение пламени и получения факелов небольшой высоты. Первичный воздух подается через регулятор воздуха.
В электрических и паровых кипятильниках водонагреватель выполняется в виде коробки, в которой устанавливаются ТЭНы или паровой трубчатый нагреватель.
Кипятильники выполняются из оцинкованной или нержавеющей стали, иногда их наружная поверхность хромируется.
Электрические кипятильники КНЭ-25, КНЭ-50 и КНЭ-100
Кипятильник КНЭ-50
Электрические кипятильники КНЭ-25, КНЭ-50 и КНЭ-100 имеют аналогичную конструкцию и различаются только размерами, мощностью нагревательных элементов и производительностью.
Кипятильник КНЭ-50 состоит из сварного металлического корпуса, внутри которого находится питательная коробка, водонагреватель и сборник кипятка. Воздушный зазор между стенками водонагревателя и корпусом служит теплоизоляцией. Водонагреватель и сборник кипятка выполнены в виде единого цилиндрического сосуда и отделены от другого перегородкой, в которую вварена переливная труба. Дно водонагревателя представляет собой съемный фланец, на котором закреплены ТЭНы. Для слива воды из водонагревателя и питательной коробки во фланце имеется парубок с заглушкой. Сборник коробки снабжен отражателем.
Кипятильник полностью автоматизирован: в нем происходит автоматическое отключение ТЭНов от электрической сети при понижении уровня воды в питательной коробке ниже минимально допустимого (защита от «сухого хода») и заполнении сборника кипятка до максимального уровня, а также автоматическое включение ТЭНов при понижении уровня кипятка в сборнике до минимального уровня. При полной автоматизации сигнальная трубка кипятильника служит для слива воды в случае выхода из строя автоматики или неисправности поплавкового клапана.
Все пускорегулирующие устройства находятся в блоке автоматического пульта управления АПУ, укрепленном на корпусе кипятильника.
Электрическая схема кипятильниковАвтоматическая работа кипятильника обеспечивается электролитическим реле уровня РУ и магнитным пускателем П. Работой электролитического реле уровня РУ управляют три электрода, один из которых — электрод «сухого хода» Э1 — установлен на дне питательной коробки, два других — Э2 и Э3 — в сборнике кипятка: электрод верхнего уровня Э2 — на высоте, соответствующей максимальному уровню кипятка в сборнике, электрод нижнего уровня Э3 — на высоте, соответствующей минимальному уровню кипятка в сборнике. Один конец каждого электрода находится в регулируемом объеме, другой соединен с вторичной обмоткой трансформатора Тр. Все электроды представляют собой металлические стержни, установленные в стеклянных проходных электроизоляторах. При их установке должна быть обеспечена герметизация как между электроизолятором и корпусом питательной коробки или корпусом сборника кипятильника, так и между электродом и электроизолятором.
При включении выключателя Вк ток через трансформатор Тр поступает в цепь питания сигнальной лампы Л1, которая при этом загорается, и в цепь питания электрического реле РУ, замыкающие контакты которого замыкают цепь катушки магнитного пускателя П.
Если уровень воды в питательной коробке находится на уровне электрода Э1 или выше его, цепь между этим электродом и корпусом кипятильника замкнута. Объясняется это тем, что вода, находящаяся между ними, не будучи дистиллированной, содержит то или иное количество растворенных солей и поэтому является электролитом, т. е. проводником электрического тока. Обладающим незначительным электрическим сопротивлением. В этом случае электрическое реле РУ окажется под напряжением и его замыкающие контакты замкнут цепь питания катушки магнитного пускателя П, который включит через свои замыкающие контакты ТЭНы и сигнальную лампу Л2. Размыкающий контакт П магнитного пускателя одновременно разомкнет цепь питания электрода Э3. Это необходимо для того, чтобы при заключение сборника кипятка до минимального уровня не произошло обесточивания катушки магнитного пускателя и отключения ТЭНов от сети. Электролитическое реле РУ может работать только при прохождения по обмоткам его магнита постоянного тока, поэтому питание этого реле осуществляется через выпрямители-диоиды.
Диод — электронная лампа с двумя электродами (анод, катод). Эмиттированные катодом электроны достигают анода только тогда, когда он заряжен положительно. При изменении полярности анода эмиттированные электроны не могут его достигнуть. Таким образом, диод обладает односторонней проводимостью, пропуская ток в одном направлении. Для того чтобы при изменении полярности питание электролитического реле РУ не прекращалось, в рассматриваемой схеме используются две пары диодов В1 — В3 и В2 — В4.
При отсутствии разбора кипятка во время работы кипятильника уровень воды в сборнике кипятильника достигнет максимального значения, соответствующего положению электрода Э2. В этом случае ток пройдет по цепи: вторичная обмотка трансформатора, электрод Э2, вода, корпус, резистор R. Одновременно ток будет продолжать проходить по параллельной цепи: вторичная обмотка трансформатора, электрод Э1, вода, корпус, обмотка электромагнита, реле РУ.
Ток в резисторе R возрастает, так как к нему окажутся подключенными две параллельно соединенные цепи. Напряжение в цепях упадет и окажется недостаточным для питания катушки магнита реле РУ, в результате магнитное поле уменьшится, якорь реле опустится, а замыкающие контакты реле РУ разомкнутся и обеспечат катушку магнитного пускателя П. Последняя через свои замыкающие контакты отключит питание ТЭНов и сигнальной лампы Л2, а через размыкающие подключит питание электрода Э3. Если уровень воды в сборнике кипятка опустится ниже электрода Э2, никакого изменения в цепи не произойдет, ибо напряжение посредством резистора будет продолжать поступать на две параллельные цепи: через реле РУ и электрод Э3. Когда уровень воды в сборнике кипятка упадет ниже электрода Э3, цепь, параллельная реле РУ, разомкнется, ток в резисторе уменьшится, а напряжение, подаваемое на катушку магнита реле РУ, возрастает, в результате чего якорь ее поднимется, питание катушки магнитного пускателя возобновится и ТЭНы кипятильника вновь включатся.
Электрические кипятильники ЭКГ-25, ЭКГ-50 и ЭКГ-100
Кипятильники представляет собой сосуд цилиндрической формы, состоящий из кожуха 1 и кипятильного сосуда 2, сборника кипятка 3, стакана-отражателя 4, питательного сосуда 5, поплавкового устройства 9, датчика сухого хода 21, крышки 7, автоматического пускового устройства (АПУ) 13, электрода верхнего уровня 22, электрода нижнего уровня 23.
Вода из водопровода поступает через трубу подающую 17, клапан 14 в питательную коробку 5. Питательный и кипятильный сосуды соединены между собой питательной трубкой 10, трубчатые электронагреватели (ТЭНы) 12, подключенные к электросети через блок управления, нагревают воду до кипения. Кипящая вода выбрасывается из кипятильного сосуда 2 в сборник кипятка по кольцевому каналу между стаканом-отражателем 4 кипятильного сосуда. Слив кипятка производится через кран 16.
Схема кипятильника ЭКГКожух 1 металлический сварной служит для создания тепло изоляционной воздушной прослойки. На кожухе установлена панель 15. Внутри кожуха под кипятильным сосудом расположено АПУ 13. Питательный сосуд 5 предназначен для поддержания постоянного уровня воды в кипятильном сосуде. Внутри питательного сосуда находится электрод сухого хода и поплавковое устройство. Трубки переливные 8, 11 предназначены для слива воды в канализацию в случае переполнения питательного сосуда. На дне кипятильного сосуда закреплены ТЭНы 12. Поплавковое устройство состоит из поплавка 9, рычага 20, клапана 14. Назначение поплавкового устройства — поддерживать определенный уровень воды в питательном сосуде. Поступление воды из водопровода должно прекращаться при достижении уровня воды над питательной трубкой на 59-74 мм выше, что соответствует достижению уровня воды в кипятильном сосуде ниже края на 50-65 мм. Стакан-отражатель 4 закреплен на кипятильном сосуде 2 замковым устройством. Сверху кипятильник закрыт крышкой 7 с ручкой 6.
