как паять мелкие детали паяльником с толстым жалом
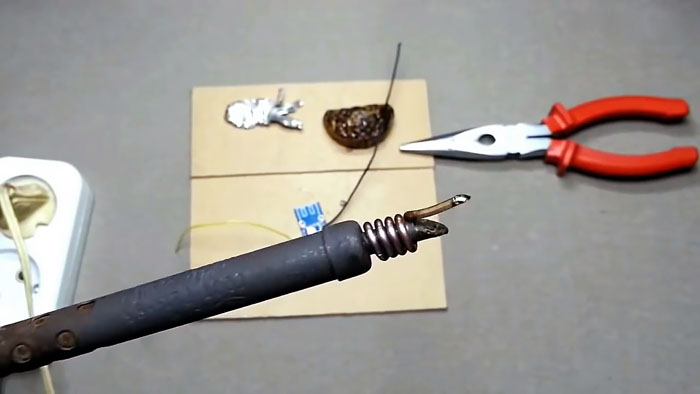
Наверняка у каждого в жизни была такая ситуация, когда необходимо было подпаять отвалившийся тонкий провод, или заменить пайкой очень маленький СМД компонет, но под рукой был только обычный паяльник. Произвести мелкую пайку толстым жалом очень трудно, если вообще возможно. Но тут на помощь может придти хитрость — лайфхак: как сделать для обычного паяльника мини жало, которое как раз и подойдет для подобных дел.
Понадобится
- Медная проволока (провод в изоляции одножильный) 1-1,5 мм в диаметре.
- Кусачки.
- Плоскогубцы.
- Напильник.
- Острый нож.
- Ну и естественно сам паяльник с толстым жалом.
Дорабатываем жало паяльника для пайки мелких деталей
Берем толстый одножильный медный провод и откусываем нужную длину порядка 10 см. С помощью ножа снимаем изоляцию с медной жилы. Если будете использовать проволоку — не забудьте удалить лаковое покрытие ножом или отжигом.
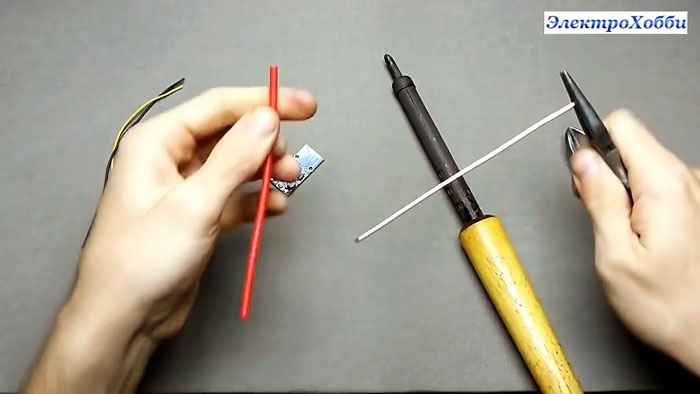
Берем наш паяльник и накручиваем плотно провод на жало. Чтобы обеспечить наилучшую теплопередачу, хорошо бы предварительно зачистить жало от нагара. Как нельзя кстати для этого подойдет мелкая наждачная бумага.
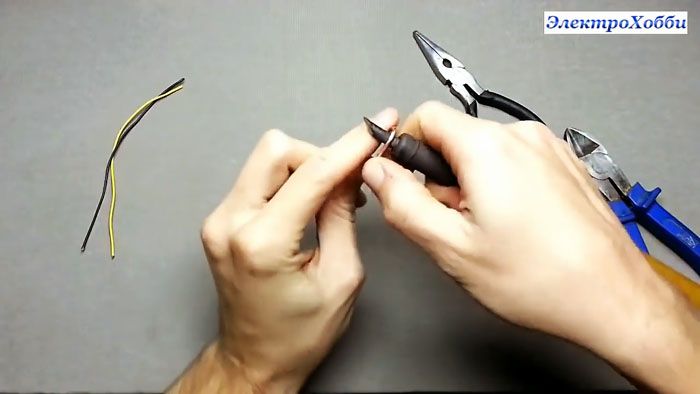
Загибаем задний кончик плоскогубцами.
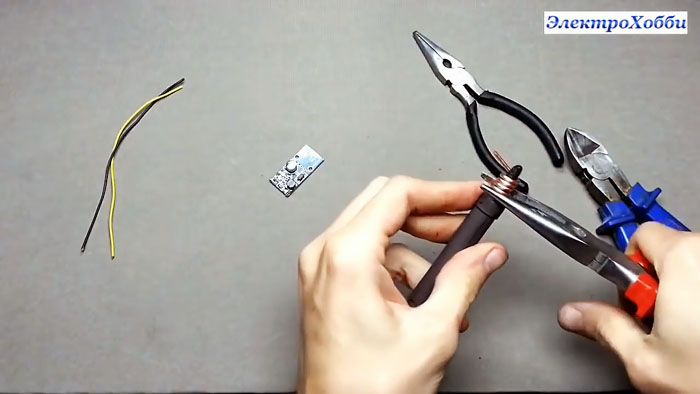
А передний выравниваем — это и будет новое жало для паяльника.
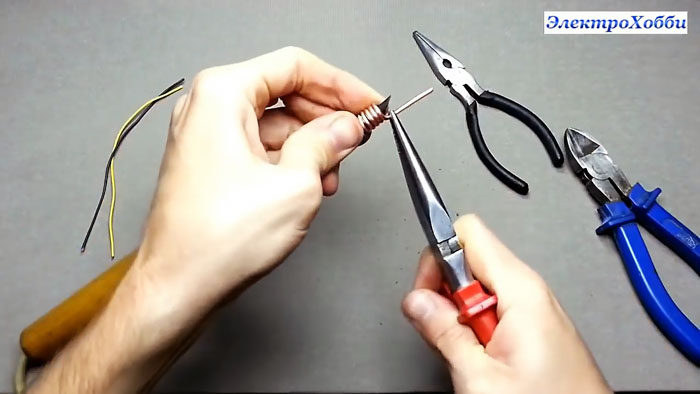
Откусываем нужную длину. Сильно длинный конец оставлять не стоит — не будет прогреваться, да и паять будет не удобно.
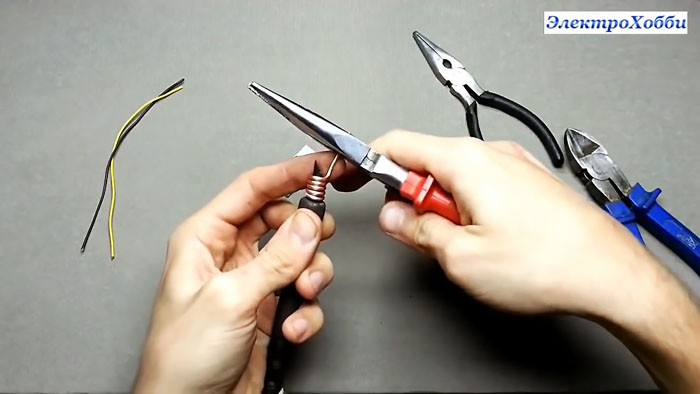
С помощью напильника придаем нужную форму новому жалу. В общем стачиваем под скос.
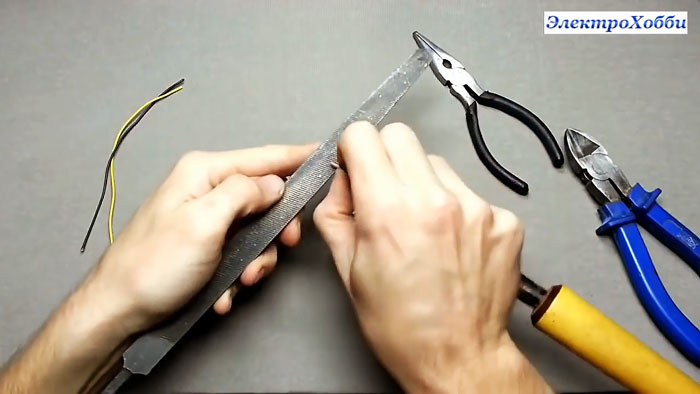
Теперь включаем паяльник и разогреваем его. Облуживаем как обычно новое жало используя олово и канифоль, процедура не хитрая.
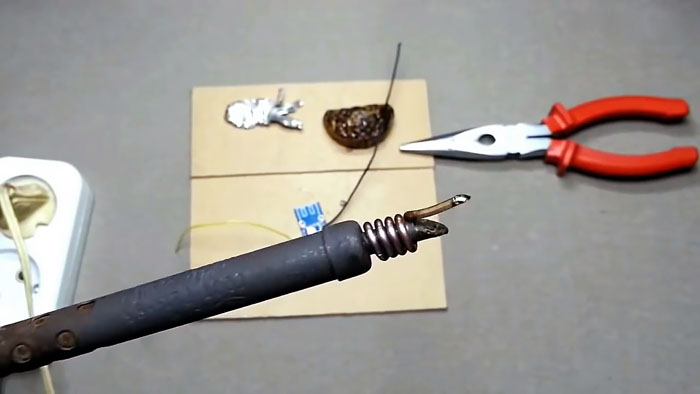
Теперь вам не составит труда паять любые СМД компоненты или другие мелкие соединения.
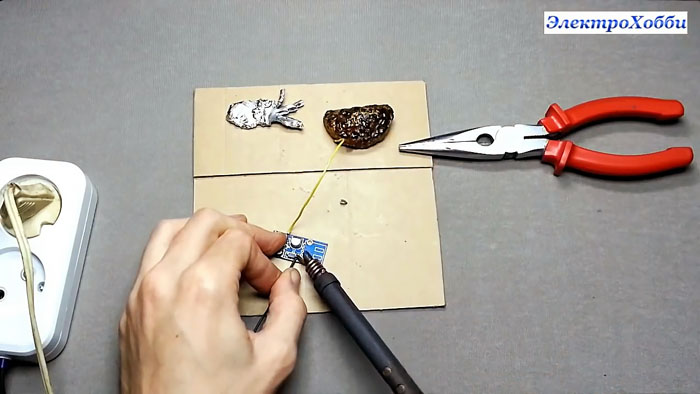
Если вы все правильно сделали спиралька должна сидеть хорошо и не болтаться при пайке.
Смотрите видео
Как паять мелкие детали в телефоне
Все понимают, как можно с помощью обычного паяльника ЭПСН, мощностью 40 ватт, и мультиметра, самостоятельно ремонтировать различную электронную технику, с выводными деталями. Но такие детали сейчас встречаются, в основном только в блоках питания различной техники, и тому подобных силовых платах, где протекают значительные токи, и присутствует высокое напряжение, а все платы управления, сейчас идут на SMD элементной базе.
На плате SMD радиодетали
Так как же быть, если мы не умеем демонтировать и впаивать обратно SMD радиодетали, ведь тогда минимум 70% от возможных ремонтов техники, мы уже самостоятельно не сможем выполнить. Кто нибудь, не очень глубоко знакомый с темой монтажа и демонтажа, возможно скажет, для этого необходимы паяльная станция и паяльный фен, различные насадки и жала к ним, безотмывочный флюс, типа RMA-223, и тому подобное, чего в мастерской домашнего мастера обычно не бывает.
