Индукционный нагрев, основные принципы и технологии.
1 августа 2013
Индукционный нагрев (Induction Heating) — метод бесконтактного нагрева токами высокой частоты (англ. RFH — radio-frequency heating, нагрев волнами радиочастотного диапазона) электропроводящих материалов.Описание метода.
Индукционный нагрев — это нагревание материалов электрическими токами, которые индуцируются переменным магнитным полем. Следовательно — это нагрев изделий из проводящих материалов (проводников) магнитным полем индукторов (источников переменного магнитного поля). Индукционный нагрев проводится следующим образом. Электропроводящая (металлическая, графитовая) заготовка помещается в так называемый индуктор, представляющий собой один или несколько витков провода (чаще всего медного). В индукторе с помощью специального генератора наводятся мощные токи различной частоты (от десятка Гц до нескольких МГц), в результате чего вокруг индуктора возникает электромагнитное поле. Электромагнитное поле наводит в заготовке вихревые токи. Вихревые токи разогревают заготовку под действием джоулева тепла (см. закон Джоуля-Ленца).
Система «индуктор-заготовка» представляет собой бессердечниковый трансформатор, в котором индуктор является первичной обмоткой. Заготовка является вторичной обмоткой, замкнутой накоротко. Магнитный поток между обмотками замыкается по воздуху.
На высокой частоте вихревые токи вытесняются образованным ими же магнитным полем в тонкие поверхностные слои заготовки Δ (Поверхностный-эффект), в результате чего их плотность резко возрастает, и заготовка разогревается. Нижерасположенные слои металла прогреваются за счёт теплопроводности. Важен не ток, а большая плотность тока. В скин-слое Δ плотность тока уменьшается в e раз относительно плотности тока на поверхности заготовки, при этом в скин-слое выделяется 86,4 % тепла (от общего тепловыделения. Глубина скин-слоя зависит от частоты излучения: чем выше частота, тем тоньше скин-слой. Также она зависит от относительной магнитной проницаемости μ материала заготовки.
Для железа, кобальта, никеля и магнитных сплавов при температуре ниже точки Кюри μ имеет величину от нескольких сотен до десятков тысяч. Для остальных материалов (расплавы, цветные металлы, жидкие легкоплавкие эвтектики, графит, электролиты, электропроводящая керамика и т. д.) μ примерно равна единице.
Например, при частоте 2 МГц глубина скин-слоя для меди около 0,25 мм, для железа ≈ 0,001 мм.
Индуктор сильно нагревается во время работы, так как сам поглощает собственное излучение. К тому же он поглощает тепловое излучение от раскалённой заготовки. Делают индукторы из медных трубок, охлаждаемых водой. Вода подаётся отсасыванием — этим обеспечивается безопасность в случае прожога или иной разгерметизации индуктора.
Применение:
Сверхчистая бесконтактная плавка, пайка и сварка металла.
Получение опытных образцов сплавов.
Гибка и термообработка деталей машин.
Ювелирное дело.
Обработка мелких деталей, которые могут повредиться при газопламенном или дуговом нагреве.
Поверхностная закалка.
Закалка и термообработка деталей сложной формы.
Обеззараживание медицинского инструмента.
Преимущества.
Высокоскоростной разогрев или плавление любого электропроводящего материала.
Возможен нагрев в атмосфере защитного газа, в окислительной (или восстановительной) среде, в непроводящей жидкости, в вакууме.
Нагрев через стенки защитной камеры, изготовленной из стекла, цемента, пластмасс, дерева — эти материалы очень слабо поглощают электромагнитное излучение и остаются холодными при работе установки. Нагревается только электропроводящий материал — металл (в том числе расплавленный), углерод, проводящая керамика, электролиты, жидкие металлы и т. п.
За счёт возникающих МГД усилий происходит интенсивное перемешивание жидкого металла, вплоть до удержания его в подвешенном состоянии в воздухе или защитном газе — так получают сверхчистые сплавы в небольших количествах (левитационная плавка, плавка в электромагнитном тигле).
Поскольку разогрев ведётся посредством электромагнитного излучения, отсутствует загрязнение заготовки продуктами горения факела в случае газопламенного нагрева, или материалом электрода в случае дугового нагрева. Помещение образцов в атмосферу инертного газа и высокая скорость нагрева позволят ликвидировать окалинообразование.
Удобство эксплуатации за счёт небольшого размера индуктора.
Индуктор можно изготовить особой формы — это позволит равномерно прогревать по всей поверхности детали сложной конфигурации, не приводя к их короблению или локальному непрогреву.
Легко провести местный и избирательный нагрев.
Так как наиболее интенсивно разогрев идет в тонких верхних слоях заготовки, а нижележащие слои прогреваются более мягко за счёт теплопроводности, метод является идеальным для проведения поверхностной закалки деталей (сердцевина при этом остаётся вязкой).
Лёгкая автоматизация оборудования — циклов нагрева и охлаждения, регулировка и удерживание температуры, подача и съём заготовок.
Установки индукционного нагрева:
На установках с рабочей частотой до 300 кГц используют инверторы на IGBT-сборках или MOSFET-транзисторах. Такие установки предназначены для разогрева крупных деталей. Для разогрева мелких деталей используются высокие частоты (до 5 МГц, диапазон средних и коротких волн), установки высокой частоты строятся на электронных лампах.
Также для разогрева мелких деталей строятся установки повышенной частоты на MOSFET-транзисторах на рабочие частоты до 1,7 МГц. Управление транзисторами и их защита на повышенных частотах представляет определённые трудности, поэтому установки повышенной частоты пока ещё достаточно дороги.
Индуктор для нагрева мелких деталей имеет небольшие размеры и небольшую индуктивность, что приводит к уменьшению добротности рабочего колебательного контура на низких частотах и снижению КПД, а также представляет опасность для задающего генератора (добротность колебательного контура пропорциональна L/C, колебательный контур с низкой добротностью слишком хорошо «накачивается» энергией, образует короткое замыкание по индуктору и выводит из строя задающий генератор). Для повышения добротности колебательного контура используют два пути:
— применение ферромагнитных вставок в индукторе; обклеивание индуктора панельками из ферромагнитного материала.
Так как наиболее эффективно индуктор работает на высоких частотах, промышленное применение индукционный нагрев получил после разработки и начала производства мощных генераторных ламп. До первой мировой войны индукционный нагрев имел ограниченное применение. В качестве генераторов тогда использовали машинные генераторы повышенной частоты (работы В. П. Вологдина) или искровые разрядные установки.
Схема генератора может быть в принципе любой (мультивибратор, RC-генератор, генератор с независимым возбуждением, различные релаксационные генераторы), работающей на нагрузку в виде катушки-индуктора и обладающей достаточной мощностью. Необходимо также, чтобы частота колебаний была достаточно высока.
Например, чтобы «перерезать» за несколько секунд стальную проволоку диаметром 4 мм, необходима колебательная мощность не менее 2 кВт при частоте не менее 300 кГц.
Выбирают схему по следующим критериям: надёжность; стабильность колебаний; стабильность выделяемой в заготовке мощности; простота изготовления; удобство настройки; минимальное количество деталей для уменьшения стоимости; применение деталей, в сумме дающих уменьшение массы и габаритов, и др.
На протяжении многих десятилетий в качестве генератора высокочастотных колебаний применялась индуктивная трёхточка (генератор Хартли, генератор с автотрансформаторной обратной связью, схема на индуктивном делителе контурного напряжения). Это самовозбуждающаяся схема параллельного питания анода и частотно-избирательной цепью, выполненной на колебательном контуре. Она успешно использовалась и продолжает использоваться в лабораториях, ювелирных мастерских, на промышленных предприятиях, а также в любительской практике. К примеру, во время второй мировой войны на таких установках проводили поверхностную закалку катков танка Т-34.
Недостатки трёх точки:
Низкий кпд (менее 40 % при применении лампы).
Сильное отклонение частоты в момент нагрева заготовок из магнитных материалов выше точки Кюри (≈700С) (изменяется μ), что изменяет глубину скин-слоя и непредсказуемо изменяет режим термообработки. При термообработке ответственных деталей это может быть недопустимо. Также мощные твч-установки должны работать в узком диапазоне разрешённых Россвязьохранкультурой частот, поскольку при плохом экранировании являются фактически радиопередатчиками и могут оказывать помехи телерадиовещанию, береговым и спасательным службам.
При смене заготовок (например, более мелкой на более крупную) изменяется индуктивность системы индуктор-заготовка, что также приводит к изменению частоты и глубины скин-слоя.
При смене одновитковых индукторов на многовитковые, на более крупные или более малогабаритные частота также изменяется.
Под руководством Бабата, Лозинского и других учёных были разработаны двух- и трёхконтурные схемы генераторов, имеющих более высокий кпд (до 70 %), а также лучше удерживающие рабочую частоту. Принцип их действия состоит в следующем. За счёт применения связанных контуров и ослабления связи между ними, изменение индуктивности рабочего контура не влечёт сильного изменения частоты частотозадающего контура. По такому же принципу конструируются радиопередатчики.
Недостаток многоконтурных систем — повышенная сложность и возникновение паразитных колебаний УКВ-диапазона, которые бесполезно рассеивают мощность и выводят из строя элементы установки. Также такие установки склонны к затягиванию колебаний — самопроизвольному переходу генератора с одной из резонансных частот на другую.
Современные твч-генераторы — это инверторы на IGBT-сборках или мощных MOSFET-транзисторах, обычно выполненные по схеме мост или полумост. Работают на частотах до 500 кГц. Затворы транзисторов открываются с помощью микроконтроллерной системы управления. Система управления в зависимости от поставленной задачи позволяет автоматически удерживать
а) постоянную частоту
б) постоянную мощность, выделяемую в заготовке
в) максимально высокий КПД.
Например, при нагреве магнитного материала выше точки Кюри толщина скин-слоя резко увеличивается, плотность тока падает, и заготовка начинает греться хуже. Также пропадают магнитные свойства материала и прекращается процесс перемагничивания — заготовка начинает греться хуже, сопротивление нагрузки скачкообразно уменьшается — это может привести к «разносу» генератора и выходу его из строя. Система управления отслеживает переход через точку Кюри и автоматически повышает частоту при скачкообразном уменьшении нагрузки (либо уменьшает мощность).
Замечания.
Индуктор по возможности необходимо располагать как можно ближе к заготовке. Это не только увеличивает плотность электромагнитного поля вблизи заготовки (пропорционально квадрату расстояния), но и увеличивает коэффициент мощности Cos(φ).
Увеличение частоты резко уменьшает коэффициент мощности (пропорционально кубу частоты).
При нагреве магнитных материалов дополнительное тепло также выделяется за счет перемагничивания, их нагрев до точки Кюри идет намного эффективнее.
При расчёте индуктора необходимо учитывать индуктивность подводящих к индуктору шин, которая может быть намного больше индуктивности самого индуктора (если индуктор выполнен в виде одного витка небольшого диаметра или даже части витка — дуги).
Имеются два случая резонанса в колебательных контурах: резонанс напряжений и резонанс токов.
Параллельный колебательный контур – резонанс токов.
В этом случае на катушке и на конденсаторе напряжение такое же, как у генератора. При резонансе, сопротивление контура между точками разветвления становится максимальным, а ток (I общ) через сопротивление нагрузки Rн будет минимальным (ток внутри контура I-1л и I-2с больше чем ток генератора).
В идеальном случае полное сопротивление контура равно бесконечности — схема не потребляет тока от источника. При изменение частоты генератора в любую сторону от резонансной частоты полное сопротивление контура уменьшается и линейный ток (I общ) возрастает.
Последовательный колебательный контур – резонанс напряжений.
Главной чертой последовательного резонансного контура является то, что его полное сопротивление минимально при резонансе. (ZL + ZC – минимум). При настройке частоты на величину, превышающую или лежащую ниже резонансной частоты, полное сопротивление возрастает.
Вывод:
В параллельном контуре при резонансе ток через выводы контура равен 0, а напряжение максимально.
В последовательном контуре наоборот — напряжение стремится к нулю, а ток максимален.
Статья взята с сайта http://dic.academic.ru/ и переработана в более понятный для читателя текст, компанией ООО «Проминдуктор».
Индукционный нагреватель металла. Принцип работы
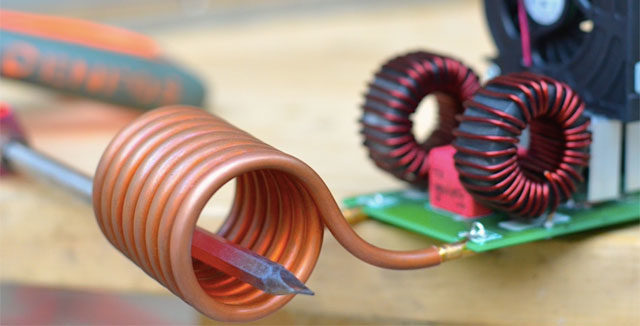
Технология индукционного нагрева заготовок востребована не только в цехах горячей объёмной штамповки. Компактные индукторы необходимы, в частности, для автосервиса, занимающегося изготовлением и ремонтом стальных деталей из профилированного проката. Приобретать промышленный индуктор дорого. Есть ли альтернатива?
Как работает индукционный нагреватель?
Для реализации процесса индукционного нагрева используется известный физический принцип, когда для деформирования в горячем состоянии заготовку размещают в магнитном поле кольцеобразного индуктора. Питание такой катушки производится электрическим переменным током частоты, резко выше, чем обычная (50 или 60 Гц).
Принцип работы индукционного нагревателя следующий. Создаваемые в электромагнитном поле вихревые токи (у них есть и другое название – токи Фуко) производят нагрев металла. Непосредственное соприкосновение заготовки и нагревательного элемента не обязательно, важно только, чтобы индуктор равномерно охватывал нагреваемую поверхность металла. Используя трансформатор, установка подключается к генератору, который обеспечивает требующиеся значения мощности и частоты.
Индукционным нагревом можно обеспечить сравнительно быстрое повышение температуры поверхностных слоёв. В частности, для нагревания прутковой заготовки сечением 35…40 мм и длиной 140….150 мм потребуется около 20…25 с.
Примерные диапазоны соответствия наилучшей частоты тока и поперечного сечения круглого прутка приведены в таблице.
Диаметр, мм | 20…40 | 40…60 | 60…80 | 80…100 | 100…120 |
Частота, кГц | 100…40 | 40…10 | 10…4 | 4…1 | 1…0,5 |
Для полосового металла применять индукционный нагрев менее выгодно, чем для круглого прутка, поскольку расстояние между внутренним диаметром катушки и металлом непостоянно.
Обычно применяется частота от 10 кГц, тогда КПД индукционного нагревателя достигает максимума. Частота регулируется в зависимости от:
- требуемой производительности нагрева;
- температуры нагреваемого металла;
- размеров поперечного сечения.
Конструкции промышленных индукторов снабжаются устройствами для автоматической загрузки-выгрузки нагретых заготовок. Это необходимо потому, чтобы интервал между нагревом и пластическим деформированием металла был минимальным.
Время нагрева стальных заготовок невелико: для сечения 20 мм оно составляет всего 10 с, поэтому потери металла в окалину незначительны.
Индукционный нагреватель своими руками
Известен ряд конструкций индукторов, изготовленных из сварочного инвертора, принцип действия которых может быть использован для наведения в металле вихревых токов Фуко.
Изготовление самодельного индуктора заключается в следующем. Вначале потребуется изготовить прочный корпус, в котором будет находиться узел крепления нагреваемой заготовки. Корпус необходимо подвергнуть закалке, чтобы он не деформировался под воздействием возможных ударов. Ещё лучше, если материал подвергнуть азотированию: в этом случае реализуются два преимущества — дополнительное увеличение твердости за счет более полного превращения остаточного аустенита в мартенсит, и улучшение скин-эффекта, когда по внешней стороне заготовки будет протекать более мощный ток. Прочность оценивается по пробе на искру.
Следующей стадией является изготовление нагревающей катушки. Её делают из индивидуально изолированных проводов: в этом случае потери мощности будут минимальными. Подойдёт и медная трубка – она имеет большую площадь поверхности, по которой будут наводиться вихревые токи, при этом собственный нагрев индуктора из-за высокой электропроводности меди практически отсутствует.
После подключения катушки к системе водяного охлаждения и проверки системы прокачки индуктор готов к работе.
Рабочая схема
В состав нагревателя входят следующие составляющие:
- Инверторный блок, рассчитанный на напряжение 220…240 В, при токе не менее 10 А.
- Трёхпроводная кабельная линия (один провод – заземляющий) с нормально разомкнутым переключателем.
- Система водяного охлаждения (крайне желательно использовать очистные фильтры для воды).
- Набор катушек, отличающихся внутренними диаметрами и длиной (при ограниченных объёмах работ можно обойтись и одной катушкой).
- Нагревающий блок (можно применить модуль на силовых транзисторах, которые выпускаются китайскими фирмами Infineon или IGBT).
- Демпферная цепь с несколькими конденсаторами Semikron.
Генератор высокочастотных колебаний принимается тот же, что и у базового инвертора. Важно, чтобы его эксплуатационные характеристики полностью соответствовали тем, которые указаны в предыдущих разделах.
После сборки блок заземляется, и с помощью соединительных кабелей нагревательная индукционная катушка присоединяется к блоку питания инвертора.
Примерные эксплуатационные возможности самодельного индукционного нагревателя металла:
- Наибольшая температура нагрева, °С – 800.
- Минимальная мощность инвертора – 2 кВА.
- Продолжительность включения ПВ, не менее – 80.
- Рабочая частота, кГц (регулируемая) — 1,0…5,0.
- Внутренний диаметр катушки, мм – 50.
Следует отметить, что такой индуктор потребует специально подготовленного рабочего места – бака для отработанной воды, насоса, надёжного заземления.
Индукционный нагрев – применение в целях обработки металла
Индукционный нагрев – это способ бесконтактной тепловой обработки металлов, способных проводить электрическую энергию, под воздействием токов высокой частоты. Индукционный нагрев все активнее стал применяться на предприятиях для осуществления высокотемпературной обработки металлов. На сегодняшний день индукционное оборудование смогло занять лидирующие позиции, вытесняя альтернативные методы нагрева.
