Как подключить сверлильный станок?
Сверлильный станок – незаменимый инструмент, если необходимо выполнить идеальное, сверхточное отверстие с заданными параметрами. Перед эксплуатацией необходимо правильно подключить его к сети.
Подключение
Бытовые и промышленные станки оборудованы двигателем и прочими элементами, которые запитываются от сети. Поэтому важно выполнить подключение правильно и аккуратно – ошибки и неполадки силовой части устройства чреваты короткими замыканиями, выходом его из строя, а также поражением током окружающих.
Крупные агрегаты, используемые на предприятиях, обычно имеют рабочее напряжение 380 В, но их подключением занимаются опытные специалисты. Бытовые приборы с напряжением 220 В зачастую подключают самостоятельно.
Чтобы избежать ошибок, следуйте советам:
- используйте только новую, качественную проводку без поврежденной изоляции;
- сечение провода рассчитывайте, исходя из соотношения не менее 1,5 мм2 на 350 Вт мощности электропривода, немного увеличивая цифру, если розетка находится на значительном расстоянии;
- кабель используйте только медный, трехжильный, избегая лишних соединений «скруткой», в особенности с проводами из других материалов – именно в таких местах с высокой долей вероятности возникнет разрыв;
- розетка, к которой будет подключен провод, должна быть заземлена.
Обязательно проверьте это, особенно если речь идет о частном доме, даче – заземление является обязательным требованием;
- предохранительный автомат в сети должен быть минимум на 10 А.
В срочном порядке устраняйте все обнаруженные несоответствия. Использовать станок без надлежащего заземления, с плохой проводкой или при наличии неполадок в пусковом механизме строго запрещено.
Техника безопасности
Несмотря на простоту подключения и использования сверлильного станка, работа с ним может быть опасной без должного соблюдения правил безопасности. Среди них стоит выделить следующие:
- любые ремонтные или очистные работы выполняйте только при отключенном питании двигателя;
- используйте защитную одежду и очки, чтобы обезопаситься от летящих стружек, пыли, капель смазочно-охлаждающей жидкости, частей сверла при надломе;
- длинные волосы прячьте под головной убор, избегайте работы в перчатках – намотавшись на вращающиеся элементы, они могут привести к серьезным травмам;
- внимательно проверяйте перед началом работ все движущиеся узлы станка на предмет наличия дефектов и повреждений.
При их обнаружении использовать устройство запрещено.
Чтобы узнать больше о том, как подключить сверлильный станок, свяжитесь с представителями компании Metaltool – они подробно ответят на ваши вопросы.
Подключение трехфазного двигателя к однофазной сети через частотник
Практически вся генерируемая электроэнергия в мировом хозяйстве трехфазная. В быту, где в больших мощностях нет особой необходимости, для безопасности людей, простоты управления и удешевления применяется однофазная сеть. Что делать, если при определенных обстоятельствах возникает необходимость приспособить однополюсную бытовую розетку для питания техники, рассчитанной на трехфазное напряжение? Скажем, для подключения циркулярной пилы, насоса, наждачного или сверлильного станка.
Прежде всего, необходимо уточнить какого рода сама нагрузка. Электродвигатели бывают постоянного/переменного токаи, в то же время, делятся на синхронные/асинхронные. При этом на втором различии основываетсяэлектромагнитный принцип возникновения вращения, а постоянный/переменный тип тока используется для работы электродвигателя.
Таким образом, двигатель постоянного тока вполне может быть асинхронным. Тогда достаточно преобразовать напряжение 220 В переменного тока в 380 В постоянного тока.
Схема подключения его очень простая:
Читая чертёж слева направо, видим, что имеется однофазная сеть с переменным током. Приведение напряжения 220 к 380 В осуществляется с помощью повышающего трансформатора и мостового выпрямителя. Это делается путем выбора соответствующего соотношения обмоток каждой стороны преобразующего трансформатора.
При монтаже выпрямителя необходимо учесть полярность на выходе. Есть риск повредить конденсатор и считайте, повезёт, если этим дело ограничится. Схема мостового выпрямителя, наиболее популярная, по ней выполнена почти все выпущенные трансформаторные блоки питания. Сложно? Есть много других способов подключения.
Схема регулирования трёхфазного двигателя, подключенного в однофазную сеть через частотный преобразователь
- UZ –частотник;
- L — фаза;
- N — нулевая фаза;
- u, v, w — выводы для включения электродвигателя.
Реле времени:K1 — пуск электродвигателя;
- K2 — реверс;
- K3, K4 – II и III скорости.
Принцип построения всех преобразователей частоты одинаковый. Сначала посредством выпрямителя преобразовывается напряжение переменноевпостоянное. Далее управляемым приводом создаются разно частотные импульсы.
Импульсы, распределенные по трем фазам асинхронного двигателя, порождают вращающееся магнитоэлектрическое поле статора. Регулировка частотным преобразователем может осуществляться либо с его съемной панели, либо с помощью аналоговых входов.