Электрооборудование кипятильника состоит из нагревателей трубчатых (ТЭНов), встроенного автоматического пускового устройства (АПУ), электродов 21-23, сигнального устройства. АПУ состоит из блока управления кипятильником ВК1-03, переключателя ПВ2-16 для включения автоматического пускового устройства в сеть. В качестве датчиков верхнего и нижнего уровня кипятка используются электроды 22, 23. Сигнальное устройство состоит из светодиодов, смонтированных на кожухе кипятильника. Белая сигнальная лампа говорит о подаче напряжения на АПУ, зеленая — о наличии напряжения на ТЭНах. При включении переключателя напряжение подается на блок управления кипятильником и загорается белая сигнальная лампа. При отсутствии холодной воды в питательном сосуде электрод сухого хода 21 оголяется и напряжение с ТЭНов снимается, подогрев прекращается. При наличии воды в питательной коробке между электродом «сухого хода» S2 (21) и корпусом кипятильника возникает электрический контакт и включаются пусковые реле блока. Реле блока включают ТЭНы ЕК1-ЕКЗ и размыкает цепь электрода S3 (23) «нижний уровень кипятка». При достижении кипятком верхнего заданного уровня в сборнике кипятка образуется электрический контакт между электродом S4 (22) и корпусом кипятильника и отключаются реле блока и ТЭНы. Нормально закрытые контакты реле, замкнувшись, включают цепь электрода S3. При разборе кипятка электрод S4 оголяется, но так как цепь электрода S3 замкнута, реле остаются отключенными. Когда уровень воды в сборнике кипятка понижается до нижнего заданного уровня, оголяется электрод S3 и схема приходит в рабочее положение (включаются реле блока и ТЭНы начинается подогрев воды).
При отсутствии отбора кипяченой воды для повторного запуска кипятильника необходимо слить кипяченую воду до нижнего уровня.
Ассортимент кипятильников
Помимо кипятильников КНЭ-25, КНЭ-50, КНЭ-100, КНЭ-50/100 производства «Каскад» или «Дебис» г. Челябинск на рынке можно встретить и прочие марки кипятильников, ЭКН-50, ЭКН-100 производства ООО «Гомельтехмаш» г. Гомель, ЭКГ-10, ЭКГ-25, ЭКГ-50, ЭКГ-100 производства ОАО «Гомельторгмаш» г. Гомель, КЕНД-50, КЕНД-100 производства ЗАО «Концерн «Термаль» г. Нижний Новгород.
Электрокипятильники отечественного производстваДанные модели электрокипятильников непрерывного действия выполнено из нержавеющей стали. Для подключения к канализации и системе водоснабжения им требуется стационарное подключение, напряжение питающей сети 380 В.
Кроме отечественных кипятильников, на рынке появились и импортные модели кипятильников. Так, фирма «Anvil» (ЮАР) выпускает следующие виды кипятильников URS-0012, URS-0030, URS-1012, UBR-0012, UBR-0016 и другие.
Корпус данных кипятильников выполнен из нержавеющей стали, ручки выполнены из термоизоляционного материала, конструкция крана предотвращает каплеобразование. Кроме того, конструкция подобных кипятильников имеет терморегулятор, защиту от сухого хода (в моделях URS-1012 и URB-0012), индикатор уровня воды (модель URS-1012).
Габаритные размеры кипятильника Anvil URS-0012Широкий спектр современных кипятильников выпускают фирмы из Китая. Ниже приведен кипятильник фирмы PYHL модель KSY на 10 литров. Помимо этой модели, существую модели KSY-20, KSY-30, KSY-40.
Cовременный кипятильник от фирмы «PYHL» модель KSYКипятильник САМСОН КНЭ-17-01
/ Кипятильник САМСОН КНЭ-17-01
Производитель: Atesy Кипятильник САМСОН КНЭ-17-01предназначен для приготовления кипятка и поддержания необходимой температуры приготовленной кипяченой воды.

- Кипятильник состоит из двух основный модулей: генератора кипятка и накопителя
- Генератор кипятка, кипячение воды до 100°С
- Автоматическое поддержание установленной температуры в накопителе кипятка
- Каплесборник исключает попадание кипятка на столешницу
- Цифровая индикация температуры кипятка
Диапазон регулировки температуры в накопителе, °С | 80-99 |
Максимальная производительность кипятка, чашек/ч | 210 |
Мощность нагревательного элемента генератора кипятка, кВт | 3,0 |
Мощность нагревательного элемента накопителя, кВт | 1,0 |
- Производитель
- Atesy
- Напряжение
- 220/230 В
- Номинальное электропотребление, Квт
- 3,2
- Объем варочного сосуда/чаши/дежи, л
- 17
- Вес нетто, кг
- 30
- Размеры без упаковки (Д*Г*В), мм
- 380*525*760
Цены на сайте носят ознакомительный характер и не являются публичной офертой. Окончательная цена может отличаться от указанной как в меньшую, так и в большую сторону, в зависимости от комплектации оборудования, личных предпочтений заказчика, действующих акций. Просим уточнять цены на продукцию у наших менеджеров.
Котел
| инженерия | Britannica
бойлер , также называемый парогенератором , устройство, предназначенное для преобразования жидкости в пар. В обычной паровой электростанции котел состоит из топки, в которой сжигается топливо, поверхностей для передачи тепла от продуктов сгорания воде и пространства, где может образовываться и собираться пар. Обычный котел имеет топку, которая сжигает ископаемое топливо или, в некоторых установках, отработанное топливо. Ядерный реактор также может служить источником тепла для производства пара под давлением.
Котлы были построены еще в I веке нашей эры героем Александрии, но использовались только в качестве игрушек. Лишь в XVII веке возможности пара для практической работы серьезно рассматривались. Первый котел с предохранительным клапаном был разработан Дени Папеном из Франции в 1679 году; котлы были сделаны и использовались в Англии на рубеже 18 века. Ранние котлы были сделаны из кованого железа; по мере того как были реализованы преимущества высокого давления и температуры, производители обратились к стали.Современные котлы изготовлены из легированной стали, чтобы выдерживать высокое давление и чрезвычайно высокие температуры.
Большинство обычных паровых котлов делятся на жаротрубные или водотрубные. В жаротрубном типе вода окружает стальные трубы, по которым протекают горячие газы из топки. Образующийся пар собирается над уровнем воды в барабане цилиндрической формы. Предохранительный клапан установлен для выхода пара при давлении выше нормального рабочего давления; это устройство необходимо на всех котлах, потому что постоянное добавление тепла к воде в закрытом сосуде без средств отвода пара приводит к повышению давления и, в конечном итоге, к взрыву котла.Преимущество жаротрубных котлов заключается в простоте установки и эксплуатации. Они широко используются в небольших установках для обогрева зданий и обеспечения электроэнергией производственных процессов. Жаротрубные котлы используются и в паровозах.
В водотрубном котле вода находится внутри труб, а горячие топочные газы циркулируют вне труб. Когда в начале 20 века был разработан паровой турбогенератор, современные водотрубные котлы были разработаны в ответ на потребность в большом количестве пара при давлениях и температурах, намного превышающих те, которые возможны для жаротрубных котлов.Трубки находятся вне парового барабана, который не имеет поверхности нагрева и намного меньше, чем в жаротрубном котле. По этой причине барабан водотрубного котла лучше выдерживает более высокие давления и температуры. Водотрубные котлы самых разных размеров и конструкций используются на кораблях и заводах. Экспресс-котел оборудован небольшими водяными трубками для быстрого образования пара. Для испарительного котла может не требоваться паровой барабан, потому что трубы работают при таких высоких температурах, что подаваемая вода превращается в пар и перегревается перед тем, как покинуть трубы. Самые большие агрегаты находятся на центральных станциях коммунального хозяйства. Установки значительного размера используются на сталелитейных, бумажных, нефтеперерабатывающих, химических и других крупных производственных предприятиях.