Индукционный нагрев как работает
Принцип действия индукционного нагрева предельно прост. Нагрев производится за счет трансформации электрической энергии в электромагнитное поле, обладающее высокой мощностью. Нагрев изделия осуществляется при проникновении магнитного поля индукторов в изделие, способное проводить электрическую энергию.
Заготовка (обязательно из материала, проводящего электрическую энергию) размещается в индукторе или в непосредственной близости с ним. Индуктор, как правило, выполняется в виде одного или нескольких витков провода. Чаще всего для изготовления индуктора используют толстые медные трубки (провода). Специальный генератор электрической энергии подает ее в индуктор, наводя токи высокой частоты, которые могут варьироваться от 10-и Гц до нескольких МГц. В результате наведения токов высокой частоты на индуктор, вокруг него образуется мощное электромагнитное поле. Вихревые токи образовавшегося электромагнитного поля проникают в изделие и преобразуются внутри его в тепловую энергию, осуществляя нагрев.
Во время работы индуктор довольно сильно нагревается за счет поглощения собственного излучения, поэтому он непременно должен охлаждаться во время рабочего процесса за счет проточной технической воды. Вода для охлаждения подается в установку при помощи отсасывания, такой метод позволяет обезопасить установку, если вдруг произойдет прожог или разгерметизация индуктора.
Индукционный нагрев применение в производстве
Как уже можно было понять из описанного выше, применяется индукционный нагрев в производстве довольно активно. На сегодняшний день индукционное оборудование успело занять лидирующее позиции, вытеснив конкурирующие способы обработки металлов на второй план.
Индукционная плавка металлов
Применяется индукционный нагрев для осуществления плавильных работ. Активное использование индукционных печей началось благодаря тому, что нагрев ТВЧ способен уникально обрабатывать все виды металлов, существующие на сегодняшний день.
Плавильная индукционная печь быстро осуществляет плавку металла. Температуры нагрева установки достаточно даже для плавки самых притязательных металлов. Главное преимущество индукционных плавильных печей заключается в том, что они способны производить чистую плавку металла с минимальным шлакообразованием. Работа выполняется за короткий промежуток времени. Как правило, время выплавки 100 килограмм металла равняется 45-и минутам.
Закалка ТВЧ (токами высокой частоты)
Закалка производится чаще всего в отношении изделий из стали, но может быть применена и к медным и другим металлическим изделиям. Принято различать два вида закалки ТВЧ поверхностная и глубокая закалка.
Главное достоинство, которым обладает индукционный нагрев по отношению к закалочным работам – это возможность проникновения тепла на глубину (глубокая закалка). На сегодняшний день закалка ТВЧ стала довольно часто производиться именно в индукционном оборудовании.
Индукционный нагрев позволяет не просто произвести закалку ТВЧ, но дает в конечном результате изделие, которое будет обладать отменным качеством. При использовании индукционного нагрева в целях осуществления закалочных работ количество брака в производстве существенно снижается.
Пайка ТВЧ
Индукционный нагрев полезен не только для обработки металла, но и для соединения одной части изделия с другой. На сегодняшний день пайка ТВЧ стала довольно популярной и смогла вытеснить сварку на второй план. Где только появляется возможность заменить сварку пайкой, производители делают это. Чем именно вызвано такое желание? Все предельно просто. Пайка ТВЧ дает возможность получить целостное изделие, которое будет обладать высокой прочностью.
Пайка ТВЧ получается целостной за счет прямого (бесконтактного) проникновения тепла в изделие. Для нагрева металла не требуется стороннее вмешательства в его структуру, что положительно сказывается на качестве готового изделия и на его сроке эксплуатации.
Термообработка сварных швов
Термообработка сварных швов – это еще один важный технологичный процесс, с которым отлично справится индукционный нагреватель. Термообработка осуществляется для того, чтобы придать изделию повышенную прочность и разгладить напряжение металла, которое, как правило, образуется в местах соединений.
Термообработка при помощи индукционного нагрева производится в три этапа. Каждый из них очень важен, ведь если упустить что-то, то впоследствии качество изделия станет другим и его срок эксплуатации снизится.
Индукционный нагрев положительно сказывается на металле, позволяя равномерно проникать на заданную глубину и разглаживать напряжение, образовавшееся во время произведения сварочных работ.
Ковка, пластика, деформация
Кузнечный нагреватель – это один из видов установок, в основе которых лежит индукционный нагрев. Используют кузнечный нагреватель для произведения деформации металла, а также в целях штамповки и т.п.
Индукционный нагрев равномерно прогревает металл, позволяет изогнуть его в нужных местах и придать изделию необходимую форму.
На сегодняшний день все больше предприятий стали использовать кузнечный нагреватель в целях штамповки и пластики изделий.
Индукционный нагрев способен справиться со всеми необходимыми операциями тепловой обработки металла, но чаще всего применяется в тех случаях, которые были описаны выше.
Индукционный нагрев преимущества и недостатки
У каждой вещи есть преимущества и недостатки, хорошие и плохие стороны. Индукционный нагрев не отличается и имеет как плюсы, так и минусы. Однако минусы индукционного нагрева настолько ничтожны, что не видны за огромным количеством преимуществ.
Так как недостатков у индукционного нагрева меньше, сразу же перечислим их:
- Некоторые установки являются довольно сложными и для их программирования необходимо квалифицированный персонал, который сможет обслуживать установку (осуществлять ремонт, чистку, программировать).
- Если индуктор и заготовка плохо согласованы между собой, то потребуется куда больше мощности нагрева, чем если выполнять похожу задачу в электрической установке.
Как видите, недостатков действительно немного и они не оказывают сильное влияние на принятие решение в пользу использования или неиспользования индукционного нагрева.
Достоинств индукционный нагрев имеет гораздо больше, но мы укажем только главные:
- Скорость нагрева изделия очень высокая. Индукционный нагрев практически сразу приступает к обработке металлического изделия, никаких промежуточных этапов прогрева оборудования не требуется.
- Нагрев изделия может производиться в любой воссозданной среде: в атмосфере защитного газа, в окислительной, в восстановительной, в вакуумной и в непроводящей жидкости.
- Индукционная установка обладает сравнительно небольшими размерами, благодаря чему довольно удобна в эксплуатации. Если возникает необходимость, то индукционное оборудование можно перевезти на место проведения работ.
- Нагрев металла производится через стенки защитной камеры, которая изготавливается из материалов способных пропускать вихревые токи, поглощая незначительное количество. Во время работы индукционное оборудование не нагревается, поэтому оно признано пожаробезопасным.
- Так как нагрев металла производится при помощи электромагнитного излучения, загрязнение самой заготовки и окружающей атмосферы отсутствует. Индукционный нагрев был по праву признан экологически безопасным. Он не причиняет абсолютно никакого вреда сотрудникам предприятия, которые будут находиться в цеху во время работы установки.
- Индуктор может быть изготовлен практически любой сложной формы, что позволит подогнать его под габариты и форму изделия, чтобы нагрев получился более качественным.
- Индукционный нагрев позволяет просто производить избирательный нагрев. Если нужно прогреть какую-то конкретную область, а не все изделие, то достаточно будет разместить в индукторе только ее.
- Качество обработки при помощи индукционного нагрева получается отменным. Количество брака в производстве существенно снижается.
- Индукционный нагрев позволяет экономить электрическую энергию и другие производственные ресурсы.
Как видите, достоинств у индукционного нагрева очень много. Выше были указаны лишь основные, которые оказали серьезное воздействие на решение многих владельцев приобрести индукционные установки для термообработки металла.
Если заметили ошибку, выделите фрагмент текста и нажмите Ctrl+Enter
Индукционный нагреватель металла на 12 киловатт – схема инвертора и компоненты
Сейчас мы узнаем как сделать своими руками индукционный нагреватель, который можно использовать для разных проектов или просто для удовольствия. Вы сможете мгновенно плавить сталь, алюминий или медь. Вы можете использовать её для пайки, плавления и ковки металлов. Вы можете использовать самодельный индуктивный нагреватель и для литья.
Мое учебное пособие охватывает теорию, компоненты и сборку некоторых из важнейших компонентов.
Инструкция большая, в ней мы рассмотрим основные шаги, дающие вам представление о том, что входит в такой проект, и о том, как его спроектировать, чтобы ничего не взорвалось.
Для печи я собрал очень точный недорогой криогенный цифровой термометр. Кстати, в тестах с жидким азотом он неплохо себя показал против брендовых термометров.
Шаг 1: Компоненты
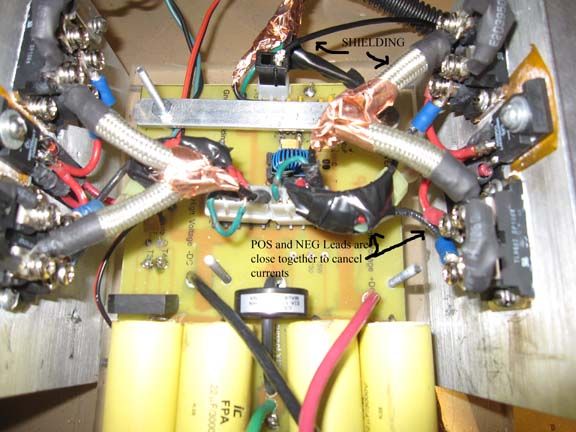
Основные компоненты высокочастотного индукционного нагревателя для нагрева металла электричеством — инвертор, драйвер, соединительный трансформатор и колебательный контур RLC. Вы увидите схему чуть позже. Начнем с инвертора. Это — электрическое устройство, которое изменяет постоянный ток на переменный. Для мощного модуля он должен работать стабильно. Сверху находится защита, которая используется, чтобы защитить привод логического элемента МОП-транзистора от любого случайного перепада напряжения. Случайные перепады вызывают шум, который приводит к переключению на высокие частоты. Это приводит к перегреву и отказу МОП-транзистора.
Линии с большой силой тока находятся внизу печатной платы. Много слоев меди используются, чтобы позволить им пропускать более 50А тока. Нам не нужен перегрев. Также обратите внимание на большие алюминиевые радиаторы с водяным охлаждением с обеих сторон. Это необходимо, чтобы рассеивать тепло, вырабатываемое МОП-транзисторами.
Изначально я использовал вентиляторы, но чтобы справиться с этой мощностью, я установил небольшие водяные насосы, благодаря которым вода циркулирует через алюминиевые теплоотводы. Пока вода чистая, трубки не проводят ток. У меня также установлены тонкие слюдяные пластины под МОП-транзисторами, чтобы гарантировать отсутствие проводимости через стоки.
Шаг 2: Схема инвертора
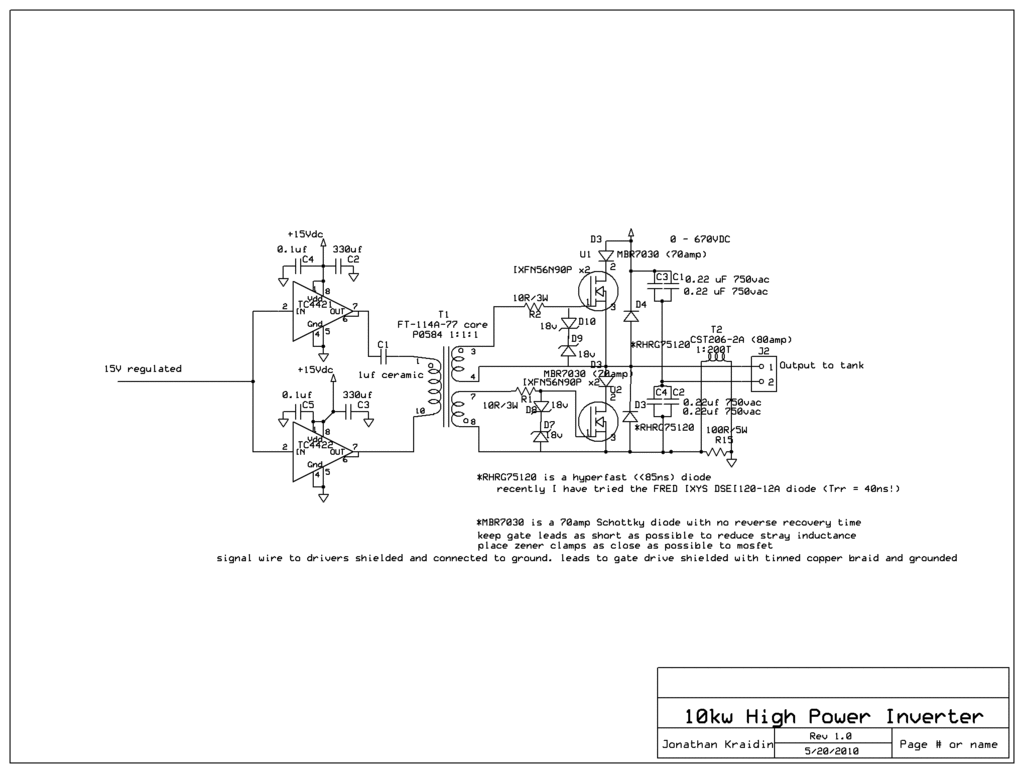
Это схема для инвертора. Схема на самом деле не такая сложная. Инвертированный и неинвертированный драйвер повышает или понижает напряжение 15В, чтобы настроить переменный сигнал в трансформаторе (GDT). Этот трансформатор изолирует чипы от мосфетов. Диод на выходе мосфета действует для ограничения пиков, а резистор минимизирует колебания.
Конденсатор C1 поглощает любые проявления постоянного тока. В идеале, вам нужны самые быстрые перепады напряжения на цепи, так как они уменьшают нагрев. Резистор замедляет их, что кажется нелогичным. Однако если сигнал не угасает, вы получаете перегрузки и колебания, которые разрушают мосфеты. Больше информации можно получить из схемы демпфера.
Диоды D3 и D4 помогают защитить МОП-транзисторы от обратных токов. C1 и C2 обеспечивают незамкнутые линии для проходящего тока во время переключения. T2 — это трансформатор тока, благодаря которому драйвер, о котором мы поговорим далее, получает обратный сигнал от тока на выходе.
Шаг 3: Драйвер
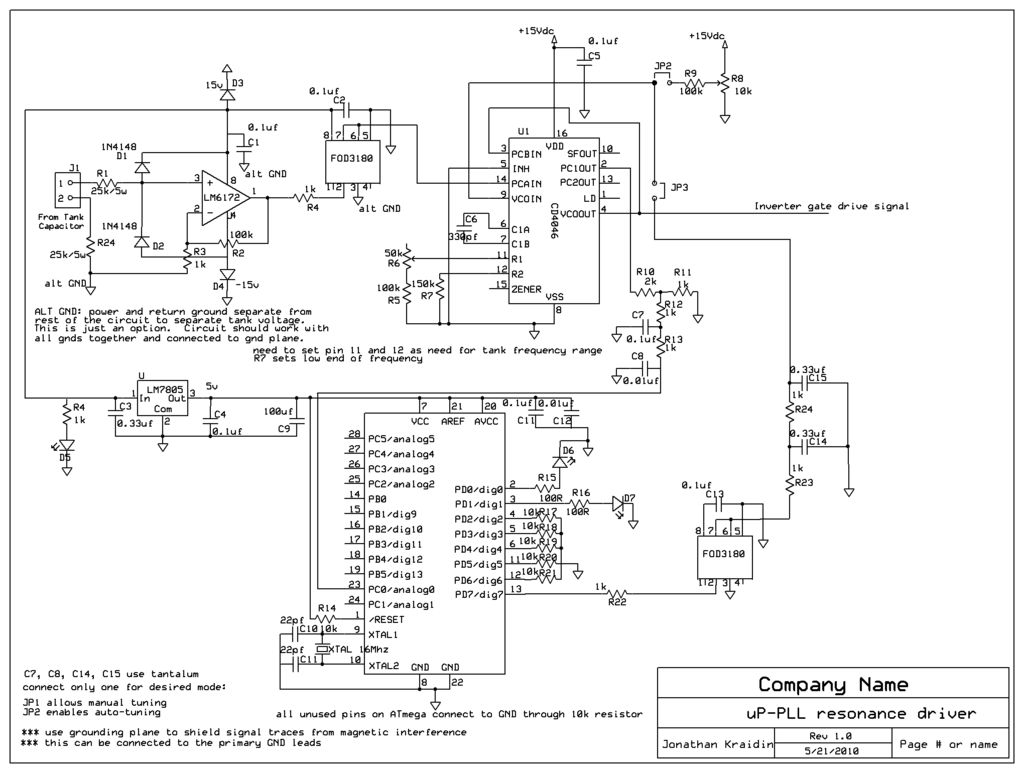
Эта схема действительно большая. Вообще, вы можете прочитать про простой маломощный инвертор. Если вам нужна большая мощность, вам нужен соответствующий драйвер. Этот драйвер будет останавливаться на резонансной частоте самостоятельно. После того, как ваш металл расплавится, он останется заблокированным на правильной частоте без необходимости какой-либо регулировки.
Если вы когда-либо строили простой индукционный нагреватель с чипом PLL, вы, вероятно, помните процесс настройки частоты, чтобы металл нагревался. Вы наблюдали за движением волны на осциллографе и корректировали частоту синхронизации, чтобы поддерживать эту идеальную точку. Больше не придется этого делать.
В этой схеме используется микропроцессор Arduino для отслеживания разности фаз между напряжением инвертора и емкостью конденсатора. Используя эту фазу, он вычисляет правильную частоту с использованием алгоритма «C».
Я проведу вас по цепи:
Сигнал емкости конденсатора находится слева от LM6172. Это высокоскоростной инвертор, который преобразует сигнал в красивую, чистую квадратную волну. Затем этот сигнал изолируется с помощью оптического изолятора FOD3180. Эти изоляторы являются ключевыми!
Далее сигнал поступает в PLL через вход PCAin. Он сравнивается с сигналом на PCBin, который управляет инвертором через VCOout. Ардуино тщательно контролирует тактовую частоту PLL, используя 1024-битный импульсно-модулированный сигнал. Двухступенчатый RC-фильтр преобразует сигнал PWM в простое аналоговое напряжение, которое входит в VCOin.
Как Ардуино знает, что делать? Магия? Догадки? Нет. Он получает информацию о разности фаз PCA и PCB от PC1out. R10 и R11 ограничивают напряжение в пределах 5 напряжений для Ардуино, а двухступенчатый RC-фильтр очищает сигнал от любого шума. Нам нужны сильные и чистые сигналы, потому что мы не хотим платить больше денег за дорогие мосфеты после того, как они взорвутся от шумных входов.
Шаг 4: Передохнём
Это был большой массив информации. Вы можете спросить себя, нужна ли вам такая причудливая схема? Зависит от вас. Если вы хотите автонастройку, тогда ответ будет «да». Если вы хотите настраивать частоту вручную, тогда ответ будет отрицательным. Вы можете создать очень простой драйвер всего лишь с таймером NE555 и использовать осциллограф. Можно немного усовершенствовать его, добавив PLL (петля фаза-ноль)
Тем не менее, давайте продолжим.
Шаг 5: LC-контур
К этой части есть несколько подходов. Если вам нужен мощный нагреватель, вам понадобится конденсаторный массив для управления током и напряжением.
Во-первых, вам нужно определить, какую рабочую частоту вы будете использовать. Более высокие частоты имеют больший скин-эффект (меньшее проникновение) и хороши для небольших объектов. Более низкие частоты лучше для больших объектов и имеют большее проникновение. Более высокие частоты имеют большие потери при переключении, но через бак пройдет меньше тока. Я выбрал частоту около 70 кГц и дошел до 66 кГц.
Мой конденсаторный массив имеет ёмкость 4,4 мкФ и может выдерживать более 300А. Моя катушка около 1мкГн. Также я использую импульсные пленочные конденсаторы. Они представляют собой осевой провод из самовосстанавливающегося металлизированного полипропилена и имеют высокое напряжение, высокий ток и высокую частоту (0.22 мкФ, 3000В). Номер модели 224PPA302KS.
Я использовал две медные шины, в которых просверлил соответствующие отверстия с каждой стороны. Паяльником я припаял конденсаторы к этим отверстиям. Затем я прикрепил медные трубки с каждой стороны для водного охлаждения.
Не берите дешевые конденсаторы. Они будут ломаться, и вы заплатите больше денег, чем если бы вы сразу купили хорошие.
Шаг 6: Сборка трансформатора
Если вы внимательно читали статью, вы зададите вопрос: а как управлять LC-контуром? Я уже рассказывал об инверторе и контуре, не упоминая, как они связаны.
Соединение осуществляется через соединительный трансформатор. Мой от Magnetics, Inc. Номер детали — ZP48613TC. Adams Magnetics также является хорошим выбором при выборе ферритовых тороидов.
Тот, что слева, имеет провод 2мм. Это хорошо, если ваш входной ток ниже 20А. Провод перегреется и сгорит, если ток больше. Для высокой мощности вам нужно купить или сделать литцендрат. Я сделал сам, сплетя 64 нити из проволоки 0.5мм. Такой провод без проблем может выдержать ток 50А.
Инвертор, который я показал вам ранее, принимает высоковольтный постоянный ток и изменяет его на переменные высокие или низкие значения. Эта переменная квадратная волна проходит черезч соединительный трансформатор через переключатели мосфета и конденсаторы связи постоянного тока на инверторе.
Медная трубка из емкостного конденсатора проходит через нее, что делает ее одновитковой вторичной обмоткой трансформатора. Это, в свою очередь, позволяет сбрасываемому напряжению проходить через конденсатор емкости и рабочую катушку (контур LC).
Шаг 7: Делаем рабочую катушку
Один из вопросов, который мне часто задавали: «Как ты делаешь такую изогнутую катушку?» Ответ — песок. Песок будет препятствовать разрушению трубки во время процесса изгиба.
Возьмите медную трубку от холодильника 9мм и заполните ее чистым песком. Перед тем, как сделать это, закройте один конец какой-нибудь лентой, а также закройте другой после заполнения песком. Вкопайте трубу соответствующего диаметра в землю. Отмерьте длину трубки для вашей катушки и начните медленно наматывать её на трубу. Как только вы сделаете один виток, остальные будет сделать несложно. Продолжайте наматывать трубку, пока не получите количество желаемых витков (обычно 4-6). Второй конец нужно выровнять с первым. Это упростит подключение к конденсатору.
Теперь снимите колпачки и возьмите воздушный компрессор, чтобы выдуть песок. Желательно делать это на улице.
Обратите внимание, что медная трубка также служит для водного охлаждения. Эта вода циркулирует через емкостный конденсатор и через рабочую катушку. Рабочая катушка генерирует много тепла от тока. Даже если вы используете керамическую изоляцию внутри катушки (чтобы удерживать тепло), вы по-прежнему будете иметь чрезвычайно высокие температуры в рабочем пространстве, нагревающие катушку. Я начну работу с большим ведром ледяной воды и через некоторое время она станет горячей. Советую заготовить очень много льда.
Шаг 8: Обзор проекта
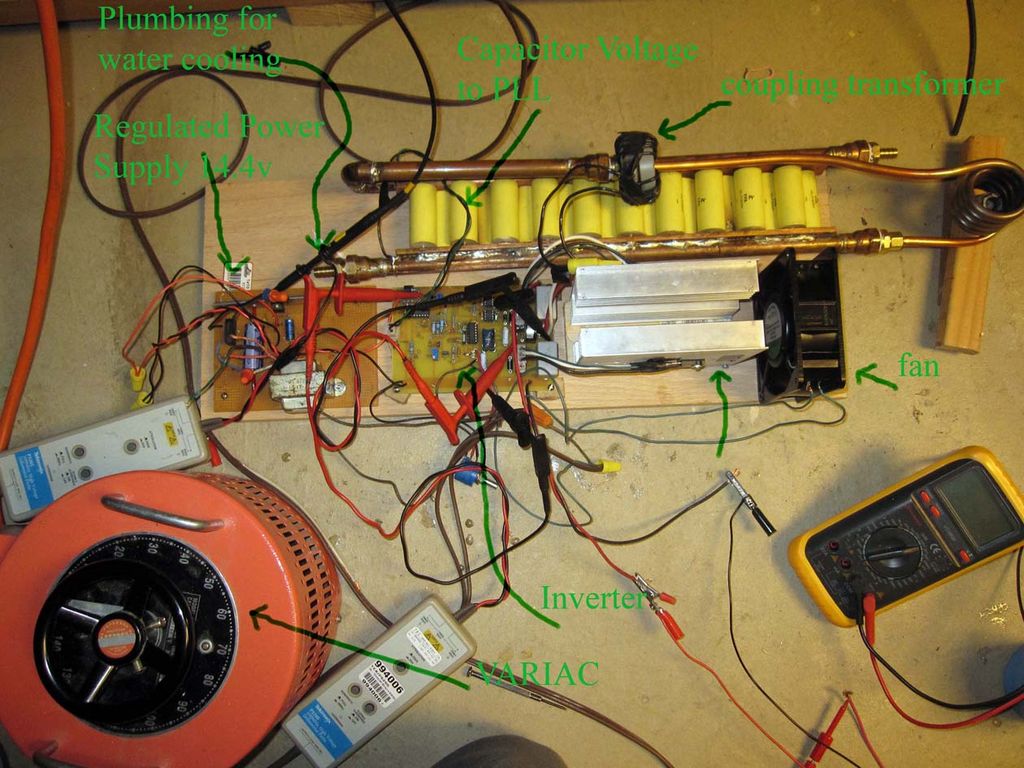
Выше представлен обзор проекта на 3 кВт. Он имеет простой PLL-драйвер, инвертор, соединительный трансформатор и бак.
Видео демонстрирует 12кВт индукционный горн в работе. Основное различие заключается в том, что он имеет управляемый микропроцессором драйвер, более крупные МОП-транзисторы и теплоотводы. Блок 3кВт работает от 120В переменного тока; блок 12 кВт использует 240В.
Простой, но мощный индукционный нагреватель
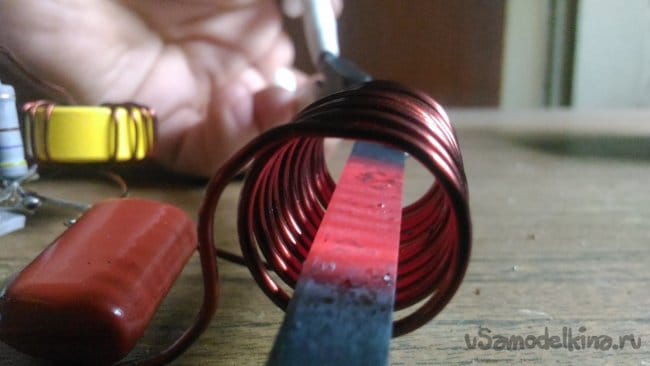