У меня есть дома в наличии, паяльная станция и фен, насадки и жала, флюсы, и припой с флюсом различных диаметров. Но как быть, если тебе вдруг потребуется починить технику, на выезде на заказ, или в гостях у знакомых? А разбирать, и привозить дефектную плату домой, или в мастерскую, где есть в наличии соответствующее паяльное оборудование, неудобно, по тем или иным причинам? Оказывается выход есть, и довольно простой. Что нам для этого потребуется?
Что нужно для хорошей пайки
- 1. Паяльник ЭПСН 25 ватт, с жалом заточенным в иголку, для монтажа новой микросхемы.
- 2. Паяльник ЭПСН 40-65 ватт с жалом заточенным под острый конус, для демонтажа микросхемы, с применением сплава Розе или Вуда. Паяльник, мощностью 40-65 ватт, должен быть включен обязательно через Диммер, устройство для регулирования мощности паяльника. Можно такой как на фото ниже, очень удобно.
- 3. Сплав Розе или Вуда. Откусываем кусочек припоя бокорезами от капельки, и кладем прямо на контакты микросхемы с обоих сторон, в случае если она у нас, например в корпусе Soic-8.
- 4. Демонтажная оплетка. Требуется для того, чтобы удалить остатки припоя с контактов на плате, а также на самой микросхеме, после демонтажа.
- 5. Флюс СКФ (спиртоканифольный флюс, растолченная в порошок, растворенная в 97% спирте, канифоль), либо RMA-223, или подобные флюсы, желательно на основе канифоли.
- 6. Удалитель остатков флюса Flux Off, или 646 растворитель, и маленькая кисточка, с щетиной средней жесткости, которой пользуются обычно в школе, для закрашивания на уроках рисования.
- 7. Трубчатый припой с флюсом, диаметром 0.5 мм, (желательно, но не обязательно такого диаметра).
- 8. Пинцет, желательно загнутый, Г — образной формы.
Распайка планарных деталей
Итак, как происходит сам процесс? Кое-что почитайте тут. Мы откусываем маленькие кусочки припоя (сплава) Розе или Вуда. Наносим наш флюс, обильно, на все контакты микросхемы. Кладем по капельке припоя Розе, с обоих сторон микросхемы, там где расположены контакты. Включаем паяльник, и выставляем с помощью диммера, мощность ориентировочно ватт 30-35, больше не рекомендую, есть риск перегреть микросхему при демонтаже. Проводим жалом нагревшегося паяльника, вдоль всех ножек микросхемы, с обоих сторон.
Демонтаж с помощью сплава Розе
Контакты микросхемы у нас при этом замкнутся, но это не страшно, после того как демонтируем микросхему, мы легко с помощью демонтажной оплетки, уберем излишки припоя с контактов на плате, и с контактов на микросхеме.
Итак, мы взялись за нашу микросхему пинцетом, по краям, там где отсутствуют ножки. Обычно длина микросхемы, там где мы придерживаем ее пинцетом, позволяет одновременно водить жалом паяльника, между кончиками пинцета, попеременно с двух сторон микросхемы, там где расположены контакты, и слегка тянуть ее вверх пинцетом. За счет того что при расплавлении сплава Розе или Вуда, которые имеют очень низкую температуру плавления, (порядка 100 градусов), относительно бессвинцового припоя, и даже обычного ПОС-61, и смещаясь с припоем на контактах, он тем самым снижает общую температуру плавления припоя.
Демонтаж микросхем с помощью оплетки
И таким образом микросхема у нас демонтируется, без опасного для нее перегрева. На плате у нас образуются остатки припоя, сплава Розе и бессвинцового, в виде слипшихся контактов. Для приведения платы в нормальный вид мы берем демонтажную оплетку, если флюс жидкий, можно даже обмакнуть ее кончик в нее, и кладем на образовавшиеся на плате “сопли” из припоя. Затем прогреваем сверху, придавив жалом паяльника, и проводим оплеткой вдоль контактов.
Выпаивание радиодеталей с оплеткой
Таким образом весь припой с контактов впитывается в оплетку, переходит на нее, и контакты на плате оказываются очищенными полностью от припоя. Затем эту же процедуру, нужно проделать со всеми контактами микросхемы, если мы собираемся запаивать микросхему в другую плату, или в эту же, например после прошивания с помощью программатора, если это микросхема Flash памяти, содержащая прошивку BIOS материнской платы, или монитора, или какой либо другой техники. Эту процедуру, нужно выполнить, чтобы очистить контакты микросхемы от излишков припоя. После этого наносим флюс заново, кладем микросхему на плату, располагаем ее так, чтобы контакты на плате строго соответствовали контактам микросхемы, и еще оставалось немного места на контактах на плате, по краям ножек. С какой целью мы оставляем это место? Чтобы можно было слегка коснувшись контактов, жалом паяльника, припаять их к плате. Затем мы берем паяльник ЭПСН 25 ватт, или подобный маломощный, и касаемся двух ножек микросхемы расположенных по диагонали.
Припаивание SMD радиодеталей паяльником
В итоге микросхема у нас оказывается “прихвачена”, и уже не сдвинется с места, так как расплавившийся припой на контактных площадках, будет держать микросхему. Затем мы берем припой диаметром 0.5 мм, с флюсом внутри, подносим его к каждому контакту микросхемы, и касаемся одновременно кончиком жала паяльника, припоя, и каждого контакта микросхемы. Использовать припой большего диаметра, не рекомендую, есть риск навесить “соплю”. Таким образом, у нас на каждом контакте “осаждается” припой. Повторяем эту процедуру со всеми контактами, и микросхема впаяна на место. При наличии опыта, все эти процедуры реально выполнить за 15-20 минут, а то и за меньшее время. Нам останется только смыть с платы остатки флюса, растворителем 646, или отмывочным средством Flux Off, и плата готова к тестам, после просушивания, а это происходит очень быстро, так как вещества применяемые для смывания, очень летучие. 646 растворитель, в частности, сделан на основе ацетона. Надписи, шелкография на плате, и паяльная маска, при этом не смываются и не растворяются.
Единственное, демонтировать таким образом микросхему в корпусе Soic-16 и более многовыводную, будет проблематично, из-за сложностей с одновременным прогреванием, большого количества ножек. Всем удачной пайки, и поменьше перегретых микросхем! Специально для Радиосхем — AKV.
Вот, решил показать, как я паяю SMD компоненты («Surface Montage Details» — означает поверхностный монтаж деталей). Вообще, почему-то, бытует мнение, что паять SMD компоненты сложно и неудобно. Я постараюсь Вас переубедить в обратном. Более того, я докажу, что паять SMD компоненты намного проще обычных TH компонентов («Through Hole» в переводе «сквозь отверстие» — сквозьдырочные компоненты :)).
Если быть совсем уж откровенным у TH и SMD компонентов есть свои назначения и области использования и попытки с моей стороны убеждать Вас в том, что SMD лучше, немного не корректны. Ну да ладно — все равно, я думаю, Вам будет интересно почитать.
Знаете, какая главная ошибка тех, кто первый раз пробует паять SMD компоненты? Разглядывая меленькие ножки микросхемы, сразу возникает мысль о том, какое тонкое жало нужно взять, чтобы паять эти мелкие ножки и не насажать «соплей» между ними. В магазине находим конусное тонкое жало, цепляем его на паяльник, набираем маленькую капельку припоя и пытаемся иголкой-жалом обпаять каждую ножку отдельно. Получается долго, утомительно и не аккуратно. Данный подход, казалось бы, логичен, но в корне не верен! И вот почему – паять SMD компоненты помогают такие «страшные силы» как поверхностное натяжение, силы смачивания, капиллярный эффект и не использовать их значит сильно усложнять свою жизнь.
Как все должно проходить в теории? Когда жало паяльника приложено к ножкам начинает действовать сила смачивания — олово под действием этой силы начинает «обтекать» ножку со всех сторон. Под ножку олово «затягивается» капиллярным эффектом одновременно начинается «смачиваться» контактная площадка под ножкой и на плате. Припой равномерно «заливает» площадку вместе с ножкой. После того как жало паяльника убрано от ножек и пока еще припой в жидком состоянии, сила поверхностного натяжения формирует из припоя каплю, не давая ему растекаться и сливаться с соседними ножками. Вот такие сложные процессы происходят при пайке. Но все эти процессы происходят сами собой, а от Вас требуется лишь поднести жало паяльника к ножке (или сразу к нескольким). Правда просто?!
На практике есть определенные проблемы с пайкой очень мелких SMD компонентов (резисторы, конденсаторы …) они могут во время пайки «прилипать» к жалу. Для того чтобы избежать такой проблемы нужно паять отдельно каждую сторону.
Для того, чтобы добиться хорошей пайки, нужны определенные материалы и инструменты.
Главным материалом, обеспечивающим комфортную пайку, является жидкий флюс. Он обезжиривает и снимает окислы с поверхности спаиваемого металла, что увеличивает силу смачивания. Кроме того, во флюсе припою легче образовать каплю, что препятствует созданию «перемычек-соплей» Рекомендую применять именно жидкий флюс — канифоль или вазелин-флюс не дают такого эффекта. Жидкий флюс не редкость в магазинах — купить его будет не проблема. На вид это прозрачная жидкость с противным запахом напоминающий ацетон (тот, что я покупаю называется «F5 – флюс для пайки тонкой электроники»). Можно, конечно, попробовать паять и спирто-канифолью, но во-первых, эффект будет хуже, во-вторых, после удаления застывшей канифоли спиртом, остается белый налет, который очень проблематично убрать.
Вторым по важности является паяльник. Очень хорошо если имеется регулировка температуры – можно не боятся перегреть компоненты. Оптимальная температура для пайки SMD компонентов находится в пределах 250-300 оС. Если нет паяльника с регулировкой температуры, тогда лучше применять низковольтный паяльник (12v или 36v мощность 20-30w) он имеет меньшую температуру жала. Самый худший результат дает обычный паяльник на 220v. Проблема в том, что температура жала у него слишком высока, из-за чего флюс быстро испаряется и ухудшается смачиваемость поверхности пайки. Большая температура не позволяет длительно греть ножку, из-за этого пайка превращается в нервное тыканье жалом в плату. Как частичный выход из положения можно посоветовать включить паяльник через регулятор мощности (сделать самому – схема довольно простая или купить готовый – в магазине светильников такие продаются как регуляторы яркости свечения светильников, люстр).
Жало у паяльника должно иметь ровный рабочий срез (это может быть или классический «топорик», типа «отвертка» или срез под 45 градусов).
Жало-конус плохо подходит для пайки SMD компонентов – не паяйте им, намучаетесь. Очень хорошие результаты дает жало «микроволна». Кто не знает – это жало имеющее в рабочей плоскости отверстие. При помощи этого отверстия и капиллярного эффекта создаваемого в нем припой можно не только наносить, но и эффективно убирать излишки (после того как я попробовал паять «микроволной» остальные жала валяются в коробочке без дела).
