Простая аккумуляторная дрель на 775-ом


Если вы постоянно что-то мастерите и у вас возникает потребность в мобильной маленькой дрели, эта инструкция именно для вас. Сегодня мы разберем, как сделать такую дрель своими руками. Изготовленная дрель имеет удобную рукоятку, которая изготавливается из ПВХ-трубы. В дрели установлен выключатель с плавной регулировкой оборотов, это позволит экономить энергию и настраивать режим сверления под свои потребности. Для этого понадобится собрать контроллер на JLCPCB или купить уже готовый.
В качестве силового элемента мы будем использовать двигатель 775, который работает от напряжения 12В. Эти движки довольно мощные и выносливые, их активно используют при изготовлении разных домашних станочков. Особенность таких движков в том, что они имеют встроенный вентилятор, что не позволит двигателю перегреться при продолжительном периоде работы. Также у таких двигателей ротор вращается не на втулках, а на подшипниках, что повышает надежность и срок службы. Вал моторчика имеет стандартный диаметр, под него изготавливается множество различных адаптеров, которые можно заказать из Китая. В нашем случае понадобиться патрон от дрели. Питается дрель от аккумуляторов 18650, правда автор забыл устроить гнездо для подключения зарядного устройства. Итак, рассмотрим более подробно, как же сделать такую дрель.
Материалы и инструменты, которые использовал автор:
Список материалов:
— двигатель 775 на 12В;
— ПВХ-труба и уголок;
— фанера;
— печатная плата JLCPCB;
— аккумуляторы 18650;
— включатель от дрели;
— провода;
— термоусадка;
— патрон дрели на 6 мм;
— винтики;
— шуруп и деревянная пробка;
— суперклей;
— электроника для плавной регулировки оборотов;
— термоусадка.
Список инструментов:
— дрель;
— ножовка по металлу;
— клеевой пистолет;
— паяльник;
— мультиметр;
— кусачки.
Процесс изготовления дрели:
Шаг первый. Подготавливаем моторчик
Для самоделки понадобится двигатель 775, можно использовать и другой подобный, самое главное, чтобы он был достаточно мощным. Припаиваем к контактам моторчика провода питания, а потом изолируем места пайки на всякий случай с помощью термоусадки. Используйте провода разных цветов, чтобы не перепутать их при подключении. При неправильной полярности сверло может вращаться в противоположную сторону. Другое дело, если у вас будет реверс.
Шаг второй. Крепим моторчик на уголке
Уголок позволит закрепить моторчик на трубе в виде буквы «Г». Сверлим в уголке отверстия под винты, они будут заворачиваться напротив вентиляционных окон. Двигатель должен максимально плотно заходить в трубу. Если это не так, на него можно подмотать изоленты. Тут есть одно но, автор не предусмотрел окон для охлаждения двигателя. Если дрелью пользоваться долго, двигатель может перегреться. Лучше всего насверлить напротив вентиляционных окон двигателя отверстий для охлаждения.
Шаг третий. Делаем боковую ручку
Для изготовления боковой ручки понадобится кусок не толстой трубки из ПВХ. Под нее делаем пробку из дерева, к которой сверлим отверстие и заворачиваем шуруп, чтобы он немного вылез с другой стороны. Со стороны шляпки отрезаем шуруп. На всякий случай проклейте шуруп суперклеем.
Пробку забиваем в трубу, потом сверху заливаем суперклеем. В уголке сверлим отверстие и теперь просто можно завернуть ручку на свое место.
Шаг четвертый. Подготовка ручки и установка выключателя
Для изготовления ручки понадобится кусок трубы, в ней проделываем окно под включатель. Ну а далее припаиваем необходимые провода к «курку» от дрели. Ну а далее установим курок в корпусе, посадив его на горячий клей. Вставляем ручку в уголок, сверлим отверстия и фиксируем винтами.
Провода для подключения используйте разных цветов и каждый цвет лучше записать, так как проводов тут довольно много.
Шаг пятый. Сборка аккумулятора
В качестве источника питания автор решил использовать старые ячейки 18650 от ноутбука. Учитывайте, что тут нет никаких контроллеров, автор даже забыл вывести гнездо для зарядки. В таком режиме эти аккумуляторы прослужат очень недолго. Вместо аккумуляторов вы всегда можете использовать блок питания на 12В.
Шаг шестой. Корпус для аккумулятора
Аккумуляторы нужно закрепить в корпусе, который делается своими руками. Нам просто нужно собрать коробочку из фанеры. Автор склеивает детали, используя суперклей. В крышке сверлим отверстие и выводим провода. Над проводами вам нужно установки кусок ПВХ трубы такого диаметра, чтобы в него могла зайти ручка. Благодаря этому аккумулятор можно будет закрепить на дрели. Приклеиваем эту деталь, используя суперклей.
Шаг седьмой. Покраска
Покрасьте детали своей дрели, чтобы она красиво смотрелась. Для этого заматываем провода и другие части пакетом и красим детали с помощью баллончика. Автор решил использовать комбинацию желтой и черной краски. Теперь ваше устройство похоже на покупную модель серийного производства!


Шаг восьмой. Сборка контроллера оборотов
Для управления плавностью оборотов понадобится собрать специальную схему. Она собирается на плате JLCPCB. Стоит она недорого, заказать можно из Китая. Ищем в интернете подходящую схему и устанавливаем электронные элементы на свои места. Если нет желания собирать контроллер самому, можно купить уже готовый.