Существует несколько способов подключения фаз двигателя. Классические варианты соединения фаз: «звезда» и треугольник». «Звезда» — это соединение, при коем концы фазных обмоток соединяются в один узел. Подключение фаз в «треугольник», это когда конец одной фазы является началом следующей.
Но самым распространённым способом плавного пуска асинхронного двигателя считается вариант «звезда-треугольник».
Схема подключения трехфазного двигателя к 220В через преобразователя частоты по принципу «звезда – треугольник»
Для уменьшения пусковых токов и момента (P движка больше 5 кВт) часто используется комбинированный способ.
При пуске напряжение на статор подаётся по принципу «звезда», по мере разгона мотора до номинального значения скорости, питание переключается на «треугольник». В схеме задействовано реле времени, выполняющее переключение. При этом на нём выставляется продолжительность разгона, чтобы движок успел набрать обороты по номиналу.
Заключение
Пусковые токи асинхронных двигателей очень большие и, если не делать пуск плавным, их величина теоретически может достигать значений токов КЗ. Случается, она равняется 90% от номинала двигателя. Схема подключения трехфазного двигателя к 220 В по принципу «звезда-треугольник» — это один из эффективных способов плавного пуска со снижением напряжения, преимущества которого состоят в высоком пусковом моменте, снижении пускового тока, повышении КПД, широком диапазоне регулирования скорости,полном спектре встроенных защит привода.
Сверлильный станок 2М112 — технические характеристики и особенности
От качества выполнения операций сверления и рассверливания отверстий зависят характеристики будущих изделий и узлов. Если их диаметр небольшого размера (до 12 мм) – чаще всего применяют универсальный сверлильный станок 2М112 с вертикальным положением сверла, технические характеристики которого мы и рассмотрим.
Область применения и особенности конструкции
Конструкция станка 2М112
Конструкция станка состоит из 3-х основных узлов – силового агрегата, механизма для подъема и поднятия шпинделя и плиты. Передача вращательной энергии происходит с помощью ременной передачи. Для регулирования степени натяжения ремня в станке предусмотрен механизм натяжения.
Для работы силового электрического агрегата необходимо напряжение 380 В. Максимальная мощность силового агрегата составляет 0,55 кВт. Число оборотов при этом может варьироваться от 450 до 4500.
Благодаря небольшим габаритам и простоте конструкции станок 2М112 является одним из оптимальных вариантов для обработки обычных углеродистых сталей. Поэтому его можно увидеть в небольших мастерских, малых и средних производственных организациях.
К особенностям эксплуатации станка можно отнести следующие:
- Зафиксировать глубину сверления можно с помощью упоров или контролируя показания на плоской шкале.
- Удобный механизм изменения положения ремня на шкивах. Он дает возможность оперативно изменять скорость вращения шпинделя без полного прекращения работы установки. Для этого в конструкции предусмотрены пять возможных передач.
- Расположение кнопки запуска на лицевом торце под плитой удобно – включение и выключение не представляет сложностей. Тугой механизм запуска защищается от случайного запуска установки.
Благодаря этим преимуществам с помощью станка 2М112 можно выполнять как сквозное сверление, так и формировать резьбу. Подобные технические характеристики указаны в таблице.
Параметр | Значение |
Максимальный диаметр просверленного отверстия | 12 мм |
Шпиндель | |
Минимальное расстояние до опорной плиты | 20 мм |
Максимальное расстояние до плиты | 400 мм |
Расстояние от шпинделя до колонны | 190 |
Наружный диаметр | 17,781 |
Конус, Морзе | 18 |
Длина линейки | 100 мм |
Эксплуатационные характеристики | |
Мощность двигателя | 0,55 кВт |
Кол-во скоростей | 5 |
Подключение к электросети | 380 В |
Габариты | 730*355*820 мм |
Вес | 120 кг |
Габариты плиты | 250*250 мм |

Перед работой со станком необходимо внимательно ознакомиться с инструкцией по эксплуатации, а также соблюсти правила его подключения и монтажа.
Электроудар | A380 Этап 1 GRAWDE
На самолетах Airbus усиление шасси крепится через нижнюю обшивку крыла с помощью болтов диаметром до 1 дюйма через столько же как стек размером 4 дюйма. Эта операция обычно выполняется в крыле. ящики монтажные приспособления. Ручное сверление отверстий под эти болты традиционно требовались массивные шаблоны для сверл и большие двигатели для сверл с прямой подачей. В несмотря на эти большие инструменты, отверстия необходимо просверливать в несколько этапов, чтобы уменьшить осевые нагрузки, что увеличивает время обработки.
GRAWDE (Автоматизированное буровое оборудование для крыльев с зубчатой передачей) — это буровая установка для бурения крыльев.