ОСНОВНЫХ КОМПОНЕНТОВ КОТЛА | Каталог котлов
Котлы являются частью системы водяного отопления. Гидравлические системы используют воду для передачи тепла распределительному источнику, например радиатору, для обогрева дома.Гидравлические системы могут нагреваться с помощью горячей воды или пара, в зависимости от типа используемого котла. Котел — это часть системы, которая нагревает распределяемую воду. Ключевые элементы котла включают горелку, камеру сгорания, теплообменник, выхлопную трубу и органы управления. Аксессуары котла, включая экономайзер дымовых газов, также обычно используются в качестве эффективного метода рекуперации тепла из котла.
Ключевые компоненты котлов: —
- Горелка — Горелка — это компонент котла, который обеспечивает тепло для нагрева воды в системе.Используемое топливо может быть природным газом или нефтью.
- Теплообменник — Теплообменник котла позволяет теплу от горелки нагреть воду в системе. Работа теплообменника заключается в передаче тепла от горелки к воде без прямого контакта с водой. Это похоже на кипячение воды в кастрюле.
- Линии подачи — В системах водяного отопления используются трубопроводы для подачи нагретой воды или пара к точкам распределения, а линии подачи — это трубы, по которым горячая вода или пар распределяются по распределителю.
- Обратные линии — Когда вода охлаждается или пар остывает и снова меняет свое состояние на воду, обратные линии возвращают эту воду в котел для повторного нагрева.
- Топка — Топка — это место, где топливо системы встречается с воздухом, создавая пламя.
- Огнеупорный материал — Огнеупорный материал на самом деле относится к огнеупорным материалам, которые используются для заполнения любых зазоров и / или отверстий, которые могут быть вокруг топки — это помогает обеспечить сохранение огня в топке.
- Циркуляционные насосы — Циркуляционные насосы нагнетают горячую воду или пар из системы к распределителям тепла в наших домах.
- Деаэраторы / конденсаторы — Деаэраторные и конденсаторные баки используются только в системах паровых котлов, а не при кипении горячей воды и горячего масла, потому что здесь жидкость всегда находится в жидкой форме. Конструкция этих двух типов танков практически идентична, но, как следует из названия, они используются для разных целей.
В этой форме резервуара используются два основных принципа: термический и вакуумный.Это зависит от того, какой тип котла используется. К каждому принципу также предъявляются различные требования к конструкции насоса.
Термо принципРезервуар, работающий по термическому принципу, связан с атмосферой. Эта конструкция обычно используется на небольших предприятиях. Здесь пар используется для поддержания температуры воды в резервуаре около 105 ° C, что удаляет воздух из воды.
Принцип вакуумаЗдесь эжекторный насос используется для создания вакуума в резервуаре.Это приводит к тому, что вода в резервуаре начинает закипать из-за низкой температуры, что, в свою очередь, удаляет воздух из воды. Этот принцип обычно используется для паровых турбин.
- Экономайзер
Исторически экономайзеры использовались только на крупных электростанциях. Однако потребность в более эффективных котлах в промышленности и судостроении означает, что экономайзеры стали гораздо более распространенным явлением. Экономайзер — это теплообменник, который размещается в выхлопе котла или в выхлопной воронке главного двигателя корабля.
Требования к насосу сильно различаются в зависимости от того, где установлен экономайзер.
- Перегреватель
Является составной частью котла и размещается на пути выхода горячих дымовых газов из топки. Тепло, рекуперированное из дымовых газов, используется для перегрева пара перед входом в турбину (то есть в первичный двигатель). Его основная цель — повысить температуру насыщенного пара без повышения его давления.
В котлах, работающих на природном газе, используется один из двух типов горелок: атмосферные горелки, также называемые горелками с естественной тягой, и горелки с наддувом, также называемые механическими горелками.Из-за более строгих требований к качеству воздуха горелки с низким уровнем выбросов NOx и горелки с предварительным смешиванием становятся все более распространенными и даже необходимыми в некоторых регионах. Обеспечивая эффективное смешивание воздуха и топлива при его поступлении в горелку, эти типы горелок могут гарантировать снижение выбросов NOx.
Камера сгорания, обычно сделанная из чугуна или стали, вмещает горелки и процесс горения. Температура внутри камеры сгорания может очень быстро достигать нескольких сотен градусов.
Теплообменники могут быть изготовлены из чугуна, стальных трубных пучков или, в случае некоторых небольших котлов, из меди или стали, плакированной медью.
Дымоход — это трубопровод, по которому горячие газы сгорания отводятся от котла наружу. Обычно этот трубопровод изготавливается из стали, но в случае конденсационных котлов он должен быть изготовлен из нержавеющей стали для обработки коррозионного конденсата. Еще одно соображение заключается в том, будет ли выхлопная труба находиться под положительным или отрицательным давлением. Это может определить, как должны быть герметизированы стыки выхлопной трубы.
Средства управления котлом помогают производить горячую воду или пар регулируемым, эффективным и безопасным способом.Органы управления горением и работой регулируют скорость использования топлива для удовлетворения спроса. Главный рабочий орган управления контролирует температуру горячей воды или давление пара и отправляет сигнал для управления скоростью горения, скоростью, с которой топливо и воздух поступают в горелку. Обычные последовательности розжига горелки включают в себя включение / выключение, высокое / низкое / выключенное состояние и плавное регулирование.
Средства безопасности котла включают средства управления высоким давлением и температурой, высоким и низким давлением газа / масла, а также средства контроля высокого и низкого уровня воды и контроля пламени. Эти средства управления считаются мерами безопасности или ограничениями, которые разрывают электрическую цепь, чтобы предотвратить возгорание котла.Например, если давление в котле превышает настройку предельного давления, топливный клапан закрывается, чтобы предотвратить небезопасное состояние высокого давления. Цепь безопасности системы контроля пламени обычно включает в себя переключающие контакты для отсечки низкого уровня воды, высоких пределов, переключатели подачи воздуха, резервные средства управления безопасностью и работой, а также датчики пламени. Датчики пламени часто состоят из стержней пламени и ультрафиолетовых или инфракрасных сканеров для контроля состояния пламени и отключения горелки в случае отсутствия воспламенения или другого небезопасного состояния.Органы управления защитой от пламени запрограммированы на управление горелкой и ее циклическое переключение между этапами работы.
Что такое бойлер? | Компоненты и применение
Что такое бойлер?Определение котла
Котлы определяются как
« Котел — это закрытый сосуд , в котором вода или другая жидкость нагревается, пар или пар, пар перегревается или любое их сочетание, под давлением или в вакууме, для использования вне себя, путем прямого приложения энергии от сжигания топлива , электричества или ядерной энергии.«
Котел является основной частью глобальной системы отопления на электростанциях. ”
Типы котлов и классификации котлов:Существуют следующие типы котлов:
1.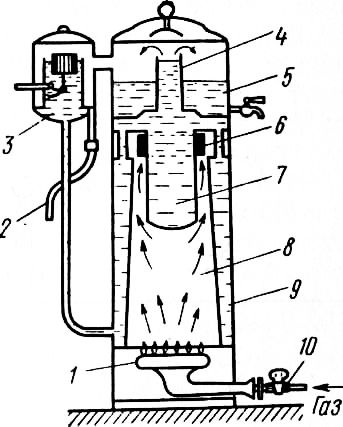
- Котел с естественной циркуляцией
- Котел с принудительной циркуляцией
- Мобильный котел
- Стационарный котел
- Однобарабанный котел
- Многобарабанный котел
- Котел с принудительной засухой
- Котел с естественной засухой
- Котел с одной топкой
- Котел с двумя топками
- Котел на твердом топливе
- Котел на жидком топливе
- Котел на газе
Котельные печи, совместимые со следующими видами топлива
Котельное твердое топливо
Котельное жидкое топливо
Котельное газообразное топливо
- СНГ
- СПГ
- PNG может использоваться для сжигания конкретная цель.
