Пиролизный воздушный теплогенератор D-P — воздушного отопления жилья, ферм, теплиц., видео
Воздушный теплогенератор D-P 30-150 кВт- полу-промышленный (бытовой) воздухонагреватель пиролизный предназначен предназначен для экономичного воздушного отопления теплиц, жилых и производственных помещений, гаражей, подвалов, хлевов, кунгов, ферм, сушильных камер, где необходим кратковременный или быстрый нагрев. При этом температура в теплогенераторе без слива воды может опускаться до минусовых значений.
Твердотопливный теплогенератор D-P 30-150 кВт Благодаря высокому качеству, современному дизайну и производной технологии работает очень тихо и с большой производительностью.
В комплект воздушных теплогенераторовD-P входят нагнетательная турбина, электронный блок управления, дымосос продуктов горения
По своей конструкции полу-промышленный воздухонагревательD-P в роли стандартного теплоносителя использует горячий воздух. В связи с этим не нужно вкладывать деньги в дорогую систему водяного отопления — трубопроводы, радиаторы, запорной арматуры, систем ХВО, в связи с этим существенно упрощается и удешевляется стоимость отопления. Температура нагретого воздуха который выходит с теплогенератора имеет температуру от 40 до 120 градусов. Воздушный Теплогенератор на твердом топливе имеет высокий КПД — 95% , что позволяет при низких эксплуатационных затратах получать дешевое тепло.
В качестве топлива в Воздухонагревателях с ручной подачей используется дрова, брикеты, торф и другое топливо которое горит. По мощности теплогенераторы выпускаются от 30 до 150 кВт, что позволяет отопить даже жилое помещение или теплицу площадью от 300 до 1700 м.кв.
Области применения Воздушных теплогенераторов
- Обогрев промышленных помещений (склады, цехи, выставочные залы)
- Обогрев ферм и теплиц
- Сушение зерновых. (Горизонтальные стационарные сушилки, вертикальные силосные сушилки
- Сушение Кукурудзы
- Сушение сухофруктов, трав, хмеля
- Сушение древесины (стационарные и транспортабельные камеры сушилки)
Модельный ряд Теплогенераторов
Серийно выпускается 3 модели воздушных теплогенераторов с номинальной мощностью от 30 до 5000 кВт, для отопления теплиц и помещений с максимальной площадью от 300 до 50000 м2 соответственно.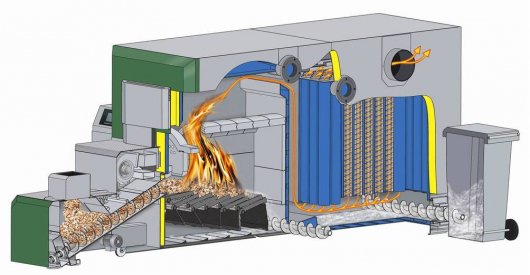
Основные типы теплогенераторов
- P — Пиролизного типа (ручная подача дров)
- R — Ручная подача дров или угля
- RA — Ручная и автоматическая загрузка топлива (пеллет, угля-семечки, зерна, дров, кускового угля)
- A — Полностью автоматическая подача топлива (пеллет, угля-семечки, зерна)
Преимущества пиролизных воздушных теплогенераторов серии D-P
- Ответственные элементы футеровки выполнены из жаростойкого бетона производства США.
- В конструкции теплообменника используется жаропрочная сталь (в-ва Германии, Италии).
- Электронная система автоматической поддержки температуры на выходе с цифровой индикацией.
- Безопасная конструкция, которая исключает попадание продуктов сгорания в теплоноситель (воздух)
Принципиальная схема воздушного теплогенератора пиролизного D-P 30-150 кВт
Технические характеристики воздушного теплогенератора D-P 30-150 кВт
МОДЕЛЬ: | D-30P | D-50P | D-100P | D-150P |
Мощность, кВт: | 30 | 50 | 100 | 150 |
Объем помещения, м3 | 800 | 1500 | 3000 | 4500 |
Производительность на выходе, м3/ ч: | 1000 | 1700 | 4700 | 5000 |
Температура воздуха на выходе, ° С: | 90 | 90 | 65 | 90 |
Рабочий цикл, ч | 4-8 | 4-8 | 4-8 | 4-8 |
Расход топлива (при влажности-10%), кг / ч: | 9-11 | 15-20 | 30-40 | 40-50 |
Объем топливного бункера, дм3 | 130 | 310 | 430 | 600 |
Максимальная длина поленьев, м: | 0,5 | 1,0 | 1,0 | 1,0 |
Потребление электроэнергии, кВт: | 0,55 | 1,5 | 4,0 | 5,5 |
Напряжение питания, В: | 220/380 | 380 | 380 | 380 |
Вес, кг: | 530 | 1050 | 1550 | 2100 |
Габариты (ВхШхД, мм): (или необходимая площадь, м2) | 1900 700 1000 | 2650 930 1630 | 2650 970 1890 | 2960 140 420 |
Пиролизный теплогенератор (предтопочная камера) для парового котла ДКВР
Пиролизные теплогенераторы это суперсовременная конструкция и новый подход в сжигании твердого топлива. теплогенератор твердотопливный типа СВДТ спроектирован инженерами с 25 летним опытом в области теплотехнической инженерии и подступает для модернизации парового газомазутного отопительного прибора тип ДКВР.
Твердотопливные теплогенераторы типа СВДТ с складом для горючего шнековой подачей твердого топлива созданы для горения ( опилок, щепы, шелуха подсолнечника, пеллеты, брикеты, торфа и т.д.) на производственных и сельскохозяйственных предприятиях использующих газовые, газомазутные паровые отопительные приборы, а также сушилки зерна и сушилки барабанного типа.
Инновационные пиролизные теплогенераторы (предтопки), дают возможность применять котлоагрегаты без утраты их теплотехнической мощности. Данный вид обогревателей помогает устанавливать их на существующую систему. Чистка золы быть может как в ручном так и в автоматическом режиме в необходимости от зольности горючего. Автоматическая подача твердого топлива и чистки золы разрешают системе работать безпрерывно 24/7, другими словами бесперебойная подача пара.
Сжигание твердого топлива происходит в 2 шага, поначалу горения происходит в основной камере горения и пиролиза 2-ой шаг это вихревая камера с вторичной подачей кислорода где и происходит абсолютное горения пиролизного газа, таковым образом достигается КПД 95%, уменьшаются вредные выбросы товаров сжигания в атмосферу (наименьшие чем от газовых систем). теплогенератор пиролизный типа СВДТ представляет собой конструкцию, сваренную из качественной жаростойкой стали S = 6, 8, 10 мм. Обратите внимание на то, что внутренняя часть теплогенератора на твердом топливе вполне футерованная огнеупорным кирпичом, который выдерживает высочайшие температуры до 1600 градусов цельсия.
В пиролизном теплогенераторе применена неповторимая охлаждающая система корпуса, забор кислорода для горения осуществляется по всему периметру с нижней части теплогенератора пиролизного проходит верх к пропеллерам и подается в камеру горения нагретым до температуры 45-50 градусов Цельсия. Решетки, на которых происходит процесс горения, сделанные из шамотного кирпича, что продлевает срок службы предтопка, предотвращает деформацию.
Блок управления, помогает предтопку работать в автоматическом режиме, персонал на программаторе лишь выбирает нужное давление пара. Как опциональная функция, блок управления комплектуется дистанционным управлением по телефону либо ПК.
Бункер с автоподачи делается персонально в каждом случае, беря во внимание условия расположения конструкции. Опциональной опцией комплектуется датчиками уровня горючего.
Удаление золы происходит в ручном режиме, для высокозольного твердого топлива комплектуется автоматизированной шнековой системой удаления золы.Принципиальным показателем является экономия средств на топливные ресурсы, которые составляют от 50 до 80% по сопоставлению с газовыми системами. Ниже в таблице приведен пример на 1, 5, 10 тон пара в час. Горючее щепа 35 % влажности 2600 ккал/кг
Назначение Предтопочной камеры
- Усовершенствование газовых , газомазутных Паровых котлов ДКВР ( E, КЕ, Loos, Bosch, AVOGADRO и др.
)
- Усовершенствование газовых Водогрейных котлов
- Усовершенствование газовых воздушных зерносушилок, сушилок дерева
Установка теплогенератора пиролизного
Устройство устанавливается на существующую систему (паровой котлоагрегат) без реконструкции бойлерной, благодаря персональной разработке для каждого объекта теплогенератор твердотопливный просто адаптируется к оборудованию.