GRAWDE может точно позиционировать зенковку
крепежные отверстия диаметром до 1,25 дюйма через 4-
дюймовая стопка.У него есть возможность повторно синхронизироваться с функцией на
крыло или в кондукторе, подъехать к точному месту, отрегулировать
для нормальности и просверлите отверстие за один выстрел. Это
исключает использование пневматических бурильных двигателей и
шаблоны. Это сокращает время сверления до менее одного
минуту на отверстие, создавая при этом отверстия высочайшего качества.
Мобильность этой машины обеспечивает максимальную
ценный основной капитал в нескольких параллельных рабочих зонах.
При работе с GRAWDE операторы стоят на подвижной платформе на 250 мм ниже пола завода и на 500 мм выше. машинные кровати.С платформы операторы могут дотянуться до поверхности крыла, органов управления и перьевого ящика для сменные инструменты. Платформа имеет поручни и ворота с двух сторон для защиты оператора от падения и для защиты от точек среза между GRAWDE и компонентами сборочного стапеля. Также можно получить ручной доступ отогнав GRAWDE от непосредственной близости и встав прямо на станину машины.
HAWDE Пятиосевой сверлильный станок с крылом
Образец цитирования: Calawa, R., Смит, С., Мур, И., и Джексон, Т., «Пятиосевой сверлильный станок с крыльями HAWDE», Технический документ SAE 2004-01-2806, 2004, https://doi.
Загрузить Citation
Автор (ы): Рик Калава, Стив Смит, Ян Мур, Тони Джексон
Филиал: Electroimpact, Inc., Airbus UK, Ltd.
Страниц: 7
Событие: SAE 2004 Конференция и выставка по аэрокосмическому производству и автоматическому креплению
ISSN: 0148-7191
e-ISSN: 2688-3627
Также в: SAE 2004 Transactions Journal of Aerospace-V113-1
Автоматизация ускоряет сборку крыла A380
Строительство больших конструкций крыла этого самолета потребовало разработки уникального оборудования и технологий.
Генеральным подрядчиком по поставке средств автоматизации на завод Airbus в Бротоне, Великобритания, который занимается сборкой крыльев крупнейшего в мире коммерческого самолета — А380, — является Electroimpact Inc. (Мукилтео, Вашингтон). Сборка крыла происходит в несколько этапов:
- Сборка панелей крыла (этап 00), на которой задействованы четыре автоматизированные линии по производству обшивки крыла протяженностью 165 метров с использованием клепально-болтовых машин E4380 компании Electroimpact;
- Манипуляторы с крыльевыми панелями, в которых используются сервогидравлические рычаги для позиционирования панелей на следующем этапе;
- Производство сборки крыльев (этап 01), в котором используется четырехъярусное приспособление, включающее HAWDE (горизонтальное автоматизированное сверлильное оборудование для крыльев) компании Electroimpact, портативный сверлильный станок с ЧПУ и платформы для удаленного доступа к инструментам и рабочим с гидравлическим приводом. .Это оборудование работает вместе с мобильной системой GRAWDE (Автоматизированное буровое оборудование с зубчатым венцом), используемой для прикрепления ходовой части к нижнему крылу.
Electroimpact сотрудничал с Bosch Rexroth (Hoffman Estates, Иллинойс), чтобы предоставить решения для гидравлических и линейных перемещений, поскольку Rexroth могла соответствовать необходимым техническим спецификациям и требованиям графика. Электроудар потребовался для поэтапной поставки оборудования, поскольку предприятие наращивало объемы операций по размещению и просверливанию примерно 180 000 отверстий, необходимых для изготовления единственного кессона крыла Airbus 380, а затем вставки заклепок и болтов.Более высокий уровень автоматизации позволяет предприятию Broughton использовать модель технологического процесса для производства четырех пар крыльев в месяц.
Когда Airbus A380 поднимется на борт в 2005 году, это будет самый большой коммерческий самолет в мире и единственный двухпалубный четырехфюзеляжный реактивный самолет в воздухе. Базовая пассажирская конструкция рассчитана на 555 мест в трех классах, а трехэтажное грузовое судно будет перевозить до 150 тонн (165 тонн). Для сравнения: танк-транспортер C-5 Galaxy американских вооруженных сил имеет максимальную грузоподъемность 135 т (149 т).
Размах крыла A380 составляет 261 фут (79,6 м), тогда как у C-5 — 223 фут (68 м). Каждое крыло простирается на 119 футов (36,3 м) от законцовки крыла до фюзеляжа; вместе они вмещают 41 000 галлонов (155 197 л) топлива плюс шасси. Большая площадь поверхности крыла — 9100 футов 2 (845 м 2 ) — улучшает взлетно-посадочные характеристики.
Процесс производства крыла для А380 состоит из создания каркаса из лонжеронов и нервюр — конструкции крыла, — который в конечном итоге покрывается металлическими панелями.Лонжероны проходят по длине крыла. В дополнение к переднему и заднему лонжеронам, по центру крыла проходит лонжерон длиной 21 дюйм и шириной 6 футов (6,4 х 1,8 м). Нервюры пересекают лонжероны и проходят от передней к задней кромке крыла. К этому каркасу прикреплены панели, состоящие из обшивки из алюминиевого сплава, усиленной стрингерами.