Припой. Особого припоя не нужно – используйте тот, каким Вы обычно пользуетесь. Очень удобен припой в тонкой проволочке – легко дозировать. У меня проволочка диаметром 0.5мм. Не используйте припой без свинца (на него пытаются заставить перейти производителей электроники по причине вредности свинца). Из-за отсутствия в припое свинца значительно уменьшается сила поверхностного натяжения, паять обычным паяльником станет проблематично.
Еще нужен пинцет. Тут без особенностей – подойдет любой удобный для Вас.
Технология пайки очень проста! Кладем на контактные площадки SMD компонент, обильно его смачиваем жидким флюсом, прикладываем жало паяльника к компоненту, припой с жала перетекает на контакты компонента и контактные площадки платы, убираем паяльник. Готово! Если компонент очень мелок или большой (жало не захватывает одновременно обе стороны) паяем каждую сторону отдельно, придерживая компонент пинцетом.
Если паяем микросхему, то технология такая. Позиционируем микросхему так, чтобы ножки попали на свои контактные площадки, обильно смачиваем места пайки флюсом, припаиваем одну крайнюю ножку, окончательно совмещаем ножки с площадками (припаянная ножка позволяет, в определенных пределах, «вертеть» корпус микросхемы), припаиваем еще одну ножку по диагонали, после этого микросхема надежно закреплена и можно спокойно пропаивать остальные ножки. Паяем не спеша, проводя жалом по всем ножкам микросхемы. Если образовались перемычки нужно очистить жало от избытка припоя, обильно смазать перемычки жидким флюсом и повторно пройтись по ножкам. Лишний припой заберется жалом — «сопли» устранятся.
042-Пайка SMD компонентов. : 52 комментария
и еще совет,2х выводные смд детали очень удобно снимать с помощью 2х паяльников, если не имеется специальный термопинцет:)
SMD — Surface Mounted Devices — Компоненты для поверхностного монтажа — так расшифровывается эта английская аббревиатура. Они обеспечивают более высокую по сравнению с традиционными деталями плотность монтажа. К тому же монтаж этих элементов, изготовление печатной платы оказываются более технологичными и дешевыми при массовом производстве, поэтому эти элементы получают все большее распространение и постепенно вытесняют классические детали с проволочными выводами.
Монтажу таких деталей посвящено немало статей в Интернете и в печатных изданиях, в своей статье про выбор главного инструмента я уже писал немного по этой теме. Сейчас хочу ее дополнить.
Надеюсь мой опус будет полезен для начинающих и для тех, кто пока с такими компонентами дела не имел.
Выход статьи приурочен к выпуску первого датагорского конструктора, где таких элементов 4 шт., а собственно процессор PCM2702 имеет супер-мелкие ноги. Поставляемая в комплекте печатная плата имеет паяльную маску, что облегчает пайку, однако не отменяет требований к аккуратности, отсутствию перегрева и статики.
Инструменты и материалы
Несколько слов про необходимые для этой цели инструменты и расходные материалы. Прежде всего это пинцет, острая иголка или шило, кусачки, припой, очень полезен бывает шприц с достаточно толстой иголкой для нанесения флюса. Поскольку сами детали очень мелкие, то обойтись без увеличительного стекла тоже бывает очень проблематично. Еще потребуется флюс жидкий, желательно нейтральный безотмывочный. На крайний случай подойдет и спиртовой раствор канифоли, но лучше все же воспользоваться специализированным флюсом, благо выбор их сейчас в продаже довольно широкий.
В любительских условиях удобнее всего такие детали паять при помощи специального паяльного фена или по другому — термовоздушной паяльной станцией. Выбор их сейчас в продаже довольно велик и цены, благодаря нашим китайским друзьям, тоже очень демократичные и доступны большинству радиолюбителей. Вот например такой образчик китайского производства с непроизносимым названием. Я такой станцией пользуюсь уже третий год. Пока полет нормальный.
Ну и конечно же, понадобится паяльник с тонким жалом. Лучше если это жало будет выполнено по технологии «Микроволна» разработанной немецкой фирмой Ersa. Оно отличается от обычного жала тем, что имеет небольшое углубление в котором скапливается капелька припоя. Такое жало делает меньше залипов при пайке близко расположенных выводов и дорожек. Настоятельно рекомендую найти и воспользоваться. Но если нет такого чудо-жала, то подойдет паяльник с обычным тонким наконечником.
В заводских условиях пайка SMD деталей производится групповым методом при помощи паяльной пасты. На подготовленную печатную плату на контактные площадки наносится тонкий слой специальной паяльной пасты. Делается это как правило методом шелкографии. Паяльная паста представляет собой мелкий порошок из припоя, перемешанный с флюсом. По консистенции он напоминает зубную пасту.
После нанесения паяльной пасты, робот раскладывает в нужные места необходимые элементы. Паяльная паста достаточно липкая, чтобы удержать детали. Потом плату загружают в печку и нагревают до температуры чуть выше температуры плавления припоя. Флюс испаряется, припой расплавляется и детали оказываются припаянными на свое место. Остается только дождаться охлаждения платы.
Вот эту технологию можно попробовать повторить в домашних условиях. Такую паяльную пасту можно приобрести в фирмах, занимающихся ремонтом сотовых телефонов. В магазинах торгующих радиодеталями, она тоже сейчас как правило есть в ассортименте, наряду с обычным припоем. В качестве дозатора для пасты я воспользовался тонкой иглой. Конечно это не так аккуратно, как делает к примеру фирма Asus когда изготовляет свои материнские платы, но тут уж как смог. Будет лучше, если эту паяльную пасту набрать в шприц и через иглу аккуратно выдавливать на контактные площадки. На фото видно, что я несколько переборщил плюхнув слишком много пасты, особенно слева.
Посмотрим, что из этого получится. На смазанные пастой контактные площадки укладываем детали. В данном случае это резисторы и конденсаторы. Вот тут пригодится тонкий пинцет. Удобнее, на мой взгляд, пользоваться пинцетом с загнутыми ножками.
Вместо пинцета некоторые пользуются зубочисткой, кончик которой для липкости чуть намазан флюсом. Тут полная свобода — кому как удобнее.
После того как детали заняли свое положение, можно начинать нагрев горячим воздухом. Температура плавления припоя (Sn 63%, Pb 35%, Ag 2%) составляет 178с*. Температуру горячего воздуха я выставил в 250с* и с расстояния в десяток сантиметров начинаю прогревать плату, постепенно опуская наконечник фена все ниже. Осторожнее с напором воздуха — если он будет очень сильным, то он просто сдует детали с платы. По мере прогрева, флюс начнет испаряться, а припой из темно-серого цвета начнет светлеть и в конце концов расплавится, растечется и станет блестящим. Примерно так как видно на следующем снимке.
После того как припой расплавился, наконечник фена медленно отводим подальше от платы, давая ей постепенно остыть. Вот что получилось у меня. По большим капелькам припоя у торцов элементов видно где я положил пасты слишком много, а где пожадничал.
Паяльная паста, вообще говоря, может оказаться достаточно дефицитной и дорогой. Если ее нет в наличии, то можно попробовать обойтись и без нее. Как это сделать рассмотрим на примере пайки микросхемы. Для начала все контактные площадки необходимо тщательно и толстым слоем облудить.
На фото, надеюсь видно, что припой на контактных площадках лежит такой невысокой горочкой. Главное чтобы он был распределен равномерно и его количество на всех площадках было одинаково. После этого все контактные площадки смачиваем флюсом и даем некоторое время подсохнуть, чтобы он стал более густым и липким и детали к нему прилипали. Аккуратно помещаем микросхему на предназначенное ей место. Тщательно совмещаем выводы микросхемы с контактными площадками.
Рядом с микросхемой я поместил несколько пассивных компонентов керамические и электролитический конденсаторы. Чтобы детали не сдувались напором воздуха нагревать начинаем свысока. Торопиться здесь не надо. Если большую сдуть достаточно сложно, то мелкие резисторы и конденсаторы запросто разлетаются кто куда.
Вот что получилось в результате. На фото видно, что конденсаторы припаялись как положено, а вот некоторые ножки микросхемы (24, 25 и 22 например) висят в воздухе. Проблема может быть или в неравномерном нанесении припоя на контактные площадки или в недостаточном количестве или качестве флюса. Исправить положение можно обычным паяльником с тонким жалом, аккуратно пропаяв подозрительные ножки. Чтобы заметить такие дефекты пайки необходимо увеличительное стекло.
Паяльная станция с горячим воздухом — это хорошо, скажете вы, но как быть тем, у кого ее нет, а есть только паяльник? При должной степени аккуратности SMD элементы можно припаивать и обычным паяльником. Чтобы проиллюстрировать эту возможность припаяем резисторы и пару микросхем без помощи фена одним только паяльником. Начнем с резистора. На предварительно облуженные и смоченные флюсом контактные площадки устанавливаем резистор. Чтобы он при пайке не сдвинулся с места и не прилип к жалу паяльника, его необходимо в момент пайки прижать к плате иголкой.
Потом достаточно прикоснуться жалом паяльника к торцу детали и контактной площадке и деталь с одной стороны окажется припаянной. С другой стороны припаиваем аналогично. Припоя на жале паяльника должно быть минимальное количество, иначе может получиться залипуха.
Вот что у меня получилось с пайкой резистора.
Качество не очень, но контакт надежный. Качество страдает из за того, что трудно одной рукой фиксировать иголкой резистор, второй рукой держать паяльник, а третьей рукой фотографировать.
Транзисторы и микросхемы стабилизаторов припаиваются аналогично. Я сначала припаиваю к плате теплоотвод мощного транзистора. Тут припоя не жалею. Капелька припоя должна затечь под основание транзистора и обеспечить не только надежный электрический контакт, но и надежный тепловой контакт между основанием транзистора и платой, которая играет роль радиатора.
Во время пайки можно иголкой слегка пошевелить транзистор, чтобы убедиться что весь припой под основанием расплавился и транзистор как бы плавает на капельке припоя. К тому же лишний припой из под основания при этом выдавится наружу, улучшив тепловой контакт. Вот так выглядит припаянная микросхема интегрального стабилизатора на плате.
Теперь надо перейти к более сложной задаче — пайке микросхемы. Первым делом, опять производим точное позиционирование ее на контактных площадках. Потом слегка «прихватываем» один из крайних выводов.
После этого нужно снова проверить правильность совпадения ножек микросхемы и контактных площадок. После этого таким же образом прихватываем остальные крайние выводы.
Теперь микросхема никуда с платы не денется. Осторожно, по одной припаиваем все остальные выводы, стараясь не посадить перемычку между ножками микросхемы.
Вот тут то нам очень пригодится жало «микроволна» о котором я упоминал вначале. С его помощью можно производить пайку многовыводных микросхем, просто проводя жалом вдоль выводов. Залипов практически не бывает и на пайку одной стороны с полусотней выводов с шагом 0,5 мм уходит всего минута. Если же такого волшебного жала у вас нет, то просто старайтесь делать все как можно аккуратнее.
Что же делать, если несколько ножек микросхемы оказались залиты одной каплей припоя и устранить этот залип паяльником не удается?
Тут на помощь придет кусочек оплетки от экранированного кабеля. Оплетку пропитываем флюсом. Затем прикладываем ее к заляпухе и нагреваем паяльником.