Шаг девятый. Сборка дрели
Берем паяльник и припаиваем провода от курка к контроллеру, также подключаем к контроллеру аккумулятор. Сам контроллер аккуратно укладываем в корпусе, лучше всего его закрепить горячим клеем, чтобы не болтался. Прикручиваем ручку, используя винты.
Шаг десятый. Завершающая сборка
На вал моторчика устанавливаем патрон дрели на 6 мм. Он удобно крепится с помощью винта. В завершении прикрутите к дрели боковую ручку. Дополнительно ее можно закрепить клеем, нанеся его на резьбу винта. Дрель готова, можно испытать!
Шаг одиннадцатый. Испытания
В качестве эксперимента установим в патрон дрели сверло и попробуем что-то просверлить. Автор на видео сверли доски без особых усилий. Эта дрель вполне себе должна справиться и с более сложными задачами, такими как фанера, металлы, пластик и так далее.

Какой вывод можно сделать? Дрель получилась неплохая, удобная, мощная и красиво смотрится. Но устройство имеет существенный недостаток – отсутствие гнезда для подключения зарядного устройства. Но, вероятнее всего, автор просто про него забыл. Помимо этого очень важно установить контроллер для литиевых аккумуляторов. Эти АКБ очень не любят глубокого разряда, а также перезаряда. Их емкость при этом сильно снижается, и количество циклов перезарядки уменьшается с нескольких тысяч до нескольких десятков. На этом все, изготовление дрели можно считать оконченным. Надеюсь, проект вам понравился, и вы почерпнули из этого что-то полезное. Удачи и творческих вдохновений при изготовлении собственных проектов, не забывайте делиться своими наработками с нами.
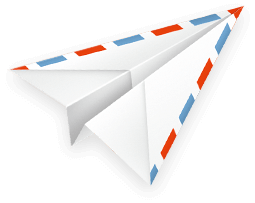
Получайте на почту подборку новых самоделок. Никакого спама, только полезные идеи!
*Заполняя форму вы соглашаетесь на обработку персональных данных
Становитесь автором сайта, публикуйте собственные статьи, описания самоделок с оплатой за текст. Подробнее здесь.Как сделать аккумуляторную дрель (с контроллером батареи)

Привет, друзья самоделкины! В сегодняшней статье мне бы хотелось вам показать, как сделать очень полезную и нужную в хозяйстве самоделку. А именно сегодня мы рассмотрим, как сделать такой ручной инструмент как ручная дрель. Преимуществом данной самоделки заключается в том, что по мощности она не будет уступать заводским аналогам, и при этом её себестоимость будет гораздо ниже, а также основным преимуществом является то, что она «беспроводная», то есть будет работать не от сети, а от аккумулятора. Повторить данную самоделку может абсолютно каждый, во-первых, потому что сама конструкция отличается своей простотой, и во-вторых, потому что она каждому по карману (так как все комплектующие можно найти как в местных магазинах, так и у наших китайских друзей). В общем, самоделка очень интересная, поэтому давайте не будем тянуть с длинным предисловием, погнали!
Для данной самоделки нам понадобится:
— Коллекторный электродвигатель 775 класса. (такие обычно ставят на профессиональные РУ модели).
— Провода
— ПВХ труба с внутренним диаметром максимально похожим на внешний диаметр взятого электродвигателя
— Уголок для ПВХ трубы
— Кнопка
— Аккумуляторные батареи формата 18650 3шт.
— 3S BMS контроллер (плата контроллер заряда/разряда, для 3-ёх литиевых аккумуляторов)
— «Т» образный переходник для ПВХ трубы
— Стандартный разъём питания
— Сверлильный патрон
— Две пластиковые заглушки для ПВХ трубы.
— Набор свёрл
Из инструментов нам также понадобится:
— Паяльник
— Припой
— Маркер
— Ножницы
— Термоклей
— Изолента
— Шестигранник
Ну что приступим к сборке самоделки. Для начала нам следует взять хороший и качественный коллекторный электродвигатель 775 класса, вал которого должен стоять на подшипниках. Для большей тяги следует брать электродвигатель «мало-оборотистый» то есть с большим количеством витков. Ссылка на подходящий электродвигатель находится в конце статьи. Собственно для начала к самому электродвигателю следует припаять два силовых провода длиной около 15-20см.
После чего нам потребуется взять подходящий по внутреннему диаметру уголок для ПВХ трубы. То есть электродвигатель должен плотно садиться в него и не вываливаться. «Запрессовываем» наш электродвигатель в уголок, просунув перед этим провода.
Следующим шагом нам следует зять ПВХ трубу такого же диаметра как уголок. Данная ПВХ труба в данном случае у нас будет выполнять роль рукоятки, то есть длину трубы вы выбираете сами, длина, должна быть такой, чтобы вам потом было удобно работать. На самой трубе нам следует проделать сквозное отверстие для кнопки, для этого в удобном для вас месте при помощи маркера оставляем метку. Затем при помощи паяльника проделываем сквозное отверстие, и после чего при помощи ножниц или ножа расширяем отверстие до нужного нам диаметра (чтобы могла плотно садиться кнопка).
Далее просовываем провода от электродвигателя через ПВХ трубу и через только что проделанное отверстие изнутри (см. фото). И собственно саму трубы соединяем с уголком, в нашем случае достаточно просто вставить трубу на свое место без использования клея.


Один из проводов просовываем внутрь, второй просовываем так же как и первый, но оставив при этом петельку (см. фото). Ножницами перерезаем петельку и очистив изоляцию с кончиков провода припаиваем саму кнопку. Припаяв кнопку к выше сказанным контактам, устанавливаем её на свое место.