Используемые отопительные приборы для перехода на био горючее
ТИП котла | МОДЕЛЬ котла | СОСТОЯНИЕ ИЛИ ТЕМПЕРАТУРА ПАРЫ, ° С |
Газомазутный паровой котел типа ДКВР | ДКВР- 2,5-13, ДКВР- 4-13, ДКВР-6,5-13, ДКВР — 10 -13, ДКВР- 20-13-250, ДКВР- 6,5-2,3, ДКВР- 10-23 | Насыщенный |
*Газомазутные паровые устройства ДКВР-2,5; 4; 6,5; 10; 20 (Двухбарабанный котел Вертикально — водотрубный Реконструированный) с газомазутными топками созданы для выработки насыщенного либо перегретого пара, идущего на технологические нужды производственных компаний, в системы отопления, вытяжки и горячего водоснабжения котлоагрегат ДКВР. ДКВР имеет сборную конструкцию, что разрешает устанавливать его в бойлерной, не разрушая стенок, и быстро подключить к уже имеющимся системам.Возможен перевод отопительного прибора с 1-го вида горючего на иной.Возможность перехода отопительного агрегата в водогрейный режим.Суперсовременные отопительные приборы ДКВР оснащаются таковыми горелками, которые разрешают применять фактически все самые суперсовременные технологии и принципы регулирования почти всех действий горения горючего и работы отопительного агрегата.
Основное Горючее теплогенератора
- Щепа
- Пеллета
- Торфобрикет
- Бурый уголь
- лузга семечки
Достоинства теплогенератора пиролизного
- Срок окупаемости 1-3 месяца
- 1 год гарантии
- Срок службы 15 лет
- Решетки из шамотного кирпича. Решетки изготавливают из шамотного кирпича, что предотвращает их от прогорания либо деформированию. По мере необходимости их можно просто заменить.
- Цифровая панель управления
- КПД 95%
- автоматизация процесса подачи и горения твердого топлива.
- Аварийная защита поврежения шнека. В случае попадания постороннего объекта в бункер что приводит к остановке шнека 2-ой шнек работает продуктивнее чтоб дополнить нехватку горючего. Остановка шнека устраняется нажатием клавиши РЕВЕРС что выталкивает сторонний объект в бункер.
- Облицовка внутренней части теплогенератора пиролизного огнеупорным кирпичем
- Камера пиролиза газов СО. В вихревой камере происходит полное сгорание пиролизного газа, который появляется в процессе горения твердого топлива. Таковым образом увеличивается температура газов, уменьшаются вредные выбросы товаров сжигания в атмосферу. Камеры дожига с вторичной подачей кислорода изготавливают от 1 МВт.
- Автоматическое удаление золы (для высокозольного твердого топлива)
- Система пожаротушения
- Размещение склада с фронта теплогенератора твердотопливного с правой либо левой стороны (в необходимости от особенностей монтажа)
- Воздушное остывание корпуса
- Установка без реконструкции отопительного агрегата
- Котловая сталь 6, 8, 10 мм.
- Дистанционное управление (опциональная функция)
- Полная сервисная поддержка
Твёрдотопливный теплогенератор
Существует множество видов теплогенераторов. Это газовые, жидкотопливные (дизельные), универсальные (по использованию топлива), электрические и твердотопливные. Теплогенератор на твердом топливе применяется как оборудование для обогрева помещений различных площадей и направлений, таких как сельскохозяйственные помещения, склады и производственные помещения. Твердотопливный теплогенератор работает как на угле, дровах, топливных брикетах, гранулах, так и на отходах деревопереработки — опилках, стружке, щепе, и других. Работает он по принципу принудительного воздухообмена. Различают классический и пиролизный воздушный теплогенератор на твердом топливе.
Пиролизный воздушный теплогенератор
Классический твердотопливный теплогенератор работает по принципу «обычной печи», то есть сгорание топлива происходит в камере сгорания, и выделяется тепло.
При работе пиролизного теплогенератора в камеру загрузки помещается топливо и поджигается. Под воздействием высоких температур вкупе с недостатком воздуха происходит обугливание топлива и выделяется газ. Нагрев газа происходит в камере сгорания, где он, собственно, сгорает, после чего вентилятором прокачивается воздух, нагревается и подается на обогрев воды, воздуха, или другие технические нужды. Происходит более равномерное отапливание помещения за счет направленного движения нагретого воздуха. Такие котлы более удобны и их производительность выше, имеют почти полное сгорание топлива.
Чугунные и стальные тепрогенераторы
Также тепрогенераторы могут быть чугунные и стальные. Чугунные менее чувствительны к качеству воды, долго нагреваются и остывают, конструкция таких котлов позволяет производить чистку реже, и они довольно неприхотливы в эксплуатации. Стальные теплогенераторы, как правило, более компактны и имеют привлекательный внешний вид, быстро нагреваются и более удобны в эксплуатации.
Выбор теплогенератора
Если Вы думаете какой теплогенератор купить, то Вам необходимо узнать о возможностях данного оборудования — теплогенератор на твердом топливе безопаснее и легче в использовании, чем газовые или жидкотопливные, поэтому подходят для использования не только в производственных помещениях, но и в частных домах. Он обладает массой преимуществ:
- возможность регулирования самого процесса горения топлива, регулируя подачу воздуха;
- высокая экономичность топлива и горения, в результате чего чистить агрегат следует реже, чем другие;
- воздушный теплогенератор на твердом топливе экологически чище работает, чем остальные. Это обусловлено экологичностью сырья для топлива, так как при сгорании угля или древесины выбросы токсичных веществ значительно меньше, чем при сгорании газа или нефтепродуктов;
- Высокая производительность. Сгорает не только топливо, но выделяемый газ, что способствует повышению коэффициента полезного действия и уменьшению отходов;
- возможность выбора котла нужной мощности;
- компактные размеры.
При выборе теплового оборудования, конечно, встает вопрос: «где теплогенератор купить на твердом топливе?» У нас! Предприятием «Вятские котлы» за последние 17 лет выпущено более 400 единиц теплового оборудования, в десятках регионах России и Белоруссии используются наши котлы. Мы тщательно следим за производством с начальных стадий до готовой продукции, имеем огромный опыт в производстве и гарантируем Вам высокое качество. На сайте нашей компании Вы можете просмотреть нашу продукцию, просмотреть документы на нашу продукцию: патенты, сертификаты, заключения. Узнать стоимость продукции и помочь определиться с вопросом, какой же теплогенератор необходим именно Вам, помогут наши консультанты. Чтобы Вы не ошиблись в том, какой теплогенератор купить на твердом топливе, мы подберем Вам самый лучший и удобный для Вас вариант, поможем определиться с видом, моделью, размерами и энергопотреблением необходимого Вам теплогенератора, в точном соответствии с Вашими пожеланиями и(или) производственными необходимостями.
- < Назад
- Вперёд >
Теплогенератор твердотопливный
Главная \ Теплогенераторы \ Теплогенератор твердотопливныйТеплогенератор
В теплогенераторах применяется принцип пиролизного котла. Теплогенератор состоит непосредственно из теплогенератора, вентилятора, дымососа. Теплогенератор работает в ручном режиме загрузки топлива — в стандартном комплекте поставки. Энергия, которая возникает в процессе горения (пиролиза) снимается со стенок теплообменника воздухом, который нагнетает вентилятор и подает в отапливаемое помещение. Продукты горения выводятся через дымовую трубу.
Пиролизный котёл — одна из разновидностей твердотопливного котла, в котором топливо (дрова, отходы деревообрабатывающей промышлености) и выходящие из него летучие вещества сгорают раздельно.
Топливо
Наиболее высокую эффективность пиролизные котлы показывают при использовании топлива с высоким выходом летучих — древесине (дрова, древесные отходы, топливные брикеты и пеллеты).
Конструкция
Топка пиролизного котла разделена на две части. В первой части (газифицирующая камера, или камера загрузки при недостатке кислорода медленно горит и пиролизуется топливо, а выделяющиеся при этом газы догорают во второй части (камера сгорания), куда подаётся вторичный воздух. Потери энергии при отводе тепла минимизируются.
Дрова (или иное топливо) загружаются в бункер. Их поджигают, дверца закрывается и запускается дымосос. При недостатке воздуха и под действием высокой температуры (200—800 °C и выше) происходит обугливание и выделение древесного газа, то есть собственно пиролиз. Выделившиеся продукты (в основном углеводороды, угарный газ и водород, плюс азот из первичного воздуха) поступают под колосник. Там к продуктам пиролиза подмешивается вторичный воздух, в котором летучие сгорают; часть тепла при этом возвращается к нижнему слою дров и поддерживает пиролиз. Полученное тепло может быть использовано для нагрева теплоносителя — воздуха.
При полной или частичной замене газовых котлов пиролизными котлами в условиях России – период средний период окупаемости составляет 1-1,5 года.
Схема работы пиролизного котла- 1. Топливо
- 2. Первичный воздух
- 3. Вторичный воздух
- 4. Уходящие газы
- 5 и 6 вход и выход воздуха (теплоноситель).
- А. Камера газификации
- В. Колосник
- С. Камера дожигания
- D. Газоход
- E. Дымосос
Теплогенератор предназначен для отопления бытовых, производственных, складских помещений, мастерских площадью от 300 до 15000 м2, а также для сушки древесины, продуктов сельского хозяйства, теплиц и
Теплогенераторы промышленные технологические для сушилок и пиролизных печей, небольшой обзор.