Оплетка как губка впитает в себя лишний припой и освободит от замыкания ножки микросхемы. Видно, что на выводах остался минимум припоя, который равномерно залил ножки микросхемы.
Надеюсь, я не утомил вас своей писаниной, и не сильно расстроил качеством фотографий и полученных результатов пайки. Может кому-нибудь этот материал окажется полезным. Удачи!
С уважением, Тимошкин Александр (TANk)
С паяльником с детства. По этой причине попал в спецшколу, где вместо уроков труда в старших классах были уроки радиоэлектроники.
Потом физфак университета. Работа технологом в цехе микроэлектроники на оборонном заводе, пока завод не развалили.
Потом преподавал всяческую физику в университете. И вот уже лет двадцать — лужу паяю, компы починяю.
Самодельное приспособление для демонтажа SMD без фена
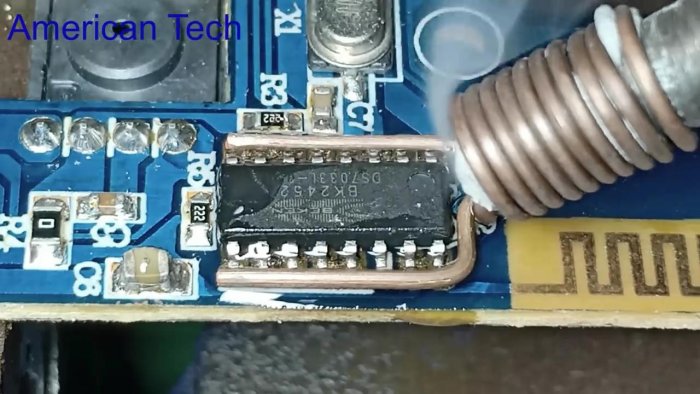
Электронные компоненты поверхностного монтажа, в отличие от традиционных радиодеталей, не имеют гибких выводов. Пассивные элементы изготавливаются в виде цилиндра или параллелепипеда с металлизированными торцами. У микросхем, где выводов много, электроды короткие и жесткие, их нельзя изгибать.
Для снятия с платы припаянной SMD-детали не выйдет нагревать паяльником и отделять по очереди каждый вывод, чтобы отогнуть его от контактной площадки. Поэтому место пайки обдувают горячим воздухом из фена, нагревая все выводы одновременно до расплавления припоя и освобождения детали. Если оказалось, что в нужный момент фена с собой нет, можно, как временную меру, использовать самодельную насадку, устанавливаемую на жало любого паяльника.
Материалы и инструменты
Приспособление изготавливается обычными инструментами. Понадобятся:
- паяльник;
- пассатижи;
- кусачки;
- пинцет.
Используемые материалы часто применяются в обычной практике и добыть их не составит труда:
- Медная проволока без изоляции, диаметром 1÷2 мм. Если есть выбор, лучше взять более жесткую, чтобы она сохраняла форму изгиба.
- Термопаста, уложенная на жало до намотки, способствует передаче тепла.
- Жидкий или гелеобразный неактивный флюс, нанесенный на контакты перед отпайкой, улучшит равномерность прогрева и распределения тепла. Растворит образовавшийся окисел.
- Свинцово-оловянный проволочный припой. Поможет распределить нагрев, сделав его одинаковым, между большим количеством выводов.
Изготовление насадки
На кончик жала нанести немного термопасты, аккуратно распределяя ее равномерно на участке, где будут уложены витки насадки. Толщина слоя примерно равна половине диаметра используемой проволоки.
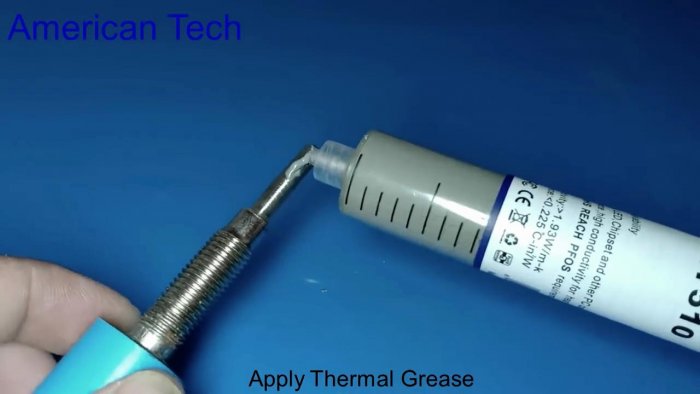
Взять медную проволоку и расположить ее поперек жала в месте начала намотки.
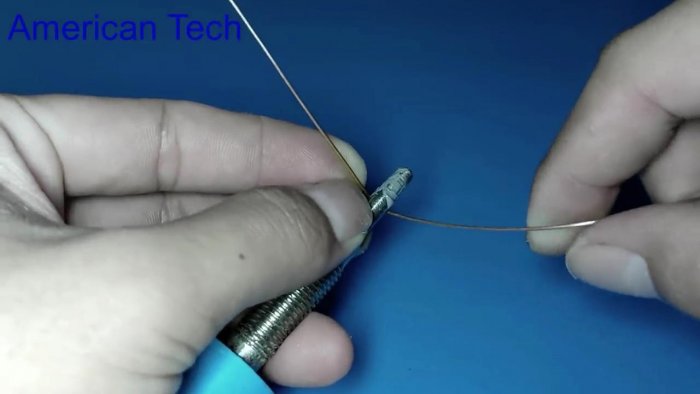
Ближним концом проволоки сделать 2÷3 витка, утапливая их термопасте и плотно укладывая в направлении к концу жала.
Дальний конец проволоки уложить поперек начальной обмотки, после чего продолжить укладку витков ближним концом, плотно зажимая провод к жалу.
Сделав еще 5÷6 оборотов, ближний и дальний конец проволоки туго скрутить между собой несколько раз. Плотная навивка надежно закрепит насадку на жале. Все витки должны быть погружены в пасту.
Кусачками обрезать концы получившейся рогатки, оставив от развилки длину 5 мм.
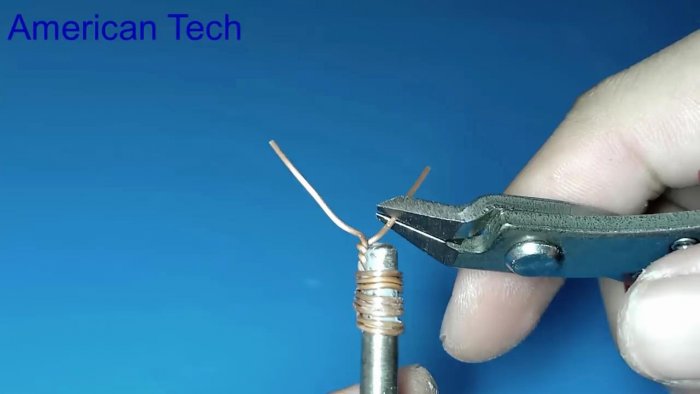
Пассатижами придать концам вилкообразную форму с расстоянием, равным длине элемента между металлизированными площадками.
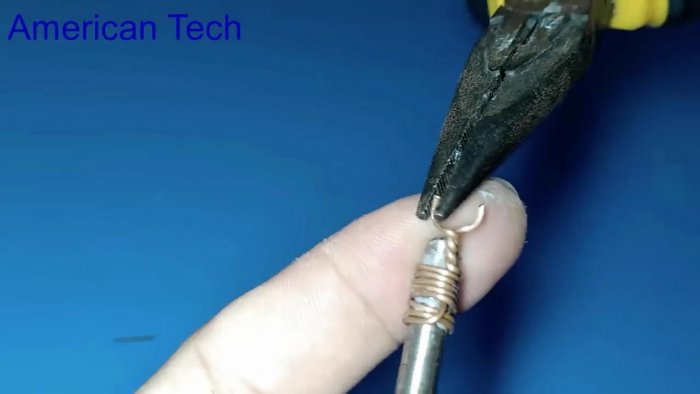
Демонтаж резисторов, конденсаторов, диодов
При помощи палочки нанести на контактные площадки небольшое количество флюса.
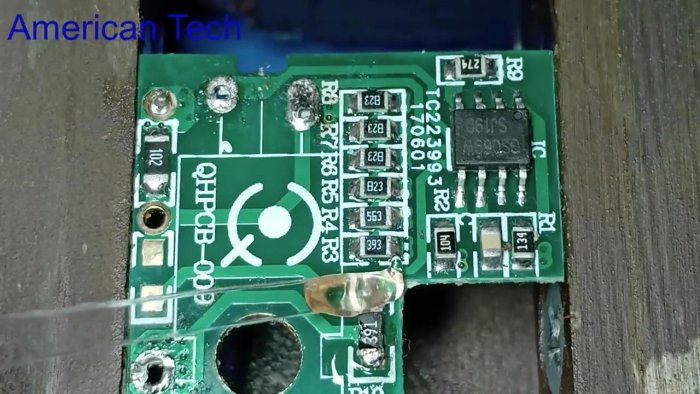
Прикоснуться к контактным площадкам детали разогнутыми на необходимое расстояние медными концами насадки.
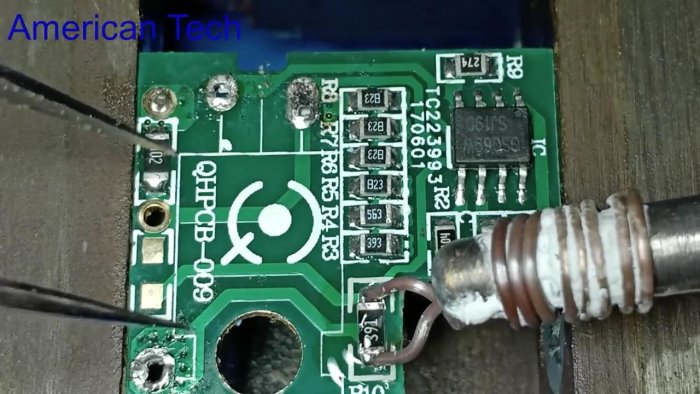
Флюс закипает с небольшим выделением дыма, припой расплавляется, освобождая выводы.
Пинцетом снять отпаянную деталь с платы.

Также выпаиваем все остальные компоненты соответствующих габаритов.
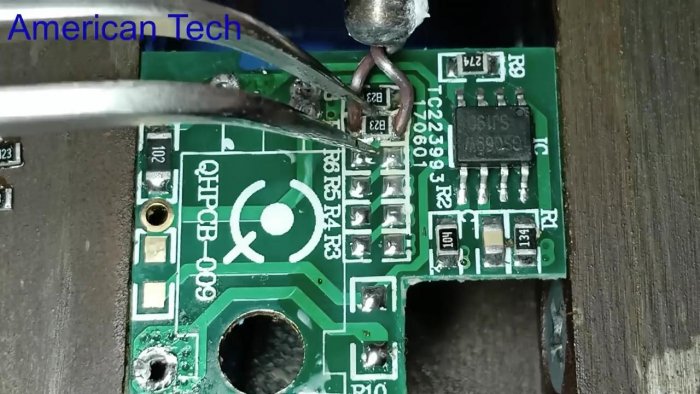
Выпаивание микросхем
Элементы с большим количеством выводов выпаивают насадкой, сделанной по такому же принципу, но рожки обрезаются по расстоянию между крайними в ряду контактами. Размер и форма вилки зависят от конкретной микросхемы.