Привет, в данной самоделке я покажу процесс создания мощного, но простого индукционного нагревателя. Этот «индукционник» способен за считанные секунды разогревать стальное лезвие «до красна». С помощью него, можно «калить» предметы (инструменты, гвозди, саморезы), а так же расплавлять различные материалы (олово, алюминий и тд).

Вот схема которую нужно собрать
Перед началом чтения статья, я рекомендую посмотреть процесс сборки и испытаний:
[media=https://www.youtube.com/watch?v=cEaiQcxifcM]
Нам потребуется:
— 2 транзистора марки IRF3205
— 2 стабилитрон 1.5ке12
— 2 диода HER208
— 2 резистора на 10кОм и на 220Ом
— Пленочный конденсатор на 400В 1мкФ
— 2 ферритовых кольца (можно достать из старого блока питания компа)
— 2 изоляционные шайбы
— Радиатор (для охлаждения транзисторов)
— Пара винтиков (для закрепления транзисторов в радиаторе)
— Термопаста
— 2 кусочка слюды (для изоляции транзисторов от радиатора)
— Медный залакированный провод сечением 1.4мм2 длинной 1 метр
— Медный залакированный провод сечением 1.2мм2 2 куска по 1.5 метр
— Форма на намотки катушки (я буду использовать аккумулятор формата 18650)
— Аккумулятор для питания схемы (8-20В)
— 2 небольших кусочка провода
А так же:
— Бокорезы, ножик, отвертка, паяльник.
Подробное описание изготовления:
Шаг 1: Намотка катушки. Первым делом намотаем провод 1.4мм2 на «форму» (еще раз напомню что в качестве «формы» я буду использовать аккумулятор формата 18650) что-бы получить катушку.
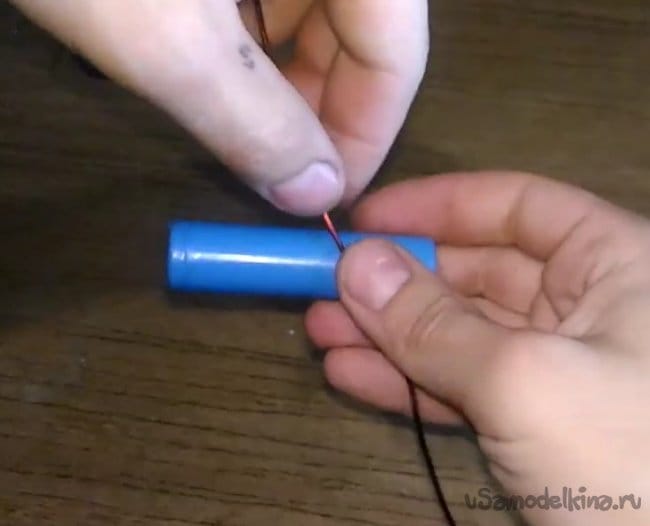
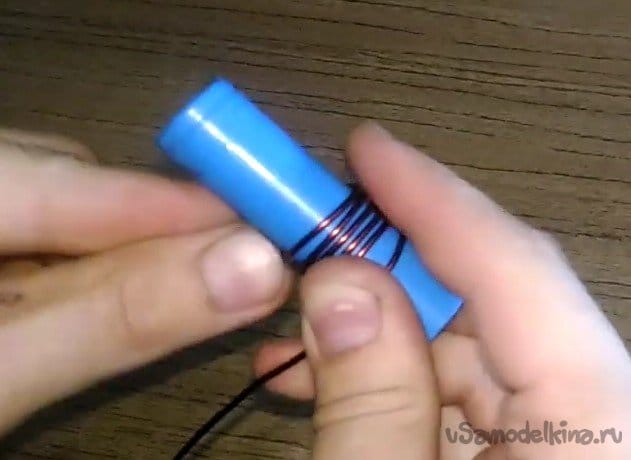
Должно получится что-то наподобие этого