Ну начнем с простого, вот выносной теплогенератор пиролизной печи углежжения, он работает так, с начало разжигается на дровах- тут обзол, горбыль, дымовые горячие газы обогревают реторты в печи, куда заложены березовые дрова… затем как реакция пиролиза пошла в него поступают пиролизные газы и уже тепло сгорающих в теплогенераторе пиролизных газов поддерживают процесс пиролиза. Такой по сути теплогенератор я применяю и на печах по переработки отработанных РТИ в топливо.
Конструкция «трубы» дает довольно хорошую надежность данному теплогенератору, внутри он обложен высокотемпературным кирпичом.
Пиролиз в печи происходит при температуре более 350 градусов… ну и до 650..далее нежелательно… выйдет печь из строя, этот теплогенератор справляется с данной работой, проблем нет.
Ну а вот просто на дровах под печью типа УВП, так для коллекции, такие печи думаю уже врят ли кто использует… тут небольшая температура..поэтому как правило после разжега дверь закрывается и процесс пиролиза идет несколько суток..ну а дрова в печь-теплогенератор подкладываются по мере сгорания..но обзор есть обзор:
Ну и вот новенький еще не эксплуатировали подобный теплогенератор для барабанной сушилки, сушки сырья, для производства пеллет- тоже на отходах типа горбыля:
Очень хорошо сделали свод..вот этот свод печи теплогенератора дает гарантию надежной долгой работы:
Ну и видня технология изготовления свода :
В общем неплохо!
Ну а далее обзор воздухообменного теплогенератора так скажем. .то есть дымовые газы нагревают через стенку атмосферный воздух который и служит агентом в технологическом процессе сушки. Мне повезло, аппарат разобрали после года службы на технологический ремонт, так что очень хорошо все видно. Кстати о нем очень неплохие одзывы, ну а то что сгорел колосник тут вина скорее тех кто эксплуатировал, так скажем «поджарили» немного засыпав брак брикетированного древесного угля…Но машинка выдержала по сути… а так он должен работать на щепе и опиле… естественной влажности по сути..
Общий вид.. слевасам теплогенератор куда засыпаются щепа и опилки ну а справа сам теплообменник… Сверху видим дымосос вентилятор котрый обеспечивает тягу горения опила и щепы.. ну а внизу вентилятор для воздуха теплообмена, который нагнетает воздух от проходит через теплобменник и уже горячий идет в камеру сушки температрура сушильного воздуха в районе 120 градусов..ну а температура в теплогенераторе при горении щепы и опила в районе 1000 градусов и более..
Вот вид сверху куда засыпается щепа и опил:
Сейчас тут нет колосниковой решетки , её вытащили для замены:
Топочный люк который расположен выше колосниковой решетки:
Ну а это поддувальные люки куда идет забор воздуха, находятся под колосниковой решеткой, кстати и колосниковая решетка сгорела там где они были в основном открыты:
Воздуховод горячего воздуха который подает его в сушилку:
Ну а это вентилятор дымосос обеспечивающий горение . .тягу.. и вывод дымовых газов после отдачи тепла воздуху , который и подается потом в сушилку:
Вид со стороны теплообменника:
Ну и выполнен такой немаловажный нюансик как воздухозаборник для полного сгорания щепы и опила в системе теплообменника:
Хорошая штуковина..но система от перегрева тут подразумевает автоматическое закрывание заслонки при повышения температуры выше положенной..что на мой взгляд имеет недостаток- инерцию… я бы просто на вентилятор тяговый- дымосос поставил бы частотник..и плавной регулировкой тяги обеспечивал бы температурный режим..хотя заслонку бы не убирал..но это мое частное мнение.
Приборный щит:
Плохо получился, потом сделаю другую фото и заменю..
Не стоит недооценивать это оборудование в связи с тем что показаны сгоревшие колосники.. машина проработала в таких экстремальных условиях и выдержала год.. а это редкость.
Кстати этот теплогенератор работает на сушилку брикетов которые делаются из древесноугольной пыли, считайте отходов, кто занимается производством древесного угля знает сколько таких отходов получается. Но возможно и эти отходы превратить в хороший товар!
Суслов Михаил Борисович, ООО «Экосинтез»
Тел: 8-911-281-95-62
эл. почта: [email protected]
Теплогенераторы на щепе, опилках, древесных отходах
Внимание: эта страница находится в архиве. Перейти на действующий сайт
Для работы сушилки необходим теплогенератор, который вырабатывает необходимое для сушки тепло. На заводах по производству биотоплива теплогенератор обычно работает на том же сырье, которое используется для производства готовых пеллет или брикетов. Чаще всего это древесные отходы — опилки, щепа, в хороших теплогенераторах сжигается кора и прочие не используемые отходы древесины.
В других случаях это может быть лузга подсолнечника, высушенный торф, солома, прочие растительные отходы.
Можно использовать теплогенератор соответствующей мощности на любом другом топливе: будь то газ, мазут или электричество, однако, по причине высокой цены, практически имеет смысл альтернативно рассматривать только природный газ, если он есть на производстве и все равно используется, однако такие решения применяются редко, т.к. обычно выгоднее сжигать именно подлежащие утилизации отходы.
Далее мы будем говорить о теплогенераторах на древесных отходах, как наиболее часто встречающемся варианте. Как уже было сказано, теплогенератор дает тепловую энергию для сушки. Рассмотрим основные факторы, влияющие, в том числе, на его эксплуатационные характеристики.
Топить теплогенератор разумно наименее ценными отходами, обычно влажной щепой, которую получают из горбыля и других неиспользуемых кусковых отходов. Однако чем более влажное топливо используется, тем сложнее его сжигать. Дело в том, что перед тем, как древесина начнет гореть, из нее должна испариться лишняя влага, на что может затрачиваться большая часть энергии, заключенная в древесине. Так, если влажность дерева превысит 60%, то вся энергия, которая выделится при сжигании, уйдет на испарение влаги и такое топливо гореть не будет.
Напомним, что, в частности, отходы пилорамы имеют естественную влажность на уровне 40-50%, при хранении они легко могут набрать 60% и более, то есть их влажность изначально находится недалеко от допустимой границы. Вот почему очень важна способность теплогенератора стабильно работать на таком топливе.
Влияние влажности топлива на его потребление теплогенератором мощностью 1МВт приведено в таблице ниже:
Влажность отн, % | 10% | 20% | 30% | 40% | 50% |
Расход топлива на 1МВт *, кг | 230 | 290 | 340 | 420 | 535 |
( * ) — Для сушки материала со скоростью 1 т/час потребуется 1 МВт тепловой мощности. Расход топлива при этом будет приблизительно (с поправкой на КПД и породу древесины) соответствовать таблице .
Наиболее просто и эффективно использовать в качестве топлива сухой материал. Идеальное топливо — стружка после обработки сухой доски, отлично горит и не вызывает проблем. С другой стороны такой материал представляет ценность сам по себе и его можно использовать для производства продукции, а не сжигать.
Часто задается вопрос о возможности ручной загрузки топки крупными отходами, которых много на предприятии, без предварительного измельчения в щепу. На автоматических линиях загружать топливо вручную нельзя, потому что уже при открывании дверцы топки нарушается кислородный режим горения, а если еще туда закинуть дрова, то температура резко упадет, что вызовет сбой в работе сушилки.
С другой стороны, если в качестве теплогенератора предлагается примитивная печка (в увеличенных габаритах), то возможность загрузки топки вручную будет преподноситься, как достоинство, часто это единственный вариант. Оценить это можно будет немного поэксплуатировав данный агрегат, потому что кочегары хороши на допотопных котельных, которые обогревают помещения. Не так важно выше или ниже там температура, лишь бы не замерзнуть. Если же от кочегара зависит работа полностью автоматического импортного пресса, то результат вполне предсказуем.
В работе теплогенератора, особенно на топливе повышенной влажности, решающее значение имеет конструкция топки.
Относительно простая конструкция.
Горение происходит в потоке воздуха, когда поступающее топливо срывается, закручивается и горит в сильном воздушном вихре, создаваемом системой дутья.
Известные конструкции не работают на топливе влажностью выше 30%, поскольку вихрь не раздувает мокрые опилки или щепу. |
Слой топлива создается на сужающейся колосниковой решетке и продувается снизу специальной системой дутья. В верхней части топлива образуется т.н. кипящий слой, который непрерывно горит. Теплогенератор, работающий на этом принципе, имеет более сложную конструкцию, однако может эффективно работать на влажном топливе. Кусковая древесина предварительно измельчается до размеров щепы и подается в топку с помощью мощного шнека в зависимости от сигнала контроллера, обрабатывающего показатели датчиков температур. |
Процесс горения древесины изначально разбит на 3 стадии:
- сначала испаряется влага, а горения еще нет;
- затем начинается пиролиз — выделение из древесины т.н. пиролизных газов, горение которых можно наблюдать в виде языков пламени. Отдача энергии относительно невысока;
- затем древесина превращается в уголь, который горит с высоким выделением энергии без внешнего пламени;
Пиролизный теплогенератор должен быть разбит на две раздельные камеры. В первой камере находится сухое топливо и она нагревается. Выделяется пиролизный газ и поступает во вторую камеру, где горит. Достоинством такого способа можно назвать отсутствие искр, поскольку горит газ, а не опилки. Топливо превращается в уголь и дожигается каким то другим способом.