Конструкция котла состоит из 3 основных компонентов —
- Система питательной воды
- Паровая система
- Топливная система
Вода, которая преобразуется в пар с помощью системы паровых котлов, называемой питательной водой, и системы, которая регулирует питательную воду, называется системой питательной воды.
В котлах есть два типа систем питательной воды:
- Открытая система подачи
- Закрытая система подачи
Есть два основных источника питательной воды:
- Конденсированный пар, возвращаемый из технологических процессов
- Сырая вода организованные извне процессов котельной (называемые: подпиточная вода)
Паровая система — это своего рода основная система управления процессом котла. Steam Systems отвечает за сбор и контроль всего производимого пара в процессе.
Паровые системы направляют пар, образующийся в процессе, к месту использования по трубам (система трубопроводов). На протяжении всего процесса давление пара контролируется и регулируется с помощью таких частей системы котла, как клапаны, манометры пара и т. Д.
3.Топливная система котлаЗаправка топливом — это сердце процесса котла. Топливная система состоит из всех необходимых компонентов и оборудования для подачи топлива для выработки необходимого тепла. Оборудование, необходимое в топливной системе, зависит от типа топлива, используемого в системе.
Также читайте: Котлы в корпусе
Применение котловКотлы имеют очень широкое применение в различных отраслях промышленности, таких как
Индийский производитель котлов Компонент котла: сосуд под давлением Thermodyne проектирование, производство и поставка ISO 9001: 2008 сертифицированы паровые котлы , для таких процессов и некоторые другие тоже.
Thermodyne Engineering Systems может помочь вам сэкономить до 30% стоимости топлива за счет предоставления высокоэффективных котлов, консультаций по вопросам энергетики и индивидуальных решений в области отопления.
Экономия топлива важен не только для прибыли, но и для окружающей среды. Промышленность может рассчитывать на Thermodyne, потому что мы верим в повышение энергоэффективности.
Ресурсы, связанные с котломТакже подпишитесь на наш канал Youtube: Thermodyne Boilers
Инфографика, относящаяся к котлу
Boiler Vs.Инфографика печи Часто задаваемые вопросы по применению котла и компонентам Каковы функции котла?Паровой котел подает сухой и насыщенный пар при требуемом давлении.
Какие области применения котла? Есть несколько применений для котлов в промышленности —
1. В рабочих паровых машинах.
2. В действующей паровой турбине.
3. Производственные процессы в химическом машиностроении.
4. Для производства горячая вода должна подаваться в помещения в очень холодных зонах.
5. На тепловых электростанциях.
Источником тепла для котла является сжигание различных видов топлива, таких как древесина, уголь, масло, рисовая шелуха или природный газ. Иногда ядерное деление также используется в качестве источника тепла для выработки пара из котельной системы.
Сколько стоит новый промышленный котел?Стоимость котла зависит от нескольких факторов, таких как потребность в тепле, размер и индийский сертификат соответствия котельным нормам.
Каков средний срок службы котла? г Средний срок службы промышленного котла — до 15 лет.Если ваш котел приближается к этому возрастному рубежу, вам следует начать поиск новой котельной системы для вашей тепловой станции. Вы можете увеличить этот период времени, если будете проводить ежегодное техническое обслуживание вовремя и постоянно поддерживать свой котел в идеальном состоянии.
Описание котла —
Котел — это закрытый сосуд, который нагревает жидкость, например воду, для создания пара или испаренной формы жидкости.После этого пар или горячая вода циркулируют по трубопроводу для передачи тепла для различных целей, включая нагрев, выработку электроэнергии и другие процессы. Котлы и связанные с ними системы являются эффективными системами теплообмена, но при неправильном управлении и эксплуатации они могут быть небезопасными.
Промышленный котел, используемый в больницах и здравоохранении для следующих применений —
— Стерилизация операционной.
-Стерилизация оборудования.
-Производство чистого пара.
-Обеспечение отопления здания.
-Увлажнение для отделений неотложной помощи.
-Промышленная прачечная.
-Пищевые продукты.
Котел — обзор | Темы ScienceDirect
Сравнение промышленных и коммунальных котлов
Большая часть угля, потребляемого в США, используется для выработки электроэнергии, но также используется значительное количество небольших котлов, не генерирующих электричество, которые сжигают уголь. Поэтому следует краткое обсуждение промышленных котлов и сравнение с котлами для коммунальных служб.
Коммунальные котлы и промышленные котлы очень разные. Основные различия между коммунальным котлом и промышленным котлом:
- •
Размер котла
- •
Применение пара, вырабатываемого котлом
- •
Конструкция котел
- •
Разнообразие видов топлива, включая использование побочного топлива
- •
Глобальная конкуренция за создаваемую продукцию
Для сравнения, типовой котел для коммунальных предприятий намного больше чем средний промышленный котел.В результате, промышленные котлы не получают такой экономии от масштаба, как котлы для коммунальных предприятий, и в случае сокращения выбросов должны платить больше за удаление определенного количества выбросов.
Размер и количество блоков
Средний новый промышленный котел значительно меньше, чем коммунальный котел. Типичный водогрейный котел производит около 3,5 миллионов фунтов пара в час (приблизительно 400 МВт), в то время как типичный промышленный котел производит около 100 000 фунтов пара в час.Многие промышленные котлы рассчитаны на менее 250 000 фунтов пара / час, но могут быть рассчитаны на более чем 1 миллион фунтов пара / час [6, 8]. Небольших промышленных котлов значительно больше, чем крупных котлов для коммунальных предприятий, и промышленные котлы приспособлены для удовлетворения потребностей и ограничений самых разных производственных процессов. CIBO (Совет владельцев промышленных котлов) сообщает, что совокупность промышленных котлов и технологических нагревателей (всего, а не только угольных агрегатов) состоит из 70 000 и 15 000 единиц, соответственно, размером от 10 000 до 1 400 000 фунтов пара / ч, с средний размер установки — 100 000 фунтов пара / час [9, 10].
Для сравнения, существует около 4000 энергоблоков, из которых около 1250 котлов используют обычную технологию сжигания угля (Таблица 5. 1), а еще 67 котлов с псевдоожиженным слоем для коммунальных предприятий [11]. Это дополнительно проиллюстрировано на Рисунке 5.4, где показано распределение котлов, работающих на угле, по мощности для обычных коммунальных, обычных, не коммунальных, FBC коммунальных и не коммунальных котлов FBC [11]. EPA определяет некоммунальный котел как котел, основным продуктом которого является не электричество, а пар.Некоторые из котлов, не предназначенных для коммунальных служб (как обычные, так и FBC), являются когенерационными установками, поскольку они производят как пар, так и электричество.