Панели производятся одновременно на отдельном предприятии. Сначала формируются шкуры нужной кривизны. Затем стрингеры прикрепляются к обшивке с помощью клепально-болтовой машины E4380 в ячейке Stage 00.Готовые панели перемещаются в конструкцию для сборки. После загрузки в приспособление панели устанавливаются, просверливаются, зенковываются, приклепываются или привинчиваются титановыми стопорными болтами к предварительно просверленному каркасу. В верхнем крыле А380 используется самая большая (длина 111 футов или 34 м) одинарная обшивка.
Этот процесс требует больших затрат труда и автоматизации — изготовление полного «кессона крыла» занимает недели, что по-прежнему является быстрым по отраслевым стандартам.
Строительство крыльев А380. поставило ряд серьезных проблем для производственной группы Airbus в Бротоне и для Electroimpact.
Что касается программ Airbus, компания Electroimpact решила сотрудничать с Bosch Rexroth в области гидравлических и линейных перемещений, а также опытом применения, а также с дистрибьютором компании Pacific Power Tech (Сиэтл).
«Процесс сборки выполняется в два этапа, — поясняет Бен Хемпстед из Electroimpact, ведущий специалист по машиностроению. «Для этапа 00 компания Electroimpact предоставила четыре ряда приспособлений для сборки верхней и нижней панелей крыла. Это высокоавтоматизированный процесс, в котором клепально-болтовые машины пересекают панели, прикрепляя стрингеры к обшивке. В этой камере практически не требуется ручной труд ».
Затем панели переходят в процесс сборки несущего крыла. Размер и вес готовой панели — длиной до 111 футов и весом до 8818 фунтов (4003 кг) — создают большую проблему. «Использование кранов не работает, — говорит инженер проекта« Электроимпакт »Теодор Карагиас.«Панели крыла деформируются при подвешивании к кранам».
Вместо этого компания Electroimpact разработала многорычажный манипулятор для поддержания правильной формы панели и обеспечения точного позиционного управления при поднесении панели к конструкции крыла для крепления.
Сборка конструкции крыла Этапа 01 более трудоемка, чем предыдущая операция. Собранные панели обшивки помещаются манипулятором в четырехъярусные стапели, которые содержат другие части крыла — нервюры, лонжероны, переднюю и заднюю кромки. Для верхнего крыла требуется сочетание мобильной буровой техники (HAWDE) и доступа персонала на большой площади верхних панелей крыла. Для нижнего крыла просверлены отверстия диаметром 1,25 дюйма (31,75 мм) для крепления болтов обшивки нижнего крыла к усилителям ходовой части.
Для производства панелей обшивки компании Airbus UK и Electroimpact объединились для создания высокоавтоматизированного производства.
«В рамках этой программы мы столкнулись с несколькими проблемами, — говорит Хемпстед, — а именно с тем, как собрать крепление из стрингеров и обработанных панелей обшивки вместе в точную конфигурацию сборки, в то время как автоматизированный станок скрепляет компоненты в сборку панелей обшивки.”
Каждая поверхность крыла состоит из пяти панелей в сборе, всего 20 панелей. Завод Airbus Stage 00 производит 16 таких панелей.
Традиционно сборка панелей производилась на ручных приспособлениях, что требовало от многих квалифицированных рабочих поиска и сверления отверстий, разборки компонентов для удаления заусенцев и очистки, нанесения герметика и вставки двухкомпонентных замков с замком. Затем панели в сборе транспортировали на клепальный станок для окончательной установки заклепок. Производительность ограничивалась количеством обрабатываемых приспособлений, доступом рабочих и скоростью, а также требованиями к качеству отверстий и доработке.Качество готовой панели также ограничивалось тем, насколько хорошо приспособление удерживало компоненты в правильном контуре.
«Основываясь на нашей предыдущей работе на предприятии в Бротоне, мы в конечном итоге расширили диапазон производительности системы и повысили точность более раннего оборудования для производства панелей», — говорит Хемпстед. «Результатом является новое поколение станков для изготовления панелей крыла. Наша цель проектирования заключалась в том, чтобы дать возможность одному оператору настроить, загрузить ленты с ЧПУ, проверить точность и настроить приспособления ».
Для завода по производству панелей Airbus A380 компания Electroimpact построила четыре линии по производству панелей с верхней и нижней поверхностью в каждой. Каждая линия включает по три крепления, в которые загружены четыре панели. Шаблоны удерживают компоненты в точной форме и в точном положении, в то время как автоматизированные станки сверлят, клепают и скрепляют компоненты вместе. Герметик наносится на детали во время кондукторной нагрузки. Никаких временных креплений не используется, поэтому после крепления монтаж панелей крыла завершен. Никаких промежуточных операций по очистке и удалению заусенцев не требуется.