Эффективному пиролизу всегда мешает необходимость первоначального испарения влаги, поэтому такие устройства очень чувствительны к влажности и фракционному составу топлива, имеют ограничение по допустимой влажности топлива в 20-25%.
Следует отметить, что модное слово «пиролиз» является предметом различных спекуляций в среде производителей печек и котлов, хотя, как было указано выше, без фазы пиролиза не обходится горение даже обычного костра, поэтому любой поставщик, применяющий приставку «пиролизный» к своему изделию, будет безусловно прав.
.
Как мы видим, многие теплогенераторы имеют ограничение по допустимой влажности топлива. Чаще всего верхний предел составляет 30% и это является серьезной проблемой, потому что в реальности возможны два варианта:
- имеется сухое сырье, которое вообще не нужно сушить и вопрос отпадает;
- имеются отходы «естественной» влажности в 40% и выше, другими словами, топить такой теплогенератор оказывается нечем;
- чтобы получить топливо влажностью 30%, щепу необходимо предварительно высушить в естественных условиях, например несколько месяцев хранить под навесом с периодическим ворошением, что возможно, но хлопотно и лучше заказать более подходящий теплогенератор.
Данная проблема стоит очень остро перед всеми производителями теплогенераторов и котлов, в том числе и за рубежом, просто у нас она обычно замалчивается. Производитель, утверждающий, что его изделие может работать на любых отходах, любой влажности, намеренно вводит покупателей в заблуждение. Правильнее будет приобрести более дорогой теплогенератор, хотя бы частично лишенный этих недостатков.
Для полносты картины следует упомянуть еще одно возможное решение. Если сушилка имеет запас производительности и имеется избыток сырья, то можно сделать обратную связь — отбирать часть уже высушенного материала после сушилки и пневмотранспортом подавать его в топливный бункер теплогенератора.
Таким образом проблема будет решена, но порядка 200 кг с каждой тонны готовых опилок, на сушку которых были сделаны все затраты, пропадут зря и такое решение нельзя назвать эффективным.
Проекты котлов и теплогенераторов! — LiveJournal
Проекты котлов и теплогенераторов! WhatsApp: +375447279575 viber +375447279575 Предлагаю сотрудничество в разработке твердотопливного котла, (водогрейный, паровой: обычный и термосифон-тепловая труба) теплогенератора, предтопка, топки, сушилки! Помогу изготовить собственными силами: котел, теплогенератор, предтопок (2 м. куб. загрузка), экономайзер для существующего котла, теплообменник, водонагреватель, пропарку бетонных изделий. Чертежи, схемы, фотографии, авторское сопровождение. По интернету, приезд на место, есть опыт, работает хорошо. |
semilet56
semilet56Cделал Котел-Теплогенератор по принципу Термосифон-Тепловая труба. Использовал развитую, непроточную теплообменную поверхность, в 2 раза меньше!!! Процесс теплопередачи происходит в большом количестве небольших глухих полостей (непроточных) вваренных в общий проточный коллектор. Что облегчает подвод тепла к толще теплоносителя. Замкнутый объем теплоносителя. Для сушилки досок 30 м.куб. Температура пара около 130 град., давление 0.3 МПа. (Можно 158 град. и 0.6 МПа-давление пара). В 30 град. мороз при дырявых дверях сушилки, легко набирал 60-80 град. Испытал в водном режиме, сильно хуже парового. Обьем воды 70 литров. Предтопок 2 м.куб. на сырых опилках и дровах, загрузка сверху (транспортерной лентой или шнеком). Теплообменник-испаритель (1200х420х410). Паровой калорифер (1000х1000х200) конденсирует пар, охлаждаясь от вентилятора. Замкнутый объем теплоносителя исключает образование накипи. 1 грамм воды при конвективном теплообмене, в толще воды, переносит 20 кал., а 1 грамм испаренной воды переносит 540 кал. Разница в 27 раз. По аналогии пешеход-велосипедист (книга: «Что такое тепловая труба?» Елисеев В.Б., Сергеев Д.И. и др., М. Энергия, 1971 г.). Критический тепловой напор 1000 кВт на 1 м.кв., когда происходит пузырьковое кипе-ние, а не пленочное. При котором резко падает теплоотвод от поверхности нагрева. В эту схему хорошо вписывается моя теплообменная поверхность |
Предтопок — (на естественной и принудительной тяге) оригинальной конструкции, от 2 до 4 м.куб., загрузка сверху и спереди, дрова и опилки. Нажмите на изображение для увеличения: .Конструкция предтопка позволяет устанавливать со стандартными котлами, для перевода на отходы древесины, биотопливо (лузга, жмых, солома, тырса…), дрова, торф, торфокрошка, брикет, щепа. Для сушки древесины и опилок, отопления, нагрева воды, экономайзер, паровой котел, и т.д. |
semilet56
Предтопок-Теплогенератор с искрагасителем для сушки опилок и досок! 2000 кВт.
Предтопок-Теплогенератор с искрагасителем для сушки опилок и досок!
Предтопок на твердом топливе к теплогенератору для сушки зерна 1000 кВт.
BLAGO — TT — Вспомогательное оборудование
Устройство и принцип работы
Пиролизный теплогенератор с фронтальной камерой дожигания горючих газов содержит корпус 1, водяную рубашку 2, образованную в корпусе 1, дверной проем 3, накопитель топлива 4, расположенный в корпусе 1 над камерой сгорания 5, механизм подачи воздуха в камеру сгорания. камера 5 и камера дожигания горючих газов 6, отверстие 7, соединяющее камеру сгорания 5 и камеру дожига горючих газов 6, и зольную камеру 8, расположенную под камерой сгорания 5.
Отверстие 7 и камера дожигания горючих газов 6, расположенные под нижней стенкой 9 дверного прохода 3, и каналы 11, установленные за боковыми стенками 10 дверного проема 3, для отвода горючих газов из камеры дожига горючих газов 6.
Механизм подачи воздуха в камеру дожигания горючих газов 6 осуществляется через сквозное отверстие 12, соединяющее камеру дожигания горючих газов 6 с зольной камерой 8 и клапаном 13, регулирующим объем поступающего извне воздушного потока.
Клапан 13 совмещенный с пластиной зольного ящика 14 и площадь сечения сквозного отверстия 12 регулируется перемещением зольного ящика 14. Камера дожигания горючих газов 6 футерована огнеупорным материалом. При этом верхняя плита из огнеупорного материала в камере 6 дожигания горючих газов является нижней стенкой 9 дверного прохода 3 и выполнена съемной. Каналы 11 для отвода горючих газов из камеры дожигания горючих газов выполнены в водяной рубашке 2.
В каналах 11, соединенных с рычажным механизмом 16, установлены стимуляторы турбулентности 15. Тяговые механизмы 16 расположены по бокам дверного проема 3 и предназначены для возвратно-поступательного движения стимуляторов турбулентности 15.
За счет возвратно-поступательного движения стимуляторов турбулентности 15 каналы 11 очищаются от золы, смол и гудрона. Зольник 8 имеет колосниковую решетку 22. Колосниковая решетка 22 очищается топочным механизмом 17. Тяговый терморегулятор 18 установлен в водяной рубашке 2 котла.
Тяговый терморегулятор 18 i соединен с поворотным клапаном 19 цепью. Имеются ковш 20 и змеевик аварийного охлаждения 21, колосниковая решетка 22.
Описание работы теплогенератора
Пиролизный теплогенератор с фронтальной камерой дожига горючих газов работает следующим образом. Дверь дверного гарнитура 3 открыта. Сухая щепа кладется на колосниковую решетку 22. Разжигается. При воспламенении щепы необходимо положить на нее дрова, уголь или опилки.
Затем дверь дверцы 3 закрывается. При этом хранилище топлива 4 должно быть плотно закрыто. Задана подача воздушного потока, движущегося в камеру дожигания горючих газов 6. Для этого край клапана 13 устанавливается посередине проходного участка сквозного отверстия 12; зольник 14 перемещается одновременно.
Окончательная регулировка основана на цвете пламени в камере дожигания горючих газов 6, наблюдая за ним через смотровое окошко.Пламя должно быть соломенного цвета при оптимальном режиме сжигания топлива. Шкала в терморегуляторе тяги 18 установлена на 85 o C (для воды), а поворотный клапан 19 — в среднее положение. Но это не должно быть связано с цепью. При повышении температуры теплоносителя до 85 o C (определяется по показаниям термопар) поворотный клапан опускается с зазором 3 мм и цепочкой соединяется с тягодутьевым терморегулятором 18. Регулировка была сделана. Температура охлаждающей жидкости изменяется в процессе сгорания топлива.