После чего для следующего шага нам потребуются 3 литиевые аккумуляторные батарейки формата 18650. Ссылку на качественные батарейки вы также можете найти внизу статьи. Но следует добавить, что это самый распространённый формат аккумуляторных батарей и найти их в своём городе не составит особого труда, например, они находятся внутри старых аккумуляторах от ноутбука, и в ремонтном центре вам отдадут их за «спасибо». Но также стоит учесть, что б/у аккумуляторы не смогут выдать вам большой мощности и большого объёма, и всё-таки рекомендую вам приобрести новые банки.

Разобравшись с аккумуляторами продолжаем. При помощи термоклея соединим 3 аккумулятора между собой в одну батарею так чтобы их, потом можно было бы легко соединить последовательно, то есть, например два аккумулятора «+» кверху, а третий «+» вниз (см. фото). Затем заслуживаем провод, и припаиваем его к аккумуляторам, соединяя их последовательно. Важно отметить, что аккумуляторы вообще не рекомендуется паять обыкновенным паяльником, а делать это следует при помощи контактной сварки, но если у вас её нет, то паяйте предельно аккуратно, а самое главное очень быстро!
Затем нам потребуется взять BMS контроллер для трёх параллельно соединённых литиевых аккумуляторов. Ссылка на данный контроллер тоже имеется в конце самой статьи. Данный контролер следит за зарядом и разрядом каждой банки и балансирует их, он не даст вам переразрядить и перезарядить ваши аккумуляторы. Ну, в общем, полезная вещь. Сам контроллер с аккумулятором и двигателем будем соединять, так как это изображено на схеме ниже.
После чего нам потребуется взять «Т» образный переходник для той же ПВХ трубы. В сам «Т» образный переходник устанавливаем аккумулятор, просунув через центральное отверстие провода от аккумулятора для электродвигателя. Припаиваем провода от аккумулятора (контроллера) к проводам от электродвигателя так, чтобы потом электродвигатель вращался в нужную для сверления сторону.
Далее возьмём разъём питания и припаяем его во «вход» контроллера питания. Следующим шагом нам потребуется сверлильный патрон. Ссылка на патрон тоже есть в конце статьи. Если вы будете покупать данный патрон в местном магазине, следует учесть то, что они бывают разные, и основное отличие у них, это радиус отверстия для вала, на который они собственно и устанавливаются. Так что будьте внимательней. Устанавливаем патрон на вал электродвигателя и затягиваем крепёжный шестигранный винт при помощи обыкновенного шестигранника, следует отметить, что желательно крепёжный винт перед установкой смазать фиксатором резьбы.
Ну и в конце нам потребуются две пластиковые заглушки для «Т» образного переходника, так как у автора самоделки их не оказалось, и найти он их не смог, он эти заглушки напечатал на 3D принтере. Если вы тоже не смогли найти такие заглушки, и 3D принтера у вас нет, то вы можете использовать какой-либо пластик, из которого вырежете нужные окружности и вклеите их. Разобравшись с заглушками, в одной из них следует проделать сквозное отверстие под установку разъёма питания. Ну и вставляем заглушки на свои места.
Всё готово. Осталось зарядить самоделку и протестировать. В итоге у нас получилась очень крутая самоделка, которая точно сможет вам пригодиться, и не будет лежать без дела.
Приобрести комплектующие которые могут пригодиться для сборки данной самоделки можно тут:
Самый популярный BMS 3S контроллер
Сверлильный патрон
Коллекторный электродвигатель
Стальные свёрла
Силовой провод
Качественный припой
Разъём питания
Кнопка вкл/выкл в оригинальном металлическом корпусе (будет смотреться брутально и надёжно).
Вот видео от автора с подробной сборкой и испытаниями данной самоделки:
Ну и всем спасибо за внимание и удачи в будущих проектах самодельщики!
Источник
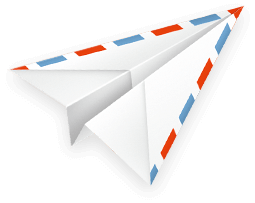
Получайте на почту подборку новых самоделок. Никакого спама, только полезные идеи!
*Заполняя форму вы соглашаетесь на обработку персональных данных
Становитесь автором сайта, публикуйте собственные статьи, описания самоделок с оплатой за текст. Подробнее здесь.Как превратить дрель в фрезер с помощью простой оснастки
Не обязательно покупать фрезер заводского изготовления, если появилась необходимость в таком устройстве, ведь он стоит немалых денег. Его можно сделать своими руками из бытовой дрели и самых простых материалов.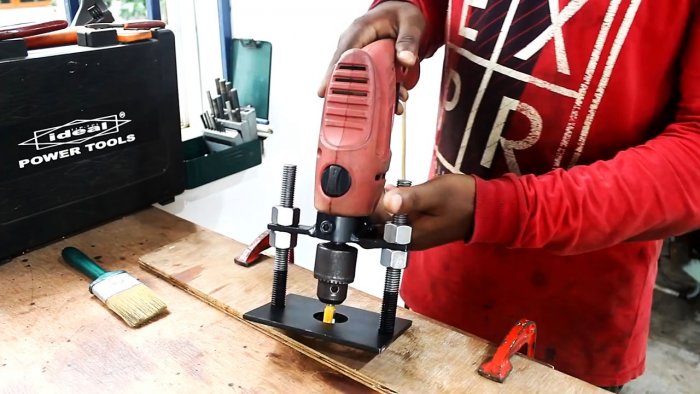
Понадобится
Чтобы трансформировать дрель в вертикальный фрезер, до начала работ заготовим следующие материалы и изделия:
- трубу круглую;
- полосу и пластину стальную;
- фундаментные или анкерные болты;
- четыре гайки;
- электродрель;
- три стопорных болта;
- фрезу по дереву.