Таблица 5.1. Распределение коммунальных котлов по традиционным технологиям сжигания угля
Технология сжигания | Количество котлов | Мощность (в мегаваттном эквиваленте) | ||
---|---|---|---|---|
Котлы на пылеугольном топливе | 1,068 | 94 | 1,077 | |
Циклоны | 89 | 25,727 | ||
Всего | 1,251 | 320,839 | 04.![]() Применение параПромышленные котлы используются во многих отраслях промышленности для самых разных целей, и основным продуктом является технологический пар. Работа промышленного котла может значительно варьироваться в зависимости от сезона, дня и даже часа, в зависимости от потребности в паре. А вот коммунальный котел вырабатывает пар с единственной целью — приводить в действие турбины для производства электроэнергии.Типичный водогрейный котел — например, агрегат с базовой нагрузкой — работает с постоянной скоростью, близкой к максимальной, из-за постоянной потребности в паре. Колебания нагрузки от котлов энергосистемы общего пользования, которые работают в соответствии с колебаниями нагрузки коммунальных предприятий в течение дня или для сезонных пиковых нагрузок, то есть пиковых агрегатов, контролируются в большей степени, чем промышленные котлы, поскольку они могут сбалансировать свою нагрузку по всей электрической сети производства и распределения. Следовательно, коммунальные котлы, как правило, имеют более низкие эксплуатационные расходы, чем промышленные котлы, оборудованные аналогичным образом. Коммунальные блоки обычно имеют множество альтернативных вариантов резервного копирования на случай незапланированных отключений. Однако в промышленности редко бывает резервная система для производства пара из-за необходимости минимизировать затраты на производство пара. Следовательно, промышленные котлы обычно работают с коэффициентом надежности 98 процентов. Конструкция котлаКоммунальные котлы — это в основном устанавливаемые на месте установки, предназначенные для пара высокого давления и высокой температуры. Конструкция котла, мощность, давление пара и температура, среди других параметров, зависят от топлива и условий эксплуатации.Далее в этой главе подробно обсуждается влияние типа и характеристик угля на конструкцию котла. Две основные конструкции водотрубных котлов, выбранные коммунальными предприятиями США, — это подкритические котлы барабанного типа, рассчитанные на номинальное рабочее давление пара 1900 или 2600 фунтов на кв. ]. Парогенераторы и их вспомогательные компоненты имеют множество критериев проектирования, но важными вопросами являются эффективность, надежность / доступность и стоимость.Несмотря на то, что в эксплуатации находится несколько котлов со стоками и циклонами, новые конструкции в основном представляют собой агрегаты с угольной пылью и псевдоожиженным слоем. Промышленные котлы и встроенные в них системы сжигания широко различаются по своей конструкции и конструкции, включая производство пара низкого и высокого давления, разнообразие размеров, сборные котлы заводской сборки или устанавливаемые на месте установки, а также их способность сжигать широкий выбор видов топлива. Промышленные котлы состоят из комплектных и монтируемых на месте агрегатов различных типов котлов: водотрубных, пожарных, топочных, псевдоожиженного слоя, пылевидного угля и циклонных агрегатов.Доступны агрегаты в упаковке с производительностью примерно до 600 000 фунтов пара / час, но котлы производительностью более 250 000 фунтов пара / час обычно не могут быть доставлены по железной дороге, хотя они могут быть отправлены баржами или океанскими судами [6]. На промышленность по производству промышленных котлов влияет несколько факторов [7]:
Разнообразие видов топлива и глобальная конкуренция продуктовРазнообразие видов топлива и глобальная конкуренция продуктов являются в первую очередь представляют интерес для промышленного сектора, поэтому здесь они не рассматриваются подробно. В то время как электроэнергия продается на всей территории Соединенных Штатов в результате дерегулирования во многих штатах, электроэнергия не является глобальным продуктом (за исключением продаж электроэнергии в Мексику или Канаду), тогда как многие промышленные товары должны конкурировать с международными рынками.Разнообразие видов топлива влияет на коммунальные услуги, но не в такой степени, как на промышленных котельных. Уголь является самым дешевым доступным энергетическим сырьем и широко используется в электроэнергетике. Некоторые виды топлива сжигаются совместно с углем, например нефтяной кокс, шины и материалы из биомассы, но в котлах, работающих на угле, как правило, используется только уголь. Это может измениться в будущем, если будет принят закон, который требует, чтобы производители электроэнергии производили часть своей электроэнергии из возобновляемых источников энергии.С другой стороны, пользователи промышленных котлов заинтересованы в использовании более широкого разнообразия видов топлива, поскольку они испытывают большую нестабильность в доступности топлива и ценах. Примеры топлива для промышленных котлов (не включая) включают отходы угля, такие как битуминозные частицы и антрацитовый шлам, древесные отходы, жмых, варочный (черный) щелок, доменный газ, нефтяной кокс, нефтеперерабатывающий газ, отходящий газ окиси углерода, скорлупа арахиса, пальмовые листья, рисовая шелуха, животные жиры и белки, а также навоз и подстилка [6, 9, 12–15]. Корпуса котлов | Спиракс СаркоЛанкаширский котелСэр Уильям Фэйрберн разработал котел в Ланкашире в 1844 году на основе однотрубного котла Корнуолла Тревитика. Хотя всего несколько из них все еще находятся в эксплуатации, они были повсеместными и были предшественниками сложных и высокоэффективных котлов, используемых сегодня. Ланкаширский котел состоял из большого стального кожуха, обычно длиной от 5 до 9 м, через который проходили две топочные трубы с большим диаметром отверстия, называемые дымоходами.Часть каждого дымохода была гофрирована, чтобы компенсировать расширение при нагревании котла и предотвратить разрушение под давлением. На входе в каждый дымоход, в передней части котла, была установлена топка. Обычно печь предназначена для сжигания угля с ручным или автоматическим топлением. Горячие газообразные продукты сгорания выходили из топки по гофрированным дымоходам большого диаметра. Тепло от горячих дымовых газов передавалось воде, окружающей эти дымоходы. Котел имел кирпичную кладку, которая была устроена так, чтобы отводить горячие газы, выходящие из дымоходов, вниз и под котел, передавая тепло через нижнюю часть кожуха котла и, во-вторых, обратно по бокам котла перед выходом через дымовую трубу. . Эти два боковых канала встречаются в задней части котла и ведут в дымоход. Эти проходы были попыткой извлечь максимальное количество энергии из горячих продуктовых газов до того, как они будут выпущены в атмосферу. Позже эффективность была улучшена за счет добавления экономайзера. Газовый поток после третьего прохода прошел через экономайзер в дымоход. Экономайзер нагревает питательную воду и приводит к повышению теплового КПД. Одним из недостатков котла в Ланкашире было то, что многократное нагревание и охлаждение котла с происходящим в результате расширением и сжатием нарушало кладку кирпичной кладки и воздуховоды. Это привело к проникновению воздуха, что нарушило тягу печи. Эти котлы сейчас было бы очень дорого производить из-за большого количества используемого материала и трудозатрат, необходимых для строительства кирпичной кладки. Большой размер и водоемкость этих котлов имели ряд существенных преимуществ:
Эта низкая скорость означала, что даже с водой, содержащей высокие концентрации общего растворенного твердого вещества (TDS), было много возможностей для разделения пара и частиц воды и подачи сухого пара на установку. По мере того, как системы управления, материалы и технологии производства стали более сложными, надежными и рентабельными, конструкция котельной изменилась. Обзор проблем и решений для компонентов, подверженных возгоранию котловОсновными проблемами, возникающими в котлах, являются агломерация, высокотемпературная коррозия, шлакообразование, загрязнение, щелочное охрупчивание и усталостное разрушение. АгломерацияПроблема агломерации в основном возникает у очага пожара в котлах с псевдоожиженным слоем [27].Агломерация — это в основном проблема золы в котлах, работающих на биомассе. Зола, образующаяся из топливных агломератов с высоким содержанием серы и с низким содержанием золы, если они длительное время склонны к сульфатированию. Степень сульфатирования зависит как от времени, так и от температуры. Он изменяется пропорционально увеличению температуры и времени. Зола агломерируется, когда на месторождении образуется 50–60% или более количества сульфата кальция и Ca – K-силикатов. Петлевые уплотнения и зола более склонны к агломерации, чем летучая зола.Летучая зола образует более слабые отложения, чем зола, но все они со временем агломерируются [28]. Скорость агломерации увеличивается при повышении температуры от 850 до 950 ° C. Агломерация происходит сначала из-за карбонизации, а затем из-за сульфатации при более низких температурах [29]. Склонность золы к агломерации увеличивается с увеличением содержания железа или щелочного металла [27]. Сильвеннойнен сообщил, что смесь силикатов щелочных металлов с низкой температурой плавления образуется, когда богатая щелочами зола реагирует со свободным кварцем, который присутствует в песке, и эта смесь образует адгезионную связь между частицами псевдоожиженного слоя, что приводит к агломерации [30].Легкоплавкие хлориды щелочных металлов могут увеличивать липкость частиц летучей золы и увеличивать скорость осаждения золы на трубах пароперегревателя. Осажденные хлориды щелочных металлов могут увеличивать скорость коррозии пароперегревателей, поскольку хлориды могут образовывать эвтектики с низкой температурой плавления и вызывать агрессивную жидкофазную коррозию [31]. Возможные решения для агломерацииДобавки, такие как сера, каолин и сульфат аммиака, могут использоваться для уменьшения агломерации на трубах пароперегревателя.Дэвидссон сообщил, что если каолин добавить к материалу слоя перед сжиганием, то это наверняка решит проблему агломерации. В одном из исследований сообщалось, что температуры агломерации соломы и коры пшеницы были определены как 739 и 988 ° C соответственно [32]. Однако, если в слой добавлен каолин, начальные температуры агломерации слоя увеличиваются до 886 и 1000 ° C соответственно. Когда в слой добавляли каолин, состав покрытий изменялся в сторону более высоких температур плавления, в основном из-за пониженного содержания калия, поскольку каолин поглощает основные виды калия.Однако коммерческое использование каолина против отложений обходится дорого [29]. Проблему также можно решить, если вместо каолина добавить сульфат аммония или серу [28,29,30,31,32,33]. Реакции между добавками, такими как сера и хлориды щелочных металлов, образуют сульфаты щелочных металлов, а хлор выделяется в газовую фазу в виде HCl. Сульфаты щелочных металлов имеют более высокие температуры плавления, чем соответствующие хлориды щелочных металлов, и поэтому будут иметь меньшую тенденцию к прилипанию к перегревателям в виде отложений.Таким образом, можно минимизировать образование отложений и коррозионный потенциал перегревателей [31]. ШлакообразованиеВ зависимости от различных методов отложения золы на поверхности нагрева наблюдаются два типа отложения золы, а именно шлакование и засорение. Шлакование и засорение котла — два основных фактора, отрицательно влияющих на эффективность котлов [34, 35]. Эти проблемы в основном влияют на возгорание котла. Эти два процесса приводят к частому отключению сажеобдувщиков.Шлак — это расплавленная зола и негорючий побочный продукт, который остается в виде остатка после сжигания угля. Шлакование — это отложение частично расплавленных остатков на стенках или поверхностях печи, подверженных тепловому излучению. Это происходит в самых горячих частях котла. Шлак образуется, когда частицы расплавленной размягченной золы не охлаждаются до твердого состояния, когда они достигают горячей поверхности [36, 37]. Это снижает поглощение тепла в топке, увеличивает температуру газа на выходе из топки, снижает КПД и готовность котла из-за незапланированных остановов, приводящих к потерям в работе [37].Установлено, что серьезное шлакообразование происходит в основном на стенках печи. Дымовые газы в центре топки заставляют ее отклоняться с двух других сторон стенок; это приводит к попаданию пламени пылевидного угля на боковые стенки печи. Благодаря этому на боковых стенках происходит зашлаковывание. Это приводит к небольшому зашлаковыванию областей арочной горелки, а также областей передней и задней стенок нижней печи [38]. Возможные решения по шлакованиюПроцесс шлакования полностью предотвратить невозможно.Однако его можно уменьшить, используя несколько способов, например, обеспечение равномерного распределения тепла во избежание локальных температур. Его также можно свести к минимуму путем добавления кондиционера к частицам расплавленной золы, переносимым дымовым газом, который поглощается этими расплавленными частицами и создает эффект зародышеобразования, когда эти частицы охлаждаются, заставляя их затвердевать более быстро, тем самым предотвращая образование отложений или в значительно большем количестве рыхлых депозитов [39]. Образование отложений на конвенционной поверхности можно уменьшить, поддерживая соответствующую температуру на выходе из печи, а также удаляя достаточное количество тепла.Помимо вышеуказанных решений, соотношение высоты, ширины и глубины печи должно быть пропорциональным, чтобы ограничить возможность воздействия частиц золы на поверхность печи [40]. ОбрастаниеОбрастание — это образование отложений спеченной золы на обычных поверхностях нагрева, таких как подогреватели и пароперегреватели [40], которые не подвергаются прямому воздействию излучения пламени. Это происходит при охлаждении взвешенной золы-уноса вместе с дымовыми газами [41]. Чрезмерное загрязнение может привести к повышению температуры газа и скорости осаждения, что приводит к постоянному изменению условий в котле и, следовательно, к снижению его эффективности [42].Изменение температуры для высокотемпературного обрастания находится в диапазоне от 900 до 1300 ° C, а для низкотемпературного загрязнения — от 300 до 900 ° C [38]. Загрязнение котлов происходит из-за снижения теплопередачи, что в дальнейшем приводит к значительным потерям перегрева и температуры горячих дымовых газов [43, 44]. Основными факторами, которые приводят к удалению отложений, являются прочность отложений и адгезионная связь между теплопередающей поверхностью и отложением золы. Процесс удаления отложений включает разрушение матрицы отложений и / или разрыв клеевого соединения.В котлах угольных электростанций возникает множество производственных проблем из-за обрастания. Отсутствие своевременного обслуживания и очистки также может привести к засорению [45]. Возможные решения для загрязненияПостоянных решений для устранения загрязнения не существует, но есть определенные технологии, которые могут помочь свести к минимуму проблемы отложений в котлах. Некоторые из этих процессов — это технология импульсной детонационной волны, интеллектуальный нагнетатель сажи, технология химической обработки, противообрастающие покрытия и т. Д. [35].Эти технологии могут помочь в некоторой степени уменьшить проблему загрязнения труб котла в зависимости от их эффективности. Заключительные замечания и рекомендации могут быть составлены в соответствии с показанными результатами. Сажеобдувочные машины могут использоваться для очистки нагретой плоскости котлов во время работы с продувочной средой в виде воды и пара. Вода или пар направляются на осадок через сопло, что приводит к его разрушению и коррозии. Есть некоторые инструменты для прогнозирования воздействия золы, такие как AshProSM, которые используются для анализа ситуации с зашлаковыванием и загрязнением угольных котлов.Интегрированный котел с расчетным гидродинамическим моделированием (CFD) с моделями воздействия золы используется для определения образования, переноса, осаждения, роста отложений и прочности [36]. Некоторые из других методов, которые используются для предотвращения загрязнения в котлах, включают влажную предварительную обработку энергетического котла, работающего на буром угле, с использованием минеральных добавок в угольном коммунальном котле, мониторинг тенденций загрязнения, технология химической обработки: нацелена на печь технология впрыска (TIFI) и др.[44]. Каустическое охрупчиваниеВ котлах происходит процесс каустического охрупчивания, который приводит к образованию трещин на склепанных пластинах из низкоуглеродистой стали. Температура колеблется от 200 до 250 ° C, что в дальнейшем приводит к отложению концентрированного гидроксида на водной стороне котла [46]. Мы также можем объяснить каустическое охрупчивание как явление, при котором котел становится хрупким из-за накопления каустической соды [47]. Щелочное охрупчивание также известно как коррозионное растрескивание под напряжением [46].Едкое охрупчивание вызывается наличием каустической соды в питательной воде котла, которая находится в прямом контакте со сталью и барабанами котла [48]. В котле при испарении воды увеличивается концентрация карбоната натрия. Карбонат натрия используется для умягчения воды. известково-содовый процесс. Во время этого процесса есть вероятность, что некоторые частицы карбоната натрия могут остаться. Со временем концентрация карбоната натрия увеличивается, и он подвергается гидролизу с образованием гидроксида натрия.