Положение поворотного клапана 19, соединенного цепью с терморегулятором 18 тяги, изменяется пропорционально. При подъеме температуры охлаждающей жидкости рычаг терморегулятора тяги 18 поворачивается. Поскольку он соединен цепью с поворотным клапаном 19, поворотный клапан 19 опускается вниз, закрывая проходное сечение зольного ящика 8, через которое всасывается воздух.
Снижается поток воздуха и процесс окисления с выделением тепловой энергии. При дозаправке топливом подачу воздуха в камеру сгорания 5 и камеру дожигания горючих газов 6 необходимо перекрыть, опустив поворотный клапан 19 до упора, открыть дверцу дверного проема 3 на угол 25-30 градусов. , подождите 5 минут, а затем полностью откройте дверцу.
Поворотный ковш предназначен для загрузки угля в теплогенератор. Уголь загружается и вращением ковша 20 вверх загружается в загрузочный бункер 4.
Реактор пиролиза — обзор
Газификация и пиролиз
При нагревании топливо из биомассы разлагается на ряд газообразных и конденсируемых веществ, оставляя после себя твердый углеродистый остаток, известный как полукокс. Это ранняя стадия горения, и светящееся пламя, наблюдаемое при сжигании древесины и другой биомассы, является результатом окисления летучих соединений, выделяемых во время пиролиза и газификации сырья, и теплового излучения частиц сажи от пламени, дающего характерный желтый цвет. .
Когда отношение эквивалента топлива к воздуху, ϕ , в уравнении [6] существенно больше единицы (богатое топливо), топливо будет только частично окисляться из-за недостатка кислорода, и продукты реакции не будут состоять из только углекислый газ и вода, но большие количества окиси углерода и водорода в дополнение к различным количествам газообразных углеводородов и конденсируемых соединений (смол и масел), а также полукокса и золы. Другие окислители, включая водяной пар, также можно использовать вместо воздуха, и в этом случае набор продуктов реакции будет отличаться.Условия реакции могут быть изменены для максимального увеличения производства топливных газов, жидких топливных веществ или полукокса (как для древесного угля), в зависимости от предполагаемого энергетического рынка или рынков. Термин «газификация» применяется к процессам, которые оптимизированы для производства топливного газа (в основном CO, H 2 и легких углеводородов). При нагревании без добавления окислителя сырье подвергается пиролизу. Реакторы пиролиза обычно проектируются так, чтобы максимально увеличить производство жидкостей за счет быстрого, а не медленного нагрева, хотя растущий интерес к биоугля или сажи теперь меняет предпочтительную смесь продуктов.Катализаторы иногда используются для ускорения различных реакций, особенно крекинга высокомолекулярных углеводородов, образующихся во время газификации, а также в химическом каталитическом синтезе жидких углеводородов и других продуктов при производстве транспортного биотоплива.
Технология газификации была разработана более 200 лет назад (Kaupp and Goss, 1984), а в последнее время была усовершенствована в первую очередь с целью обеспечения доступа твердого топлива (биомасса, уголь и кокс) к некоторым из тех же коммерческих рынков, что и природные. газ и нефть.Газификаторы уже давно используются для преобразования твердого топлива в топливные газы для работы двигателей внутреннего сгорания, как с искровым зажиганием (бензин), так и с воспламенением от сжатия (дизели). Их также можно использовать для устройств внешнего сгорания, таких как котлы и двигатели Стирлинга. Наиболее распространенными типами являются газификаторы прямого действия, в которых частичное окисление сырья в топливном слое дает тепло для реакций пиролиза и газификации, которые в основном являются эндотермическими. В газификаторах непрямого действия и в реакторах пиролиза используется внешний теплообмен для обеспечения тепла, необходимого для пиролиза топлива.Тепло может быть произведено путем сжигания части исходного топлива из биомассы или путем сжигания выходящих топливных газов, жидкостей или полукокса. Аллотермические реакторы были разработаны для подачи тепла за счет внутреннего, но раздельного сжигания фазы полукокса после газификации сырья, в основном в системах с двумя реакторами (Wilk and Hofbauer, 2013). Газификаторы могут иметь меньше проблем со шлакованием золы из-за более низких рабочих температур по сравнению с камерами сгорания, хотя шлакование, засорение и агломерация слоя остаются проблемами с некоторыми видами топлива (например.г., солома).
Когда в газификаторы прямого действия подается воздух для реакции с сырьем, топливные газы будут содержать большое количество азота, а теплотворная способность или содержание энергии в газе будет низким (3–6 МДж м –3 ) по сравнению с природный газ (сравните метан при 36,1 МДж м –3 ) и другие более традиционные виды топлива. Двигатели без наддува, работающие на таком газе, будут иметь пониженную выходную мощность по сравнению с их работой на бензине или дизельном топливе (Jenkins and Goss, 1988).В случае дизельных двигателей газ не может использоваться в одиночку, и для обеспечения надлежащего зажигания и выбора момента впрыскивается пилотное количество дизельного топлива. Для двигателей с искровым зажиганием выходная мощность двигателя примерно вдвое меньше, чем у того же двигателя на бензине, потому что объем воздуха в двигателе (количество воздуха, всасываемого в цилиндр двигателя во время такта впуска) уменьшается из-за большого занимаемого объема. топливным газом, и поэтому во время каждого цикла можно сжечь не так много топлива (Jenkins and Goss, 1988).Частично это можно преодолеть с помощью наддува двигателя. Для двухтопливных дизельных двигателей газ, как правило, может обеспечивать до 70% общей энергии топлива, не сталкиваясь с серьезным ударом, который возникает из-за длительной задержки зажигания, связанной с генераторным газом, тем же свойством, которое дает газу отличное октановое число ( Chancellor, 1980; Ogunlowo et al ., 1981). Те же свойства генераторного газа, которые приводят к позднему воспламенению и детонации в дизельном двигателе, делают его достаточно устойчивым к детонации в двигателе с искровым зажиганием, поэтому можно использовать степени сжатия значительно выше 10.При правильной конструкции головки блока цилиндров и увеличенной степени сжатия эффективность двигателя может быть улучшена по сравнению с бензиновым двигателем, компенсируя некоторое снижение характеристик из-за уменьшения объема воздуха.
Если в реакторе газификации используется обогащенный или чистый кислород, полученный топливный газ или синтез-газ будет более высокого качества. Однако стоимость производства кислорода высока, и такие системы обычно предлагаются для более крупных масштабов или для производства более дорогих товаров, таких как химикаты и жидкое топливо.Метанол, жидкое спиртовое топливо, CH 3 OH, образуется в каталитической реакции
[7] CO + 2h3 = Ch4OH
Этой реакции способствует низкая температура (400 ° C), но высокое давление (30– 38 МПа). Оксид цинка и оксид хрома являются общими катализаторами. Используя медь в качестве катализатора, можно снизить температуру и давление реакции (260 ° C, 5 МПа), но медь чувствительна к отравлению серой и требует хорошей очистки газов (Probstein and Hicks, 1982). Реакции Фишера-Тропша можно использовать для получения ряда химических веществ, включая спирты и алифатические углеводороды.Снижены требования к температуре и давлению, а выбор катализатора может быть получен с большей селективностью.
Жидкости, такие как бензины, могут производиться косвенными путями, включающими газификацию или пиролиз твердой биомассы для получения реакционноспособных промежуточных продуктов, которые могут быть каталитически улучшены (Kuester et al. ., 1985; Prasad and Kuester, 1988; Kuester, 1991; Браун, 2011). Жидкости, произведенные непосредственно путем пиролиза, обычно коррозионно-агрессивны, страдают окислительной нестабильностью и не могут быть напрямую использованы в качестве моторного топлива.Многие продукты также канцерогены. Как правило, для получения товарных соединений необходима какая-либо очистка. Несмотря на это, реакторы быстрого пиролиза, использующие биомассу и другие виды топлива, находятся в стадии коммерческого запуска для производства бионефти (Ensyn Corp, 2014). Жидкое топливо также можно производить прямыми термохимическими способами, такими как гидрирование в растворителе с присутствующим катализатором (Elliott et al ., 1991; Bridgwater and Bridge, 1991).
Одним из основных технических препятствий, особенно в малых масштабах, при применении газификаторов для целей, отличных от прямого сжигания сырого газа, является очистка и очистка газа.Удаление твердых частиц и смол из газа имеет решающее значение для последующего производства электроэнергии и синтеза топлива. Смолы представляют собой класс тяжелых органических материалов, которые особенно трудно удалить или обработать. Существуют системы для производства газа приемлемого качества, но, как правило, они основаны на некоторой комбинации влажной и сухой очистки и фильтрации, что увеличивает расходы на систему конверсии. Маломасштабные газификаторы, используемые для удаленного производства электроэнергии, часто применялись без надлежащих процедур обращения с гудроном, отделенным от газа.Очистка газа и обработка гудрона остаются критическими инженерными задачами для более широкого внедрения технологии во всех масштабах.