Для изготовления оснастки и ее сборки нам потребуется: дисковая пила, токарный и сверлильный станки, болгарка, напильники разные, расточка с двумя резцами, метчик с воротком, сварка, штангенциркуль и др.
Процесс изготовления фрезера на основе дрели
Отрезаем маятниковой пилой от стальной трубы кольцо необходимой ширины.
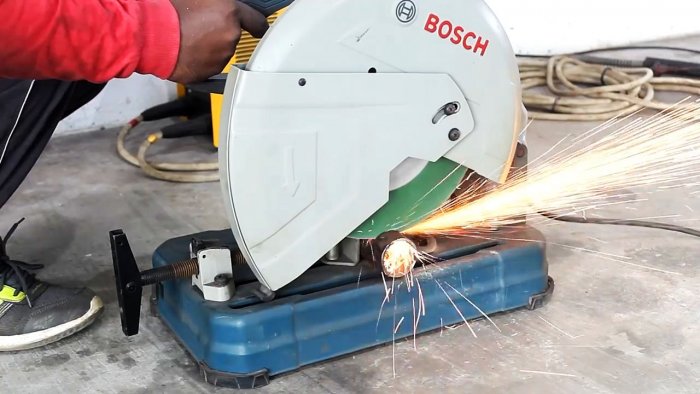
На токарном станке торцуем концы, удаляем заусенцы и сглаживаем кромки. С помощью расточной головки получаем нужный размер внутреннего диаметра.
Выполняем на сверлильном станке по центру боковой поверхности кольца три радиальных отверстия, отстоящих друг от друга на 120 градусов.
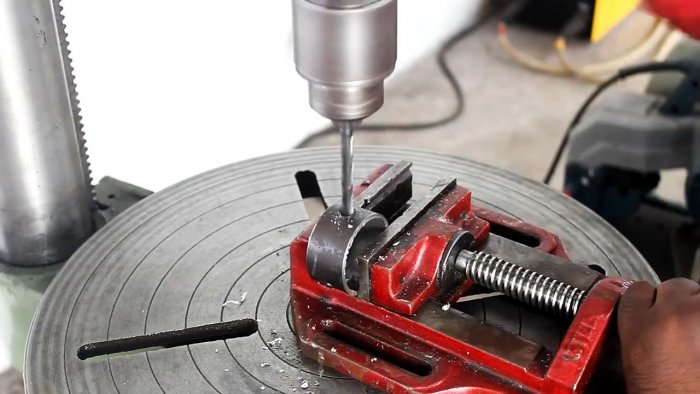
Зажимаем кольцо в тиски и круглым напильником удаляем заусенцы с отверстий. Затем в них нарезаем резьбу, используя метчик и вороток.
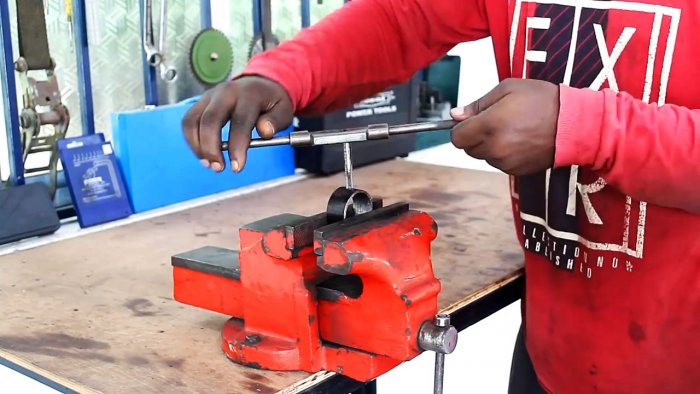
Отрезаем маятниковой пилой два одинаковых фрагмента от металлической полосы.
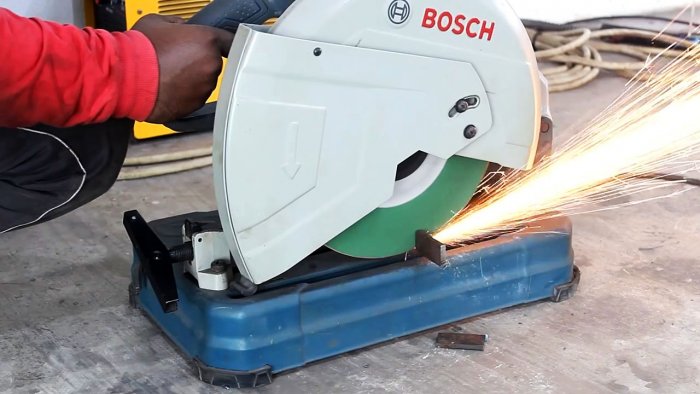
Выполняем в них с одного конца отверстия на сверлильном станке, используя сперва малое, а потом большое сверло.
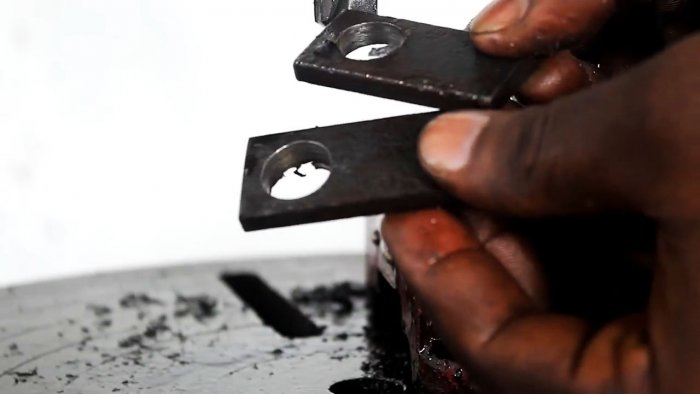
Привариваем полоски отверстиями наружу к нижней части боковой поверхности кольца в диаметрально противоположных направлениях.