Процесс сборки в один прием снижает вероятность повреждений при манипулировании и неточности позиционирования (ошибки нулевой точки).Машины могут устанавливать заклепки и болты диаметром 1/4 — 1/2 дюйма (6,4 — 12,7 мм) с диапазоном стопки до 2,5 дюймов (63,5 мм). Автоматическая холодная обработка, зондирование отверстий, герметизация зенковки и установка манжеты включены.
Были использованы роликовые каретки с предварительным натягом, шарико-винтовые передачи с предварительным натягом и каретки с сепаратором, поскольку предварительный натяг обеспечивает жесткость системы и тем самым максимизирует точность.
«Точная оценка сроков поставки продукции, поставляемой поставщиками, имеет решающее значение для соблюдения графика сборки», — говорит Хемпстед.«Я рад сообщить, что с момента начала эксплуатации предприятие Stage 00 производило сборки вовремя и с гораздо большей скоростью, качеством и точностью, чем ручные и более ранние автоматизированные системы».
После изготовления панелей крыла, их необходимо переместить на стапели конструкции крыла. Их размер создает серьезную проблему при транспортировке материалов.
Для решения этой задачи команда инженеров Airbus, состоящая из Алана Фергюсона, старшего конструктора инструмента, сборка этапа 01; Аллан Эллсон, старший конструктор инструмента, сборка этапа 01; и Джим Роу, инженер-технолог; обратился к Теду Карагиасу из Electroimpact.Он возглавлял команду, которой было поручено разработать решение. Вместо кранов компания Electroimpact создала набор из шести скоординированных сервогидравлических рычагов, которые сцепляются с панелью по всей ее длине.
По словам Карагиаса, манипулировать панелью крыла с несколькими точками опоры очень сложно. «По сути, у вас есть статически неопределенная система. Панели будут скручиваться, изгибаться и толкаться, поскольку они реагируют на силы, создаваемые подъемным оборудованием.
«Чтобы решить эту проблему, два из шести рычагов контролируют вертикальное положение панели», — говорит Карагиас.«Остальные четыре рычага действуют как подчиненные и передают постоянную запрограммированную силу на панель крыла. Таким образом, когда позиционирующим рычагам дается команда двигаться вверх или вниз, рычаги поиска нагрузки следуют за ним, чтобы сохранить форму панели ».
Основная ось движения поддерживается сервоуправлением с обратной связью с помощью сервогидравлического контроллера Rexroth HNC 100. HNC объединяет линейную шкалу SSI, датчик нагрузки и сервомагнитный клапан Rexroth. Эта конфигурация обеспечивает точное управление положением с плавным переходом между управлением положением и контролем силы. По словам Карагиаса, сервоось обеспечивает контроль над положением панели, а контроллер Rexroth HNC дает несколько преимуществ системы, а именно:
- Сведение статически неопределенной проблемы к определенной, позволяя гибким панелям крыла двигаться, как если бы они были жесткой частью.
- Управление распределением силы, прикладываемой к панели крыла, для управления формой панели и ее приложением к конструкции крыла.
- Упрощение логики ПЛК системного уровня и команд управления положением.
- Обеспечивает прямой доступ ко всем критически важным системным компонентам и обеспечивает сервоуправление через порт SSI с использованием аналоговых и цифровых шин ввода / вывода, ProfiBus и CANbus, независимо от скорости сканирования ПЛК или скорости сети.
После загрузки панелей крыла в приспособление Stage 01 выполняются две операции:
- Крепление панелей крыла к нервюрно-лонжеронной конструкции, что требует автоматического сверления, крепления болтами и позиционирования с использованием мобильной сверлильной машины HAWDE компании Electroimpact; и
- Крепление усиления ходовой части через нижнюю обшивку крыла с использованием системы GRAWDE от компании Electroimpact.
Основываясь на предыдущих успехах, Airbus обратился к Electroimpact с целью автоматизации крепления панели крыла к конструкции крыла. Традиционно эта задача выполняется путем сверления, закрепления болтов и установки панелей вручную. Автоматизация процесса означала преодоление нескольких проблем с помощью уникальных решений.
«Основная проблема заключалась в том, как транспортировать оборудование от приспособления к приспособлению между левым и правым крыльями, при этом выполняя необходимую ручную работу на всех вертикальных уровнях», — говорит Райан Халдиманн, инженер проекта из группы HAWDE Electroimpact.«Фактически, станок необходимо было транспортировать по направлениям Y, (вертикальное) и X (горизонтальное), как инструментальную головку в гигантском станке с ЧПУ».
В качестве решения группа из шести человек Electroimpact во главе с Риком Калава, ведущим специалистом в области машиностроения, создала машину HAWDE — портативное устройство, которое может перемещаться по секциям панели, используя элементы, встроенные в каждое приспособление. Чтобы дать рабочим доступ ко всему периметру конструкции крыла, приспособление включает в себя откидной настил.Каждый откидной пол состоит из небольшой платформы для доступа рабочих, которая откидывается вверх, когда готовое крыло снимается. В одном зажимном приспособлении используется 150 откидных этажей, каждый из которых задействует гидроцилиндр для приведения в действие. В конечном итоге будут использоваться четыре приспособления, для которых потребуется 600 цилиндров Rexroth.