Расширенные возможности производства электроэнергии из биомассы включают использование газификатора биомассы для производства топливного газа для газовой турбины в интегрированной системе с комбинированным циклом газификации (Рисунок 17; Meerman et al ., 2013). Эффективность этих систем может быть значительно выше, чем у традиционных систем выработки электроэнергии с циклом Ренкина. Основные технические задачи включают очистку горячего газа для получения газа надлежащего качества, чтобы избежать загрязнения турбины, а также разработку надежных реакторов или компрессоров высокого давления и систем подачи топлива.Считается, что использование газогенератора является преимуществом по сравнению с камерой сгорания с прямым сгоранием, поскольку потери тепла в системе газоочистки вызывают меньшее беспокойство, поскольку большая часть энергии топлива находится в форме химической энергии получаемого газа. Другие преимущества газификаторов перед камерами сгорания включают способность работать при более низких температурах и меньшие объемы газа на единицу преобразованного сырья, что способствует удалению соединений серы и азота для снижения выбросов загрязняющих веществ. Системы этого типа в настоящее время находятся в стадии разработки, и несколько крупномасштабных демонстрационных проектов были завершены, но эта технология еще не была внедрена в коммерческих целях для биомассы, хотя она применяется для угля в более крупных масштабах (Stahl and Neergaard, 1998).На рисунке 17 также показано возможное использование впрыска пара для уменьшения тепловых выбросов NO x и увеличения выходной мощности газовой турбины. Высокая теплоемкость пара по сравнению с продуктами сгорания приводит к увеличению мощности, а добавление пара снижает температуру пламени, что способствует снижению термического образования NO x (Weston, 1992). Многие другие варианты термохимической конверсии находятся в стадии разработки (Brown, 2011).
Рис. 17. Передовая концепция выработки электроэнергии с комбинированным циклом с интегрированной газификацией. Показана газификация сжатым воздухом. Также показан вариант газовой турбины с впрыском пара (IG / STIG).
Реактор пиролиза — обзор
3.4 Конструкция лабораторных реакторов пиролиза с неподвижным слоем («Hot-Rod»)
В реакторе пиролиза с неподвижным слоем частицы пробы укладываются на желаемую глубину слоя. Тепло обычно диффундирует внутрь от стенок реактора. Выделяемые летучие вещества расширяются, повышая локальное давление небольшими приращениями.Результирующий градиент давления помогает летучим компонентам медленно выходить из слоя и из реактора [, например, ср. Берк, 1978]. Пропускание потока инертного газа через неподвижный слой поможет сократить время пребывания летучих в зоне реакции. Постоянная скорость газа-носителя требуется для поддержания достаточно стабильного времени пребывания летучих внутри реактора. Сопоставимое время пребывания тогда позволило бы сравнить данные для реакторов разных размеров, но схожей формы [Dryden & Sparham, 1963].Корпус реактора можно также использовать в качестве резистивного нагревателя, если электроды зажаты на обоих концах трубчатого реактора. Первоначальная конфигурация реактора с «горячим стержнем» [Hiteshue et al., 1957] завершена, когда трубчатый корпус реактора изготовлен из сплава, способного выдерживать высокие давления.
Несмотря на присущие проблемы, связанные с вторичными реакциями между сложенными частицами и выделяющимися летучими веществами, конфигурация реактора «горячий стержень» оказалась полезной. Его относительно легко построить и использовать.Первоначально он был задуман и построен в лабораториях Горного бюро США для изучения гидропиролиза углей. Он использовался в Coal Research Establishment (British Coal) для исследования производства бензола, толуола и ксилолов («БТК») во время гидропиролиза.
Реакторы типа «горячий стержень» наиболее известны из работ Хитешу и его сотрудников из Горного бюро США [1957, 1960, 1962a, 1962b], которые проводили эксперименты по гидропиролизу угля при давлении до 400 бар и почти 900 °. С.Стойки для образцов длиной 25–40 см были смонтированы в трубках из нержавеющей стали с малым диаметром отверстия. Реакторы с различным соотношением сторон (длина / диаметр) были испытаны Graff et al. [1976] и Kershaw & Barras [1979]. Версия, созданная и управляемая Ладнером и его сотрудниками [Finn et al., 1980; Fynes et al., 1984] содержал около 10 г угля в трубках реактора длиной 75 см или более с внутренним диаметром 8 мм.
В Имперском колледже был построен реактор меньшего размера (внутренний диаметр 6 мм, длина 20 см), первоначально для производства большего количества смолы во время экспериментов по гидропиролизу, чем это было возможно с помощью прибора с проволочной сеткой.От 0,5 до 1 г образца угля использовалось во время начальных экспериментов, в которых исследовалось влияние скорости потока газа-носителя и скорости нагрева. Было проведено сравнение с результатами, полученными на более крупном реакторе с «горячим стержнем» на British Coal [O’Brien, 1986; Bolton et al., 1987]. Попытки изучить точную роль высоты слоя привели к использованию более мелких (~ 4 мм) неподвижных слоев, что соответствует примерно 50 мг образца (рис. 3.4a). Использование образцов меньшего размера служило для частичного подавления вторичных реакций в слое, а также на надводном борту реактора [Gonenc et al., 1990]. Уменьшение высоты слоя также улучшило осевую однородность температуры. Этот реактор работал при скоростях нагрева от 10 ° C мин. -1 до 10 ° C с -1 . Были рассчитаны более быстрые скорости нагрева, которые привели к неприемлемо крутым радиальным градиентам температуры в слое образца диаметром 6 мм [O’Brien, 1986].
Рисунок 3.4. Конфигурация реактора «горячий стержень». (а) Обычный однослойный реактор. (b) Две неподвижные кровати в тандеме; нижний слой нагревается отдельной печью и заполнен катализатором гидроочистки летучих веществ, выделяемых при пиролизе образца в верхнем слое.
[Воспроизведено с разрешения: (a) Fuel 1987, 66, 1414; Авторское право Elsevier, 1987; b) Топливо, 1998, 77, 1715; Copyright 1998 Elsevier.]Как указано выше, конфигурация «горячего стержня» требует, чтобы корпус реактора действовал как резистивный нагреватель, а также как сосуд высокого давления. Поэтому материал трубки должен выдерживать внутренние напряжения из-за работы под высоким давлением при температурах реакции — в зависимости от конкретного эксперимента — примерно до 1000 ° C. Это предъявляет довольно жесткие требования к материалу НКТ.Первоначальные реакторы Горнодобывающего управления США состояли из толстостенных труб из нержавеющей стали малого диаметра, которые выбрасывались после каждого или нескольких экспериментов. В компании British Coal стандартной практикой было изготавливать корпуса реакторов из нержавеющей стали и утилизировать их после нескольких запусков. Похоже, это был компромисс, достигнутый после того, как было принято решение использовать реакторы диаметром 8 мм, которые были длинными (> 75 см) и требовали бурения с обоих концов. Более прочные реакторы можно было бы изготавливать из специализированных сплавов.Хотя серия Nimonic представляет собой крайний случай, многие из этих сплавов труднее обрабатывать, чем нержавеющая сталь. Однако изготовление каждого такого реактора требует значительных затрат времени и средств.
Из различных специальных сплавов изготовлены более прочные корпуса для более коротких (20 см) реакторов, используемых в Имперском колледже. Сплавы Нимоник 80 и Нимоник 105 (Сплавы Генри Виггина) первоначально использовались для экспериментов, проводимых при 850 ° C и давлении до 100 бар. Однако эти сплавы требуют термической обработки для размягчения материала перед механической обработкой, а затем для упрочнения реактора после стадии механической обработки.Incolloy 800 HT намного проще обрабатывать, и он использовался для изготовления корпусов реакторов для CO 2 и экспериментов по паровой газификации до 1000 ° C и 40 бар. При температуре выше 700 ° C необходимо учитывать тепловое расширение корпуса реактора. Использование жестких электродов может вызвать деформацию реакторных труб. В данной конструкции питание подается на один из электродов через плетеные медные кабели, и оба электрода охлаждаются водой, чтобы избежать больших изменений удельного сопротивления [Pindoria et al., 1998a; Collot et al., 1999].
В другом применении конфигурации реактора с «горячим стержнем» измеряли выбросы микроэлементов из различных видов твердого топлива во время совместной газификации и совместного сжигания угля и биомассы. Чтобы предотвратить загрязнение металлических стенок, реактор с внутренним диаметром большего размера (13,8 мм), изготовленный из Incolloy 800 HT, был облицован кварцевой гильзой и работал при давлении до 40 бар и 1000 ° C [Collot et al., 1998]. Тот же реактор также использовался для исследования, дает ли совместный пиролиз и совместная газификация угля и биомассы значительные синергетические эффекты.