Далее ножиком снимаем изоляцию с катушки
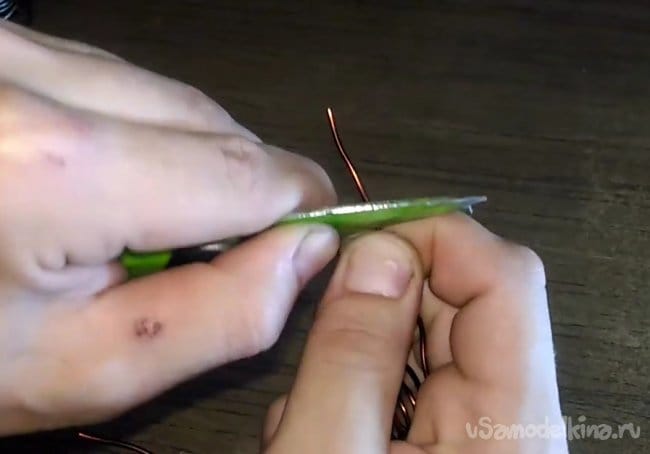
И залуживаем провода
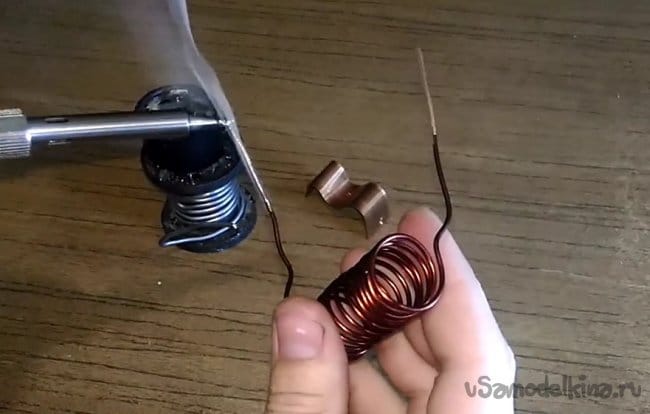
Должно получится примерно так
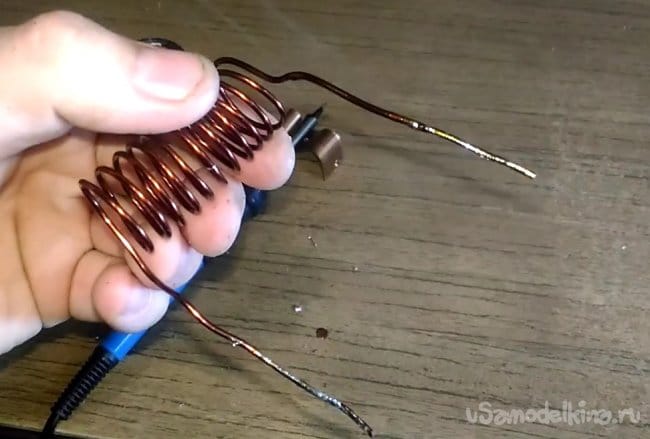
Шаг 2: Намотка катушки на ферритовые кольца. На этом этапе необходимо намотать провод 1.2мм2 на ферритовые кольца.
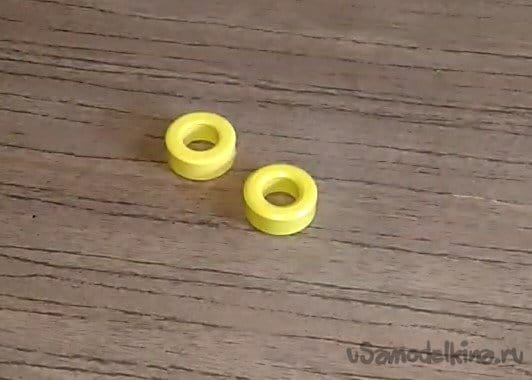
Для этого возьмем кольцо и проденем в него провод.

И начинаем намотку
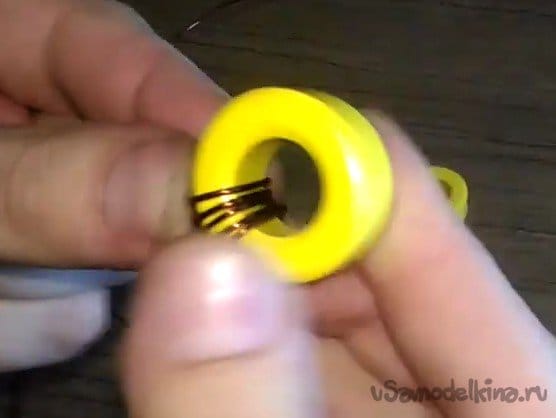
Обратите внимание, что витки должны быть плотно натянуты. В итоге получаем это.
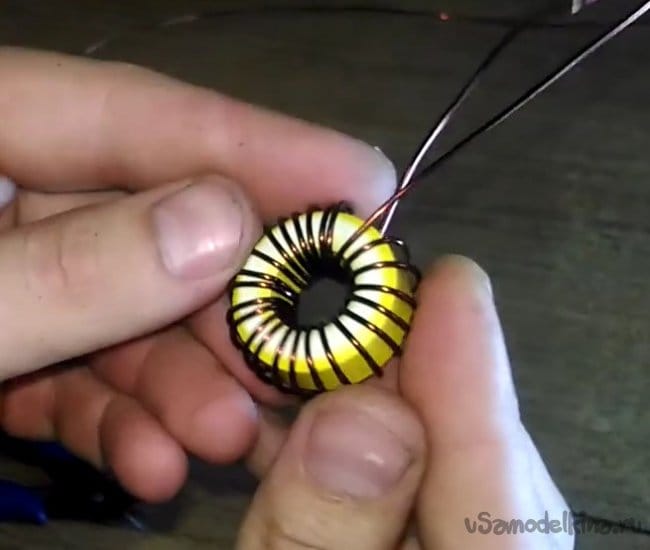
Шаг 3: Закрепление и подготовка транзисторов. Первым делом подготовим термопасту. Я буду использовать весьма распространенную КПТ-8.
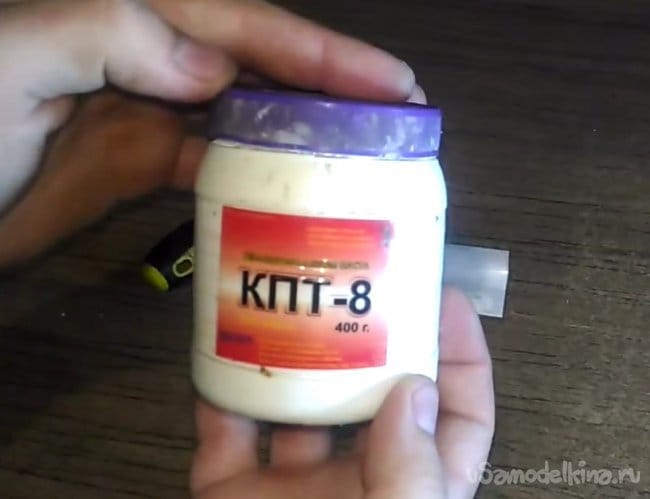
Необходимо нанести тонким слоем термопасту по всей площади на 2 кусочка слюды.
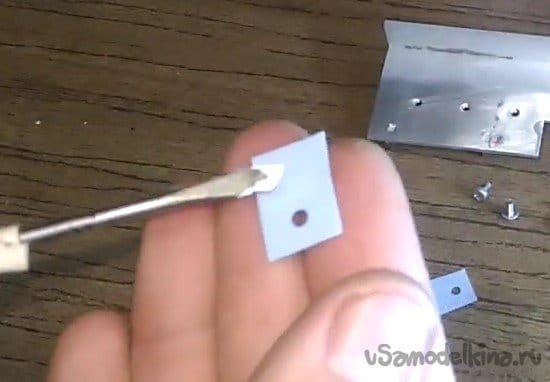
Что бы получилось так.
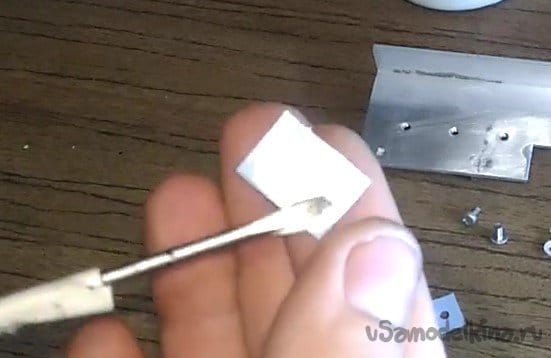
Затем «приклеиваем» слюду на радиатор
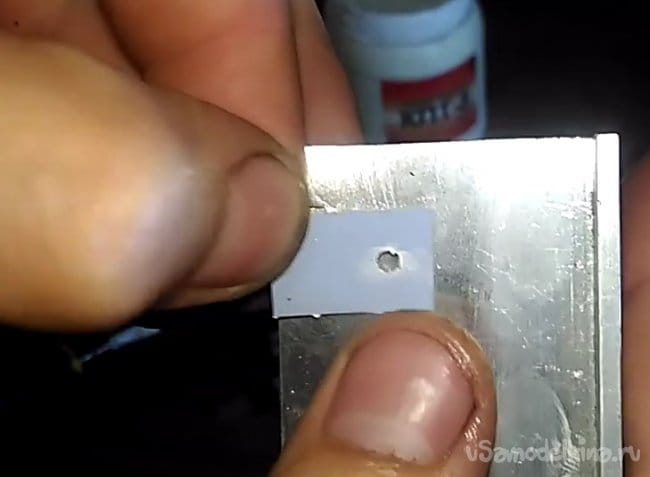
То же самое делаем и с самим транзистором.