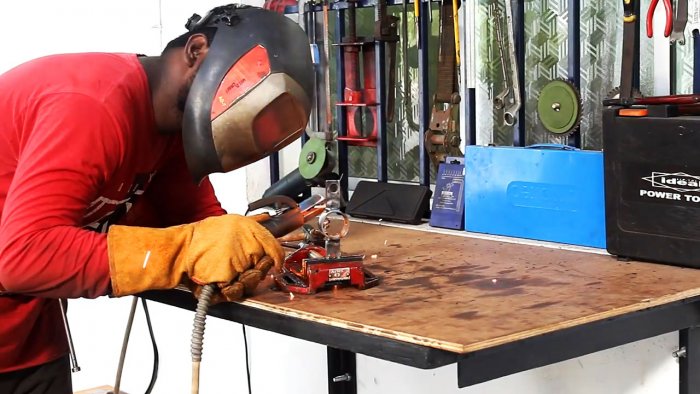
Отделяем болгаркой с отрезным диском от стальной пластины часть с заданной шириной, длиной и толщиной. Удалив заусенцы, и скруглив кромки, в центре пластины выполняем на сверлильном станке корончатым сверлом сквозное отверстие.
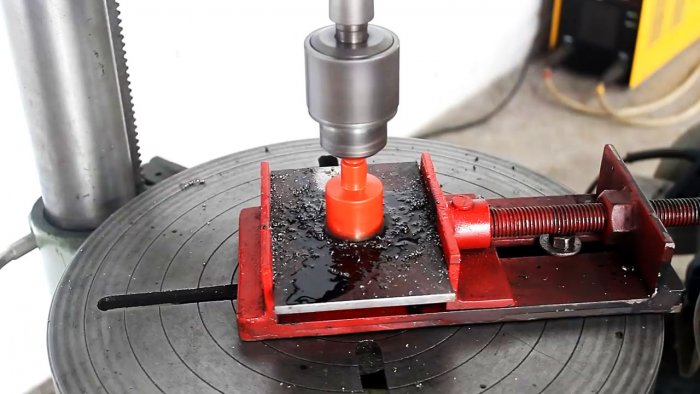
Затем спиральным сверлом требуемого диаметра, выполняем еще два сквозных отверстия, расположенных по длинной оси симметрии пластины ближе к ее краям.
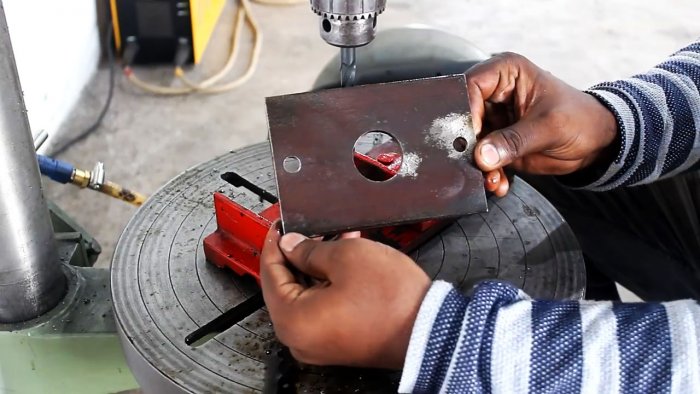
Отрезаем от длинных болтов (шпилек) по разметке части с головками, которые нам больше не понадобятся.
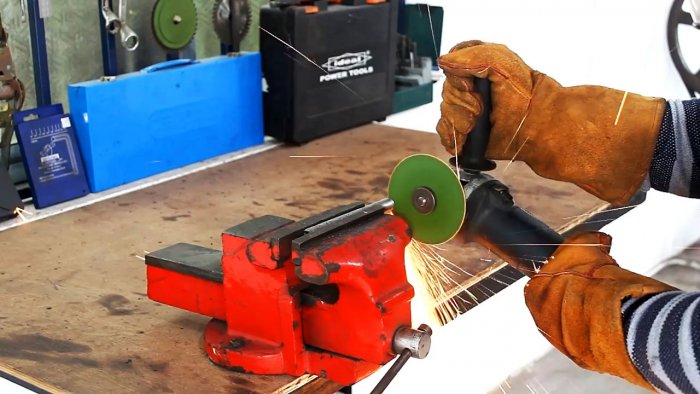
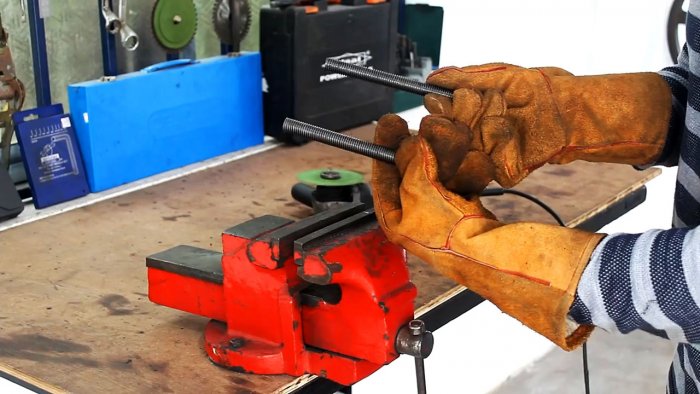
Оставшиеся резьбовые стержни торцуем на токарном станке и, с одной стороны, протачиваем под заданную длину и диаметр.