Поскольку Electroimpact отвечает как за приспособление, так и за блок HAWDE, был достигнут беспрецедентный уровень интеграции. С самого начала все мобильные элементы станка были интегрированы в приспособление.Кран-транспортер перемещает машину массой 7000 фунтов (3178 кг) с приспособления на приспособление. Для перемещения по горизонтали используется подъемник, который может выравнивать станины машины с точностью до 0,005 дюйма (0,127 мм).
Помимо облегчения доступа рабочих, установка HAWDE должна просверливать отверстия в крыле, где расположены откидные перекрытия. Чтобы добраться до участков крыла, где обычно находится настил, машина выполняет сдвиг Y , при этом колонна Y машины выступает над своим нормальным положением примерно на один метр.Это достигается с помощью системы роликовых направляющих Rexroth размера 45 для направления и гидроцилиндра для подъема пола.
Для перемещения по оси X используются направляющие с квадратным рельсом и зубчатая рейка. Все остальные оси используют традиционные линейные и поворотные подшипники. Станок включает в себя ряд инструментов: сверлильный шпиндель со скоростью до 7000 об / мин с диаметром 1/4 — 5/8 ″ (6,4 — 15,88 мм), устройство для вставки болтов для вставки вспомогательных крепежных элементов, датчик отверстия для измерения диаметров отверстий. , а также камеру для синхронизации станка с позиционирующими (исходными) отверстиями в крыле.
Параллельно с креплением панели крыла, этап 01 также включает крепление усиления шасси и обшивки крыла к конструкции шасси. Титановые болты с плоской головкой диаметром до 1,25 дюйма (31,75 мм) вставляются через стопку материалов толщиной до 4 дюймов (102 мм).
«Традиционно эта операция выполняется вручную на стендах для сборки кессона крыла», — говорит Брент Тайер, ведущий инженер по машиностроению, инженер Electroimpact, отвечающий за автоматизацию этого процесса. «Но для ручного сверления требуются массивные шаблоны для сверления и большие двигатели для сверления с прямой подачей.Работа тяжелая. Несмотря на эти большие инструменты, отверстия необходимо просверливать в несколько этапов, чтобы уменьшить осевые нагрузки, что увеличивает время обработки. Кроме того, для большинства изменений конструкции крыла требуются новые шаблоны. Принимая во внимание все переменные, добиться требуемого качества ствола вручную очень сложно ».
Airbus UK попросил Electroimpact изучить автоматизированный метод бурения. Но создание автоматизированного бурового оборудования, способного просверливать эти отверстия, при одновременном разрешении ручного доступа к зажимному приспособлению для сборки кессона крыла, было сложной задачей.
«Время, затрачиваемое на бурение в этой области крыла, составляет менее 10% от общего времени сборки кессона крыла», — говорит Тайер. «Чтобы оставаться рентабельным, буровое оборудование должно быть гибким и мобильным для использования на различных поверхностях и в разных узлах. Они используют его, а затем перемещают ».
Совместно с командой Airbus UK компания Electroimpact разработала мобильную автоматизированную систему бурения для зоны шасси A380 — GRAWDE. Программа включала в себя обширные усилия по разработке резцов. Машина может просверлить до 1 штуки.Отверстия диаметром 25 дюймов с зенковкой за одну операцию и всего 12 различных поверхностей крыла.
Конструкция аналогична пятиосевой стойке, GRAWDE использует роликовый рельс Rexroth для осей X, Y, и Z . В осях Y и Z используются шарико-винтовые передачи Rexroth.
Станок GRAWDE толкает просверливаемые детали специальной прижимной лапкой для стабилизации обшивки крыла во время сверления. Датчики или заранее запрограммированные углы обеспечивают просверливание отверстий перпендикулярно изогнутой аэродинамической поверхности.
Как и в случае с HAWDE, важно было интегрировать станок с зажимным приспособлением для крыльев. «Более 90% кессона крыла производится вручную», — подчеркивает Тайер. «Поэтому эргономичный дизайн, облегчающий доступ к ручной работе, является обязательным.
«Поскольку машине необходимо просверливать отверстия около уровня пола завода, верх станины машины расположен ниже уровня земли. Двукратный настил на уровне пола завода покрывает станины станка и обеспечивает эргономичные рабочие зоны для ручных операций ». Опять же, гидравлика (от Rexroth) используется для перемещения этажей вверх для обеспечения доступа к машинам.
Многоступенчатая операция сборки крыла для Airbus A380 включает четыре программы — изготовление панели, манипуляции с панелью крыла, сборка панели крыла (HAWDE) и усиление шасси (GRAWDE) — все это требует тесного сотрудничества между Airbus, Electroimpact, Rexroth и другие производители.