Аккуратно прислоняем транзистор (между слюдой) к радиатору.

И прикручиваем его с помощью нескольких винтиков.

Так же проделываем и со вторым транзистором. Таким образом на данном этапе уже имеется 2 транзистора прикрученных к радиатору и готовых к дальнейшей пайки.
Шаг 4: Пайка компонентов по схеме.
На этом этапе начинается самая «интересная» часть. После ее завершения уже получится полностью готовое устройство.
Подготовим 2 резистора на 220 Ом.

Их необходимо припаять к левым ногам транзисторов.

И затем оставшиеся концы соединить между собой и залудить.

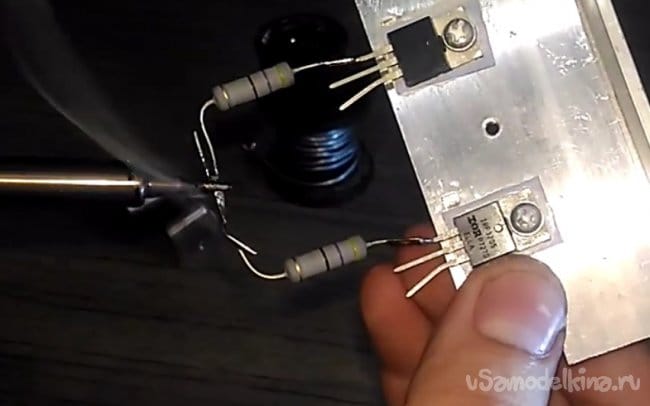
Затем необходимо подготовить стабилитроны.

Их необходимо припаять между левой и правой «ножкой» транзистора. Все это делается с 2 транзисторами.

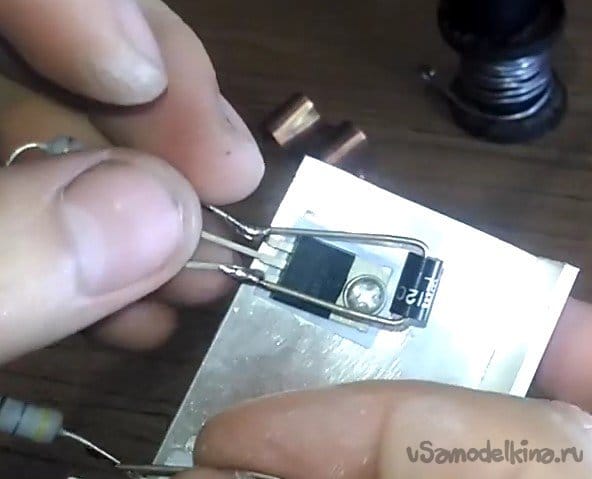
Что бы получилось так.
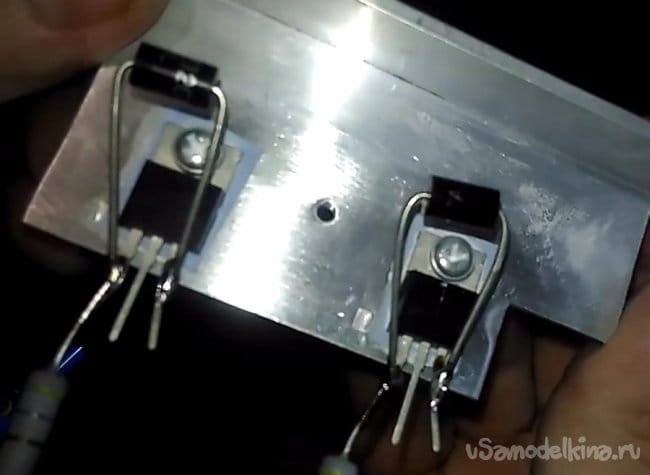
Теперь необходимо соединить «правые» ножки транзисторов (истоки) перемычкой. В ее роли послужит остаток залакированного медного провода.
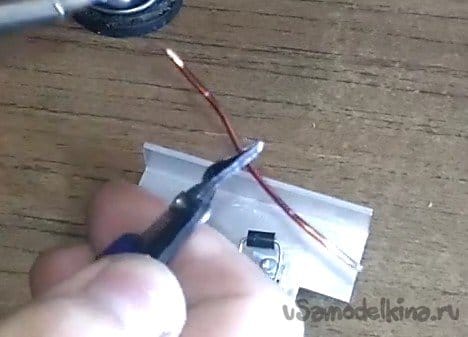

Подготовим 2 резистора на 10 кОм

Затем соединяем левую ногу транзистора (затвора) с правой ногой (истоком) резистором на 10 кОм

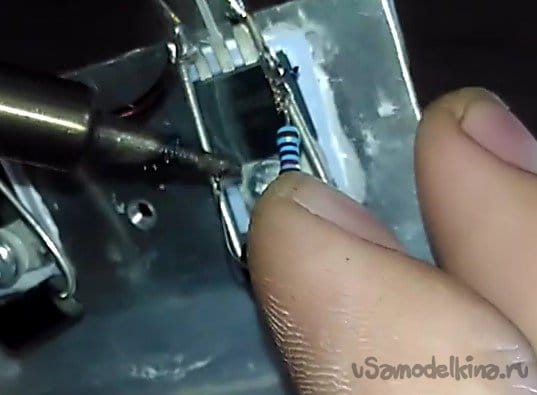
Так же делаем и со вторым транзистором. Получаем подобие этого.
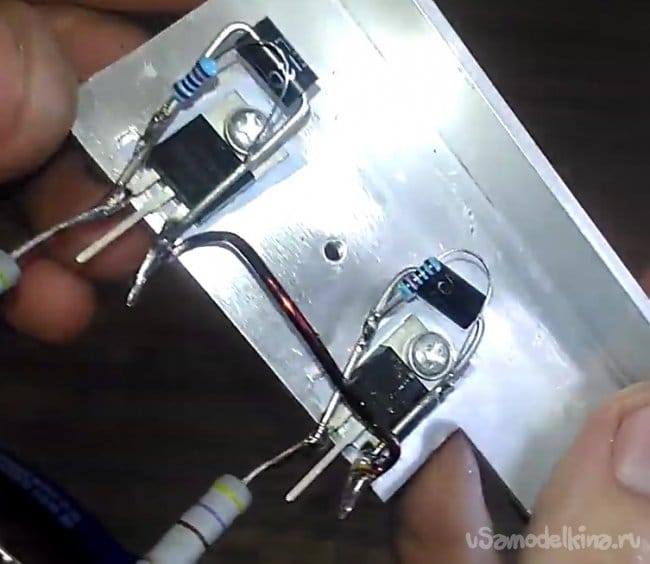
Теперь настала очередь диодов.

Необходимо припаять анод диода (значок треугольничка) к левой ноге транзистора.

А второй конец диода к центральной ноге к другому транзистору.
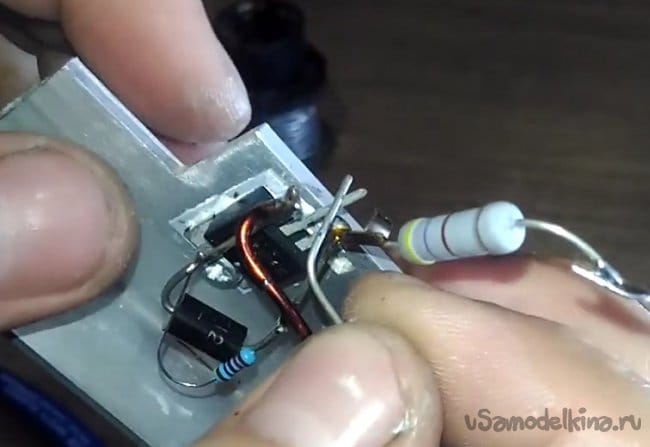
После сделать то же самое, но с другим транзистором.

Далее нужна катушка, которую сделали еще на первом этапе
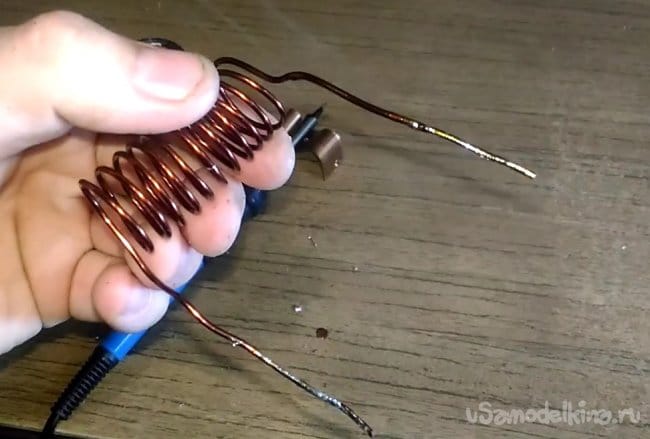
Её концы необходимо припаять к стокам транзисторов (центральные ноги транзисторов).

Следом нужно припаять конденсатор между катушкой как на фото.
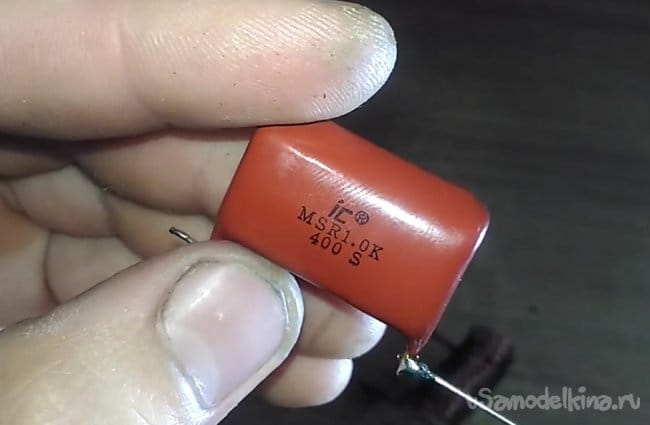

Один из последних этапов и присоединение дросселей. Но сначала его необходимо подготовить, для этого снимаете изоляцию и залуживаете концы.
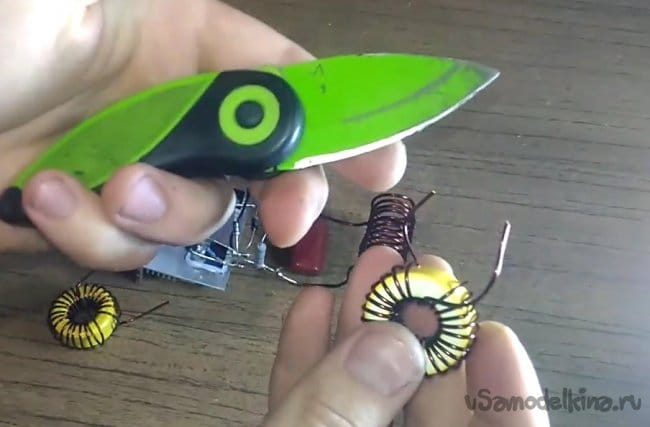
Вслед за этим с каждой стороны транзистора его нужно припаять к общей точке соединения резистором на 220 Ом и место куда паяли конденсатор.
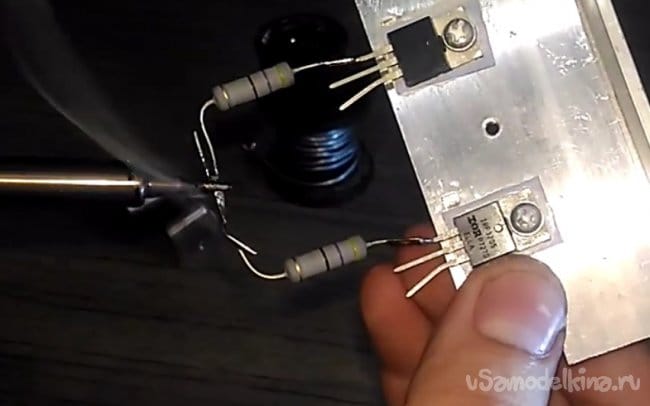
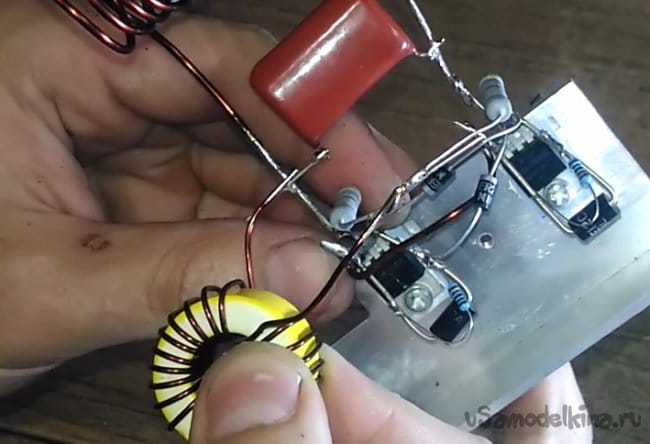
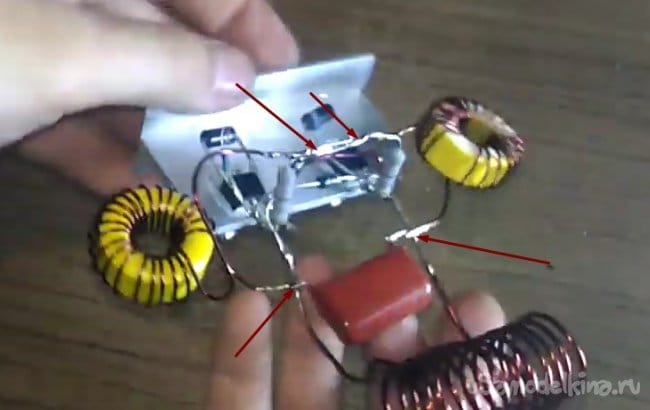
Теперь можно подготовить 2 небольших кусочка провода(желательного разного цвета) для питания всей схемы.Один из провода (в моём случаи желтый) припаиваем к месту соединения резисторов на 220 Ом, сюда будет подключаться плюс
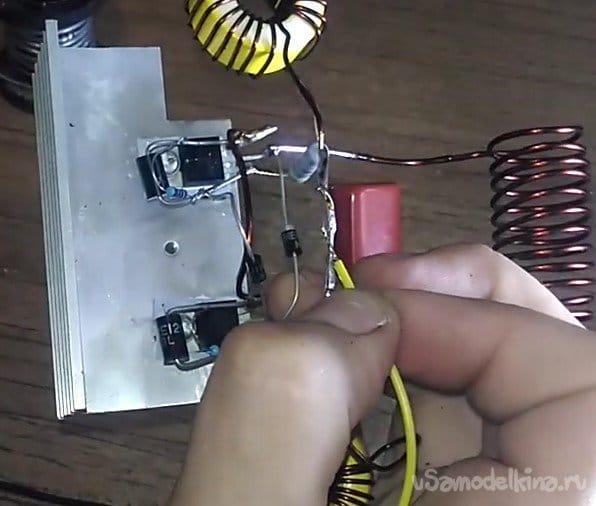
а черный провод (минус) идет на правую ногу (истоку) одного из транзисторов.