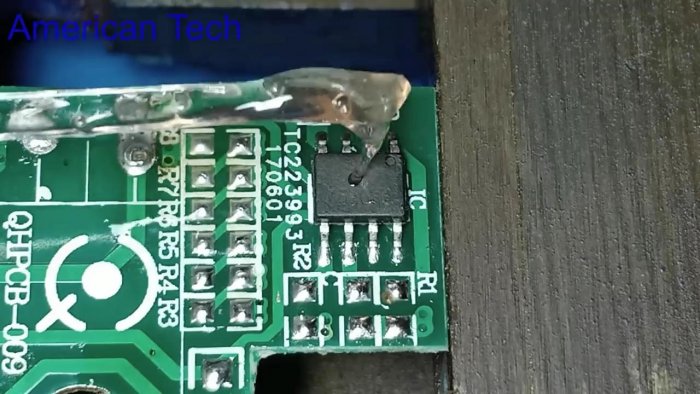
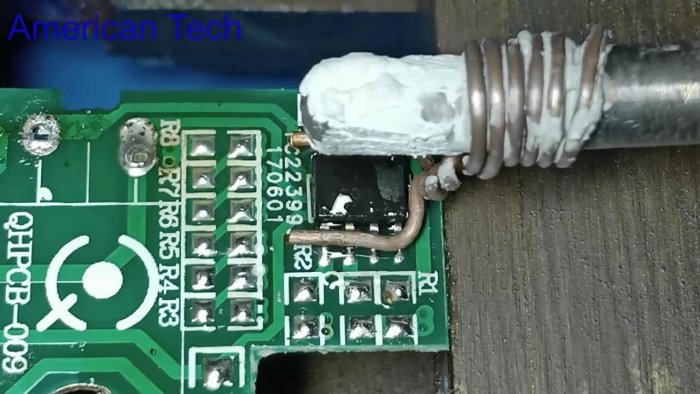
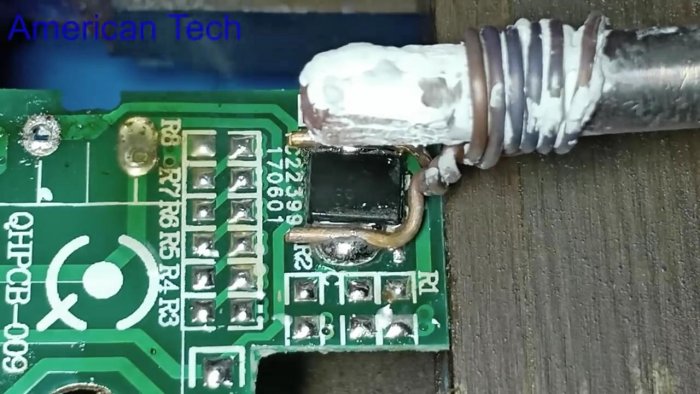
Микросхема на 8 выводов выпаивается вилкой своего вида.
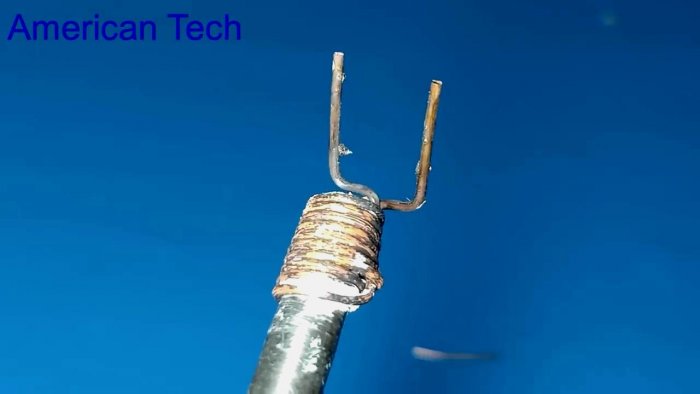
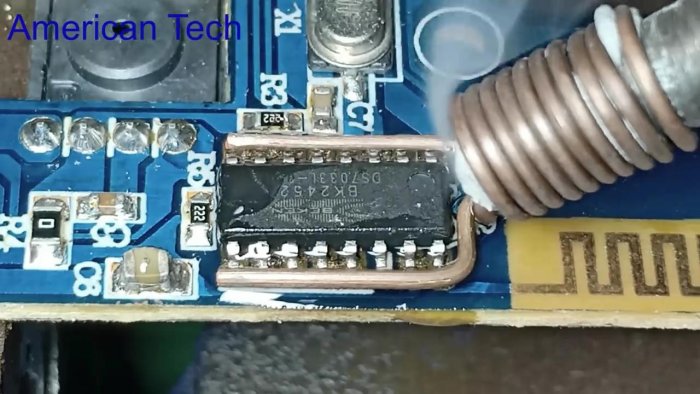
Заливание расплавленным проволочным припоем пространства между выводами, обеспечит равномерное распределение тепла и одинаковый нагрев всех контактов.
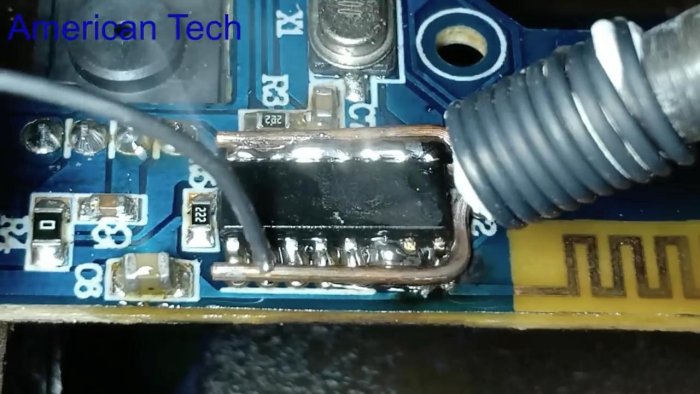
Микросхема свободно снимается с платы после расплавления припоя.
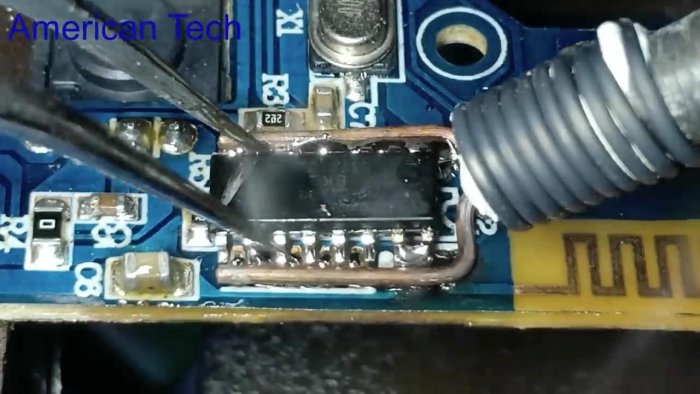
Расплавленные излишки припоя удаляются с контактных площадок.
Изменив размеры вилки выпаивают микросхему с 16-ю выводами. Порядок действий соответствует описанному.
Аналогичен демонтаж корпуса с 42-мя ножками.
Для изготовления приспособы берем более толстую проводу, для более дальнего распределения тепла.
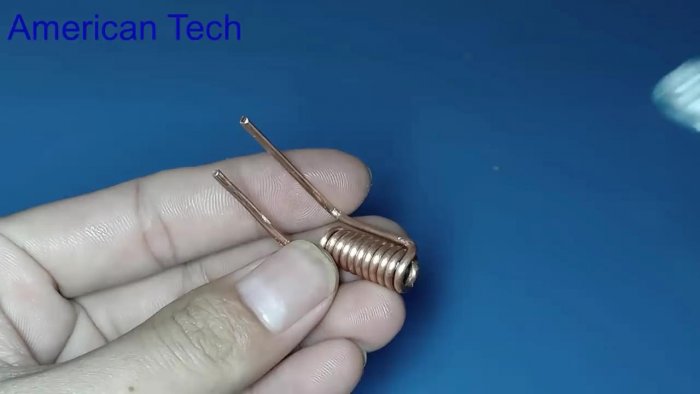
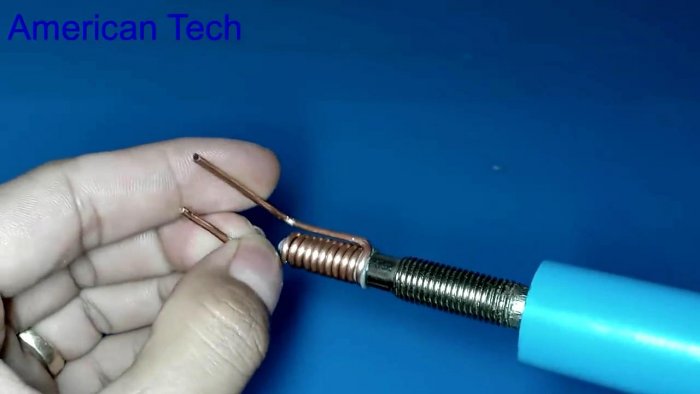
И по той же технологии выпаиваем.
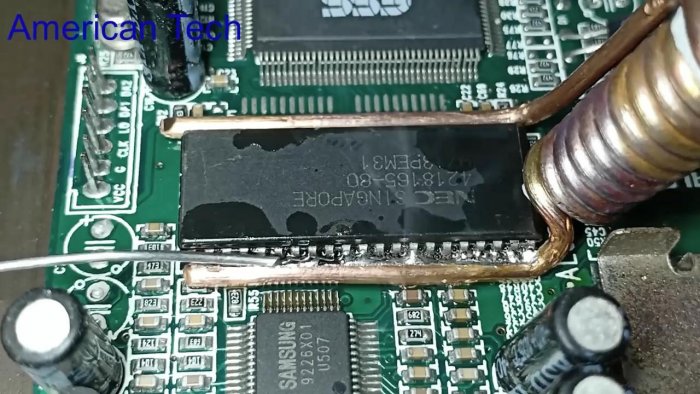
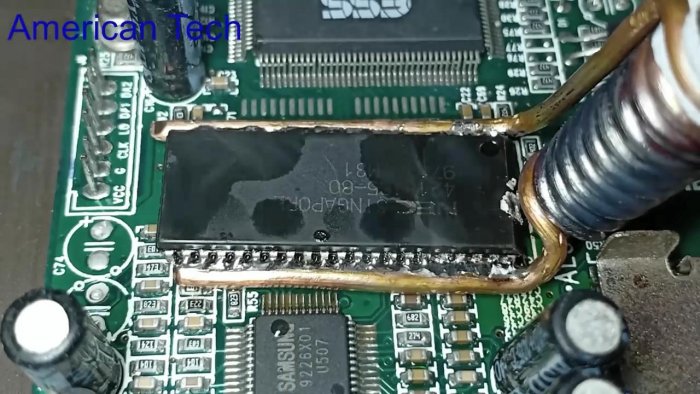
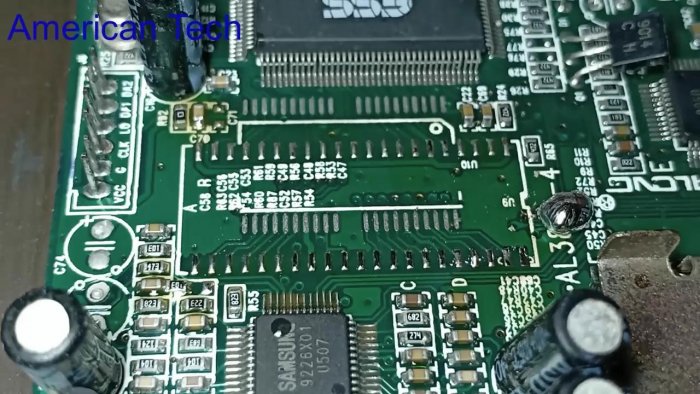
Выводы схемы в квадратном корпусе с 26-ю контактами с каждой стороны смазываются флюсом.