Когда концентрация гидроксида натрия увеличивается на определенную величину, вода становится щелочной. Эта щелочная вода проникает в мелкие трещинки внутренних стенок котла. Испарение этой воды приводит к постоянному увеличению количества гидроксида натрия в трубах котла. Этот гидроксид натрия разрушает железо, присутствующее в котлах, и растворяет его; таким образом, образуется феррат натрия, который в дальнейшем приводит к каустической хрупкости [49]. Возможные решения для каустической хрупкостиКаустическая хрупкость в котлах — естественный процесс, и его можно временно предотвратить путем добавления комбинации химикатов, состоящих из достаточного количества сульфата натрия в обычную котловую воду [50].Каустическое растрескивание происходит в растворах, где действует смешанный активный и пассивный контроль коррозии [51]. Мы можем предотвратить охрупчивание щелочью, добавив такие соединения, как сульфит натрия, танин, лигнин и фосфат, потому что он блокирует трещины, образованные проникновением щелочи [52]. Усталостное разрушениеСклонность материала к разрушению из-за непрерывного хрупкого растрескивания при повторяющихся переменных или циклических напряжениях с интенсивностью значительно ниже нормальной прочности известна как усталостное разрушение [53].Это может повлиять на подавляющее большинство материалов, в основном кристаллические твердые тела, такие как металлы и сплавы. Процесс утомления можно условно разделить на три этапа. Первый шаг — это инициация. Пересечение поверхности с полосами скольжения, образованными из-за образования и движения дислокаций, вызванных чрезмерным приложением напряжения, приводит к возникновению усталости. Затем наступает II этап — рост трещины. Усталостная трещина II стадии — это обязательно небольшая трещина, связанная с тонкими складками металла, вытесненными с поверхности.Эти щели известны как вторжения. Трещины могут развиваться и расти на границах раздела всех типов, а также могут расти на границах зерен. Последняя стадия — рост трещины Стадии III. Это наиболее важный аспект усталостного разрушения, который вызывается постепенным макроскопическим поворотом трещины в некристаллографическую плоскость [54]. На начальном этапе работы котла наблюдаются различные отказы труб, в том числе кратковременный перегрев, разрывы сварных швов, дефекты материала, разрушение из-за химического выброса, а иногда и усталостные разрушения.Усталостное разрушение вызывается высоким значением максимального предела прочности на растяжение, большим количеством вариаций приложенного напряжения, прикреплением коррозионных сварных швов, неправильной гибкостью, неправильной термообработкой, контуром сварных швов, большим количеством циклов приложенного напряжения и ограничением холодного изгиба до термического расширение [55]. Возможные решения при усталостном отказеУправление отказами труб котла важно, поскольку оно может помочь в сокращении вынужденных простоев, минимизировать риск отказов и, следовательно, повысить эксплуатационную готовность установки, а также надежность.Одну из наиболее важных причин выхода из строя трубы котла, то есть усталостного разрушения, можно предотвратить, следуя приведенным ниже мерам: избегать концентрации напряжений, уделять особое внимание деталям на этапе проектирования, чтобы убедиться, что циклические напряжения достаточно низки для достижения требуемую долговечность, используйте более прочные и более прочные материалы с высокой вязкостью разрушения и медленным ростом трещин, выбирайте хорошую отделку поверхности, отслеживайте изменения температуры, повышайте симметрию, решайте простоту конструкции и гарантируйте прочность, а также тщательное текущее обслуживание [56]. Высокотемпературная коррозияВысокотемпературная коррозия может быть определена как ускоренное окисление материалов, которое вызвано отложением солевой пленки при повышенных температурах у камина котла. Повышенная температура колеблется от 700 до 1300 ° C. К различным типам высокотемпературной коррозии относятся азотирование, хлорирование, науглероживание, окисление, сульфатирование, дымовые газы и коррозионные отложения. Плавленые сульфаты щелочных металлов осаждаются на горячие подложки в результате окисления металлических примесей, таких как сульфаты и ванадий в топливе [34]. Возможные решения для высокотемпературной коррозииa) Использование ингибиторовИнгибиторы коррозии — это вещества, которые при добавлении в окружающую среду в малых концентрациях снижают скорость коррозии металла [57]. Основными факторами, ответственными за ингибирование коррозии, являются состав жидкости, количество воды и режим потока. Мы используем ингибиторы в нефтедобывающей и перерабатывающей промышленности, потому что там они зарекомендовали себя как лучшее защитное средство от коррозии [58].Мы также можем назвать ингибиторы коррозии добавками к жидкости, окружающей металл. Выбор ингибиторов зависит от типа металла и условий окружающей среды [59]. В основном их можно разделить на два типа, такие как ингибиторы окружающей среды и ингибиторы межфазной границы. Кондиционеры окружающей среды или ингибиторы (поглотители) обладают способностью снижать коррозионную активность конкретного вещества путем улавливания (очистки) агрессивных веществ [59]. В ингибиторах межфазной границы процесс контроля коррозии осуществляется путем образования пленки на металле / окружающей среде [60]. Ингибиторы межфазной границы можно разделить на два подтипа, то есть жидкофазные ингибиторы и парофазные ингибиторы. Ингибиторы жидкой фазы — это те ингибиторы, которые классифицируются на основе их электрохимических реакций [58]. Ингибиторы паровой фазы — временные ингибиторы, которые используются для предотвращения коррозии; особенно в закрытых помещениях. Они безвредны для окружающей среды и не содержат вредных химических веществ, например нитратов. Они также имеют низкую стоимость, доступны по цене и служат долго, что дает надежные результаты [58,59,60]. Ингибиторы жидкой фазы можно разделить на три подтипа: анодные, катодные и смешанные ингибиторы. Анодные ингибиторы — это те ингибиторы, которые предотвращают коррозию, образуя защитный слой оксидной пленки на поверхности металла. Они также известны как пассиваторы, и эти ингибиторы изменяют анодные реакции в клетке [61]. Процесс контроля коррозии путем уменьшения скорости восстановления или осаждения отдельных участков катодной области (катодных рецепторов) называется катодными ингибиторами.Проще говоря, мы также можем описать катодные ингибиторы как химические соединения, которые могут снизить скорость коррозии металла или сплава при добавлении в определенную жидкость или газ [58,59,60,61,62]. Соединения, которые не являются ни анодными, ни катодными, то есть соединения, которые проявляют характеристики как анодных, так и катодных ингибиторов, называются смешанными ингибиторами. В среднем 80% органических соединений являются смешанными ингибиторами. Они защищают металл за счет физической адсорбции, хемосорбции и образования пленки.Они также уменьшают катодную и анодную реакции на работу [58, 59]. Катодные ингибиторы подразделяются на катодные отравляющие вещества и катодные осадители. Соединения, которые могут вызывать водородное охрупчивание и водородные пузыри из-за адсорбции водорода сталью, называются катодным ядом, а соединения, которые способствуют увеличению щелочности и осаждению нерастворимых соединений на металлической поверхности, называются катодными осадителями [58]. Смешанные ингибиторы также можно разделить на два подтипа: физические и химические ингибиторы.Физические ингибиторы — это те, которые физически адсорбируются и быстро взаимодействуют; однако их главный недостаток заключается в том, что они легко снимаются. В химических ингибиторах, поскольку идет химическая реакция, она замедляет процесс по сравнению с физическими ингибиторами [58]. б) Золь – гель покрытиеЗоль – гель покрытие — широко используемый метод защиты от коррозии. Он показал лучшую химическую стабильность, контроль окисления и повышенную коррозионную стойкость металлических подложек [63, 64].Это метод производства твердых материалов из небольших молекул. Он превращает мономеры в коллоидный раствор (золь), который действует как предшественник интегрированной сетки (или геля), состоящей либо из дискретных частиц, либо из сетчатых полимеров [65]. Золь – гель покрытие — это мокрый метод, который можно использовать для изготовления керамических и стеклообразных материалов. Нанесение золь-гелевого покрытия на металлы произошло сравнительно недавно и недостаточно исследовано [66]. Синтез гелей при комнатной температуре осуществляется в основном двумя способами.