Вот финальное фото уже полностью рабочей и собранной схемы.

Шаг 5: Подключение и проверка.
Для питания схемы я буду использовать Li Po аккумулятор для квадрокоптеров.
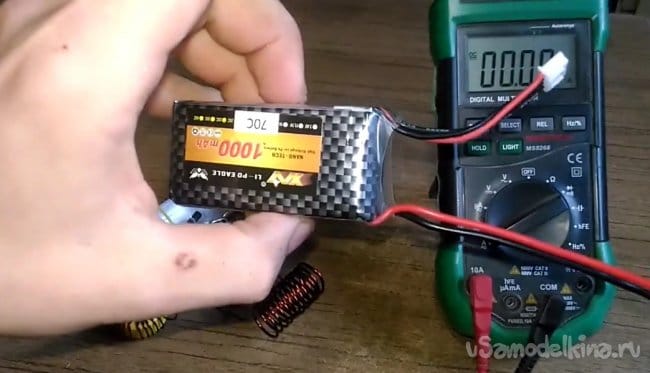
Но можно использовать любой другой (или даже несколько) напряжением от 8 В до 20 В.
Плюс с аккумулятора припаиваем к проводу, который присоединен с резисторам на 220 Ом, в моем случаи это желтый. Но я подключаю через амперметр, что бы еще и показать ток потребляемый схемой. Вы конечно можете этого не делать. Минус же идет на другой провод (черный), я рекомендую его припаять через кнопку, но для демонстрации я просто буду их соединять когда нужно что бы схема заработала.