Вместо формы вилки, проволочные усики нужной длины изгибаются, образуя квадратную рамку и процедура повторяется.
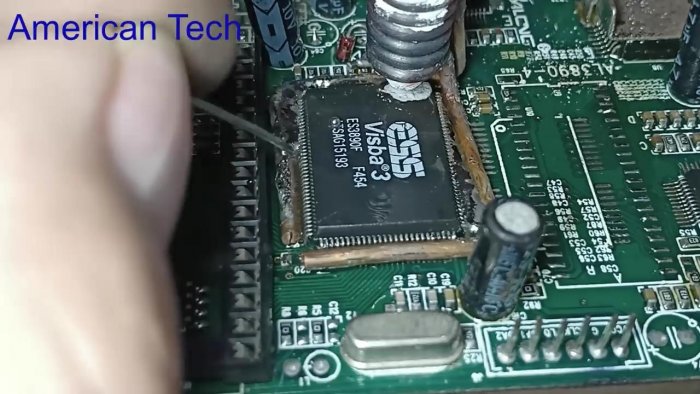
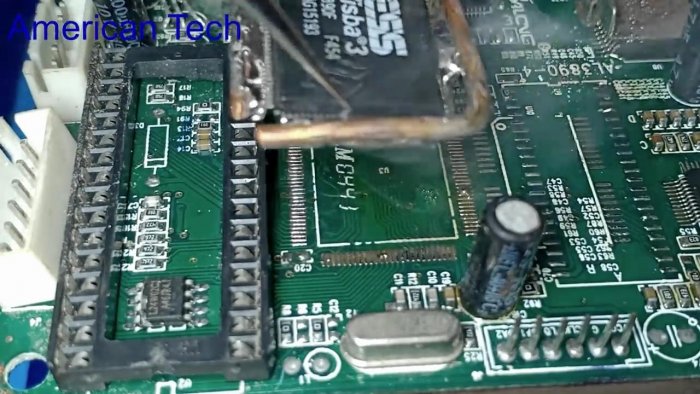
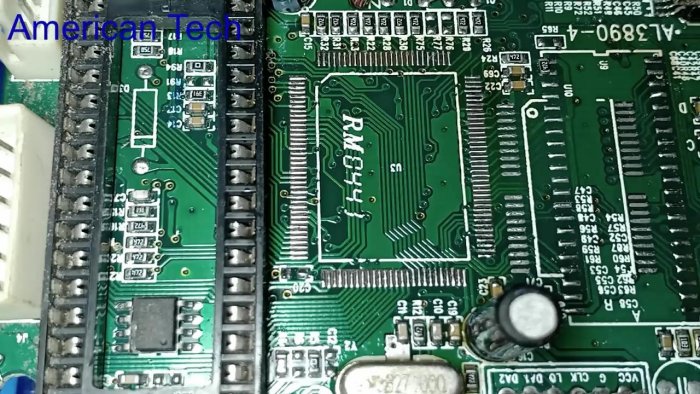
Замена термопасты
Теплопроводящая паста работает при температуре до 250 градусов Цельсия. Перегреваясь, она сохнет, теряет свойства и не передает тепло жала насадке. После выпаивания 2÷3 деталей вилка плохо греет.
- Если нужно продолжать демонтаж — снять использованную насадку.
- Вытереть жало от засохшей пасты, нанести свежую порцию.
- На жало одеть новую насадку, которую можно изготовить заранее.
Рекомендации по использованию
В качестве жидкого флюса удобно использовать самодельный раствор одной части размельченной в пыль сосновой канифоли в трех частях медицинского спирта.
Быстрое выгорание флюса с обильным задымлением свидетельствует о слишком большом нагреве паяльника.
Нужно помнить о правилах работы с горячим паяльником, чтобы избежать электрических травм или ожогов, обеспечить проветривание помещения.
Смотрите видео
Пайка SMD деталей в домашних условиях
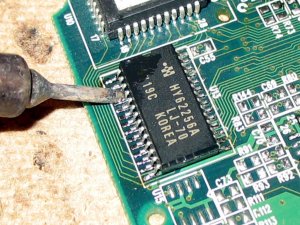
SMD — Surface Mounted Devices — Компоненты для поверхностного монтажа — так расшифровывается эта английская аббревиатура. Они обеспечивают более высокую по сравнению с традиционными деталями плотность монтажа. К тому же монтаж этих элементов, изготовление печатной платы оказываются более технологичными и дешевыми при массовом производстве, поэтому эти элементы получают все большее распространение и постепенно вытесняют классические детали с проволочными выводами.
Надеюсь мой опус будет полезен для начинающих и для тех, кто пока с такими компонентами дела не имел.
Выход статьи приурочен к выпуску первого датагорского конструктора, где таких элементов 4 шт., а собственно процессор PCM2702 имеет супер-мелкие ноги. Поставляемая в комплекте печатная плата имеет паяльную маску, что облегчает пайку, однако не отменяет требований к аккуратности, отсутствию перегрева и статики.
Инструменты и материалы
Несколько слов про необходимые для этой цели инструменты и расходные материалы. Прежде всего это пинцет, острая иголка или шило, кусачки, припой, очень полезен бывает шприц с достаточно толстой иголкой для нанесения флюса. Поскольку сами детали очень мелкие, то обойтись без увеличительного стекла тоже бывает очень проблематично. Еще потребуется флюс жидкий, желательно нейтральный безотмывочный. На крайний случай подойдет и спиртовой раствор канифоли, но лучше все же воспользоваться специализированным флюсом, благо выбор их сейчас в продаже довольно широкий.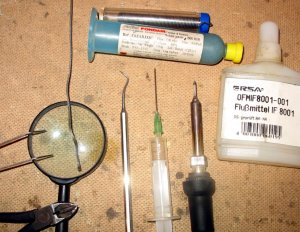
В любительских условиях удобнее всего такие детали паять при помощи специального паяльного фена или по другому — термовоздушной паяльной станцией. Выбор их сейчас в продаже довольно велик и цены, благодаря нашим китайским друзьям, тоже очень демократичные и доступны большинству радиолюбителей. Вот например такой образчик китайского производства с непроизносимым названием. Я такой станцией пользуюсь уже третий год. Пока полет нормальный.
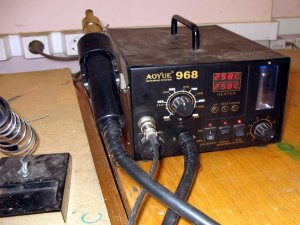
Ну и конечно же, понадобится паяльник с тонким жалом. Лучше если это жало будет выполнено по технологии «Микроволна» разработанной немецкой фирмой Ersa. Оно отличается от обычного жала тем, что имеет небольшое углубление в котором скапливается капелька припоя. Такое жало делает меньше залипов при пайке близко расположенных выводов и дорожек. Настоятельно рекомендую найти и воспользоваться. Но если нет такого чудо-жала, то подойдет паяльник с обычным тонким наконечником.
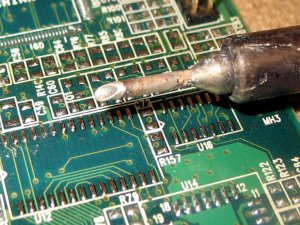
В заводских условиях пайка SMD деталей производится групповым методом при помощи паяльной пасты. На подготовленную печатную плату на контактные площадки наносится тонкий слой специальной паяльной пасты. Делается это как правило методом шелкографии. Паяльная паста представляет собой мелкий порошок из припоя, перемешанный с флюсом. По консистенции он напоминает зубную пасту.
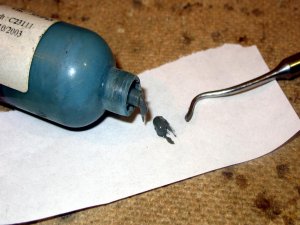
После нанесения паяльной пасты, робот раскладывает в нужные места необходимые элементы. Паяльная паста достаточно липкая, чтобы удержать детали. Потом плату загружают в печку и нагревают до температуры чуть выше температуры плавления припоя. Флюс испаряется, припой расплавляется и детали оказываются припаянными на свое место. Остается только дождаться охлаждения платы.
Вот эту технологию можно попробовать повторить в домашних условиях. Такую паяльную пасту можно приобрести в фирмах, занимающихся ремонтом сотовых телефонов. В магазинах торгующих радиодеталями, она тоже сейчас как правило есть в ассортименте, наряду с обычным припоем. В качестве дозатора для пасты я воспользовался тонкой иглой. Конечно это не так аккуратно, как делает к примеру фирма Asus когда изготовляет свои материнские платы, но тут уж как смог. Будет лучше, если эту паяльную пасту набрать в шприц и через иглу аккуратно выдавливать на контактные площадки. На фото видно, что я несколько переборщил плюхнув слишком много пасты, особенно слева.
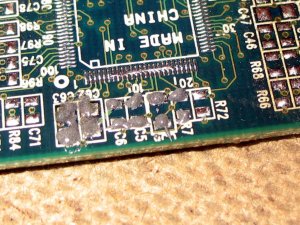
Посмотрим, что из этого получится. На смазанные пастой контактные площадки укладываем детали. В данном случае это резисторы и конденсаторы. Вот тут пригодится тонкий пинцет. Удобнее, на мой взгляд, пользоваться пинцетом с загнутыми ножками.
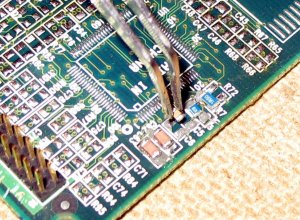
Вместо пинцета некоторые пользуются зубочисткой, кончик которой для липкости чуть намазан флюсом. Тут полная свобода — кому как удобнее.
После того как детали заняли свое положение, можно начинать нагрев горячим воздухом. Температура плавления припоя (Sn 63%, Pb 35%, Ag 2%) составляет 178с*. Температуру горячего воздуха я выставил в 250с* и с расстояния в десяток сантиметров начинаю прогревать плату, постепенно опуская наконечник фена все ниже. Осторожнее с напором воздуха — если он будет очень сильным, то он просто сдует детали с платы. По мере прогрева, флюс начнет испаряться, а припой из темно-серого цвета начнет светлеть и в конце концов расплавится, растечется и станет блестящим. Примерно так как видно на следующем снимке.