Первый шаг — это обычная реакция, которая происходит в природе, когда химические соединения кремнезема разбавляются водными растворами. Затем этот раствор конденсируется и приводит к образованию сетки кремнезема. Эта конденсация может происходить в различных водных растворах в зависимости от концентрации соли и pH. Вторая стадия — получение диоксида кремния из раствора, который соответствует химической реакции, подразумевающей алкоголяты металлов и воду в спиртовом растворителе [67]. Недостатком золь – гель технологии является высокая стоимость сырья (химикатов).Например, порошок MgO чистотой 98% доступен в небольших количествах по цене 32 доллара за кг. Этоксид магния, который является химическим субстратом для производства MgO, стоит около 210 долларов за кг. Во время сушки часто возникают трещины и большая усадка в объеме, поэтому керамисты по возможности избегают этого [68]. c) Изменяющаяся температура и давлениеТемпературу можно определить как сравнительную меру холодной или горячей системы [69]. Несколько исследований показывают, что существует множество взаимосвязей между вариациями скорости коррозии в разных диапазонах температур для разных материалов.Однако коррозию можно определить как ухудшение свойств материала из-за его взаимодействия с окружающей средой. Коррозия может привести к сбоям в различной инфраструктуре завода или в машинах, которые обычно являются дорогостоящими и обычно требуют много времени на ремонт. На рис. 2 показано сравнение скорости коррозии при повышении температуры. Некоторые из потерь загрязненных продуктов представляют собой ущерб окружающей среде, который может быть дорогостоящим с точки зрения здоровья человека [70]. Существует эмпирическое правило, согласно которому скорость коррозии металла увеличивается вдвое на каждые 10 ° C повышения температуры.Таким образом, если скорость коррозии составляет 30 миль в год (мил в год) при 30 ° C, ожидается, что она будет 60 миль в год при 40 ° C, 120 миль в год при 50 ° C и так далее [71]. Это правило применимо во многих ситуациях, но необходимо распознавать ситуации, в которых его не следует применять. Есть места, где это правило неприменимо. Правило основано на том факте, что скорость коррозии находится под контролем химической реакции при воздействии разбавленной серной кислоты на углеродистую сталь. Даже в таких ситуациях скорость коррозии увеличивается с температурой, она может варьироваться от 1.5–2 раза при повышении температуры на каждые 10 ° C. Но если скорость коррозии находится под контролем некоторых других факторов, таких как присутствие газообразного кислорода в коррозионной среде, то вышеприведенное утверждение может быть неверным. Кислород играет очень важную роль в коррозии. Например, если мы рассматриваем замкнутую систему, построенную из углеродистой стали, то скорость реакции коррозии зависит от присутствия газообразного кислорода. Такой элемент, как железо, который присутствует в углеродистой стали, имеет высокое сродство к кислороду.Следовательно, когда углеродистая сталь вступает в контакт с кислородом, на ней образуется оксидный слой (Fe 2 O 3 или Fe 3 O 4 ) как защитный, так и незащищенный, тем самым увеличивая скорость коррозии [72]. Когда газообразный кислород в окружающей среде системы израсходован в результате коррозии углеродистой стали, скорость коррозии падает до очень низких значений независимо от температуры. Это связано с тем, что в камере не остается кислорода, который может реагировать с элементами с образованием оксида.Следовательно, оксид, который уже образовался на поверхности компонентов, становится пассивным по своей природе. То же самое происходит в открытой системе, когда кислород отводится при повышенной температуре. Последнее соображение — это природа сплавов. Некоторые сплавы образуют защитную или пассивную пленку в определенных условиях, например углеродистая сталь в конц. серная кислота; или они могут развиваться естественным путем, например, в случае нержавеющих сталей и титана. При повышении температуры и до тех пор, пока пассивная пленка остается неповрежденной, скорость коррозии не увеличивается.Но как только пассивная пленка преодолевается повышением температуры, скорость коррозии быстро увеличивается. Необходимо знать фактическую температуру поверхности металла, контактирующего с технологической средой. Поскольку горячая стенка воздействует на трубы повторного котла, они делают внутренний диаметр трубы намного горячее, чем в технологической среде. Следовательно, скорость коррозии может быть выше прогнозируемой. В конденсаторах, где хладагент иногда представляет собой охлаждающую воду со стороны кожуха, снижение температуры может привести к конденсации коррозионных частиц, и это иногда называют эффектом холодного пальца или шоковым охлаждением [73]. Рис.2Сравнение скорости коррозии при повышении температуры Давление обозначается буквой P и представляет собой силу, приложенную перпендикулярно площади поверхности объекта на единицу площади, по которой распределяется сила. Манометрическое давление (иногда также пишется манометрическое давление) — это давление относительно местного атмосферного давления или давления окружающей среды [74]. Для выражения давления используются следующие единицы измерения: паскаль (Па) (это один ньютон на квадратный метр), атмосфера (атм), бар.Давление также играет очень важную роль в определении скорости коррозии [75]. Увеличение общего давления или уменьшение объема также приведет к более высокой скорости реакции, потому что увеличение давления заставляет молекулы сталкиваться с большей силой. Это приводит к более эффективному столкновению, и, следовательно, продукты будут образовываться быстрее или скорость коррозии будет высокой. Если парциальное давление кислорода и углекислого газа высокое, скорость коррозии также будет выше [76].Добавление инертного газа, такого как аргон, неон и криптон, не повлияет на скорость коррозии, поскольку парциальные давления реагирующих газов остаются неизменными [77]. На рисунке 3 показано сравнение скорости коррозии и парциального давления CO 2 . Рис.3Сравнение скорости коррозии и парциального давления CO 2 d) ПокрытиеПокрытия получили широкое распространение для защиты от эрозии и коррозии. Они помогают защитить материал от нескольких химических и физических повреждений, которые могут возникнуть из-за прямого контакта материала с окружающей средой.Поскольку коррозия приводит к разрушению, это в конечном итоге приводит к выходу из строя компонентов как в обрабатывающей, так и в обрабатывающей промышленности. Следовательно, проблемы коррозии и эрозии имеют большое значение для многих промышленных применений и продуктов. Покрытия могут использоваться в качестве инженерного ключа для улучшения поверхностей от коррозии, износа, термического износа и других поверхностных явлений. Хорошая адгезия, низкая пористость и совместимость с подложкой являются различными важными характеристиками приемлемых покрытий.Существуют различные доступные технологии нанесения покрытий, которые можно использовать для нанесения подходящего материала на основу. Обычно они отличаются толщиной покрытия: нанесением толстых пленок (20–400 мкм) и нанесением тонких пленок (менее 10–20 мкм) [78]. Как это работает: котел на биомассеРастущие цены на нефть и растущий спрос на более чистые источники энергии побудили многих производителей котлов по-новому взглянуть на традиционное использование биомассы для производства пара и тепла.Сегодняшний котел, работающий на биомассе, объединяет современные технологии для разработки автоматических систем, которые управляют процессом от выбросов и контроля воздуха до удаления золы. С модернизацией паровых котлов появились сотни разновидностей, размеров и производителей, каждый из которых представил новые конструкции, передовые технологии и предварительный просмотр того, что еще предстоит. Компания Hurst Boiler из Кулиджа, штат Джорджия, конструкция которой представлена здесь, является одной из таких компаний. В печь Гибридные котлы Пробирки для сбора Ясень Большая часть более тяжелых отходов, таких как твердые частицы и зола от сгоревшего сырья, попадает в систему транспортировки золы, которая состоит из заполненного водой желоба, насыщающего золу, чтобы предотвратить попадание пыли в теплообменник. По мере того как зола опускается на дно, цепочка вытягивает ее за пределы печи. Вода сливается по наклонному склону, а оставшаяся зола откладывается на другой конвой для использования в качестве удобрений или для других целей. Автор: Крис Хэнсон |