В литературе описано относительно немного двухэтапных экспериментов с реактором типа «горячий стержень». Болтон и др. [1988] прикрепил второй слой, заполненный водными оксидами титана для каталитического крекинга смол гидропиролиза. Эксперименты в основном проводились при 150 бар, при этом секция гидропиролиза увеличивалась до 500 ° C, в то время как стадия катализатора поддерживалась при максимальной температуре 400 ° C. Выход гудрона на первой стадии составил около 25% от исходной массы угля.Авторы сообщили о превращении смол в «бесцветные жидкости с низким содержанием гетероатомов» с температурой кипения около 40 процентов ниже 140 ° C. На рис. 3.4b показан двухступенчатый реактор с неподвижным слоем, построенный в Имперском колледже. В верхней части (укороченная «горячая штанга») пары смолы / масла производились мягким гидропиролизом (давление h3 до 40 бар). Газ проходил через неподвижный слой и уносил выделяющиеся летучие вещества на вторую стадию, заполненную катализатором, расположенную под образцом и независимо нагреваемую небольшой печью [Pindoria et al., 1998b].
В следующем разделе мы познакомим вас с третьим основным типом реакторов, стендовым реактором с псевдоожиженным слоем, успешно используемым в экспериментах по пиролизу угля. В разделе 3.6 мы сравним тенденции продуктов из экспериментов по пиролизу угля при атмосферном давлении в реакторе с «горячим стержнем» с результатами, полученными на аппарате с проволочной сеткой. Результаты экспериментов под высоким давлением в реакторе типа «горячий стержень» будут представлены в главе 4.
Новый подход к производству возобновляемой энергии
Биотопливо, полученное путем быстрого пиролиза из биомассы, является многообещающим кандидатом.Сердцем системы является реактор, который прямо или косвенно нагревается примерно до 500 ° C выхлопными газами из камеры сгорания, в которой сжигается пиролизный газ и некоторые побочные продукты сгорания. В большинстве случаев внешний нагреватель биомассы используется в качестве источника нагрева системы, в то время как внутренний электрический нагреватель недавно внедрен в качестве источника нагрева реактора. Однако эта система отопления заставляет биомассу или другие традиционные формы потребления топлива производить возобновляемую энергию и способствует загрязнению окружающей среды.Чтобы преодолеть это, была исследована возможность использования солнечной энергии с быстрым пиролизом. Основными преимуществами солнечного реакторного отопления являются возобновляемые источники энергии, сравнительно более простые устройства и отсутствие загрязнения окружающей среды. Была исследована установка пиролиза лабораторного масштаба вместе с концентратором параболического рефлектора диаметром 1,2 м, который обеспечивает горячий выхлопной газ до 162 ° C. Исследование показывает, что около 32,4% выбросов углекислого газа (CO 2 ) и почти треть стоимости топлива снижаются за счет использования солнечной системы отопления.Успешное внедрение предложенного пиролиза с использованием солнечной энергии откроет перспективу использования возобновляемых источников энергии.
1. Введение
Соответствие между спросом и предложением энергии является мерой индекса развития страны. Существует тесная взаимосвязь между уровнем потребления энергии в стране и ее экономическим развитием. Энергетический кризис является основной проблемой в современном мире из-за быстрого истощения невозобновляемых энергоресурсов, таких как ископаемое топливо, масла и природные газы, поскольку спрос на энергию растет угрожающими темпами [1].Точно так же Бангладеш десятилетиями сталкивается с серьезным энергетическим кризисом, поскольку энергия необходима почти для всех видов экономической деятельности, от орошения до производства товаров. В последнее время доказанные вероятные запасы природного газа в стране оцениваются примерно в 195400000000 м 3 [2], в то время как нынешние запасы угля в стране составляют около 2041 млн тонн [3]. Оценка показывает, что общий объем хранения нефтепродуктов (дизельное топливо, керосин, бензин и октановое число) в стране составляет около 687500 тонн, что составляет лишь 8% от общего спроса [4].По оценкам, к 2100 году спрос на энергию увеличится в пять раз по сравнению с текущим спросом, поскольку ожидается, что население мира составит более 12 миллиардов человек [5]. В Бангладеш запасов коммерческих первичных источников энергии (например, природного газа и угля) недостаточно для удовлетворения растущих потребностей страны [6]. Производство электроэнергии в стране в основном зависит от природного газа и составляет 62,16% от общей установленной мощности по выработке электроэнергии (10416 МВт) в июне 2014 г. [7].Таким образом, в последние несколько лет внимание уделяется возобновляемым источникам энергии, особенно после глобального осознания.
Пиролиз считается распространенным методом извлечения возобновляемой энергии (бионефти) из различных видов биомассы, включая сельскохозяйственные остатки, лесные остатки и городские отходы. Пиролиз, процесс термического разложения органических компонентов в отходах биомассы в отсутствие кислорода при средней температуре (около 500 ° C), дает продукты выхода гудрона (бионефть, биотопливо и биокруд), полукокса (активированный уголь) и газообразные фракции (топливо). газы) [8].Процессы пиролиза можно разделить на медленный пиролиз и быстрый пиролиз в зависимости от времени, необходимого для полного термического разложения исходных материалов. Широко используется быстрый пиролиз, так как он занимает секунды для полного разложения биомассы и дает около 60% выхода в виде бионефти, тогда как медленный пиролиз приводит к биочагу в качестве основного продукта и занимает несколько часов для завершения [9]. Однако размер частиц исходного сырья влияет на эффективность и характер процесса пиролиза. Кроме того, пиролиз может быть пиролизом в неподвижном слое или пиролизом в псевдоожиженном слое.При пиролизе с неподвижным слоем используется пиролизер с неподвижным слоем, в котором исходный материал фиксируется в реакторе и нагревается при повышенной температуре. Для создания инертных условий и сброса газовой смеси в конденсатор необходимо использовать инертный газ (обычно азот). Возможный путь процесса пиролиза показан на рисунке 1.
Эта технология с исследованиями и экспериментальными работами распространяется во многих странах современного мира [10]. Биомассу можно использовать в качестве сырья для пиролиза для получения жидкого, газообразного и твердого топлива.Технология пиролизного преобразования биомассы изучалась в течение последних трех десятилетий и используется в коммерческих целях [11]. Технология производит газ, пар и твердый уголь; однако пропорция продуктов выхода зависит от типов и свойств исходных материалов и условий процесса [10]. Твердый полукокс с высшей теплотворной способностью (ВТС) 17–36 МДж / кг может использоваться для обеспечения тепла для самого процесса пиролиза, в качестве топлива либо непосредственно в виде брикетов, либо в качестве полукокса, а также в качестве сырья для получения активированного угля.Фракция пиролизного газа включает CO 2 , CO, H 2 , CH 4 , C 2 H 4 , C 3 H 6 и углеводороды с ГТС 6,4–9,8 МДж. / кг, которые можно использовать для технологического тепла [12]. Следовательно, стоимость системы отопления может быть снижена за счет использования продуктов угля и газа в процессе пиролиза. Сельскохозяйственные отходы и твердые бытовые отходы, входящие в состав биомассы, считаются привлекательными возобновляемыми источниками энергии из-за нулевого чистого выброса углекислого газа в атмосферу [13].Пиролизное масло, полученное из сельскохозяйственных отходов с GCV в диапазоне от 15 до 38 МДж / кг, имеет некоторые преимущества при транспортировке, хранении, сжигании, модернизации и гибкости в производстве и маркетинге [14]. Жидкий продукт используется в качестве топлива в турбинах и других системах отопления, и его можно добавлять в сырье для нефтеперерабатывающих заводов или улучшать с помощью катализаторов для производства очищенного топлива нефтяного качества [15]. Стоит отметить, что бионефть, полученная из биомассы, представляет собой смесь около 300 типов основных и второстепенных органических соединений (т.например, кислоты, спирты, кетоны, альдегиды, фенолы, простые эфиры, сложные эфиры, сахара, фураны, соединения азота и многофункциональные соединения и т. д.), имеет несколько экологических преимуществ перед ископаемым топливом в качестве чистого топлива [16]. Более того, бионефть не будет облагаться налогами SO x , поскольку биомасса содержит незначительные количества серы и генерирует более чем на 50% меньше NO x , чем дизельное топливо. Кроме того, в 2005 году Продовольственная и сельскохозяйственная организация ООН оценила это примерно в 1.67 миллиардов тонн фиников было произведено в первой десятке стран-производителей фиников. Это огромное количество семян почти не используется и редко используется для корма лошадей, крупного рогатого скота, верблюдов, овец и коз. Таким образом, эти отходы могут эффективно использоваться в качестве исходного материала для рекуперации энергии в качестве топлива из-за их непищевого и другого некоммерческого использования. Однако высокая стоимость и сложность, а также угроза для окружающей среды являются основными проблемами традиционной биомассы и системы электрического нагрева пиролизной технологии. Поэтому новая концепция солнечного отопления ассимилируется с системой отопления на биомассе, чтобы смягчить проблемы.В этом исследовании реактор был частично нагрет до 162 ° C; однако непрерывное нагревание может быть более эффективным для снижения выбросов от топлива из биомассы, а также снижения стоимости топлива.