У меня ток достигал 15А. Эти значения могут колебаться в зависимости от разных условий, просто учитывайте это.
Спасибо за внимание. Всем удачи в начинаниях!
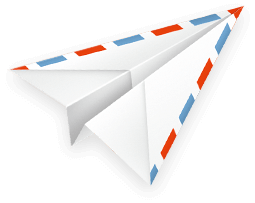
Получайте на почту подборку новых самоделок. Никакого спама, только полезные идеи!
*Заполняя форму вы соглашаетесь на обработку персональных данных
Становитесь автором сайта, публикуйте собственные статьи, описания самоделок с оплатой за текст. Подробнее здесь.Индукционный нагреватель металла своими руками
Когда перед человеком встает необходимость нагреть металлический объект, ему на ум обязательно приходит огонь. Огонь – старомодный, неэффективный и медленный способ нагреть металл. Он тратит львиную долю энергии на тепло, и от огня всегда идет дым. Как было бы здорово, если бы всех этих проблем можно было избежать.
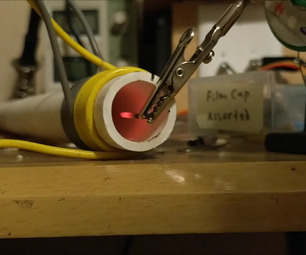
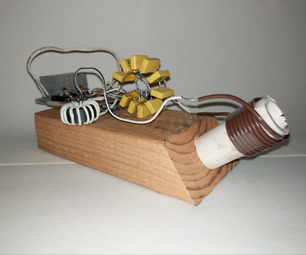
Сегодня я покажу вам как собрать индукционный нагреватель своими руками с ZVS-драйвером. Это приспособление нагревает большинство металлов с помощью ZVS-драйвера и силы электромагнетизма. Такой нагреватель высокоэффективен, не производит дыма, а нагрев таких небольших металлических изделий, как, допустим, скрепка — вопрос нескольких секунд. Видео демонстрирует нагреватель в действии, но инструкция там представлена другая.
Шаг 1: Принцип работы
Многие из вас сейчас задаются вопросом – что такое этот ZVS-драйвер? Это высокоэффективный трансформатор, способный создавать мощное электромагнитное поле, нагревающее металл, основа нашего нагревателя.
Чтобы стало понятно, как работает наш прибор, я расскажу о ключевых моментах. Первый важный момент — источник питания 24 В. Напряжение должно быть 24В при максимальной силе тока 10А. У меня будут два свинцово-кислотных аккумулятора, соединенных последовательно. Они запитывают плату ZVS-драйвера. Трансформатор дает установившийся ток на спираль, внутрь которой помещается объект, который надо нагреть. Постоянное изменение направления тока создает переменное магнитное поле. Оно создает внутри металла вихревые токи, преимущественно высокой частоты. Из-за этих токов и низкого сопротивления металла выделяется тепло. Согласно закону Ома, сила тока, трансформируемая в тепло, в цепи с активным сопротивлением, будет P=I^2*R.
Очень важен металл, из которого состоит объект, который вы хотите нагреть. У сплавов на основе железа более высокая магнитная проницаемость, они могут использовать больше энергии магнитного поля. Из-за этого они быстрее нагреваются. Алюминий имеет низкую магнитную проницаемость и нагревается, соответственно, дольше. А предметы с высоким сопротивлением и низкой магнитной проницаемостью, например, палец, вообще не нагреются. Сопротивление материала очень важно. Чем выше сопротивление, тем слабее ток пройдет по материалу, и тем, соответственно, меньше выделится тепла. Чем ниже сопротивление, тем сильнее будет ток, и согласно закону Ома, меньше потеря напряжения. Это немного сложно, но из-за связи между сопротивлением и выдачей мощности, максимальная выдача мощности достигается, когда сопротивление равно 0.
Трансформатор ZVS самая сложная часть прибора, я объясню, как он работает. Когда ток включен, он идет через два индукционных дросселя к обоим концам спирали. Дроссели нужны, чтобы убедиться, что устройство не выдаст слишком сильный ток. Далее ток идет через 2 резистора 470 Ом на затворы МДП-транзисторов.
Из-за того, что идеальных компонентов не существует, один транзистор будет включаться раньше, чем другой. Когда это происходит, он принимает на себя весь входящий ток со второго транзистора. Он также будет коротить второй на землю. Из-за этого не только ток потечет через катушку в землю, но и через быстрый диод будет разряжаться затвор второго транзистора, тем самым блокируя его. Из-за того, что параллельно катушке подключен конденсатор, создается колебательный контур. Из-за возникшего резонанса, ток поменяет свое направление, напряжение упадет до 0В. В этот момент затвор первого транзистора разряжается через диод на затвор второго транзистора, блокируя его. Этот цикл повторяется тысячи раз за секунду.
Резистор 10К призван уменьшить избыточный заряд затвора транзистора, действуя как конденсатор, а зенеровский диод должен сохранять напряжение на затворах транзисторов 12В или ниже, чтобы они не взорвались. Этот трансформатор высокочастотный преобразователь напряжения позволяет нагреваться металлическим объектам.
Пришло время собрать нагреватель.
Шаг 2: Материалы
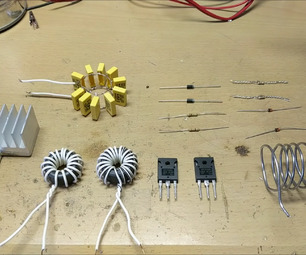
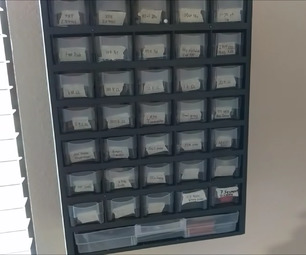
Для сборки нагревателя материалов нужно немного, и большую их часть, к счастью, можно найти бесплатно. Если вы видели где-то валяющуюся просто так электронно-лучевую трубку, сходите и заберите ее. В ней есть большая часть нужных для нагревателя деталей. Если вы хотите более качественных деталей, купите их в магазине электрозапчастей.
Вам понадобятся:
Шаг 3: Инструменты
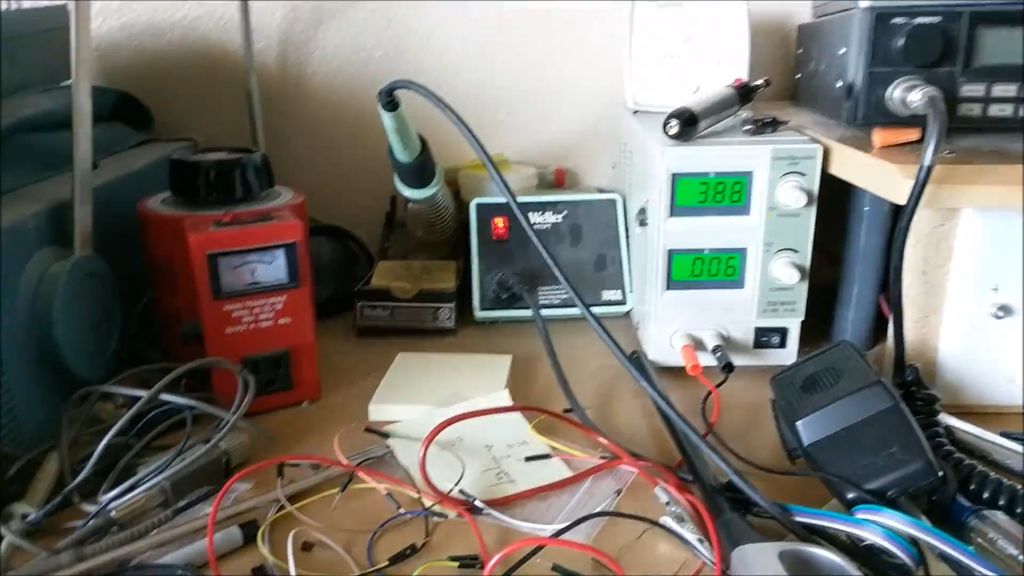
Для этого проекта вам понадобятся:
Шаг 4: Охлаждение полевых транзисторов
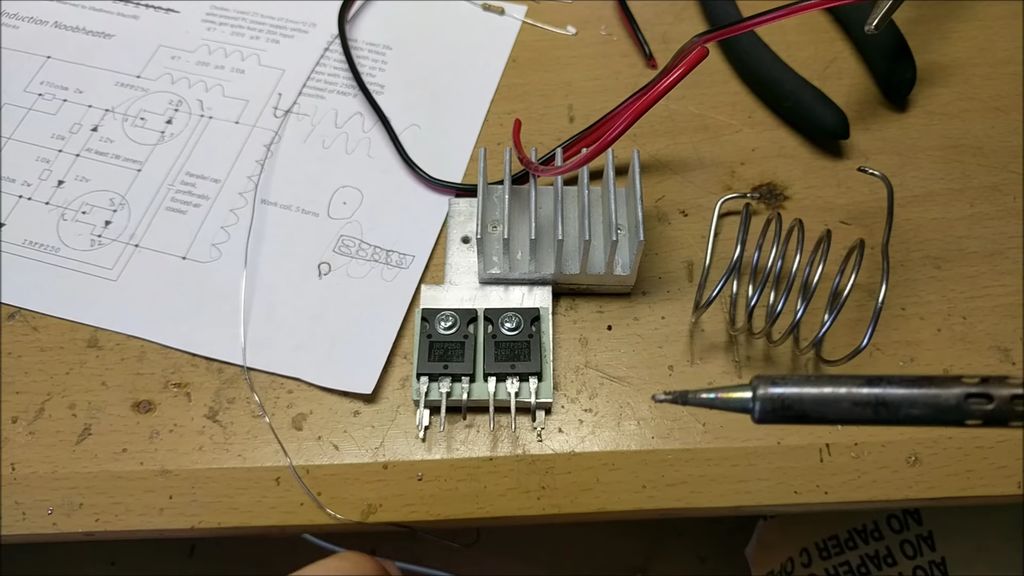
В этом приборе транзисторы выключаются при напряжении 0 В, и нагреваются не очень сильно. Но если вы хотите, чтобы нагреватель работал дольше одной минуты, вам нужно отводить тепло от транзисторов. Я сделал обоим транзисторам один общий поглотитель тепла. Убедитесь, что металлические затворы не касаются поглотителя, иначе МДП-транзисторы закоротит и они взорвутся. Я использовал компьютерный теплоотвод, и на нем уже была полоса силиконового герметика. Чтобы проверить изоляцию, коснитесь мультиметром средней ножки каждого МДП-транзистора (затвора), если мультиметр запищал, то транзисторы не изолированы.
Шаг 5: Конденсаторная батарея
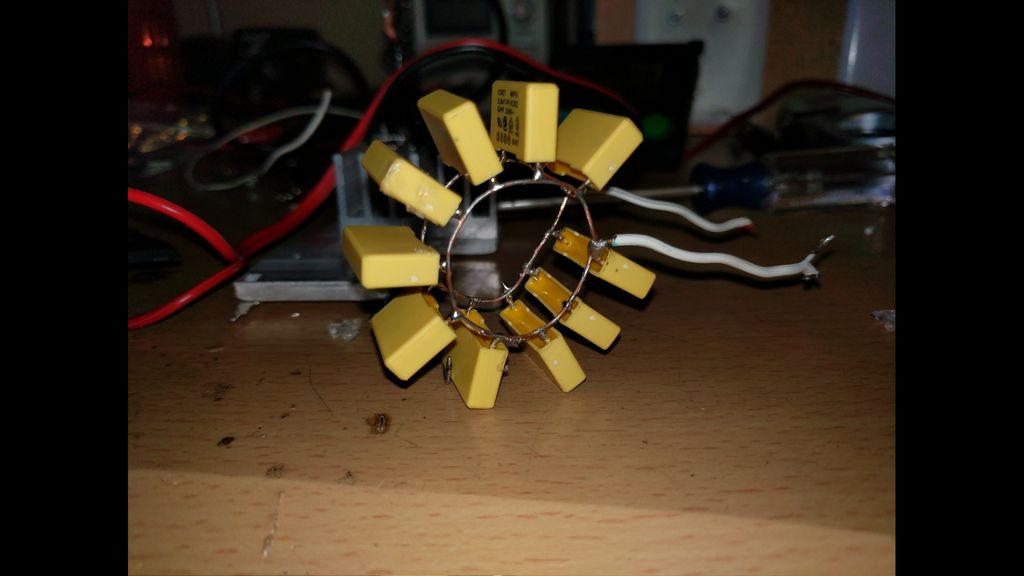
Конденсаторы очень сильно нагреваются из-за тока, постоянно проходящего через них. Нашему нагревателю нужна емкость конденсатора 0,47 мкФ. Поэтому нам нужно объединить все конденсаторы в блок, таким образом, мы получим требуемую емкость, а площадь рассеивания тепла увеличится. Номинальное напряжение конденсаторов должно быть выше 400 В, чтобы учесть пики индуктивного напряжения в резонансном контуре. Я сделал два кольца из медной проволоки, к которым припаял 10 конденсаторов 0,047 мкФ параллельно друг другу. Таким образом, я получил конденсаторную батарею совокупной емкостью 0,47 мкФ с отличным воздушным охлаждением. Я установлю ее параллельно рабочей спирали.
Шаг 6: Рабочая спираль
Это та часть прибора, в которой создается магнитное поле. Спираль сделана из медной проволоки – очень важно, чтобы была использована именно медь. Сначала я использовал для нагревания стальную спираль, и прибор работал не очень хорошо. Без рабочей нагрузки он потреблял 14 А! Для сравнения, после замены спирали на медную, прибор стал потреблять только 3 А. Я думаю, что в стальной спирали возникали вихревые токи из-за содержания железа, и она тоже подвергалась индукционному нагреву. Не уверен, что причина именно в этом, но это объяснение кажется мне наиболее логичным.
Для спирали возьмите медную проволоку большого сечения и сделайте 9 витков на отрезке ПВХ-трубы.
Шаг 7: Сборка цепи
Я сделал очень много проб и совершил много ошибок, пока правильно собрал цепь. Больше всего трудностей было с источником питания и со спиралью. Я взял 55А 12В импульсный блок питания. Я думаю, этот блок питания дал слишком высокий начальный ток на ZVS-драйвер, из-за чего взорвались МДП-транзисторы. Возможно, это исправили бы дополнительные индукторы, но я решил просто заменить блок питания на свинцово-кислотные аккумуляторы.
Потом я мучился с катушкой. Как я уже говорил, стальная катушка не подходила. Из-за высокого потребления тока стальной спиралью взорвались еще несколько транзисторов. В общей сложности у меня взорвались 6 транзисторов. Что ж, на ошибках учатся.
Я переделывал нагреватель множество раз, но здесь я расскажу, как собрал его самую удачную версию.
Шаг 8: Собираем прибор
Чтобы собрать ZVS-драйвер, вам нужно следовать приложенной схеме. Сначала я взял зенеровский диод и соединил с 10К резистором. Эту пару деталей можно сразу припаять между стоком и истоком МДП-транзистора. Убедитесь, что зенеровский диод смотрит на сток. Потом припаяйте МДП-транзисторы к макетной плате с контактными отверстиями. На нижней стороне макетной платы припаяйте два быстрых диода между затвором и стоком каждого из транзисторов.
Убедитесь, что белая линия смотрит на затвор (рис.2). Затем соедините плюс от вашего блока питания со стоками обоих транзисторов через 2 220 Ом резистора. Заземлите оба истока. Припаяйте рабочую спираль и конденсаторную батарею параллельно друг другу, затем припаяйте каждый из концов к разным затворам. Наконец, подведите ток к затворам транзисторов через 2 50 мкгн дросселя. У них может быть тороидальный сердечник с 10 витками проволоки. Теперь ваша схема готова к использованию.
Шаг 9: Установка на основание
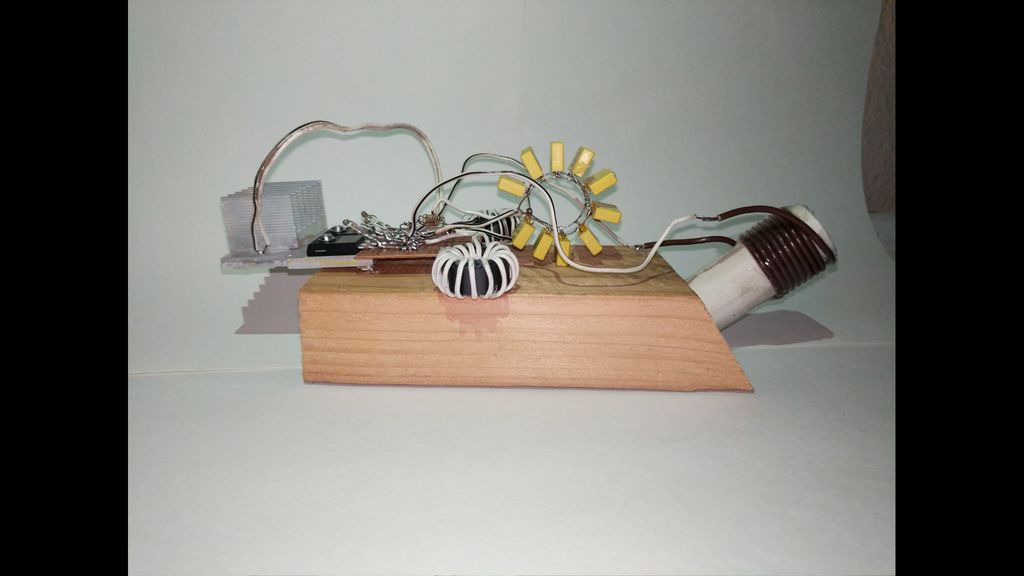
Чтобы все части вашего индукционного нагревателя держались вместе, им нужно основание. Я взял для этого деревянный брусок 5*10 см. плата с электросхемой, конденсаторная батарея и рабочая спираль были приклеены на термоклей. Мне кажется, агрегат выглядит круто.
Шаг 10: Проверка работоспособности
Чтобы ваш нагреватель включился, просто подсоедините его к источнику питания. Потом поместите предмет, который вам нужно нагреть, в середину рабочей спирали. Он должен начать нагреваться. Мой нагреватель раскалил скрепку до красного свечения за 10 секунд. Предметы крупнее, как гвозди, нагревались примерно за 30 секунд. В процессе нагревания потребление тока выросло приблизительно на 2 А. Этот нагреватель можно использовать не только для развлечения.
После использования прибора не образуется сажи или дыма, он воздействует даже на изолированные металлические объекты, например, газопоглотители в вакуумных трубках. Также прибор безопасен для человека – с пальцем ничего не случится, если поместить его в центр рабочей спирали. Однако, можно обжечься о предмет, который был нагрет.
Спасибо за чтение!
Индукционный нагрев — Википедия
Индукционный нагрев металлического стержня диаметром 25 мм с использованием установки мощностью 15 кВт, работающей на частоте 450 кГцИндукцио́нный нагре́в — метод бесконтактного нагрева электропроводящих материалов токами высокой частоты и большой величины.
История индукционного нагрева
Открытие электромагнитной индукции в 1831 году принадлежит Майклу Фарадею. При движении проводника в поле магнита в нём наводится ЭДС, так же как при движении магнита, силовые линии которого пересекают проводящий контур. Ток в контуре называется индукционным. На законе электромагнитной индукции основаны изобретения множества устройств, в том числе определяющих — генераторов и трансформаторов, вырабатывающих и распределяющих электрическую энергию, что является фундаментальной основой всей электротехнической промышленности.
В 1841 году Джеймс Джоуль (и независимо от него Эмиль Ленц) сформулировал количественную оценку теплового действия электрического тока: «Мощность тепла, выделяемого в единице объёма среды при протекании электрического тока, пропорциональна произведению плотности электрического тока на величину напряженности электрического поля» (закон Джоуля — Ленца). Тепловое действие индуцированного тока породило поиски устройств бесконтактного нагрева металлов. Первые опыты по нагреву стали с использованием индукционного тока были сделаны Е. Колби в США.
Первая успешно работающая т. н. канальная индукционная печь для плавки стали была построена в 1900 году на фирме «Benedicks Bultfabrik» в городе Gysing в Швеции. В респектабельном журнале того времени «THE ENGINEER» 8 июля 1904 г. появилась знаменитая публикация, где шведский изобретатель инженер F. A. Kjellin рассказывает о своей разработке. Печь питалась от однофазного трансформатора. Плавка осуществлялась в тигле в виде кольца, металл, находящийся в нём, представлял вторичную обмотку трансформатора, питающегося током 50-60 Гц.
Первая печь мощностью 78 кВт была запущена в эксплуатацию 18 марта 1900 года и оказалась весьма неэкономичной, поскольку производительность плавки составляла всего 270 кг стали в сутки. Следующая печь была изготовлена в ноябре того же года мощностью 58 кВт и ёмкостью 100 кг по стали. Печь показала высокую экономичность, производительность плавки составила от 600 до 700 кг стали в сутки. Однако износ футеровки от тепловых колебаний оказался на недопустимом уровне, частые замены футеровки снижали итоговую экономичность.
Изобретатель пришёл к выводу, что для максимальной производительности плавки необходимо при сливе оставлять значительную часть расплава, что позволяет избежать многих проблем, в том числе износа футеровки. Такой способ выплавки стали с остатком, который стали называть «болото», сохранился до сих пор в некоторых производствах, где применяются печи большой ёмкости.
В мае 1902 года была введена в эксплуатацию значительно усовершенствованная печь ёмкостью 1800 кг, слив составлял 1000—1100 кг, остаток 700—800 кг, мощность 165 кВт, производительность плавки стали могла доходить до 4100 кг в сутки! Такой результат по потреблению энергии 970 кВт⋅ч/т впечатляет своей экономичностью, которая мало уступает современной производительности порядка 650 кВт⋅ч/т. По расчётам изобретателя из потребляемой мощности 165 кВт в потери уходило 87,5 кВт, полезная тепловая мощность составила 77,5 кВт, получен весьма высокий полный КПД, равный 47 %. Экономичность объясняется кольцевой конструкцией тигля, что позволило сделать многовитковый индуктор с малым током и высоким напряжением — 3000 В. Современные печи с цилиндрическим тиглем значительно компактнее, требуют меньших капитальных вложений, проще в эксплуатации, оснащены многими усовершенствованиями за сотню лет своего развития, однако КПД повышен несущественно. Правда, изобретатель в своей публикации игнорировал тот факт, что плата за электроэнергию осуществляется не за активную мощность, а за полную, которая при частоте 50-60 Гц примерно вдвое выше активной мощности. А в современных печах реактивная мощность компенсируется конденсаторной батареей.
Своим изобретением инженер F. A. Kjellin положил начало развития промышленных канальных печей для плавки цветных металлов и стали в индустриальных странах Европы и в Америке. Переход от канальных печей 50-60 Гц к современным высокочастотным тигельным длился с 1900 по 1940 г.
Принцип действия
Индукционный нагрев — это нагревание материалов электрическими токами, которые индуцируются переменным магнитным полем. Следовательно — это нагрев изделий из проводящих материалов (проводников) магнитным полем индукторов (источников переменного магнитного поля).
Индукционный нагрев проводится следующим образом. Электропроводящая (металлическая, графитовая) заготовка помещается в так называемый индуктор, представляющий собой один или несколько витков провода (чаще всего медного). В индукторе с помощью специального генератора наводятся мощные токи различной частоты (от десятка Гц до нескольких МГц), в результате чего вокруг индуктора возникает электромагнитное поле. Электромагнитное поле наводит в заготовке вихревые токи. Вихревые токи разогревают заготовку под действием джоулева тепла.
Система «индуктор-заготовка» представляет собой бессердечниковый трансформатор, в котором индуктор является первичной обмоткой. Заготовка является как бы вторичной обмоткой, замкнутой накоротко. Магнитный поток между обмотками замыкается по воздуху.
На высокой частоте вихревые токи вытесняются образованным ими же магнитным полем в тонкие поверхностные слои заготовки Δ (скин-эффект), в результате чего их плотность резко возрастает и заготовка разогревается. Нижерасположенные слои металла прогреваются за счёт теплопроводности. Важен не ток, а большая плотность тока. В скин-слое Δ плотность тока увеличивается в e раз относительно плотности тока в заготовке, при этом в скин-слое выделяется 86,4 % тепла от общего тепловыделения. Глубина скин-слоя зависит от частоты излучения: чем выше частота, тем тоньше скин-слой. Также она зависит от относительной магнитной проницаемости μ материала заготовки.
Для железа, кобальта, никеля и магнитных сплавов при температуре ниже точки Кюри μ имеет величину от нескольких сотен до десятков тысяч. Для остальных материалов (расплавы, цветные металлы, жидкие легкоплавкие эвтектики, графит, электропроводящая керамика и т. д.) μ примерно равна единице.