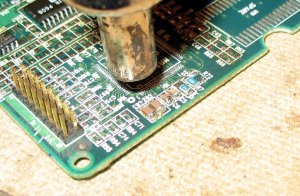
После того как припой расплавился, наконечник фена медленно отводим подальше от платы, давая ей постепенно остыть. Вот что получилось у меня. По большим капелькам припоя у торцов элементов видно где я положил пасты слишком много, а где пожадничал.
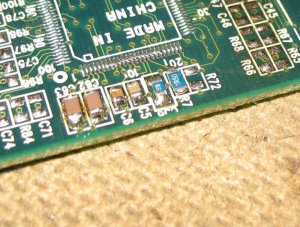
Паяльная паста, вообще говоря, может оказаться достаточно дефицитной и дорогой. Если ее нет в наличии, то можно попробовать обойтись и без нее. Как это сделать рассмотрим на примере пайки микросхемы. Для начала все контактные площадки необходимо тщательно и толстым слоем облудить.
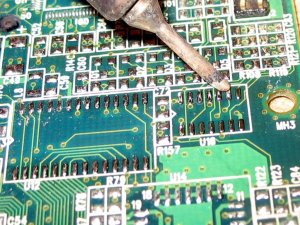
На фото, надеюсь видно, что припой на контактных площадках лежит такой невысокой горочкой. Главное чтобы он был распределен равномерно и его количество на всех площадках было одинаково. После этого все контактные площадки смачиваем флюсом и даем некоторое время подсохнуть, чтобы он стал более густым и липким и детали к нему прилипали. Аккуратно помещаем микросхему на предназначенное ей место. Тщательно совмещаем выводы микросхемы с контактными площадками.
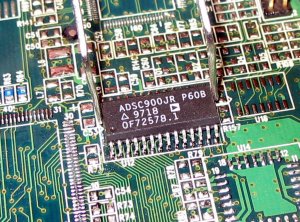
Рядом с микросхемой я поместил несколько пассивных компонентов керамические и электролитический конденсаторы. Чтобы детали не сдувались напором воздуха нагревать начинаем свысока. Торопиться здесь не надо. Если большую сдуть достаточно сложно, то мелкие резисторы и конденсаторы запросто разлетаются кто куда.
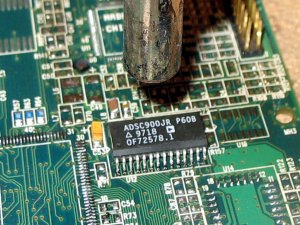
Вот что получилось в результате. На фото видно, что конденсаторы припаялись как положено, а вот некоторые ножки микросхемы (24, 25 и 22 например) висят в воздухе. Проблема может быть или в неравномерном нанесении припоя на контактные площадки или в недостаточном количестве или качестве флюса. Исправить положение можно обычным паяльником с тонким жалом, аккуратно пропаяв подозрительные ножки. Чтобы заметить такие дефекты пайки необходимо увеличительное стекло.
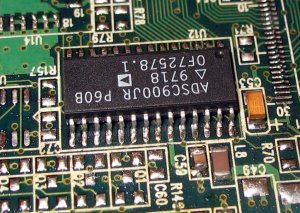
Паяльная станция с горячим воздухом — это хорошо, скажете вы, но как быть тем, у кого ее нет, а есть только паяльник? При должной степени аккуратности SMD элементы можно припаивать и обычным паяльником. Чтобы проиллюстрировать эту возможность припаяем резисторы и пару микросхем без помощи фена одним только паяльником. Начнем с резистора. На предварительно облуженные и смоченные флюсом контактные площадки устанавливаем резистор. Чтобы он при пайке не сдвинулся с места и не прилип к жалу паяльника, его необходимо в момент пайки прижать к плате иголкой.
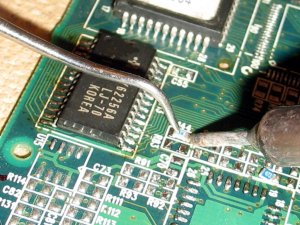
Потом достаточно прикоснуться жалом паяльника к торцу детали и контактной площадке и деталь с одной стороны окажется припаянной. С другой стороны припаиваем аналогично. Припоя на жале паяльника должно быть минимальное количество, иначе может получиться залипуха.
Вот что у меня получилось с пайкой резистора.
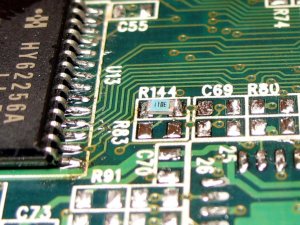
Качество не очень, но контакт надежный. Качество страдает из за того, что трудно одной рукой фиксировать иголкой резистор, второй рукой держать паяльник, а третьей рукой фотографировать.
Транзисторы и микросхемы стабилизаторов припаиваются аналогично. Я сначала припаиваю к плате теплоотвод мощного транзистора. Тут припоя не жалею. Капелька припоя должна затечь под основание транзистора и обеспечить не только надежный электрический контакт, но и надежный тепловой контакт между основанием транзистора и платой, которая играет роль радиатора.
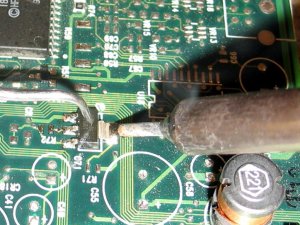
Во время пайки можно иголкой слегка пошевелить транзистор, чтобы убедиться что весь припой под основанием расплавился и транзистор как бы плавает на капельке припоя. К тому же лишний припой из под основания при этом выдавится наружу, улучшив тепловой контакт. Вот так выглядит припаянная микросхема интегрального стабилизатора на плате.
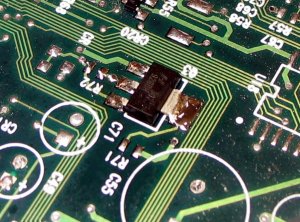
Теперь надо перейти к более сложной задаче — пайке микросхемы. Первым делом, опять производим точное позиционирование ее на контактных площадках. Потом слегка «прихватываем» один из крайних выводов.
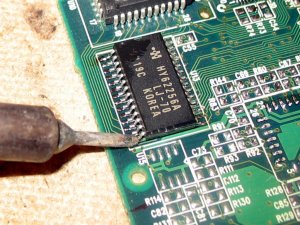
После этого нужно снова проверить правильность совпадения ножек микросхемы и контактных площадок. После этого таким же образом прихватываем остальные крайние выводы.
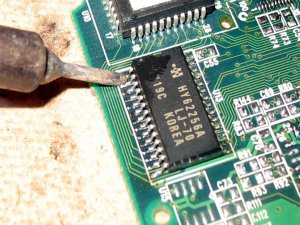
Теперь микросхема никуда с платы не денется. Осторожно, по одной припаиваем все остальные выводы, стараясь не посадить перемычку между ножками микросхемы.
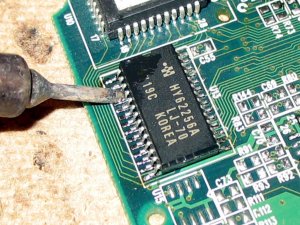
Вот тут то нам очень пригодится жало «микроволна» о котором я упоминал вначале. С его помощью можно производить пайку многовыводных микросхем, просто проводя жалом вдоль выводов. Залипов практически не бывает и на пайку одной стороны с полусотней выводов с шагом 0,5 мм уходит всего минута. Если же такого волшебного жала у вас нет, то просто старайтесь делать все как можно аккуратнее.

Что же делать, если несколько ножек микросхемы оказались залиты одной каплей припоя и устранить этот залип паяльником не удается?
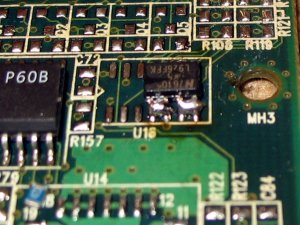
Тут на помощь придет кусочек оплетки от экранированного кабеля. Оплетку пропитываем флюсом. Затем прикладываем ее к заляпухе и нагреваем паяльником.

Оплетка как губка впитает в себя лишний припой и освободит от замыкания ножки микросхемы. Видно, что на выводах остался минимум припоя, который равномерно залил ножки микросхемы.
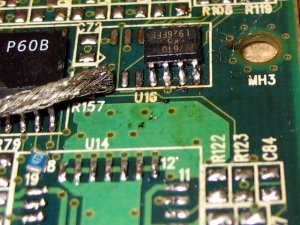
Надеюсь, я не утомил вас своей писаниной, и не сильно расстроил качеством фотографий и полученных результатов пайки. Может кому-нибудь этот материал окажется полезным. Удачи!
С уважением, Тимошкин Александр (TANk)
Камрад, смотри полезняхи!

Александр (TANk)
РФ, г.Ижевск
С паяльником с детства. По этой причине попал в спецшколу, где вместо уроков труда в старших классах были уроки радиоэлектроники.Потом физфак университета. Работа технологом в цехе микроэлектроники на оборонном заводе, пока завод не развалили.
Потом преподавал всяческую физику в университете. И вот уже лет двадцать — лужу паяю, компы починяю.
Быстрая распайка SMD компонентов с помощью утюга
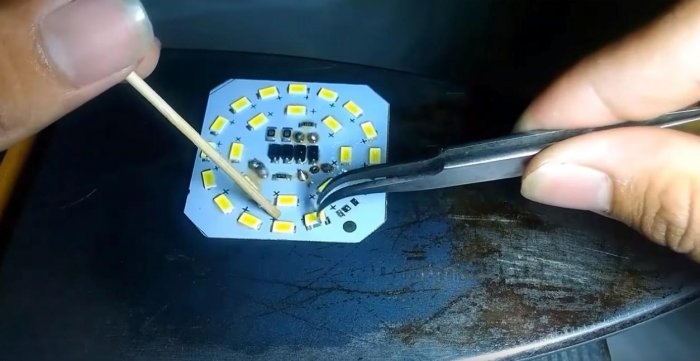
Все чаще применяются SMD детали в производстве, а так же среди радиолюбителей. Работать с ними удобней, так как сверлить отверстия для выводов не нужно, а устройства получаются очень миниатюрными.
SMD компоненты вполне можно использовать и повторно. Тут опять появляется очевидное превосходство поверхностного монтажа, потому что выпаивать мелкие детали гораздо проще. Их очень просто сдувать специальным паяльным феном с платы. Но если у вас такого не окажется под рукой, то вас выручит обычный бытовой утюг.
Демонтаж SMD деталей
Итак, у меня сгорела светодиодная лампа, и я не буду её чинить. Я её распаяю на детали для будущих своих самоделок.