«Цель заключалась не только в разработке оборудования, которое автоматизирует ручные операции, — говорит Бен Хемпстед, — но также в улучшении качества и сокращении времени обработки».
Пневматический молотDTH — Drill King
Наши пневмоударники DTH имеют уникальную конструкцию воздушного потока, которая обеспечивает максимальную производительность.Это дает вам больше мощности в скважине, и ваши инвестиции приносят больше за меньшее время. Забойный перфоратор DK — это безклапанная ударная дрель с пневматическим приводом. Как следует из названия, пневмоударник DTH использует воздух, заставляя поршень ударять по долоте, создавая очень высокую нагрузку во время удара, что приводит к проникновению через чрезвычайно твердые породы. Этот процесс отличается от метода роторного бурения, при котором для проникновения в более мягкие породы используются вес и вращение.
Перфоратор DK DTH может быть установлен на многих различных типах сверлильных станков, использующих конфигурацию крепления с верхней головкой или приводом Келли. Буровая установка должна поддерживать достаточное давление и объем воздуха, смазку, крутящий момент, частоту вращения, удерживать и удерживать. Отработанный воздух от молота проходит через дыхательные отверстия в буровом долоте и используется для промывки просверленного отверстия. Вращение происходит от приводного двигателя в верхней части бурильной колонны; однако это не следует путать с методом роторного бурения. Усилие подачи передается на ударник через прижим и вес бурильной трубы.
Линия Drill King Hammer Line предназначена для изготовления изнашиваемой втулки с увеличенной толщиной стенки, что увеличивает срок службы.
Молот DK DTH используется во многих различных областях, включая, помимо прочего, тяжелое строительство, горнодобывающую промышленность, нефтегазовую промышленность, карьеры и водозаборные скважины.
Мы хотим помочь вам «победить конкурентов», поэтому свяжитесь с Drill King сегодня, чтобы получить пневмомолот DTH !!
Heavy Duty Hammer Line
Наш Heavy Duty (HD) молот идеален для улучшенной защиты от износа в твердых абразивных породах. Для наших клиентов горнодобывающей отрасли это стандартный молот, который они предпочитают. Линия молотов HD использует те же внутренние детали, что и наши стандартные молоты, поэтому переход от стандартного молота к HD относительно прост.
— Экономьте деньги и время, заказывая встроенные внутренние изнашиваемые компоненты в одном простом в установке комплекте. Доступен для любого молотка. Доказано, что продлевает срок службы вашего молота.
Комплекты для восстановления молотка— Продлите срок службы вашего молота, если вы используете наши ремонтные комплекты для замены внешних частей молота.Доступен для любого молотка. Это даст вам максимальную отдачу от инвестиций в продукт.
Комплекты уплотнений для молотка— Мы рекомендуем вам приобретать комплект уплотнений с каждым новым молотком. Уплотнения необходимо заменять через регулярные промежутки времени, чтобы поддерживать давление воздуха и эффективно работать с молотком.
BFC Macchine Srl — станки с алмазным канатом для мрамора, гранита и бетона
АЛМАЗ БУРОВКА СКОРОСТЬ BF 60/83 СКОРОСТЬ
Новое
сверлильный станок поколения с электрическим вращением и
гидравлическое продвижение; это особенно подходит для
выполнение отверстий для прохождения карьерной проволоки
по мрамору и каменным материалам. Производится с
прочные листы на стальных направляющих, окрашенные краской последнего поколения
краски высокой прочности. Все механические, гидравлические компоненты
и специальный двигатель высокого качества. Его
подходит для вертикальной, горизонтальной и наклонной перфорации
по мрамору. Он был разработан, чтобы избежать скручивания во время
работа, создающая чрезмерные нагрузки на ось двигателя
и с гидравлической защитой от тяги для лучшего управления
рабочий процесс и избежать поломки алмазного наконечника.Дрель
диаметр отверстия 60 мм и 83 мм с алмазным наконечником.
ТЕХНИЧЕСКИЙ ДАННЫЕ
7500w 8 л.с. 3 скорости
Двигатель 380 В, 50 Гц
Электрогидравлический агрегат с рабочим давлением 120 бар
Двигатель HP2 380 В, 50 Гц
Панель управления низковольтная
Стандартный
оборудование:
Комплект для крепления с цепями и стяжками, сервисные ключи,
зажим для гидравлического шланга.
10 трубок диам. 54 х1000 мм., коническая резьба (диам. 76 х
1000 мм.)
№ 1 алмазный наконечник PCD SPEED dia. 60 мм. (СКОРОСТЬ PCD Ø 80 мм.)
алмаз бит 80 мм диам.
гидравлический хомут для труб и вращающегося водораспределителя
Высокоскоростная звездообразная дрель имеет две модели MT703 и MT703Z, бывшая ось Z один раз, два графика движения используют инкрустацию стальной направляющей, конструкция проста. Характеристики
|
IIS 10.