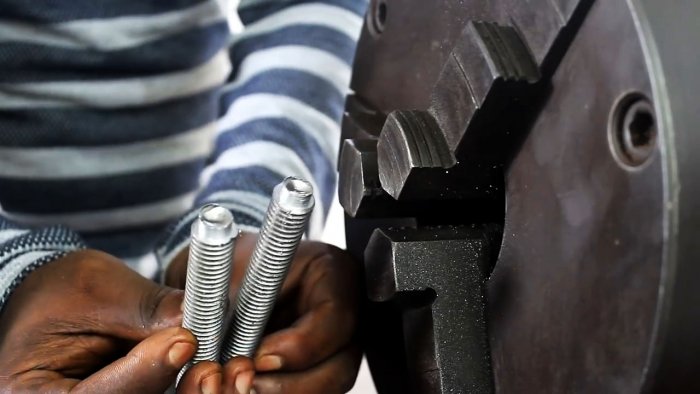
Устанавливаем стержни проточками в отверстия в пластине и с обратной стороны с помощью электродуговой сварки завариваем. Места сварки тщательно обрабатываем болгаркой с отрезным диском.
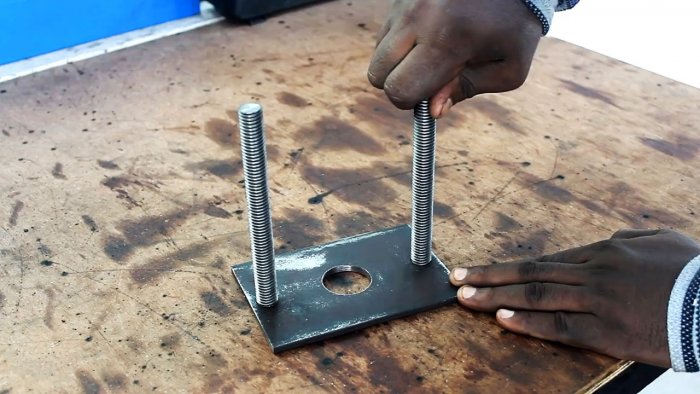
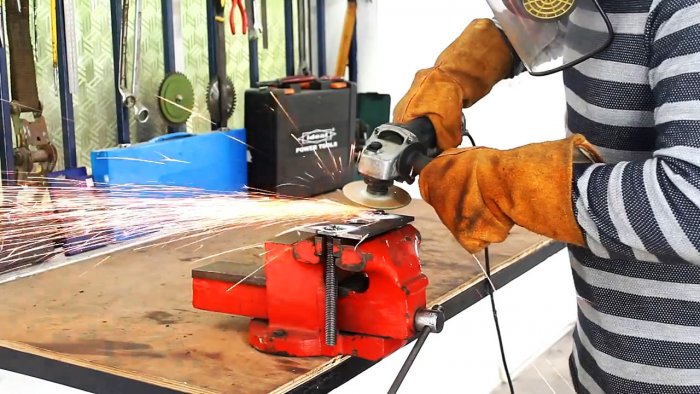
На стержни-стойки наворачиваем по одной гайке, затем ставим кольцо с приваренными пластинами, используя отверстия в них. Сверху закручиваем еще по одной гайке.
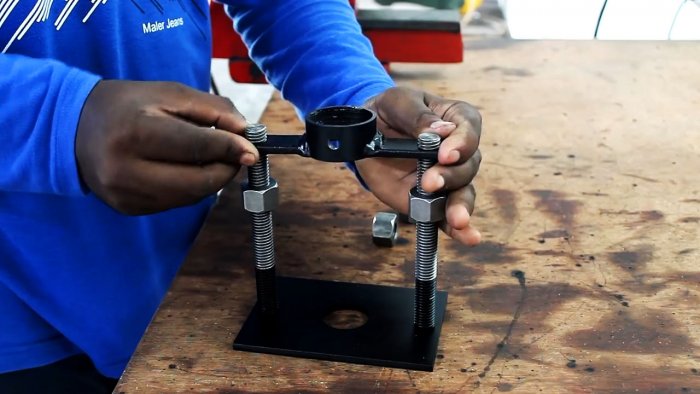
В кольцо сверху вставляем дрель, пока она не сядет цилиндрическим пояском на корпусе в кольцо. Фиксируем дрель тремя болтами, вкручиваемых в отверстия на боковой поверхности кольца.

Вставляем в патрон дрели фрезу по дереву и зажимаем ее там. Затем, опуская или поднимая нижние гайки на стержнях-стойках, выставляем требуемый вылет фрезы и затягиваем верхние гайки.
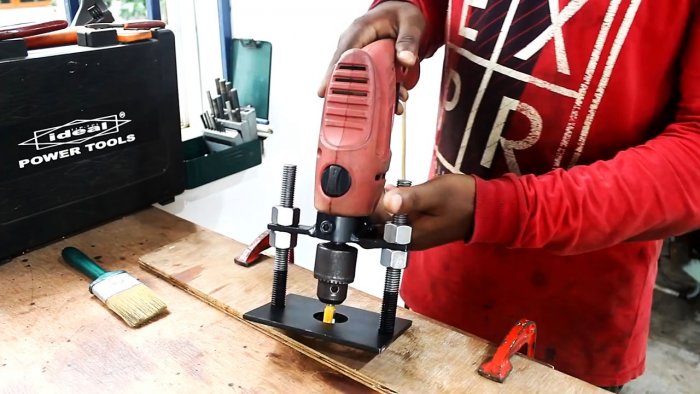
Для проверки фрезера в работе включаем дрель, беремся руками за стержни в районе гаек, ставим его основанием на поверхность обрабатываемой детали и подводим фрезу к ее торцу. Слегка прижимая вниз, перемещаем фрезер в нужную сторону. При этом согласуем величину подачи с оборотами фрезы.