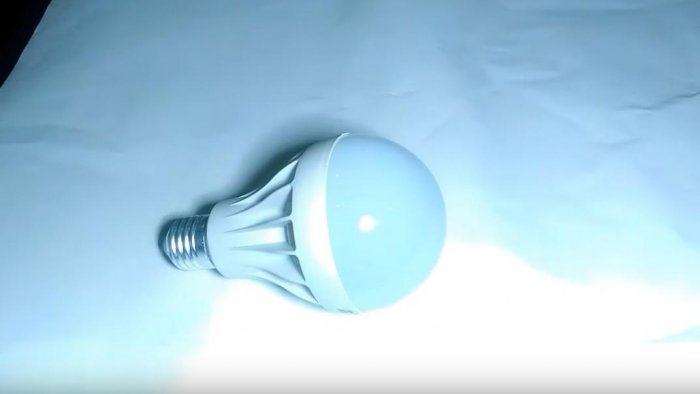
Разбираем лампочку, снимаем верхний колпак.
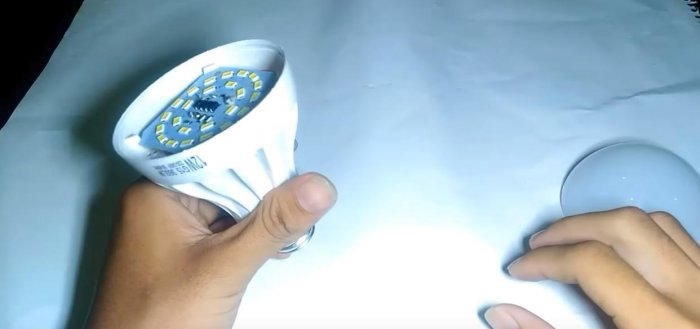
Вытаскиваем плату из основания цоколя.
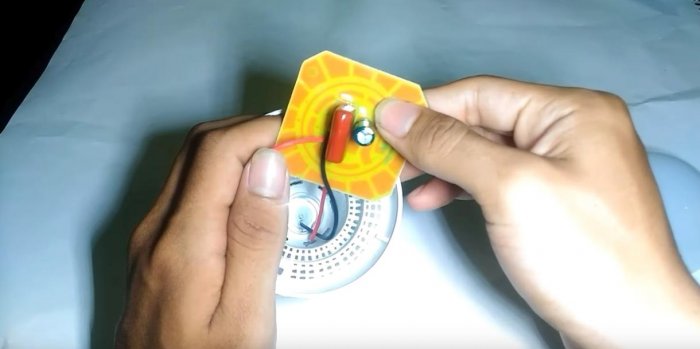
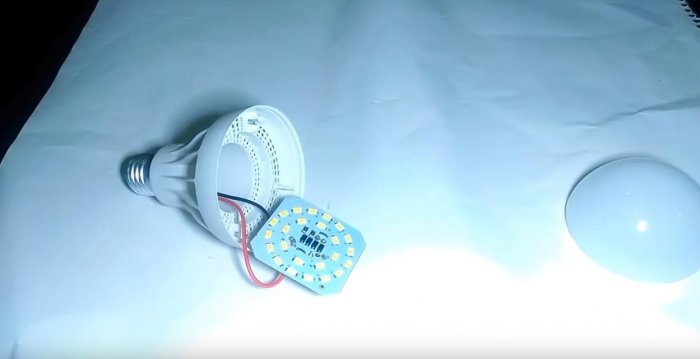
Отпаиваем навесные компоненты и детали, провода. В общем должна быть плата только с SMD деталями.
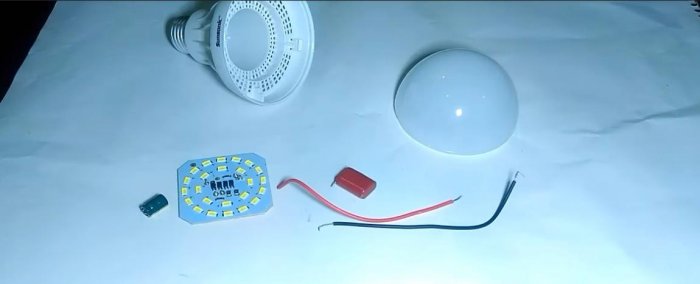
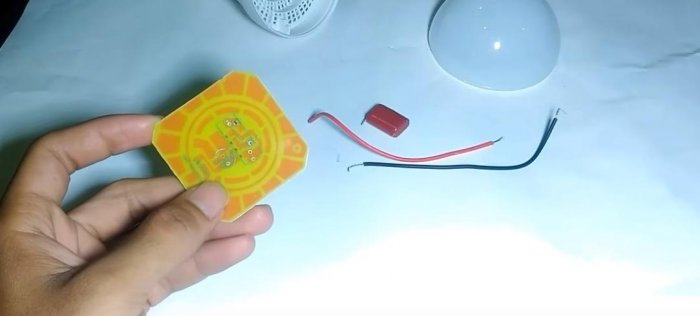
Закрепляем утюг вверх тормашками. Делать это нужно жестко, чтобы он в процессе пайки не опрокинулся.
Использование утюга ещё хорошо тем, что в нем есть регулятор, который будет довольно точно поддерживать установленную температуру поверхности подошвы. Это огромный плюс, так как поверхностные компоненты очень боятся перегрева.
Выставляем температуру около 180 градусов Цельсия. Это второй режим глажки белья, если мне не изменяет моя память. Если пайка не пойдет — постепенно увеличивайте температуру.
Кладем плату от лампочки на подошву перевернутого утюга.
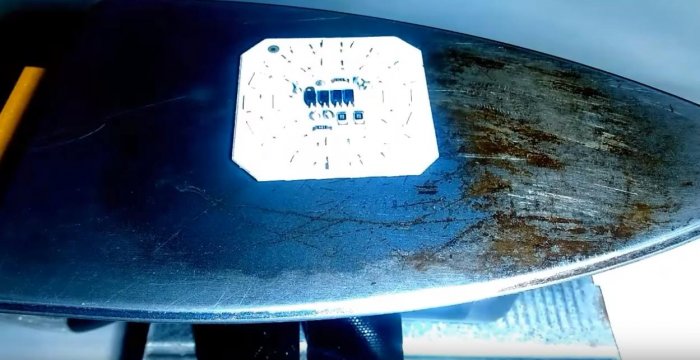
Ждем 15-20 секунд пока плата прогреется. В это время смачиваем флюсом каждую детальку. Флюс не даст перегрева, это будет своеобразный помощник при распайки. С ним все элементы снимаются без труда.
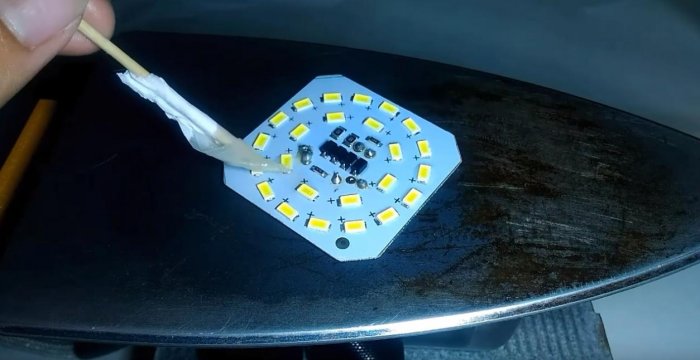
Как только все хорошо разогреется, все детали можно смахнуть с платы, ударив плату о какую-нибудь поверхность. Но я сделаю все аккуратно. Для этого возьмем деревянную палочку для удержания платы на месте и с помощью пинцета будем отсоединять каждый компонент платы.
Голая плата в конце работы:
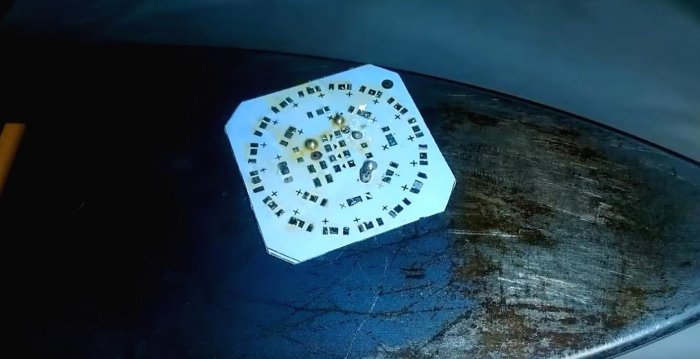
Выпаянные детали:
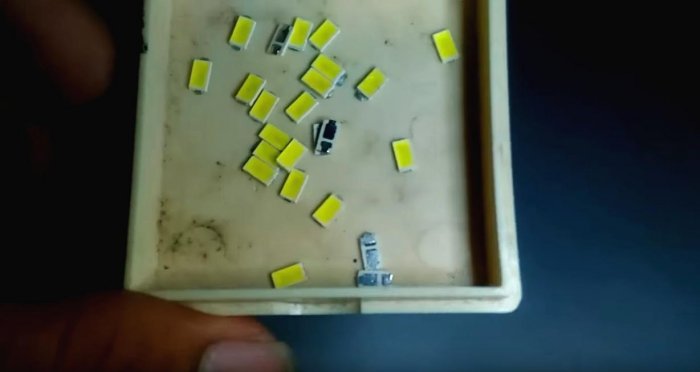
Все рабочее, ничего не пережег.
Что можно из них сделать? Решать конечно же вам!
Я сделаю фонарик на батарейку типа Крона.
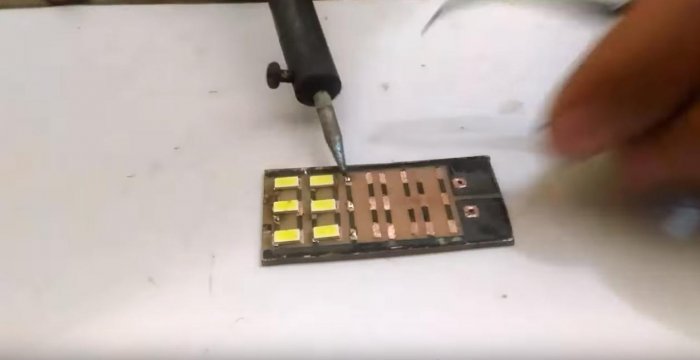
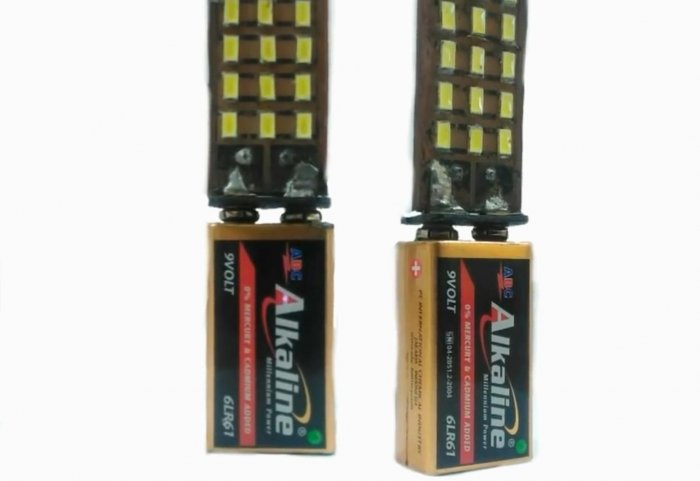
Этот способ позволит вам очень быстро распаивать любые платы с SMD деталями. Берите на вооружение друзья!