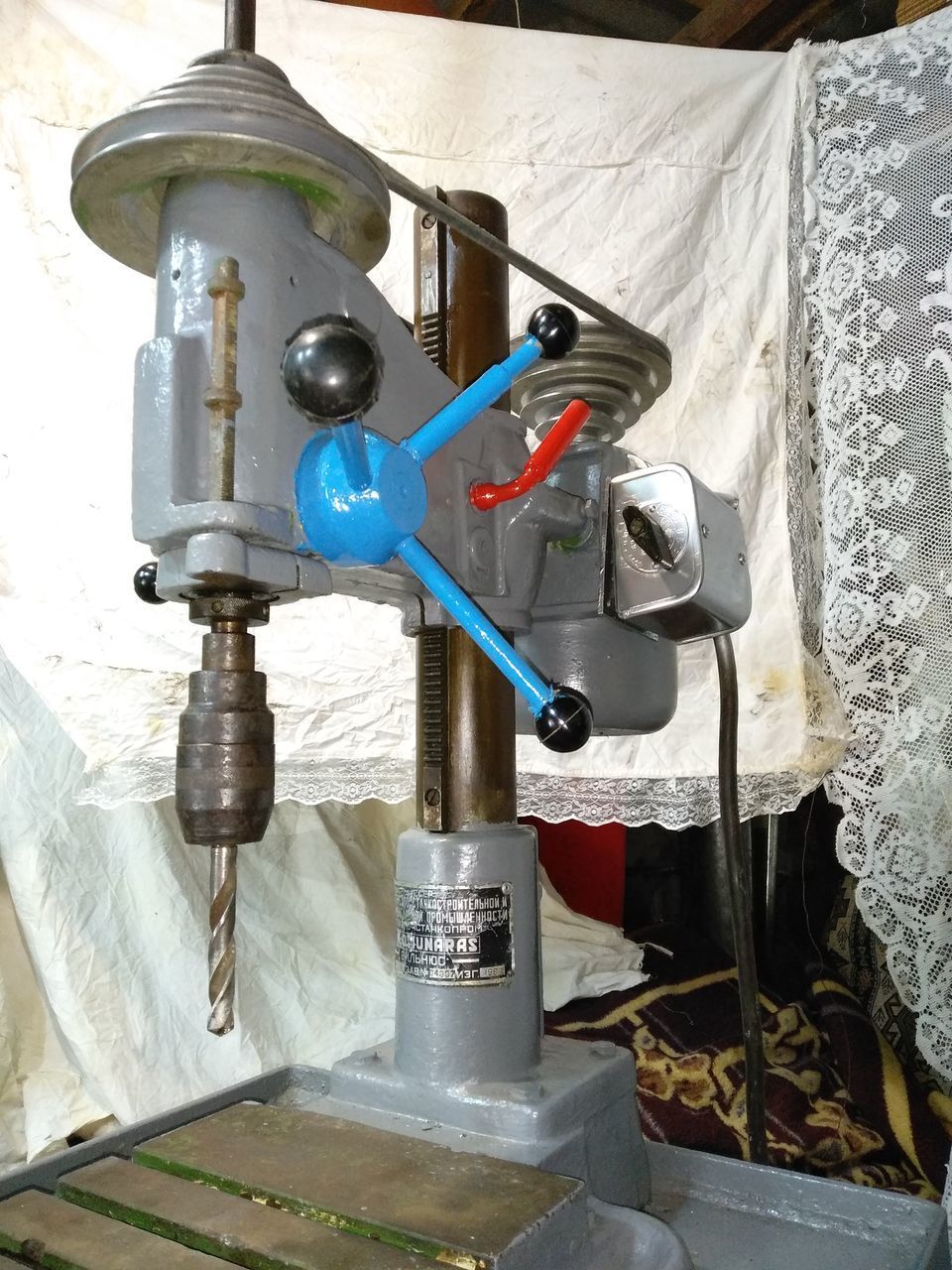
Ошибка HTTP 404.11 — не найдено
Модуль фильтрации запросов настроен на отклонение запроса, содержащего двойную escape-последовательность.
Наиболее вероятные причины:
- Запрос содержал двойную escape-последовательность, а фильтрация запросов настроена на веб-сервере, чтобы отклонять двойные escape-последовательности.
Что можно попробовать:
- Проверьте конфигурацию / систему.webServer / security / requestFiltering @ allowDoubleEscaping в файле applicationhost.config или web.confg.
Подробная информация об ошибке:
Модуль | RequestFilteringModule | ||||||||
---|---|---|---|---|---|---|---|---|---|
Уведомление | BeginRequest | ||||||||
Обработчик | StaticFile | ||||||||
Код ошибки | 1
Дополнительная информация:Это функция безопасности. Не изменяйте эту функцию, если не полностью понимаете масштаб изменения. Перед изменением этого значения необходимо выполнить трассировку сети, чтобы убедиться, что запрос не является вредоносным.![]() |