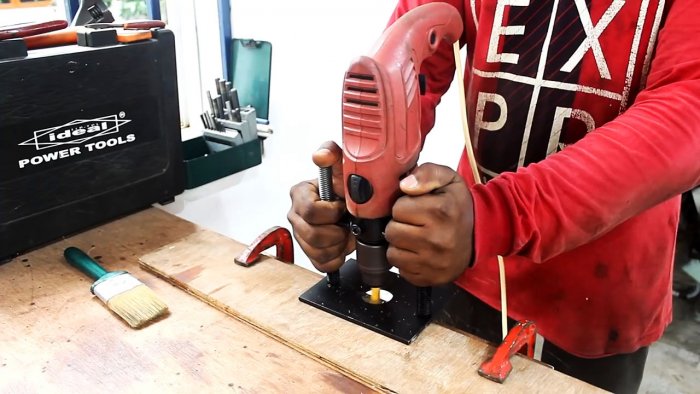
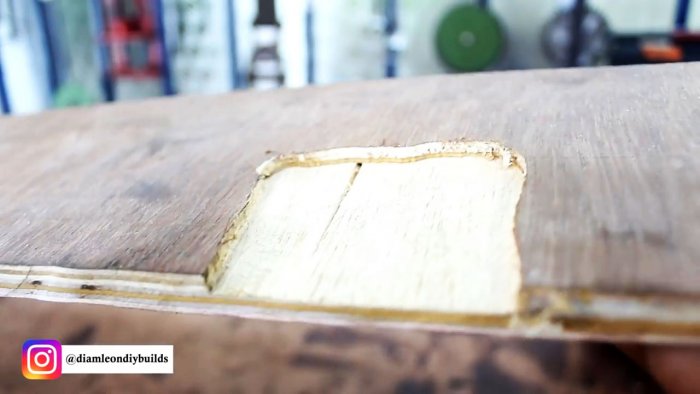
Смотрите видео
DIY сверлильный станок из стойки и ручной электродрели.
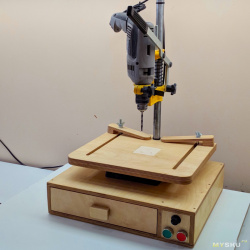
Все предыдущие года для сверления отверстий я вполне обходился шуруповертом, ну очень редко ручной дрелью. Этого вполне хватало, на деталях с небольшой толщиной проблем не возникало. Другой вопрос сверление четко вертикальных отверстий в большой толщине материала, иногда получается контролировать вертикальность сверла, иногда не очень.
Рассверливание меньшего отверстия сверлом большего диаметра: зачастую, при рассверливании изначальный центр отверстия мог и сместиться, в зависимости от того, как там себя найдет сверло.
Чтобы избежать всех этих проблем, ответственные детали и заготовки сверлить надо на сверлильном станке, которого естественно нет.
Я уже дошел до кондиции, когда сверлильный станок нужен, но вот что точно я от него хочу, какие параметры для меня важны, и какой нужно выбрать – я пока не знаю. Поэтому для наработки опыта и формирования у себя будущих потребностей, для лучшего и эффективного вложения средств в сверлильный станок в будущем, я решил поупражняться на самодельном станке из стойки для ручной дрели.
Можно было купить просто стойку, разместить в ней дрель и пользоваться, но мне необходимо было сделать удобное включение и выключение дрели, а также удобную регулировку скорости вращения. Поэтому я решил сделать для стойки небольшой постамент, с размещенными в ней органами управления, а также ящиком для сверл и других принадлежностей.
А на самом основании стойки решил сделать более широкий стол для размещения и фиксации заготовок под сверление. В ходе проектирования получилась вот такая конструкция (стойка и дрель в модели другие, взял из 3D Warehouse):
Конструкция ящика следующая, с установленным в нем органайзером под часто используемые сверла:
Чертежи с размерами:
Изучив просторы сети и отзывы, была выбрана уже довольно известная стойка для дрели Энкор 20090 с цельнометаллической колонной и чугунными основанием и кареткой. (Паспорт стойки)
Несколько фото распаковки и сборки:
Люди в отзывах пишут про люфт в пластиковой направляющей каретки, и небольшом люфте в точке колонна-каретка, но не у всех. Мне достался люфт пластиковой направляющей, который вылечился просто подкладыванием кусочка пластика от папки для бумаг. Люфт пропал вообще, каретка стала туго ходить вверх-вниз, но густая силиконовая смазка убрала и эту проблему. Стойка отличная, тяжелая, монументальная!