Формула для вычисления глубины скин-слоя в мм:
- Δ=103ρμπf{\displaystyle \Delta =10^{3}{\sqrt {\frac {\rho }{\mu \pi f}}}},
где ρ — удельное электрическое сопротивление материала заготовки при температуре обработки, Ом·м, f — частота электромагнитного поля, генерируемого индуктором, Гц.
Например, при частоте 2 МГц глубина скин-слоя для меди около 0,047 мм, для железа ≈ 0,0001 мм[источник?].
Индуктор сильно нагревается во время работы, так как сам поглощает собственное излучение. К тому же он поглощает тепловое излучение от раскалённой заготовки. Делают индукторы из медных трубок, охлаждаемых водой. Вода подаётся отсасыванием — этим обеспечивается безопасность в случае прожога или иной разгерметизации индуктора.
Применение
- Сверхчистая бесконтактная плавка, пайка и сварка металла.
- Получение опытных образцов сплавов.
- Гибка и термообработка деталей машин.
- Ювелирное дело.
- Обработка мелких деталей, которые могут повредиться при газопламенном или дуговом нагреве.
- Поверхностная закалка.
- Закалка и термообработка деталей сложной формы.
- Обеззараживание медицинского инструмента.
- Распыление геттера и прогрев (активация и тренировка) катода в процессе производства вакуумных электронных приборов.
Преимущества
- Высокоскоростной разогрев или плавление любого электропроводящего материала.
- Возможен нагрев в атмосфере защитного газа, в окислительной (или восстановительной) среде, в жидкости, в вакууме.
- Нагрев через стенки защитной камеры, изготовленной из стекла, цемента, пластмасс, дерева — эти материалы очень слабо поглощают электромагнитное излучение и остаются холодными при работе установки. Нагревается только электропроводящий материал — металл (в том числе расплавленный), углерод, проводящая керамика, жидкие металлы и т. п. Например, внутренности радиолампы можно прогревать для обезгаживания прямо через стеклянную колбу. Электролиты (растворы солей) невозможно нагревать индукционным нагревом, так как ионы, в отличие от электронов, обладают большой массой и малой подвижностью.
- За счёт возникающих МГД-усилий происходит интенсивное перемешивание жидкого металла, вплоть до удержания его в подвешенном состоянии в воздухе или защитном газе — так получают сверхчистые сплавы в небольших количествах (левитационная плавка, плавка в электромагнитном тигеле).
- Поскольку разогрев ведётся посредством электромагнитного излучения, отсутствует загрязнение заготовки продуктами горения факела в случае газопламенного нагрева или материалом электрода в случае дугового нагрева. Помещение образцов в атмосферу инертного газа и высокая скорость нагрева позволят ликвидировать окалинообразование.
- Нет загрязнения воздуха, так как отсутствуют продукты горения. Небольшие установки индукционного нагрева можно эксплуатировать в замкнутом и плохо проветриваемом помещении, не оборудованном специальными средствами вентиляции и вытяжками (гаражи, небольшие домашние мастерские, подвалы).
- Удобство эксплуатации за счёт небольшого размера индуктора.
- Индуктор можно изготовить особой формы — это позволит равномерно прогревать по всей поверхности детали сложной конфигурации, не приводя к их короблению или локальному непрогреву.
- Легко провести местный и избирательный нагрев.
- Так как наиболее интенсивно разогрев идет в тонких верхних слоях заготовки, а нижележащие слои прогреваются более медленно за счёт теплопроводности, метод является идеальным для проведения поверхностной закалки деталей (сердцевина детали при этом остаётся вязкой).
- Лёгкая автоматизация оборудования и конвейерных производственных линий. Простота управления циклами нагрева и охлаждения. Простая регулировка и удерживание температуры, стабилизация мощности, подача и съём заготовок.
Недостатки
- Повышенная сложность оборудования, необходим квалифицированный персонал для проектирования установок, их настройки и ремонта.
- При плохом согласовании индуктора с заготовкой требуется бо́льшая мощность на нагрев, чем в случае применения для той же задачи ТЭНов, электрических дуг и электронагревательных спиралей.
- Требуется мощный источник электроэнергии для питания установки индукционного нагрева, а также насос и бак с охлаждающей жидкостью для охлаждения индуктора (чиллер), которые в полевых условиях могут отсутствовать. В этом случае применение, например, газовых горелок с портативными газовыми баллонами более оправдано.
- Несмотря на небольшие размеры индуктора, агрегат индукционного нагрева в целом достаточно громоздок и маломобилен и больше подходит для стационарной установки в помещении, чем для выездных работ.
Левитационный нагрев
Устройства индукционного нагрева
Генераторы индукционных токов
Нагревательный индуктор представляет собой катушку индуктивности, входящую в состав рабочего колебательного контура с компенсирующей конденсаторной батареей. Раскачку контура осуществляют либо с помощью электронных ламп, либо с помощью полупроводниковых электронных ключей. На установках с рабочей частотой до 300 кГц используют инверторы на IGBT-сборках или MOSFET-транзисторах. Такие установки предназначены для разогрева крупных деталей. Для разогрева мелких деталей используются высокие частоты (до 5 МГц, диапазон средних и коротких волн), установки высокой частоты строятся на электронных лампах.
Также для разогрева мелких деталей строятся установки повышенной частоты на MOSFET-транзисторах на рабочие частоты до 1,7 МГц. Управление транзисторами и их защита на повышенных частотах представляет определённые трудности, поэтому установки повышенной частоты пока ещё достаточно дороги.
Индуктор для нагрева мелких деталей имеет небольшие размеры и небольшую индуктивность, что приводит к уменьшению добротности рабочего колебательного контура на низких частотах и снижению КПД, а также представляет опасность для задающего генератора (на низких частотах индуктивное сопротивление индуктора (катушки колебательного контура) мало, и возникает короткое замыкание по катушке (индуктору). Добротность колебательного контура пропорциональна L/C, колебательный контур с низкой добротностью очень плохо «накачивается» энергией. Для повышения добротности колебательного контура используют два пути:
- Повышение рабочей частоты, что приводит к усложнению и удорожанию установки;
- Применение ферромагнитных вставок в индукторе; обклеивание индуктора панельками из ферромагнитного материала.
Так как наиболее эффективно индуктор работает на высоких частотах, промышленное применение индукционный нагрев получил после разработки и начала производства мощных генераторных ламп. До первой мировой войны индукционный нагрев имел ограниченное применение. В качестве генераторов тогда использовали машинные генераторы повышенной частоты (работы В. П. Вологдина) или искровые разрядные установки.
Схема генератора может быть в принципе любой (мультивибратор, RC-генератор, генератор с независимым возбуждением, различные релаксационные генераторы), работающей на нагрузку в виде катушки-индуктора и обладающей достаточной мощностью. Необходимо также, чтобы частота колебаний была достаточно высока.
Например, чтобы «перерезать» за несколько секунд стальную проволоку диаметром 4 мм, необходима колебательная мощность не менее 2 кВт при частоте не менее 300 кГц.
Выбирают схему по следующим критериям: надёжность; стабильность колебаний; стабильность выделяемой в заготовке мощности; простота изготовления; удобство настройки; минимальное количество деталей для уменьшения стоимости; применение деталей, в сумме дающих уменьшение массы и габаритов, и др.
На протяжении многих десятилетий в качестве генератора высокочастотных колебаний применялась индуктивная трёхточка (генератор Хартли, генератор с автотрансформаторной обратной связью, схема на индуктивном делителе контурного напряжения). Это самовозбуждающаяся схема параллельного питания анода и частотно-избирательной цепью, выполненной на колебательном контуре. Она успешно использовалась и продолжает использоваться в лабораториях, ювелирных мастерских, на промышленных предприятиях, а также в любительской практике. К примеру, во время второй мировой войны на таких установках проводили поверхностную закалку катков танка Т-34.
Недостатки трёхточки:
- Низкий кпд (менее 40 % при применении лампы).
- Сильное отклонение частоты в момент нагрева заготовок из магнитных материалов выше точки Кюри (≈700 °С) (изменяется μ), что изменяет глубину скин-слоя и непредсказуемо изменяет режим термообработки. При термообработке ответственных деталей это может быть недопустимо. Также мощные твч-установки должны работать в узком диапазоне разрешённых Россвязьохранкультурой частот, поскольку при плохом экранировании являются фактически радиопередатчиками и могут оказывать помехи телерадиовещанию, береговым и спасательным службам.
- При смене заготовок (например, более мелкой на более крупную) изменяется индуктивность системы индуктор-заготовка, что также приводит к изменению частоты и глубины скин-слоя.
- При смене одновитковых индукторов на многовитковые, на более крупные или более малогабаритные частота также изменяется.
Под руководством Бабата, Лозинского и других учёных были разработаны двух- и трёхконтурные схемы генераторов, имеющих более высокий КПД (до 70 %), а также лучше удерживающие рабочую частоту. Принцип их действия состоит в следующем. За счёт применения связанных контуров и ослабления связи между ними, изменение индуктивности рабочего контура не влечёт сильного изменения частоты частотозадающего контура. По такому же принципу конструируются радиопередатчики.
Недостаток многоконтурных систем — повышенная сложность и возникновение паразитных колебаний УКВ-диапазона, которые бесполезно рассеивают мощность и выводят из строя элементы установки. Также такие установки склонны к затягиванию колебаний — самопроизвольному переходу генератора с одной из резонансных частот на другую.
Современные ТВЧ-генераторы — это инверторы на IGBT-сборках или мощных MOSFET-транзисторах, обычно выполненные по схеме мост или полумост. Работают на частотах до 500 кГц. Затворы транзисторов открываются с помощью микроконтроллерной системы управления. Система управления в зависимости от поставленной задачи позволяет автоматически удерживать:
- постоянную частоту;
- постоянную мощность, выделяемую в заготовке;
- максимально высокий КПД.
Например, при нагреве магнитного материала выше точки Кюри толщина скин-слоя резко увеличивается, плотность тока падает, и заготовка начинает греться хуже. Также пропадают магнитные свойства материала и прекращается процесс перемагничивания — заготовка начинает греться хуже.
Проблема индукционного нагрева заготовок из магнитных материалов
Если инвертор для индукционного нагрева не является автогенератором, не имеет схемы автоподстройки частоты (ФАПЧ) и работает от внешнего задающего генератора (на частоте, близкой к резонансной частоте колебательного контура «индуктор — компенсирующая батарея конденсаторов»). В момент внесения заготовки из магнитного материала в индуктор (если размеры заготовки достаточно крупны и соизмеримы с размерами индуктора), индуктивность индуктора резко увеличивается, что приводит к скачкообразному уменьшению собственной резонансной частоты колебательного контура и отклонению её от частоты задающего генератора. Контур выходит из резонанса с задающим генератором, что приводит к увеличению его сопротивления и скачкообразному уменьшению передаваемой в заготовку мощности. Если мощность установки регулируется внешним источником питания, то естественной реакцией оператора является увеличить напряжение питания установки. При разогреве заготовки до точки Кюри, её магнитные свойства исчезают, собственная частота колебательного контура возвращается обратно к частоте задающего генератора. Сопротивление контура резко уменьшается, резко возрастает потребляемый ток. Если оператор не успеет снять повышенное напряжение питания, то установка перегревается и выходит из строя. Если установка оборудована автоматической системой управления, то система управления должна отслеживать переход через точку Кюри и автоматически уменьшать частоту задающего генератора, подстраивая его в резонанс с колебательным контуром (либо уменьшать подаваемую мощность, если изменение частоты недопустимо).
Если производится нагрев немагнитных материалов, то вышесказанное значения не имеет. Внесение в индуктор заготовки из немагнитного материала практически не меняет индуктивность индуктора и не сдвигает резонансную частоту рабочего колебательного контура, и необходимости в системе управления нет.
Если размеры заготовки много меньше размеров индуктора, то она тоже не сильно сдвигает резонанс рабочего контура.
Индукционные плиты
Индукционная плита — кухонная электрическая плита, разогревающая металлическую посуду индуцированными вихревыми токами, создаваемыми высокочастотным магнитным полем, частотой 20-100 кГц.
Такая плита обладает большим КПД по сравнению с ТЭН электроплитками, так как меньше тепла уходит на нагрев корпуса, а кроме того отсутствует период разгона и остывания (когда зря тратится выработанная, но не поглощенная посудой энергия).
Индукционные плавильные печи
Индукционные (бесконтактные) плавильные печи — электрические печи для расплавления и перегрева металлов, в которых нагрев происходит за счет вихревых токов, возникающих в металлическом тигеле (и металле), либо только в металле (если тигель изготовлен не из металла; такой способ нагрева более эффективен, если тигель плохо теплоизолирован).
Применяется в литейных цехах металлургических заводов, а также в цехах точного литья и ремонтных цехах машиностроительных заводов для получения стальных отливок высокого качества. Возможна плавка цветных металлов (бронзы, латуни, алюминия) и их сплавов в графитовом тигле. Индукционная печь работает по принципу трансформатора, у которого первичной обмоткой является водоохлаждаемый индуктор, вторичной и одновременно нагрузкой — находящийся в тигле металл. Нагрев и расплавление металла происходят за счёт протекающих в нём токов, которые возникают под действием электромагнитного поля, создаваемого индуктором.
Замечания
- Индуктор по возможности необходимо располагать как можно ближе к заготовке. Это не только увеличивает плотность электромагнитного поля вблизи заготовки (пропорционально квадрату расстояния), но и увеличивает коэффициент мощности cosφ{\displaystyle \operatorname {cos} \varphi }.
- Увеличение частоты резко уменьшает коэффициент мощности (пропорционально кубу частоты).
- При нагреве магнитных материалов дополнительное тепло также выделяется за счет перемагничивания, их нагрев идёт намного эффективнее (до точки Кюри).
- При расчёте индуктора необходимо учитывать индуктивность подводящих к индуктору шин, которая может быть намного больше индуктивности самого индуктора (если индуктор выполнен в виде одного витка небольшого диаметра или даже части витка — дуги).
- Иногда в качестве генератора высокой частоты использовали списанные мощные радиопередатчики, где антенный контур заменяли на нагревательный индуктор.
- Индукционный нагрев можно проводить в воде, даже солёной. Так как ионы растворённых в воде солей тяжёлые и обладают большой инерционностью, высокочастотное электромагнитное поле не может их «раскачать» и загрязнённая вода не нагревается.
См. также
Ссылки
Литература
- Бабат Г. И., Свенчанский А. Д. Электрические промышленные печи. — М.: Госэнергоиздат, 1948. — 332 с.
- Бурак Я. И., Огирко И. В. Оптимальный нагрев цилиндрической оболочки с зависящими от температуры характеристиками материала // Мат. методы и физ.-мех. поля. — 1977. — Вып. 5. — С. 26-30.
- Васильев А. С. Ламповые генераторы для высокочастотного нагрева. — Л.: Машиностроение, 1990. — 80 с. — (Библиотечка высокочастотника-термиста; Вып. 15). — 5300 экз. — ISBN 5-217-00923-3.
- Власов В. Ф. Курс радиотехники. — М.: Госэнергоиздат, 1962. — 928 с.
- Изюмов Н. М., Линде Д. П. Основы радиотехники. — М.: Госэнергоиздат, 1959. — 512 с.
- Лозинский М. Г. Промышленное применение индукционного нагрева. — М.: Изд-во АН СССР, 1948. — 471 с.
- Применение токов высокой частоты в электротермии / Под ред. А. Е. Слухоцкого. — Л.: Машиностроение, 1968. — 340 с.
- Слухоцкий А. Е. Индукторы. — Л.: Машиностроение, 1989. — 69 с. — (Библиотечка высокочастотника-термиста; Вып. 12). — 10 000 экз. — ISBN 5-217-00571-8.
- Фогель А. А. Индукционный метод удержания жидких металлов во взвешенном состоянии / Под ред. А. Н. Шамова. — 2-е изд., испр. — Л.: Машиностроение, 1989. — 79 с. — (Библиотечка высокочастотника-термиста; Вып. 11). — 2950 экз. — ISBN 5-217-00572-6.