2. Пиролиз с использованием солнечной энергии: классификация и конструкция
Хотя процесс пиролиза является важным кандидатом в возобновляемые источники энергии, он имеет некоторые недостатки. Среди проблем системы пиролиза — снижение энергоснабжения, поскольку для нагрева реактора требуются другие источники энергии, а также глобальное потепление.Бионефть, полученная из отходов биомассы, может рассматриваться как альтернатива ископаемым видам топлива, поскольку они устойчивы и почти нейтральны по CO 2 , хотя производство тепла вызывает дополнительное загрязнение в процессе пиролиза. Реактор, сердце системы пиролиза, нагревается до повышенных температур с помощью внешнего нагревателя биомассы или внутреннего электрического нагревателя. В частности, для разложения отходов биомассы требуется много тепловой энергии. Эти системы отопления очень дороги, а при сжигании топлива из биомассы образуется огромное количество CO 2 , ответственного за загрязнение окружающей среды.В дополнение к этому, биомасса или электрический нагреватель делают реактор более сложной системой.
Эту проблему пиролизной системы можно устранить, установив солнечную систему отопления. Комбинированная система отопления с использованием солнечной энергии и биомассы может быть очень эффективной для этой цели. Эта солнечная система паралича более экологична и энергоэффективна. В этом процессе исходный материал подается в реактор, а тепло передается извне параболическим солнечным нагревателем. Концептуальная система пиролиза с использованием солнечной энергии показана на рисунке 2 вместе с солнечным нагревом.Подача сырья контролируется регулирующим клапаном вместо системы псевдоожижения, чтобы уменьшить контролируемый пиролиз с неподвижным слоем с несколькими прерывистыми критериями.
2.1. Классификация пиролиза с использованием солнечной энергии
Проблема системы отопления пиролиза является основной проблемой с момента ее изобретения. Обычная внешняя система нагрева биомассы способствует загрязнению воздуха из-за огромного количества CO 2 , выделяемого при его сжигании. С другой стороны, система внутреннего электрообогрева — очень дорогой вариант.Следовательно, будет лучше ассимилировать солнечное отопление вместе с отоплением из биомассы или системой электрического отопления для снижения затрат на отопление, а также загрязнения окружающей среды. Однако трудно получить оптимальную температуру для пиролиза, используя только солнечную систему отопления. Поскольку этот подход все еще находится в зачаточном состоянии, он требует обширных исследований и изучения дизайна и реализации в промышленных масштабах. Однако пиролиз с помощью солнечной энергии можно классифицировать как частичный и непрерывный нагрев солнечной энергией, как показано на рисунке 3.При частичном нагреве реактор сначала нагревается до определенной температуры с помощью солнечной системы нагрева, а затем с помощью биомассы или системы электрического нагрева. Напротив, реактор непрерывно нагревается системой солнечного обогрева с биомассой или системой электрического обогрева на протяжении всего цикла пиролиза при непрерывном обогреве. Можно также нагреть реактор, используя только солнечное тепло, но этому вопросу уделяется пристальное внимание в системе солнечного отопления.
2.2. Рассмотрение конструкции реактора пиролиза с использованием солнечной энергии
Конструкция реактора является жизненно важной частью любой системы пиролиза.В случае пиролиза с использованием солнечной энергии также важно спроектировать реактор. Как мы уже упоминали, реактор для этой системы проще, чем другой обычный реактор пиролиза; однако по-прежнему существует проблема получения равномерного нагрева по всей поверхности реактора как для прерывистого, так и для непрерывного нагрева с помощью солнечной энергии. Концептуальный проект системы непрерывного солнечного нагрева с вращающимся реактором и скользящим солнечным концентратором показан на рисунке 4. Эта система будет равномерно нагревать реактор и равномерно повышать температуру подаваемого материала до оптимальной температуры для разложения.
3. Перспективы солнечной энергии и пиролиза в Бангладеш: исследование
Для проверки предложенной системы пиролиза было проведено экспериментальное исследование, в ходе которого мы рассматриваем доступность солнечной энергии в Бангладеш. В следующем разделе представлено краткое обсуждение перспектив солнечной энергии и пиролиза с последующим экспериментальным исследованием.
3.1. Solar Energy Prospect
Бангладеш обладает огромными запасами солнечной энергии.Бангладеш находится между 20,308 ° и 26,388 ° северной широты и 88,048 ° и 92,448 ° восточной долготы на площади 147500 кв. Км, что является идеальным местом для наилучшего использования солнечной энергии [17]. Солнечная карта Бангладеш, предоставленная Geospatial Toolkit, показывает, что солнечная радиация находится в диапазоне 4-5 кВтч / м 2 / день примерно на 94% площади Бангладеш [17, 18]. Среднее количество солнечных часов в день в Бангладеш составляет 6,5, а также среднегодовая солнечная радиация составляет около 0.2 кВт / м 2 . Эта статистика показывает, что Бангладеш теоретически получает примерно 69751 ТВтч солнечной энергии в год, что более чем в 3000 раз превышает объем производства электроэнергии в стране в 2006 финансовом году. Установлено, что среднегодовая плотность мощности солнечной радиации в Бангладеш обычно находится в диапазоне 100–300 Вт / м 2 [19].
3.2. Пиролиз в Бангладеш
Технология пиролиза в Бангладеш находится в стадии разработки; однако технико-экономическое обоснование этой технологии возможно для производства альтернативного жидкого топлива из твердых органических отходов.Некоторые исследования в этой области продолжаются в Раджшахском инженерно-технологическом университете (RUET) с 2000 года. Многочисленные исследования показывают технико-экономическое обоснование пиролиза различных отходов биомассы семян, пластиковых отходов, твердых бытовых отходов, утиля шин и жаргонизмов. целлюлозные материалы [20–34]. Недавнее исследование предполагает, что установка среднего коммерческого масштаба, использующая утилизированный материал шин, является благоприятной с лучшими технико-экономическими показателями. Эта установка сократит ежегодный импорт энергии на 29400 тонн (205000 баррелей) масел и 22400 тонн угля.Более того, большое количество опасных отходов (изношенные шины) подлежат надлежащему обращению [35].
3.3. Материалы и методы
3.3.1. Материалы
Образцы семян фиников для пиролиза собираются на месте в Раджшахи, Бангладеш. Сырье измельчается и разрезается на три различных объема: 0–0,2 см 3 , 0,2–4 см 3 и 0,4–0,6 см 3 . Затем образец сушат в печи в течение 24 часов при 110 ° C для удаления влаги перед пиролизом. Ближайший и окончательный анализ семян фиников представлен в таблице 1.
Сравнение показывает, что плотность и вязкость жидкости для семян фиников выше, чем у обычного дизельного топлива, независимо от того, ниже ли теплотворная способность чем дизель.Теплотворная способность выше, чем у других пиролизных масел, за исключением масла семян красного дерева. 4.3. Выполнимость пиролиза с использованием солнечной энергииПоскольку концепция солнечного пиролиза находится в зачаточном состоянии, нет достаточной литературы, касающейся сравнения пиролиза с использованием солнечной энергии с традиционной системой быстрого пиролиза. На основе первичных результатов предлагаемой системы пиролиза следующие разделы посвящены технико-экономическому обоснованию этой системы. Технико-экономическое обоснование предложенной системы было оценено путем сравнения обычного первого пиролиза с точки зрения энергозатрат, стоимости отопления и загрязнения окружающей среды.Для исследования этих параметров температура реактора сначала была повышена до 162 ° C с использованием солнечного концентратора, а затем до 400–600 ° C с помощью внешнего нагрева биомассы. 4.3.1. Потребляемая энергия для нагреваОбычно при быстром пиролизе реактор нагревается от внешнего (биомасса) или внутреннего (электрического) источника энергии. Другими словами, для работы реактора разложения исходных материалов требуется значительное количество энергии. Эффективность пиролиза в значительной степени зависит от количества энергии, используемой для завершения разложения исходных материалов.Следовательно, другой возобновляемый источник энергии, такой как включение солнечной энергии, может снизить количество энергии, которое требуется в системе быстрого пиролиза. Было обнаружено, что для разложения 0,4 кг семян фиников за один цикл требуется около 6 кг рисовой шелухи [36]. Теплотворная способность рисовой шелухи колеблется от 13,16 до 15,22 МДж / кг, как показано в Таблице 3 [42]. Следовательно, с учетом более низкой теплотворной способности рисовой шелухи, по оценкам, реактор потребляет около 78,96 МДж для полного разложения семян фиников за один цикл быстрого пиролиза.С другой стороны, сочетание солнечной системы отопления с системой нагрева рисовой шелухи снижает потребление энергии рисовой шелухой до 4,056 кг, что эквивалентно 53,38 МДж, как показано на рисунке 6.
|