В качестве рабочей части нашего станка выступила старенькая, но бодрая дрель Интерскол ДУ13/780ЭР:
Дрель плотно зашла в приемное гнездо на стойке, люфтов нет, фиксация отличная:
Начинаем собирать наш постамент с ящиком. Напиливаем детали постамента. В проекте я заложил фанеру толщиной 10 мм, но так получилось, что у меня стоял уже начатый лист 12мм, который я почему-то принял за 10мм, от этого у меня плыли размеры и я еще долго не мог понять почему ):
Собираем на саморезы и ПВА:
Напиливаем детали внутреннего выдвижного ящика, дно ящика из фанеры 6мм:
Собираем ящик:
Готовим и вклеиваем заднюю и переднюю заглушки постамента:
Для выдвижного ящика используем мебельные шариковые направляющие:
Для крепления ящика к петлям положил рядом лист фанеры и подложил четыре 10-ти рублевых монеты для создания равномерного зазора между ящиком и основанием постамента:
Выпиливаем и приклеиваем на ПВА лицевую панель ящика, зазоры также регулируем монетами:
Не забываем сделать ручку для открытия ящика:
В качестве начинки для управления включением/выключением и регулировкой оборотов подобрал в закромах вот такой комплект: реле с катушкой 230V, две кнопки, c NO и NC контактами, и симмисторный регулятор оборотов (2000Вт) с Aliexpress:
На передней панели размечаем отверстия под кнопки и потенциометр регулятора:
Сверлим отверстия. Под ручку потенциометра пришлось сделать небольшое углубление дремелем с фрезой, так как толщина лицевой панели 6 мм, и ручка нормально на вал потенциометра не садилась:
Примеряем кнопки:
На заднюю заглушку блока кнопок решил поставить розетку под вилку дрели, а также сальниковый ввод для провода питания от сети:
Берем верхнюю крышку постамента, размечаем и сверлим отверстия для крепления основания стойки (верхнюю крышку постамента не приклеивал, крепил только на саморезы):
Переходим к изготовлению сверлильного стола. Будем делать из двух листов фанеры:
Соединяем два листа на четыре самореза, размечаем и выпиливаем лобзиком паз под колонну нашей стойки, дорабатываем дремелем:
Размечаем закругление углов:
Размечаем, берем фрезер и пазовой фрезой ф10мм по фанерному упору делаем пазы под перемещаемые прижимы стола, а также скругления стола:
Разбираем нашу деталь, берем нижний лист, размечаем и сверлим в нем отверстия для крепления стола к основанию стойки:
С обратной стороны, для крепления использовал вот такой крепеж с резьбой М8, чтобы утопить шляпки, сделал углубления дремелем:
Берем верхний лист стола, размечаем и выпиливаем квадратное отверстие 70х70 мм под сменный вкладыш. Вкладыш размещаем со смешением относительно центра, чтобы его можно было переворачивать и использовать все стороны квадрата вкладыша:
Склеиваем на ПВА оба листа нашего стола:
Готовим зажимы для стола. Их сделал из обрезков фанеры, немного скосил полученную пятку, чтобы получался хороший зажим тонких деталей. Отверстие 8мм под прижимной болт немного выработал в продольном направлении, чтобы болт в детали мог отклоняться относительно вертикальной оси.
Пробуем наш зажим в действии, используем длинный мебельный болт M8, шайбы и барашковую гайку:
Берем все полученные детали станка, шлифуем и покрываем маслом:
Ставим все компоненты системы питания и управления, кнопки и реле подключены по схеме с самоподхватом:
Делаем проверку включения, всё ставим и фиксируем провода:
Снизу постамента ставим прорезиненные ножки:
Крепим сверлильный стол к основанию стойки гайками М8:
Далее крепим уже основание со столом к верхней крышке постамента болтами и гайками М6:
Вставляем ящик, смотрим, что пока получилось:
Переходим к изготовлению органайзера для сверл. Все детали горизонтального отделения органайзера из фанеры 6мм. Выпиливаем по чертежу основание, напиливаем тонкие полоски фанеры, и собираем бортики на ПВА:
Напиливаем на столе разделители шириной 6мм (для таких операций мне на распиловочном столе пришлось сделать вкладыш нулевого зазора из алюминия, так как изначальная поверхность стола уже износилась, и на фанере пошли сильные сколы):
Разделители клеим через шаблон 14 мм на ПВА. Глубину и ширину (6х14 мм) отделения брал из расчета своих пальцев, чтобы я мог без труда взять мелкое сверло со дна отделения:
Вертикальный органайзер под самые ходовые сверла (два отделения под сверла по металлу и по дереву) решил сделать из фанеры 12 мм, но сверху приклеить полоску из фанеры 6мм, так как в торец фанеры сверлится совсем плохо:
Примеряем наш вертикальный органайзер к горизонтальному:
Размечаем и насверливаем уже на нашем столе отверстия в органайзере всеми доступными сверлами, от 8мм до 1мм с шагом диаметра 1 мм:
Примеряем оба органайзера в ящике:
Покрываем маслом новые детали, ставим в ящик. Вертикальный органайзер ставим на мелкие петли, чтобы его можно было откидывать в полностью вертикальное положение и иметь доступ к сверлам в нижнем отделении.
Перед горизонтальным органайзером приклеил в ящике упор из куска фанеры 6мм, после него в ящике чуть позже будет органайзер под фрезы, зенковки и другие крупные сверла. Также заготовил несколько квадратных сменных вкладышей:
Собираем все детали станка, сворачиваем и крепим кабель дрели, чтобы не мешал:
Работаем:
Сверлильный станок получился годный. Сверлить так гораздо удобнее, и главное точнее и аккуратнее. Нет конечно поддержания оборотов, с ним было бы еще комфортней, но я уже начинаю привыкать, какую скорость надо выставить на дрели и силу погружения для материала, чтобы не просаживать дрель, но и не испортить заготовку или деталь высокими оборотами. Это всё опытом отрабатывается. Поработаю на нем, пойму, что мне нужно и важно от станка, какие параметры мне будут критичны, чтобы возможно в будущем рассматривать «взрослый» станок.
В ближайших планах сделать к станку небольшие тиски для вертикального крепления заготовок и шлифовальный барабан, они мне нужны для приближающихся проектов.
3D модель станка в SketchUp: ссылка